It seems we need a new thread about sharpening drills, instead of going of topic in other threads. Sometimes you have to learn to sharpen drills, like if you're trying to drill out a roll pin or broken tap, I learned how to do a four facet point and never looked back
I will certainly be happy to learn from you, my results have always been very disappointing... Thanks in advance.
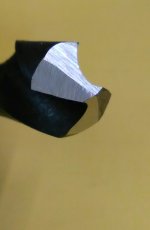
This is what I mean by four facet point. Only give the drill a little tickle before giving it a dunk in water, if if gets to hot and " blues " it's gone soft and you need to grind away the darkness. I find it easier to get a symmetrical tip by giving it a tickle on one side, flipping it 180 deg then giving it another tickle before the dunk. It still takes practice though.
You drilled out a broken tap ??
Thats interesting and what type of drill did you use to do that ?
Taps break in holes for several reasons -
1-overleaverage of the tap holder.
2-undersize hole that doesn't comply with engineering standards of thread depth in relation to the type of thread required.
3- trying to tap hardened/case-hardened steel .
4- cheap taps not complying with industrial standards hardness .
I take it you haven't heard of --( broken ) Tap Extractors ?
You do realize a genuine industrial tap will NOT be drilled out with a High Speed Steel ( HSS) drill or one that is generally used to drill mild steel ?
When drilling steel ( not aluminum/copper/brass ) and indented slope away from the cutting edge weakens it causing breakage .
A slowly receding edge is required for strength .
Thats interesting and what type of drill did you use to do that ?
Taps break in holes for several reasons -
1-overleaverage of the tap holder.
2-undersize hole that doesn't comply with engineering standards of thread depth in relation to the type of thread required.
3- trying to tap hardened/case-hardened steel .
4- cheap taps not complying with industrial standards hardness .
I take it you haven't heard of --( broken ) Tap Extractors ?
You do realize a genuine industrial tap will NOT be drilled out with a High Speed Steel ( HSS) drill or one that is generally used to drill mild steel ?
When drilling steel ( not aluminum/copper/brass ) and indented slope away from the cutting edge weakens it causing breakage .
A slowly receding edge is required for strength .
We had a set of tap extractors ( the type that engage in the tap flutes ) but they were never the right size or strong enough. A tap that has been used many times will sometimes fatigue and fail. A carbide tipped masonry drill is often pressed into service on broken taps or centre drills ( I usually modify a blunt centre drill into a spotting drill to prevent the tip breaking of). Two other common causes of tap brakeage are the flutes choking up or the tap not straight in the hole ( I'm sure you'll know many ways of guiding a tap, but new lads don't ), a sense of " feel " is very important, but overlooked quality in engineering. When mentioning " indented slope " are you referring to rake, clearance or point angle? If I'm sharpening a drill for difficult steel I usually have less point, bevel the corners, stone the edge for less rake and reduce the chisel.

Pictures -- Why Not attach Them ??
Here is the image from post #3 at 1/17th the file size.
Attachments
This is the first forum I've been on and I'm still learning, I'm more of a hitting things with a hammer type person than computer wizard.
That picture (to me ) of the drill looks like the drill bit in the Movie --
The Day the Earth Stood Still where the giant robot was encased in an underground test room and those metal eating flies /bugs started eating the bit .
See -
How to Sharpen Used and Dull Drill Bits (By Hand!!) : 11 Steps (with Pictures) - Instructables
Notice Step 8-
Shaping the Land agrees with my comment above .
The Day the Earth Stood Still where the giant robot was encased in an underground test room and those metal eating flies /bugs started eating the bit .
See -
How to Sharpen Used and Dull Drill Bits (By Hand!!) : 11 Steps (with Pictures) - Instructables
Notice Step 8-
Shaping the Land agrees with my comment above .
The picture is of a four facet drill point, that results in 50% less thrust and 60% less heat, it is a recognised drill geometry in engineering.
And you can produce this four facet drill point using your HAND --not a special machine tool/Jig--?
Hi Duncan, I'm not sure that's the best video on sharpening.See -
1. After achieving the cutting edge he added the lip clearance by dropping the tip over the wheel rather than raising the tip and dropping the shank. That could easily catch and take off your cutting edge, making you start again.
2. He did not quench near often enough.
3. He didn't clear the bit when drilling through a 2" piece of steel. True it's a horizontal hole but still, it doesn't hurt to back it out a few times just to be sure.
Last edited:
Yes, the picture is of a hand ground tip, if anything I find it easyer ( I'll admit it sounds counter-intuitive ).A comment from downstairs was ( with big grin ) " drills like a knife through butter ", ( SG iron ) and it copes with work hardening stainless if you go for it, presumably to get ahead of the heat.
Okay Cal I could have posted a better method but what I was getting at is as far as I can see the "four facet " point requires pretty critical shaping and sharpening and in every case I looked at it required a jig .
Your right about the heat learned that early in my engineering career but as I had access to factory tools in a maintenance aspect I was able to use an oil/water combination to cool down the tip as I ground it to shape, in those days it was a grinding machine I used not modern belts .
Yes I used the same methods as you.
Your right about the heat learned that early in my engineering career but as I had access to factory tools in a maintenance aspect I was able to use an oil/water combination to cool down the tip as I ground it to shape, in those days it was a grinding machine I used not modern belts .
Yes I used the same methods as you.
I guess you're better at sharpening chisel points than me, I could never get it even and to drill the right size, horses for courses I guess.And you can produce this four facet drill point using your HAND --not a special machine tool/Jig--?
Last edited:
If you are referring to a split point geometry, I don't think it's exactly the same thing. Hard to find a picture that illustrates the exact detail, but the split point's tip relief allows cutting up to the very tip. Yours looks like a variation on the chisel tip.The picture is of a four facet drill point, that results in 50% less thrust and 60% less heat, it is a recognised drill geometry in engineering.
Shop Made Drill Sharpening Jigs
Web Thinning
http://alvarestech.com/temp/nist201...ials_DASL-131_Lesson3_arquivos/spot_drill.jpg
If I understand the two differences, the four faceted tip allows for better cooling or less heat gain and is something you can sharpen by hand.
The split point is to prevent wandering by tapering the chisel, but I shudder to think of doing that by hand. It would have be a rather large bit.
The split point is to prevent wandering by tapering the chisel, but I shudder to think of doing that by hand. It would have be a rather large bit.
The split point is to prevent wandering by tapering the chisel, but I shudder to think of doing that by hand. It would have be a rather large bit.
I used to be able to split point small drills by hand, but that's a long time ago when I could see close up without glasses.
jeff
The split point reminds me of the old reduced chisel for drilling marble, not difficult to do by hand but you need a grinding wheel with a nice corner, although I'm not to sure if you're supossed to use the corner.
Oh, don't get me wrong, I have sharpened them to a point by simply going to far and eliminating the chisel. Problem is that's not how it works. Those are what we used to call wrist breakers 'cause when they grab, they don't let go.I used to be able to split point small drills by hand
I try and make them nearly flat, then immediately create a large amount of chip relief.
I also am wondering what roll pins were drilled out with hand ground drill?
Typically one would use a carbide end mill in a machine with a controlled feed, fixtures part, for anything like that. Taps are best just broken up and the pieces removed, no drill is going to help things.
I got a set of car wheels and tires one time from a guy who lost his wheel locks, had to carefully drill down the center of each stud in order to remove them.
I also am wondering what roll pins were drilled out with hand ground drill?
Typically one would use a carbide end mill in a machine with a controlled feed, fixtures part, for anything like that. Taps are best just broken up and the pieces removed, no drill is going to help things.
I got a set of car wheels and tires one time from a guy who lost his wheel locks, had to carefully drill down the center of each stud in order to remove them.
- Home
- Design & Build
- Equipment & Tools
- Sharpening drills