In typical designs it can be expected to be larger but not negligible.
Hi ! thanks for the very helpful reply.
My feeling is that the side and back emissions are usually very low in level and arrive at the listening spot not directly but reflected and possibly absorbed by room walls that should be treated in a good listening room
I believe in dampening walls that mitigate reflections.
We "hear/see" the walls when they reflect the sound.
The hole for the driver weakens the front panel and the heavy driver hanging off it drives it directly and so a balanced approach would suggest more material for the front panel relative to the other panels.
Thanks again. This confirms my feelings.
Speaking of "dead" materials i always think to bulletproof glass.
If you knock on them they sound quite dead.
They are in the end laminated materials where stiff and hard layers are combined with dampening layers
An externally hosted image should be here but it was not working when we last tested it.
of course glass is very inconvenient, but maybe steel (stiff and hard) and mdf (dampening) sheets combinations could give a similar effect ? 🙄
It is not a my idea ... i was reading the Audio Concepts site yesterday 😱
but i cannot find the link anymore. There were words about cabinets construction.
Thanks a lot again, gino 😀
Last edited:
MDF has relatively low damping compared to resin and so would not make a good damping layer. Bullet proof wood on the other hand would be a good speaker cabinet material apart from the high price. Typically a hard wood ply like beech soaked in resin and compressed to make it heavier than water.Speaking of "dead" materials i always think to bulletproof glass.
If you knock on them they sound quite dead.
They are in the end laminated materials where stiff and hard layers are combined with dampening layers of course glass is very inconvenient, but maybe steel (stiff and hard) and mdf (dampening) sheets combinations could give a similar effect ? 🙄
MDF has relatively low damping compared to resin and so would not make a good damping layer.
Bullet proof wood on the other hand would be a good speaker cabinet material apart from the high price. Typically a hard wood ply like beech soaked in resin and compressed to make it heavier than water.
Hi and thanks a lot again ! very interesting indeed.
I did not know of this particular wood.
I read ...
That could be perfect ?High sound insulation qualities
Pricey ok .. but for a high end speaker and maybe only for the front baffle it could be reasonable.
Clearly easier to work with than metal and glass
Or at least use bars of this wood for bracing the baffle of an existing speaker ?
Better than nothing i guess
I will look for it. Thanks again, gino
Last edited:
In the end it is only the acoustic measurement at the listening position that matters, right?
If we could measure it in all its detail…
dave
or try close to the box https://www.klippel.de/our-products/rd-system/modules/nfs-near-field-scanner.html ??
The hole for the driver weakens the front panel and the heavy driver hanging off it drives it directly and so a balanced approach would suggest more material for the front panel relative to the other panels.
I'm not entirely convinced that's true in all cases. In the case of a small driver in a big baffle, OK. In my current speakers, 12" woofers are located at the top of the box, with under 2" of baffle on three sides (the horn tweeter sits on top outside the box). The driver is supported by relatively narrow sections of baffle that are heavily braced by the side walls. That should make a pretty stiff connection of the driver to the cabinet and limit energy transfer to the baffle, should it not? The baffle below the driver gets a few battens to stiffen it.
I think in a lot of cases baffles are made double thick to allow the woofer to be set in flush and still allow enough material for secure mounting.
Bill
If we could measure it in all its detail…
dave
??? 😕
or try close to the box https://www.klippel.de/our-products/rd-system/modules/nfs-near-field-scanner.html ??
That technique will not separate what is box radiated from what is direct radiated - at least not the way it stands now. It could be used to predict the sound radiated by a hypothetical spherical surface surrounding the enclosure (but I don't think that it does that now,) but not right on the enclosure surface itself. I have used this same technique for quite a while now myself.
The reverse problem of source reconstruction from a measured sound field is call Acoustic Holography, or sometime Fourier Acoustics. Its resolution is almost never very high owing to the long wavelengths of acoustic sounds.
??? 😕
That says a lot… i've seen lots of really nice FR plots you have done, what happens 40 dB down? How much is real signal and how much is noise masking the real signal (from say the box)?
dave
MDF has relatively low damping compared to resin and so would not make a good damping layer. Bullet proof wood on the other hand would be a good speaker cabinet material apart from the high price. Typically a hard wood ply like beech soaked in resin and compressed to make it heavier than water.
Andy, have you ever tried and or measured (accelerometer) this stuff? Usually denser results in less damped, but if this construction increases damping along with density, it looks seriously compelling.
Special tools required to cut it?
It is too expensive for me to play with. High damping is required by bullet proof materials to locally dissipate the energy from the bullet when they hold together rather than shatter. Here is a link someone posted earlier. The entries with high damping are the brand names for woods of this type. I have no experience but it is a compressed hard wood and resin and so I would expect it to be workable with care using hard and sharp tools.Andy, have you ever tried and or measured (accelerometer) this stuff? Usually denser results in less damped, but if this construction increases damping along with density, it looks seriously compelling.
Special tools required to cut it?
Reality of applied use of best available materials
Not to step on your train of thought, but...
I built some 3 cubic ft.(net) Thiele/Small Tuned port boxes for 100W Audax PR240Z0, 10" Aerogel woofer (Fs-27Hz, Vas-3.23cu ft, Qts-.466) Design goal of F(3)-29Hz max.
Ext box size (19.5"wide 12.9"deep 30.6"high)
Used Medex (or equiv) formaldehyde free MDF: 3/4" sides & back
Baffle was of real concern due to use of large EV mid-horn 8HD/1823 (poor choice I regretted: PA horns....) So baffle design required much better than single ply 3/4"
That all said:
What I did was laminate (2) 1/2" sheets (oversize & no mill work yet), bonding the two sheets together using liberal amounts of Neopreme contact cement (both surfaces).
Issue with bonding material's spec for high applied psi requirement for proper bonding. Who has a large industrial press handy? No one!
Only solution was to protect laminate between 2 sacrafical sheets and Jack up the heaviest vehicle I could borrow and basically drive the weight of heavy front end over entire surface area. I Shi_ you not! I have pictures of driveway operation....& crazy old Cowboy. It drew a crowd.
The composite material I ended up with was sweet and did the trick with bracing & rubber 'gasket' between baffle and 1.5" wide recessed mounting frame/bracing and screws 2" apart entire periphery. Realize that I have luxury of all sizing, milling, holes and cutouts done on CNC equipment. Always use good quality polycarbonate glue, w water wetting material and clamping when gluing bracing to MDF, using crowns of bracing wood to your adavantage. This basic design allows for replacing entire baffle if one decides to change out to different size/shape of mids and highs. In my case those big horns have got to go and maybe Santa will bring me some JBL 077 prism tweeters...
Structurely best I think I could be done....resonate this! 😉
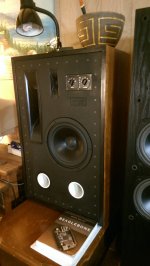
Not to step on your train of thought, but...
I built some 3 cubic ft.(net) Thiele/Small Tuned port boxes for 100W Audax PR240Z0, 10" Aerogel woofer (Fs-27Hz, Vas-3.23cu ft, Qts-.466) Design goal of F(3)-29Hz max.
Ext box size (19.5"wide 12.9"deep 30.6"high)
Used Medex (or equiv) formaldehyde free MDF: 3/4" sides & back
Baffle was of real concern due to use of large EV mid-horn 8HD/1823 (poor choice I regretted: PA horns....) So baffle design required much better than single ply 3/4"
That all said:
What I did was laminate (2) 1/2" sheets (oversize & no mill work yet), bonding the two sheets together using liberal amounts of Neopreme contact cement (both surfaces).
Issue with bonding material's spec for high applied psi requirement for proper bonding. Who has a large industrial press handy? No one!
Only solution was to protect laminate between 2 sacrafical sheets and Jack up the heaviest vehicle I could borrow and basically drive the weight of heavy front end over entire surface area. I Shi_ you not! I have pictures of driveway operation....& crazy old Cowboy. It drew a crowd.
The composite material I ended up with was sweet and did the trick with bracing & rubber 'gasket' between baffle and 1.5" wide recessed mounting frame/bracing and screws 2" apart entire periphery. Realize that I have luxury of all sizing, milling, holes and cutouts done on CNC equipment. Always use good quality polycarbonate glue, w water wetting material and clamping when gluing bracing to MDF, using crowns of bracing wood to your adavantage. This basic design allows for replacing entire baffle if one decides to change out to different size/shape of mids and highs. In my case those big horns have got to go and maybe Santa will bring me some JBL 077 prism tweeters...
Structurely best I think I could be done....resonate this! 😉
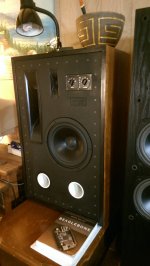
Last edited:
What I did was laminate (2) 1/2" sheets (oversize & no mill work yet), bonding the two sheets together using liberal amounts of Neopreme contact cement (both surfaces).
Issue with bonding material's spec for high applied psi requirement for proper bonding. Who has a large industrial press handy? No one!
A very simple and effective solution is the use of a vacuum pump. Not expensive, around 300$. Perfect for high psi lamination requirement.
I can send you a link in for the USA or for UK if desire.
Issue with bonding material's spec for high applied psi requirement for proper bonding. Who has a large industrial press handy? No one!
A very simple and effective solution is the use of a vacuum pump. Not expensive, around 300$. Perfect for high psi lamination requirement.
I can send you a link in for the USA or for UK if desire.
??? 😕
Yes, because Planet10 had given the correct response already, i refrained from commenting, but he is completely right.
For the same reason you can't make precise loudspeaker FR measurements from a listening distance in a live room, you can't make other fine measurements as well. Too many confounders.
The fact that it all will count up to something at the listening position is a very bad argument to do precision measurements at that location in order to tune or assess a loudspeaker. And I suppose that is not the way you measure either.
Last edited:
In order to get maximum damping we need to strongly shear a significant amount of damping material of appropriate properties. This is best done by following the "rules" of constrained layer damping which you have not done. This does not mean your approach is not an improvement on 1" thick MDF but it is not the best that can be done. This link from Andrex1965 a page or two earlier showed the measured improvements that can be expected by doing this using reasonably priced materials (avoiding branded damping material from a hi-fi shop will bring the price down further).What I did was laminate (2) 1/2" sheets (oversize & no mill work yet), bonding the two sheets together using liberal amounts of Neopreme contact cement (both surfaces).
Structurely best I think I could be done....resonate this! 😉
To some extent but I suspect how the driver is attached to the thin front baffle may have a significant influence. When the driver moves back and forth it is connected around the bolts. This will not only bend the baffle which is unconstrained around the hole but pull locally around the bolts putting the front baffle around the bolts in tension. A thicker front baffle will stiffen both these mechanisms even with close side panels.The driver is supported by relatively narrow sections of baffle that are heavily braced by the side walls. That should make a pretty stiff connection of the driver to the cabinet and limit energy transfer to the baffle, should it not?
As ever it is a question of where will the material do most good? Looking at the mode shapes of the lowest resonances it is usually clear where material needs to be added to stiffen things: where it cannot be placed. In the case of the front panel filling the hole would stiffen things up nicely.
In order to get maximum damping we need to strongly shear a significant amount of damping material of appropriate properties. This is best done by following the "rules" of constrained layer damping which you have not done. This does not mean your approach is not an improvement on 1" thick MDF but it is not the best that can be done. This link from Andrex1965 a page or two earlier showed the measured improvements that can be expected by doing this using reasonably priced materials (avoiding branded damping material from a hi-fi shop will bring the price down further).
Here's another link too a study of a very simple and non-expensive damping material: 30 roofing.
It offers great results, much better than bitumen pads.
The link for the explanations
Loudspeaker construction
And the graph of the results
http://www.silcom.com/~aludwig/images/panelvibes.gif
andy19191, here the measurements are made for a full enclosure, so the are much interesting than the previous link.
I've read with great attention the link given by Twinter damping factor values : damping factors
and recycled rubber seems to be really great. Easy to find in roll or in plate in different sizes and thickness, less expensive and more efficient than bitumen pads.
If you have never work with a vacuum pump, a link to see one in action. The easiest way to realize perfect homemade lamination. A bit more than 9 ton of pressure per square meter.
https://www.youtube.com/watch?v=WMnscjXGmTQ
Speaker manufacturers do measure it in detail using the method I gave earlier (measure vibration of whole cabinet and do some sums). It is a lot of work but here is an example of a one man speaker enterprise doing it. It is just about doable for DIYers but I have not seen anyone show results.If we could measure it in all its detail…
I think you need to be careful about reading the results. The author did not bond the damping material to the structural and constraining layers which is not going to work well particularly for stiffer damping materials. Getting a tight bond rather than a soft one is important when it comes to maximising the shearing of the damping material by the small bending motions in the structural and constraining layers. Also, why is a bit of fibreglass stuffing making those sort of differences particularly at low frequencies?Here's another link too a study of a very simple and non-expensive damping material: 30 roofing.
It offers great results, much better than bitumen pads.
The previous link showed unoptimised constrained layer damping working well for a panel. Good stuff even though the frequency resolution was insufficient to resolve the modes. I am not sure what can be read from your recent link with any confidence. I had seen it before but set it aside as not particularly useful with respect to constrained layer damping. Other sections were more useful.andy19191, here the measurements are made for a full enclosure, so the are much interesting than the previous link.
The thickness of the structural layer, damping layer and constraining layer all matter when it comes to optimising the damping. The damping effectiveness of a material also varies with frequency and mode shape. I don't think we can get too much from a single number in a table. I suspect one needs to work out the thickness of the structural layer, determine the lowest few resonant frequencies and mode shapes, check how well different grades and thicknesses of damping material work when constrained (on paper/computer) and then plump for one or two that look good to build and measure. I am pretty sure plenty of speaker companies will have done this but I am not aware of anything on the web. Anyone?I've read with great attention the link given by Twinter damping factor values : damping factors
and recycled rubber seems to be really great. Easy to find in roll or in plate in different sizes and thickness, less expensive and more efficient than bitumen pads.
That says a lot… i've seen lots of really nice FR plots you have done, what happens 40 dB down? How much is real signal and how much is noise masking the real signal (from say the box)?
dave
No need to get nasty ... No, I do not consider things below 40 dB down to be significant. Do you? And if so, based on what evidence.
And I suppose that is not the way you measure either.
Precisely, so what is your point?
- Home
- Loudspeakers
- Multi-Way
- The best cabinet material !!!!