I guess there is a problem. I count 12 poles on this one. My eyes can't be 'that' bad.
re; the rest of the points you bring up: I'll wait for others to chime in. Keep in mind that Volken is achieving best looking plots using his 3-phase PS. His is the same type of motor, but manufactured for European mains.
-Steve[/QUOTE]
Steve mine motor has also 12 poles this correct because it is a 4 pole hysteresis motor with 3 phase connection ! Speed is at 50Hz about 1440 rpm.
See the picture for a better understanding .
Volken
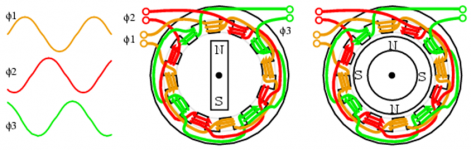
re; the rest of the points you bring up: I'll wait for others to chime in. Keep in mind that Volken is achieving best looking plots using his 3-phase PS. His is the same type of motor, but manufactured for European mains.
-Steve[/QUOTE]
Steve mine motor has also 12 poles this correct because it is a 4 pole hysteresis motor with 3 phase connection ! Speed is at 50Hz about 1440 rpm.
See the picture for a better understanding .
Volken
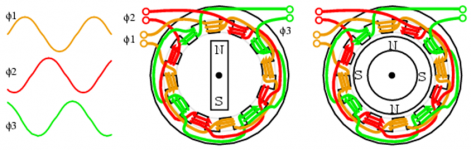
Motor types
Steve mine motor has also 12 poles this correct because it is a 4 pole hysteresis motor with 3 phase connection ! Speed is at 50Hz about 1440 rpm.
See the picture for a better understanding .
Volken
View attachment 402605[/QUOTE]
Thanks kevenkr and volken for answering sretin's observations. And thanks to sretin for bringing into focus just exactly what type of motor we are working with on this thread.
For my part I should have done more research up front to define this motor type from the outset. And I did not do that. Rather, I depended upon several anecdotal sources around the web that generally categorize this motor as a 3 phase. But I did not come up with any suitable references to support our assumptions. I'm happy to go with Volken's and kevenkr's replies on this matter.
How 'bout you, sretin. Any further observations?
-Steve
I guess there is a problem. I count 12 poles on this one. My eyes can't be 'that' bad.
re; the rest of the points you bring up: I'll wait for others to chime in. Keep in mind that Volken is achieving best looking plots using his 3-phase PS. His is the same type of motor, but manufactured for European mains.
-Steve
Steve mine motor has also 12 poles this correct because it is a 4 pole hysteresis motor with 3 phase connection ! Speed is at 50Hz about 1440 rpm.
See the picture for a better understanding .
Volken
View attachment 402605[/QUOTE]
Sreten, The standard E50 motor in a TD-124 is a shaded pole induction motor and my understanding has always been that the replacement Papst motor is a 3 phase induction motor as well - not fully synchronous. Speed is load dependent, and an eddy current brake is used to set the speed. The Garrard 301 and 401 used shaded pole induction motors with eddy current brakes as well. (I have a 401, and spare motor, as well as two running TD-124s)
There are a lot of people in Germany and elsewhere running 3 phase power to Papst motors in EMT tables and TD-124s retrofitted with the Papst. I assume they know what they are doing.
I'm quite interested in the Papst, although its noise performance concerns me a bit. (And they are expensive to acquire and relatively rare.)
I've measured other Papst turntable motors for a couple friends, and these were all delta wound 3 phase motors. (3 wire, same dcr any wire to any other wire)
Thanks kevenkr and volken for answering sretin's observations. And thanks to sretin for bringing into focus just exactly what type of motor we are working with on this thread.
For my part I should have done more research up front to define this motor type from the outset. And I did not do that. Rather, I depended upon several anecdotal sources around the web that generally categorize this motor as a 3 phase. But I did not come up with any suitable references to support our assumptions. I'm happy to go with Volken's and kevenkr's replies on this matter.
How 'bout you, sretin. Any further observations?
-Steve
cold start times and capacitor values
It occurred to me that when I started messing around with cap values that I could alter timing such that it could affect not only motor roughness, but also power output.
I've no means to measure power output from this motor but I can observe start-up times from when the motor is cold to when the motor is at correct speed.
When I had a capacitor value of 1.43 uF I achieved what I subjectively thought was smoothest running.* However, after all the excitement wore off I began to notice that the TD124 was taking an abnormal amount of time to get up to speed from a cold start-up.
Today, I thought I would try another cap value to see if this might improve start times. It did. I went with the Thorens recommended value, 1.5uF. After removing the previous (1.43uF)cap group and replacing it with the single 1.5uF cap I observed what I'd call a normal start time for an E50 powered unit operating on the mains at my place. About 5 seconds to get a speed I'd be willing to start playing a record at but still slightly slow. About 40 seconds total until the strobe holds steady.
Listening. I perceive no difference between this setting and what I heard with the previous (1.43uF) cap timing. This brings up some other questions about my history with this motor, but for now I'm just happy to have what appears to be normal operation.
-Steve
*(stethescope observation. See earlier post where I itemize my observations while trying 5 different cap values. post #11.)
It occurred to me that when I started messing around with cap values that I could alter timing such that it could affect not only motor roughness, but also power output.
I've no means to measure power output from this motor but I can observe start-up times from when the motor is cold to when the motor is at correct speed.
When I had a capacitor value of 1.43 uF I achieved what I subjectively thought was smoothest running.* However, after all the excitement wore off I began to notice that the TD124 was taking an abnormal amount of time to get up to speed from a cold start-up.
Today, I thought I would try another cap value to see if this might improve start times. It did. I went with the Thorens recommended value, 1.5uF. After removing the previous (1.43uF)cap group and replacing it with the single 1.5uF cap I observed what I'd call a normal start time for an E50 powered unit operating on the mains at my place. About 5 seconds to get a speed I'd be willing to start playing a record at but still slightly slow. About 40 seconds total until the strobe holds steady.
Listening. I perceive no difference between this setting and what I heard with the previous (1.43uF) cap timing. This brings up some other questions about my history with this motor, but for now I'm just happy to have what appears to be normal operation.
-Steve
*(stethescope observation. See earlier post where I itemize my observations while trying 5 different cap values. post #11.)
E50 Motor -Papst motor Speed
The following measurements are between the two motors and the dependence from mains voltage and frequency
Default 220 Volt , 50 Hz ref. 0 % at 33T , single phase supply !
E 50 Motor Papst motor
220 > 225 Volt + 0,25% +0,4%
230 Volt + 0,4% + 0,73 %
235 Volt + 0,6% + 1,25 %
240 Volt + 0,75 % + 1,25 %
220 < 215 Volt - 0,25% - 0,4 %
210 Volt - 0,54 % - 0,77%
205 Volt - 0,8 % -1,2 %
Freq.
50 > 50,1 Hz + 0,25% +0,25 %
50,2 Hz + 0,42 % + 0,41 %
50,3 Hz + 0,63 % + 0,58%
50 < 49,9 Hz - 0,15% - 0,2 %
49,8 Hz - 0,33% - 0,72 %
49,7 Hz - 0,54 % - 0,95 %
The speed from both motors are dependent from mains voltage and frequency and load off course.
Volken
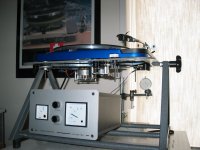
The following measurements are between the two motors and the dependence from mains voltage and frequency
Default 220 Volt , 50 Hz ref. 0 % at 33T , single phase supply !
E 50 Motor Papst motor
220 > 225 Volt + 0,25% +0,4%
230 Volt + 0,4% + 0,73 %
235 Volt + 0,6% + 1,25 %
240 Volt + 0,75 % + 1,25 %
220 < 215 Volt - 0,25% - 0,4 %
210 Volt - 0,54 % - 0,77%
205 Volt - 0,8 % -1,2 %
Freq.
50 > 50,1 Hz + 0,25% +0,25 %
50,2 Hz + 0,42 % + 0,41 %
50,3 Hz + 0,63 % + 0,58%
50 < 49,9 Hz - 0,15% - 0,2 %
49,8 Hz - 0,33% - 0,72 %
49,7 Hz - 0,54 % - 0,95 %
The speed from both motors are dependent from mains voltage and frequency and load off course.
Volken
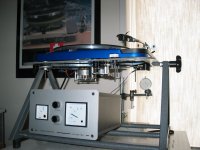
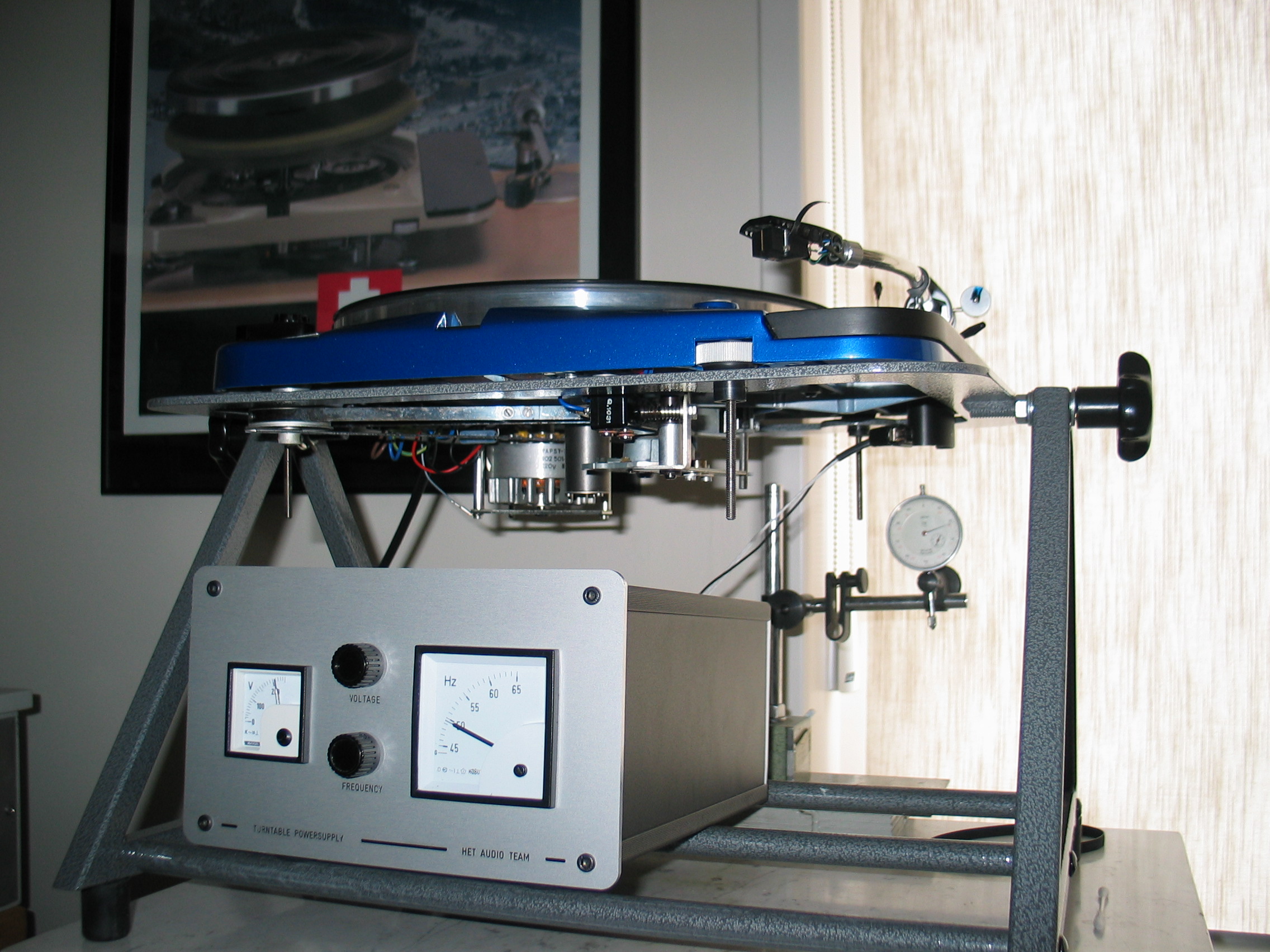
that is a nifty single phase power supply. Adjustable for both frequency and voltage. I like. I want😀.
I really like the service jig in that photo. It looks as if you guys are 'well tooled' for servicing the TD124.
The following measurements are between the two motors and the dependence from mains voltage and frequency
Default 220 Volt , 50 Hz ref. 0 % at 33T , single phase supply !
E 50 Motor Papst motor
220 > 225 Volt + 0,25% +0,4%
230 Volt + 0,4% + 0,73 %
235 Volt + 0,6% + 1,25 %
240 Volt + 0,75 % + 1,25 %
220 < 215 Volt - 0,25% - 0,4 %
210 Volt - 0,54 % - 0,77%
205 Volt - 0,8 % -1,2 %
Freq.
50 > 50,1 Hz + 0,25% +0,25 %
50,2 Hz + 0,42 % + 0,41 %
50,3 Hz + 0,63 % + 0,58%
50 < 49,9 Hz - 0,15% - 0,2 %
49,8 Hz - 0,33% - 0,72 %
49,7 Hz - 0,54 % - 0,95 %
The speed from both motors are dependent from mains voltage and frequency and load off course.
Volken
I think I understand the above collumns. 1) speed dependency at various voltage inputs. 2) speed dependency at various frequency inputs. Left %value is E50. Right %value is Papst.
If so, this is very useful because I've been having thoughts of acquiring a frequency generator type of PS to power my various TD124 players. Those values suggest that both voltage and frequency have a fractional impact on actual motor speed ....... but any fraction larger than .25% is something we will see while watching the strobe window on the Thorens. And it is noted that the Papst repeatedly indicates a higher amount of sensitivity to the voltage inputs than does the E50. Also the papst shows some sensitivity to frequency input, particularly when frequency is less than the nominal value.
And actual speed seems to be represented as a percentage of deviation from the nominal 33-1/3rd rpm.
The other factor, load, is not given any values, but we know it plays a significant part in the whole. And part of the "load" imposed on this is the eddy brake which can be load adjusted as a means of speed pitch control.
One significant factor that will happen in the North American power grid. Frequency output is no longer fastidiously maintained as it once was. The reason is that there is less dependence on mains frequency now than in the past. These days, time keeping mechanisms tend to have their regulators (quartz oscillators) on board the clock. Where in the past it was the mains frequency that regulated the synchronous clock motors in those large wall clocks we used to have in all public institutions. Those times are long gone afik.
So now it is becoming clear that if we are to maintain these antiquated mechanisms (synchronous record player motors...and tt motors that have at least 'some' sensitivity to mains frequency...), there is a need to provide an alternate means of speed regulation for both voltage and frequency. $$$ ouch.
Yet, currently, I am able to regulate voltage by manually switching between output levels on my two Viz Isotap isolated power supply units. Voltage only. I suspect, however, that the building I'm in may be subject to power drops at times of high load to the local grid. (Like when everyone in the same building gets home from work)
-Steve
Note that line operated strobes are no longer accurate when the line frequency isn't correct, if I am thinking about it correctly you won't know it at all from the strobe since it and the motor are both operating from the line frequency. An independent strobe not dependent on line frequency would show the speed discrepancy, the line operated strobe would not. (If I understand correctly)
Right. 'forgot about that. A definite and disturbing loss of certainty.
Now I really know I need a specialized TT ps.
-Steve
Now I really know I need a specialized TT ps.
-Steve
Last edited:
Service bulletin No. 23
Shortly after the introduction of the Pabst motor by Thorens (Bolex) with Service bulletin No. 22, there was another service bulletin issued the following year.
That was No. 23. I can't find a copy of that around the net anymore but we do have some documentation of it in Joachim Bung's book "Swiss Precision". See pages 256 - 257. Bung translates and condenses the message to indicate that Thorens had received enough feedback from actual use of the motor in the field that some motors had been delivered with the wrong lube. That these motors affected tended to come up to speed abnormally slow. It continued to suggest that the solution to this slow start-up speed could be alleviated by changing out the lube to the proper stuff. But I can't find out what the "proper lube" was supposed to be. Bung doesn't tell us. Perhaps a copy of service bulletin No 23 will show up and supply us with this critical information. Who knows.
This demands comparison to some of my complaints about slow start speeds in earlier posts this thread. Up until that point I had tried, with some success, to improve cold start speeds by using a different cap value. But over the days to come I had noticed that start-up speed was still less than acceptable. There is a difference between letting the motor cool off for an hour or two and letting it sit over night when room temperatures reach as low as 68 deg. F.
I had been using the Thorens recommended lube in this motor. But now it occurred to me that a lube with a thinner viscosity might be tried. But what viscosity would that be? not knowing I thought to try a multi-viscosity automotive oil. Mobile-1. 5w/30w. All I did was wipe out the bushing bore in the papst with paper towels and Q-tips, then replace liberally with the Mobil-1. This doesn't take long with the Papst. And unlike the E50, there is no need to adjust anything upon re-assembly. Just assemble and go.
Strobe window watching.
Did the thinner oil make a difference in start-up times? Yeah. But it is not the total answer here. For instance; if I set the voltage output on the Isotap to 125V, I get a quick start-up from cold. Like within less than 15 seconds the strobe indicates only slightly slower than nominal. Maybe a fraction of a percent off. But over the next several seconds that changes and the motor and drive train begin to warm up....and speed up. Within a minute, I find that pitch adjustment (eddy brake) isn't enough to hold nominal speed. So I switch the Isotap output down to 120V. That seems to hold nominal momentarily, then speed increases slowly. So, ultimately, I find that when I switch the Isotap to 115V I have a speed that is somewhere near the center of pitch-adjust range. And this holds for the rest of the session, or all day.
So my method of operation is to operate the TD124 (with Papst) through the Viz Isotap. Using this I have a means of maintaining acceptable operating speed. Without it, I'd be stuck with 115V at the mains and slow cold start-up times. Regardless of which lubes I'm using.
Other notes; The rest of the drive train appears to be at or near optimal condition.
The step pulley spins quite freely when the belt is removed. So does the idler wheel. And the idler wheel has the standard issue thrust washer at its bottom. No evidence of wear. Idler wheel to step pulley has good height adjustment so that the wheel is in the middle of the stepped pulley surface at all speeds.
Platter bearing is in very good condition. I did replace the bushing sleeves with new ones. Clearance between shaft and bushing appears optimal with evidence of free spin but no evidence of excessive slop. Example a dial indicator at the platter rim indicates less than .001 inches of vertical wobble.
Eddy brake adjustment. It is possible to adjust the gap between the magnet and the step pulley. I can do this with some precision simply by using a pair of gage pins (placed at either end of the arc) to stabilize position of the magnet while I operate the clamping screw that holds magnet position. I've tried using different gap values. And this does have some affect on how much load the eddy brake imposes upon the stepped pulley as it spins. At first I had it adjusted close by using folds of note paper (about .020 thick) at either end of the arc on the magnet. Then I tried opening this gap distance to .060 inches using a couple of .060 gage pins. Then I tried even larger gap distances, next going to .078 inches, then out to .125 inches. All this does affect the amount of influence the eddy brake imposes. But it is not a magic bullet. Currently I have it adjusted so that one end (the entry end) of the arc is open at .125, while the other end of the arc is adjusted to .060. This, I conjectured, would broaden the eddy brake load adjustment range, while not reducing its ultimate load.
Result: not a magic bullet, but it may be a usable adjustment for the eddy brake.
And yet I keep coming back to this as a power supply issue, or so I think.
-Steve
Shortly after the introduction of the Pabst motor by Thorens (Bolex) with Service bulletin No. 22, there was another service bulletin issued the following year.
That was No. 23. I can't find a copy of that around the net anymore but we do have some documentation of it in Joachim Bung's book "Swiss Precision". See pages 256 - 257. Bung translates and condenses the message to indicate that Thorens had received enough feedback from actual use of the motor in the field that some motors had been delivered with the wrong lube. That these motors affected tended to come up to speed abnormally slow. It continued to suggest that the solution to this slow start-up speed could be alleviated by changing out the lube to the proper stuff. But I can't find out what the "proper lube" was supposed to be. Bung doesn't tell us. Perhaps a copy of service bulletin No 23 will show up and supply us with this critical information. Who knows.
This demands comparison to some of my complaints about slow start speeds in earlier posts this thread. Up until that point I had tried, with some success, to improve cold start speeds by using a different cap value. But over the days to come I had noticed that start-up speed was still less than acceptable. There is a difference between letting the motor cool off for an hour or two and letting it sit over night when room temperatures reach as low as 68 deg. F.
I had been using the Thorens recommended lube in this motor. But now it occurred to me that a lube with a thinner viscosity might be tried. But what viscosity would that be? not knowing I thought to try a multi-viscosity automotive oil. Mobile-1. 5w/30w. All I did was wipe out the bushing bore in the papst with paper towels and Q-tips, then replace liberally with the Mobil-1. This doesn't take long with the Papst. And unlike the E50, there is no need to adjust anything upon re-assembly. Just assemble and go.
Strobe window watching.
Did the thinner oil make a difference in start-up times? Yeah. But it is not the total answer here. For instance; if I set the voltage output on the Isotap to 125V, I get a quick start-up from cold. Like within less than 15 seconds the strobe indicates only slightly slower than nominal. Maybe a fraction of a percent off. But over the next several seconds that changes and the motor and drive train begin to warm up....and speed up. Within a minute, I find that pitch adjustment (eddy brake) isn't enough to hold nominal speed. So I switch the Isotap output down to 120V. That seems to hold nominal momentarily, then speed increases slowly. So, ultimately, I find that when I switch the Isotap to 115V I have a speed that is somewhere near the center of pitch-adjust range. And this holds for the rest of the session, or all day.
So my method of operation is to operate the TD124 (with Papst) through the Viz Isotap. Using this I have a means of maintaining acceptable operating speed. Without it, I'd be stuck with 115V at the mains and slow cold start-up times. Regardless of which lubes I'm using.
Other notes; The rest of the drive train appears to be at or near optimal condition.
The step pulley spins quite freely when the belt is removed. So does the idler wheel. And the idler wheel has the standard issue thrust washer at its bottom. No evidence of wear. Idler wheel to step pulley has good height adjustment so that the wheel is in the middle of the stepped pulley surface at all speeds.
Platter bearing is in very good condition. I did replace the bushing sleeves with new ones. Clearance between shaft and bushing appears optimal with evidence of free spin but no evidence of excessive slop. Example a dial indicator at the platter rim indicates less than .001 inches of vertical wobble.

Eddy brake adjustment. It is possible to adjust the gap between the magnet and the step pulley. I can do this with some precision simply by using a pair of gage pins (placed at either end of the arc) to stabilize position of the magnet while I operate the clamping screw that holds magnet position. I've tried using different gap values. And this does have some affect on how much load the eddy brake imposes upon the stepped pulley as it spins. At first I had it adjusted close by using folds of note paper (about .020 thick) at either end of the arc on the magnet. Then I tried opening this gap distance to .060 inches using a couple of .060 gage pins. Then I tried even larger gap distances, next going to .078 inches, then out to .125 inches. All this does affect the amount of influence the eddy brake imposes. But it is not a magic bullet. Currently I have it adjusted so that one end (the entry end) of the arc is open at .125, while the other end of the arc is adjusted to .060. This, I conjectured, would broaden the eddy brake load adjustment range, while not reducing its ultimate load.
Result: not a magic bullet, but it may be a usable adjustment for the eddy brake.
And yet I keep coming back to this as a power supply issue, or so I think.
-Steve
Last edited:
My basement listening room in winter hardly ever makes it to 68F, low 60s is about it. I have adjusted the eddy current brakes on both of my tables so that they maintain correct speed when the table in question is fully warmed up. I currently have two fully functional TD-124s and in winter they can take 30 minutes to get to full speed, but are sufficiently close to correct speed after a few minutes of warm up. As long as I resist the temptation to adjust the speed they are both very consistent and once warm regardless of ambient temps run at a consistent speed. In the summer months they are locked within a couple of minutes, this time of the year I give them five minutes of running time before I play my first record so the pitch is not noticeably off.
Lubricants used in the motor and main bearing seem to have a pretty significant bearing on speed stability and warm up time. Initially I used a lighter modern lubricant in my late TD-124/II and regardless of position I could not get the table to run at the correct speed when fully warm, the magnet was within 0.020" of the stepped pulley and the eddy current brake was unable to regulate the speed. Interestingly enough going to 20wt oil across the board solved this problem. I suspect that 30wt in hot climates in the main bearing would allow less aggressive setting of the distance between the magnet and the pulley by virtue of the increased drag - in a climate like mine sans AC that is not going to fly.
By the time I got to the older TD-124 I had learned enough that I had few problems getting it to run on speed.
I adjust the speed settings on these tables very infrequently, on the TD-124/II the last time I made an adjustment was about a year ago, the older unit gets more use and I resist the urge to adjust it to run on speed as I then have to readjust it later.. So I just wait, untouched it too is quite consistent over time.
Incidentally I have experimented with angling the magnet and I don't think it makes any difference at all, what matters is the average distance of the magnet from the pulley. It makes sense as it is the average intensity of the magnetic field across its length that determines how much bucking field can be generated in the pulley. The internal L bracket determines the field strength which is maximum when the bracket edge is parallel to the magnet.
The Papst must be a bit short on torque compared to the E50 as my problem has always been with them running too fast when warmed up..
Some have alleged that the Papst is a hysteresis synchronous motor and if that is the case it may make more sense to run it with a variable frequency three phase sine wave drive and dispense altogether with the brake.. The motor will then run synchronously and as long as the demand for torque is not excessive it will remain locked to the line frequency. (Otherwise it slips poles which reduces available torque a bit IIRC.) AC motor - Wikipedia, the free encyclopedia
Lubricants used in the motor and main bearing seem to have a pretty significant bearing on speed stability and warm up time. Initially I used a lighter modern lubricant in my late TD-124/II and regardless of position I could not get the table to run at the correct speed when fully warm, the magnet was within 0.020" of the stepped pulley and the eddy current brake was unable to regulate the speed. Interestingly enough going to 20wt oil across the board solved this problem. I suspect that 30wt in hot climates in the main bearing would allow less aggressive setting of the distance between the magnet and the pulley by virtue of the increased drag - in a climate like mine sans AC that is not going to fly.
By the time I got to the older TD-124 I had learned enough that I had few problems getting it to run on speed.
I adjust the speed settings on these tables very infrequently, on the TD-124/II the last time I made an adjustment was about a year ago, the older unit gets more use and I resist the urge to adjust it to run on speed as I then have to readjust it later.. So I just wait, untouched it too is quite consistent over time.
Incidentally I have experimented with angling the magnet and I don't think it makes any difference at all, what matters is the average distance of the magnet from the pulley. It makes sense as it is the average intensity of the magnetic field across its length that determines how much bucking field can be generated in the pulley. The internal L bracket determines the field strength which is maximum when the bracket edge is parallel to the magnet.
The Papst must be a bit short on torque compared to the E50 as my problem has always been with them running too fast when warmed up..
Some have alleged that the Papst is a hysteresis synchronous motor and if that is the case it may make more sense to run it with a variable frequency three phase sine wave drive and dispense altogether with the brake.. The motor will then run synchronously and as long as the demand for torque is not excessive it will remain locked to the line frequency. (Otherwise it slips poles which reduces available torque a bit IIRC.) AC motor - Wikipedia, the free encyclopedia
Having a setup like Volken's would certainly have made my life easier at some points. I've serviced about a half dozen of these tables excluding my own without such aids..
My experience with the E50 is very close to your description. In Winter it can take its sweet time getting up to speed, but once set the experience repeats accurately.
re; Papst. I'm running low on enthusiasm about now. In the meantime I'll start preparing the E50 that came with this chassis as the proper motor to have. I just have to procure some MkII grommets and posts to get this thing working.
Failing a purpose-built 3-phase supply, I don't see the Papst having much future in my listening room
-Steve
re; Papst. I'm running low on enthusiasm about now. In the meantime I'll start preparing the E50 that came with this chassis as the proper motor to have. I just have to procure some MkII grommets and posts to get this thing working.
Failing a purpose-built 3-phase supply, I don't see the Papst having much future in my listening room
-Steve
That's a shame, and I have no first hand experience to relate it to, but that does seem to be the general consensus amongst the cognoscenti that the Papst is a step backwards performance wise.. If truly a hysteresis synchronous motor it certainly makes little sense to use it with the eddy current brake, but it otherwise does not run at the right speed as the TD-124 was not designed with a synchronous motor in mind, shaded pole induction motors generally run slower than synchronous motors by a few %. (Custom motor pulley might solve this issue, but you would have no way of adjusting the speed, one of the 124's charms and liabilities IMO)
That's a shame, and I have no first hand experience to relate it to, but that does seem to be the general consensus amongst the cognoscenti that the Papst is a step backwards performance wise.. If truly a hysteresis synchronous motor it certainly makes little sense to use it with the eddy current brake, but it otherwise does not run at the right speed as the TD-124 was not designed with a synchronous motor in mind, shaded pole induction motors generally run slower than synchronous motors by a few %. (Custom motor pulley might solve this issue, but you would have no way of adjusting the speed, one of the 124's charms and liabilities IMO)
I should point out that the eddy brake pitch adjuster does function with the Papst. My complaint, so far, is that I'm not at all happy with how slowly the motor reaches correct operating speed from a cold start. Otherwise, it appears to be interchangeable with the E50.
Soundwise, it might be fair to say that the papst, with its double gromment motor mounting arrangement, may be comparable to a mk1 E50 with the single grommet motor isolation. Maybe even slightly quieter. No hint of audible rumble. SQ seems to take on a "dark" presentation. Good atmospherics. But not entirely missing fine detail. It is good.
Very pleasant to listen to but "veiled". Good rhythmic delivery. Definitely a toe tapper. But is there more energy delivery than with E50 power? Not so much as to make it a definite winner. At least not in my limited experience.
Would you like to play with it?
-Steve
I should point out that the eddy brake pitch adjuster does function with the Papst. My complaint, so far, is that I'm not at all happy with how slowly the motor reaches correct operating speed from a cold start. Otherwise, it appears to be interchangeable with the E50.
Soundwise, it might be fair to say that the papst, with its double gromment motor mounting arrangement, may be comparable to a mk1 E50 with the single grommet motor isolation. Maybe even slightly quieter. No hint of audible rumble. SQ seems to take on a "dark" presentation. Good atmospherics. But not entirely missing fine detail. It is good.
Very pleasant to listen to but "veiled". Good rhythmic delivery. Definitely a toe tapper. But is there more energy delivery than with E50 power? Not so much as to make it a definite winner. At least not in my limited experience.
Would you like to play with it?
-Steve
At some point I would definitely be interested in messing around with the Papst. I might be able to come up with a single phase drive fairly easily and that might answer the question about synchronous operation or not.. ..
In terms of eddy current brake based operation a hysteresis synchronous motor will slip based on load but torque output suffers which I am wondering if that is part of the problem..
I was always impressed by the look of the luxman table.
Just a elegant class act.
Don,t know anything about how they were constructed though.
Regards
David
Just a elegant class act.
Don,t know anything about how they were constructed though.
Regards
David
Steve, I attempted to reply to your email, but I got two bounces.. Will check on your site for an alternate email addy, otherwise please send me another email address and I will reply.. Thanks! 😀
Steve, I attempted to reply to your email, but I got two bounces.. Will check on your site for an alternate email addy, otherwise please send me another email address and I will reply.. Thanks! 😀
Ooops. My email listed was out of date. I just updated that. I did get your email you sent using my website addy. Look for my reply to that one.
-Steve
- Home
- Source & Line
- Analogue Source
- new project: TD124 with the Papst motor