My building materials are slowly arriving and soon it's time to start the practical work on the panels.
I have an idea but I'm not sure how to actually build it?
Perforated steel stators, 3m VHB tape spacer, mylar diaphragm.
How can I make holes that go all the way through?
(2x steel stators, 2x VHB tape, 1x mylar diaphragm)
I need something like 8mm diameter holes. I'll probably use M8 nylon screws.
I have an idea but I'm not sure how to actually build it?
Perforated steel stators, 3m VHB tape spacer, mylar diaphragm.
How can I make holes that go all the way through?
(2x steel stators, 2x VHB tape, 1x mylar diaphragm)
I need something like 8mm diameter holes. I'll probably use M8 nylon screws.
Hi,
perforated metal features tens of thousands of holes 😛....why and what for do You need additional holes?? Certainly not to hold things together.
jauu
Calvin
perforated metal features tens of thousands of holes 😛....why and what for do You need additional holes?? Certainly not to hold things together.
jauu
Calvin
A beautiful thing about using 3M foam tape for the spacers is that it also sticks and holds the panels together quite well-- so you won't need any fasteners. For example:
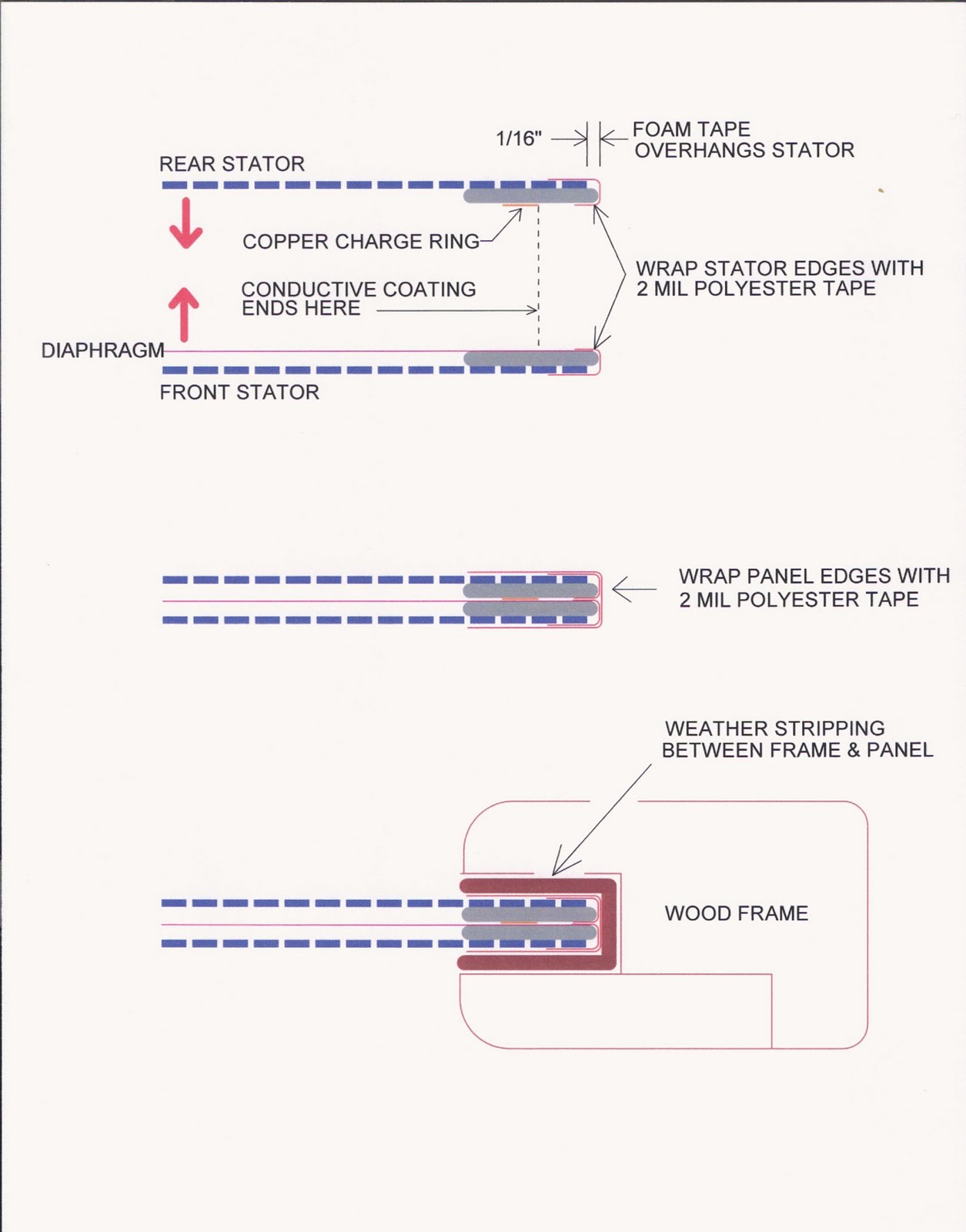
Last edited:
Hi CharlieM,
From your picture, what is a weather stripping?
Wachara C.
It's basically a medium density closed cell synthetic foam rubber material (silicone or other rubber-like material). It serves to isolate the panel from the frame, both acoustically and electrically.
Calvin> I'm thinking about a super simple frameless mounting system.
It might be a moot point if the frame is needed for stability?
Holes in the diaphram will introduce stress concentration points but bolts running through the entire structure will recuce shear stress.
CharlieM> If a frame is needed, your pictures solves most issues. Finding suitable PE-tape and weather stripping might be the hard part? How good is the insulation?
Is it good enough that you could use a metal frame instead of a wooden one?
It might be a moot point if the frame is needed for stability?
Holes in the diaphram will introduce stress concentration points but bolts running through the entire structure will recuce shear stress.
CharlieM> If a frame is needed, your pictures solves most issues. Finding suitable PE-tape and weather stripping might be the hard part? How good is the insulation?
Is it good enough that you could use a metal frame instead of a wooden one?
MarkusA,
I use 3M brand foam tape exclusively. I believe I used either 3M #4008 or #4016 tape in 1/16" (1.5mm) thickness on my latest panels. I think any of the 3M #4000 series tapes with acrylic adhesive would work fine. Here the 3M data sheet: http://multimedia.3m.com/mws/mediawebserver?66666UuZjcFSLXTtnxM658s6EVuQEcuZgVs6EVs6E666666--
Certainly, with appropriate insulation, you could use a metal frame (Martin Logan does). I used wood because it's cheap, readily available, easy to work with and cosmetically appealing. Completely dried wood would have no electrical conductivity at all but to the extent that it absorbs humidity it can become somewhat conductive. Still, I would think that a good stator coating alone would suffice in a wooden frame but some additional electrical insulation can't hurt. Additionally, I always use a medium density synthetic foam rubber cushion (weatherstripping) between the frame and stator for acoustic insulation because the ESL panel vibrates quite a bit when playing and we don't want the panel rattling against the frame or conducting vibrations into it.
I use 3M brand foam tape exclusively. I believe I used either 3M #4008 or #4016 tape in 1/16" (1.5mm) thickness on my latest panels. I think any of the 3M #4000 series tapes with acrylic adhesive would work fine. Here the 3M data sheet: http://multimedia.3m.com/mws/mediawebserver?66666UuZjcFSLXTtnxM658s6EVuQEcuZgVs6EVs6E666666--
Certainly, with appropriate insulation, you could use a metal frame (Martin Logan does). I used wood because it's cheap, readily available, easy to work with and cosmetically appealing. Completely dried wood would have no electrical conductivity at all but to the extent that it absorbs humidity it can become somewhat conductive. Still, I would think that a good stator coating alone would suffice in a wooden frame but some additional electrical insulation can't hurt. Additionally, I always use a medium density synthetic foam rubber cushion (weatherstripping) between the frame and stator for acoustic insulation because the ESL panel vibrates quite a bit when playing and we don't want the panel rattling against the frame or conducting vibrations into it.
Last edited:
I guess one could say I have a fair understanding about materials?
However I do tend to overthink problems and I'm always looking for the perfect solution. Sometimes I need to relax, take a step back and go with "good enough". 🙂
In this instance the key words might be "panel ratteling" and "vibrations".
Will I need the frame? Is the frame important?
It will add mass, rigidity and it might change resonance behavior as well.
The panels will be 165x25cm (160x20cm actual active membrane area).
I'll be using 1.0mm Rv 3-4 perf steel stators.
3M 1.6x25mm VHB tape (I'm considering 1.1mm thickness)
(25mm 5962 or 5952 since the stators will be powdercoated)
I'm not decided on the additional tape spacers needed, width and orientation will depend on the thickness of the tape.
I'll try to run them as low as possible (hybrid) without compromising the audiable qualities to badly. X-over <300Hz I think? Exactly how low depends on the final result and I won't know that until the panels are built.
Will the vibrations be large enough to warrant a frame?
And now back to the original question.
I could do it without the extra holes but holes will make a better solution I think.
I need 2 holes for M8 screws on each side (L/R) for each panel. The stands will be mounted near the floor so the holes will need to be located a few inches above floor level.
However I do tend to overthink problems and I'm always looking for the perfect solution. Sometimes I need to relax, take a step back and go with "good enough". 🙂
In this instance the key words might be "panel ratteling" and "vibrations".
Will I need the frame? Is the frame important?
It will add mass, rigidity and it might change resonance behavior as well.
The panels will be 165x25cm (160x20cm actual active membrane area).
I'll be using 1.0mm Rv 3-4 perf steel stators.
3M 1.6x25mm VHB tape (I'm considering 1.1mm thickness)
(25mm 5962 or 5952 since the stators will be powdercoated)
I'm not decided on the additional tape spacers needed, width and orientation will depend on the thickness of the tape.
I'll try to run them as low as possible (hybrid) without compromising the audiable qualities to badly. X-over <300Hz I think? Exactly how low depends on the final result and I won't know that until the panels are built.
Will the vibrations be large enough to warrant a frame?
And now back to the original question.
I could do it without the extra holes but holes will make a better solution I think.
I need 2 holes for M8 screws on each side (L/R) for each panel. The stands will be mounted near the floor so the holes will need to be located a few inches above floor level.
Instead of starting a separate thread...
Since you have my info above, what do you think about spacer thickness?
Should I stick with 1.6mm or should I go with 1.1mm?
It's a hybrid design and I'll be adding separate bass units.
Since you have my info above, what do you think about spacer thickness?
Should I stick with 1.6mm or should I go with 1.1mm?
It's a hybrid design and I'll be adding separate bass units.
I will give you my opinions but I would seek other opinions as well:
Will I need the frame? Is the frame important?
A flat panel would be quite wimpy and would definitely need a supporting frame. A curved panel would be substantially more rigid but I can't imagine it being strong enough to resist flexing and deformation when handling it so I would use a frame with a curved panel as well.
It will add mass, rigidity and it might change resonance behavior as well.
Yes, all of those things-- but I assure you it will sound wonderful. I think resonance in the panel is not a good thing and a frame can help beneficially dampen that resonance
The panels will be 165x25cm (160x20cm actual active membrane area).
I'll be using 1.0mm Rv 3-4 perf steel stators.
The perf you mentioned should work well. You're panels are large so will surely yield high output but they will also have fairly high capacitance-- it would probably be OK but I'm not positive about that and too much capacitance will pull down the treble response and makes a harder load for an amp (the tranny type and step-up ratio plays into that as well). Calvin has far more experience than I do with capacitance issues so I would certainly ask his advice before committing to that panel size.
3M 1.6x25mm VHB tape (I'm considering 1.1mm thickness)
(25mm 5962 or 5952 since the stators will be powdercoated)
I'm not decided on the additional tape spacers needed, width and orientation will depend on the thickness of the tape.
I would definitely go with 1.6 mm tape for the spacers, no matter the panel coating thickness. My view is this: In a perfect world where stators are always perfectly straight and diaphragms retain perfect tension, 1 mm of d/s (diaphragm to stator spacing) might be fine provided that the distance between support spacers does not exceed 100x d/s (70-100x d/s is the Cookbook guidline). However, I have yet to see perfectly straight and true stators, even after straightening. Also, even though you will have separate woofers for the bass, the bass notes in the room will push the diaphragms to larger excursions than the signals fed to the stators. Roger Sanders's Cookbook recommends .070" minimum d/s and I think he's not far off the mark with that so I go with .062 (1.6mm) spacers.
I'll try to run them as low as possible (hybrid) without compromising the audiable qualities to badly. X-over <300Hz I think? Exactly how low depends on the final result and I won't know that until the panels are built.
A 24/db/oct crossover @ 300 hz would be fine but I would not go higher or much lower. Mine is currently set to 270hz (lower is certainly doable but you then need more EQ on the panels to compensate the dipole phase-cancellation so it's a matter of diminishing returns).
Will the vibrations be large enough to warrant a frame?
For vibration alone, probably not, but I would use a frame anyway for structural rigidity.
And now back to the original question.
I could do it without the extra holes but holes will make a better solution I think.
I need 2 holes for M8 screws on each side (L/R) for each panel. The stands will be mounted near the floor so the holes will need to be located a few inches above floor level.
Since I would use VHB tape to assemble and secure the panels together and also place the panel in a support frame, screws and added holes would not be needed.
Last edited:
Thanks for the detailed response.
My initial thoughts were 1.6mm spacers and a frame so your advice is kind of already the default plan.
I guess I'm just exploring another option. 🙂
A 1mm steel sheet is indeed very flimsy, I was thinking the layered build with tape would transfer any bending motion/force into shear forces making the construction stiff.
Yoy're probably right, a frame is probably the way to go. 🙂
(Swedish terminology might not translate 100%, if I'm saying strange things please tell me and I'll try to find the correct words.)
My initial thoughts were 1.6mm spacers and a frame so your advice is kind of already the default plan.
I guess I'm just exploring another option. 🙂
A 1mm steel sheet is indeed very flimsy, I was thinking the layered build with tape would transfer any bending motion/force into shear forces making the construction stiff.
Yoy're probably right, a frame is probably the way to go. 🙂
(Swedish terminology might not translate 100%, if I'm saying strange things please tell me and I'll try to find the correct words.)
I might just add a little side note...
It was the free samples of 1.1mm (43mil) VHB that got me thinking if it would be a viable option to go with the smaller d/s spacing. (I got a couple of sample rolls to try out the product...)
It was the free samples of 1.1mm (43mil) VHB that got me thinking if it would be a viable option to go with the smaller d/s spacing. (I got a couple of sample rolls to try out the product...)
I might just add a little side note...
It was the free samples of 1.1mm (43mil) VHB that got me thinking if it would be a viable option to go with the smaller d/s spacing. (I got a couple of sample rolls to try out the product...)
As I said in my earlier post, I think you should seek other opinions, not just mine.
Since I have not personally built an ESL with d/s spacing smaller than .062" (1.6mm) I can't say for sure that 1.1 mm spacing would create problems, provided that the distance between support spacers is within the 70-100x d/s guideline per Roger Sanders' ESL Cookbook (which also recommends .070" minimum [about 1.6mm] d/s spacing).
It is correct to say that closer spacing gives higher efficiency because the strength of the electrostatic force falls off quadratically with distance. So, for a given power input, 1.1 d/s would yield significantly higher efficiency, within the smaller space provided for the diaphragm to move in. The question then becomes at what point and loudness the diaphragm would be driven into the stators-- and I can't answer that question.
I will stick with my recommendation of 1.6 mm d/s for the reasons given in my earlier post. I can say with certainty that 1.6 mm d/s will give no problems in a hybrid panel and will yield good output too. This I know because my 30.5cm x 122cm panels with 1.6 mm d/s will play louder than I can stand to listen.
One more thing, your 25cm x 165cm panels are only about 12% larger than mine so I'm thinking their 12% higher capacitance would likely not be a problem. (of course, if you use the smaller 1.1 mm d/s, the capacitance would then be substantially higher). Again, I would ask Calvin's opinion on your panels size/capacitance and d/s spacing.
What's the downside to bigger spacing? Voltage is cheap but burning holes in your diaphragms sure isn't. If it is a conflict between engineering design perfection versus plain good sense, it really shouldn't be hard to decide.
In my case here the 1.6mm (0.062") option is the default option. It's tried and true.
If 1.1mm (0.045") were an option it would make my life easier.
Inter-Spacer distance would be more optimal, I already have tape lying around, due to lower voltage demands a direct drive amplifier might be an option later on.
Active diapraghragm width will be 200mm.
Recommended inter-spacer distance is 70-100 x d/s spacing -> either 116-160mm or 77-110mm. Running a spacer down the centerline with 1.6mm d/s spacing would put me outside the recommended interval forcing me to go with horizontal spacers insted. -> Not as good for the active radiating area. -> possibly loosing efficiency/sensitivity?
Voltage requirements estimate 1.6kVrms vs 1.1kVrms. 3.1kVpp might be doable with a fairly simple OTL tube amplifier. I said might... I'm just keeping my options open at this point. 4.5kVpp is a harder nut to crack.
So I guess there are some incentives for me to explore the small d/s route.
If it's just a plain and simple bad idea I'll drop it and not look back, but abandoning it just because it's not the normal way of doing things just isn't my style.
If 1.1mm (0.045") were an option it would make my life easier.
Inter-Spacer distance would be more optimal, I already have tape lying around, due to lower voltage demands a direct drive amplifier might be an option later on.
Active diapraghragm width will be 200mm.
Recommended inter-spacer distance is 70-100 x d/s spacing -> either 116-160mm or 77-110mm. Running a spacer down the centerline with 1.6mm d/s spacing would put me outside the recommended interval forcing me to go with horizontal spacers insted. -> Not as good for the active radiating area. -> possibly loosing efficiency/sensitivity?
Voltage requirements estimate 1.6kVrms vs 1.1kVrms. 3.1kVpp might be doable with a fairly simple OTL tube amplifier. I said might... I'm just keeping my options open at this point. 4.5kVpp is a harder nut to crack.
So I guess there are some incentives for me to explore the small d/s route.
If it's just a plain and simple bad idea I'll drop it and not look back, but abandoning it just because it's not the normal way of doing things just isn't my style.
markusA:
I would go with the 1.6mm spacers!
I use 2mm for my midpanel and 1mm for the tweeterpanels in my ESL-hybrids.
It will be a compromise as you want to cross over to your woffer as low as possible => the need off larger d/s, small d/s => lower EHT, transformers etc. as you previous stated. With 1.6mm d/s you should have no problem getting your XO below 300Hz!
Roger
I would go with the 1.6mm spacers!
I use 2mm for my midpanel and 1mm for the tweeterpanels in my ESL-hybrids.
It will be a compromise as you want to cross over to your woffer as low as possible => the need off larger d/s, small d/s => lower EHT, transformers etc. as you previous stated. With 1.6mm d/s you should have no problem getting your XO below 300Hz!
Roger
Hi,
1.1mm is good for a maximum SPL-value of 110dB@4m for f>200Hz with my small panel.
Sounds sufficient eyyh? 😉 Gives any bass a good run for the money.
jauu
Calvin
1.1mm is good for a maximum SPL-value of 110dB@4m for f>200Hz with my small panel.
Sounds sufficient eyyh? 😉 Gives any bass a good run for the money.
jauu
Calvin
- Status
- Not open for further replies.
- Home
- Loudspeakers
- Planars & Exotics
- ESL Panel construction?