Hello Edmond
>>Why should they fail as they are already protected by an over-current limiter?
Of coarse you are right , but my personal preference is for flame proof parts in these locations in the event of catastrophic failure.
Are you going to use relay speaker protection on the output.
Regards
Arthur
>>Why should they fail as they are already protected by an over-current limiter?
Of coarse you are right , but my personal preference is for flame proof parts in these locations in the event of catastrophic failure.
Are you going to use relay speaker protection on the output.
Regards
Arthur
>Are you going to use relay speaker protection on the output.
Yes, by means of a relay or low Rdson MOSFETs. Don't know yet which of the two.
Cheers,
E.
Do you have data on the THD performance of the low Rdson Mosfets at highish power >100watts. I assume you are using it in series with output of the amp or am I wrong.
Regards
>Are you going to use relay speaker protection on the output.
Yes, by means of a relay or low Rdson MOSFETs. Don't know yet which of the two.
Cheers,
E.
Why not use electronic fuse and loudspeaker protection as in JLH 80W MOSFET amp, I used something similar(regulator not stabilizer) and it works very good.
dado
Hi Damir,
Do you have a link to the schematic, please?
Cheers,
E.
Edmond some schematics are here: http://www.tcaas.btinternet.co.uk/ETI5-89a.gif
and here:A Paul Kemble web page - JLH mosfet amplifiers.
and you can look how I did somthing similar for my TT amp:http://www.diyaudio.com/forums/solid-state/182554-thermaltrak-tmc-amp-10.html#post3031504
Damir
Thanks Damir.
I will have a look at it later on, because at the moment I'm finishing the adaption* of the schematic to the PCB version (a lot of work). Besides, LS protection will be put on a separate PCB and will be one of the next steps.
* That also means the incorporation of a DC servo, making the amp even more complex. As a matter of fact, I'm doing it with huge aversion: adding (read: wasting) needlessly a dozen extra components, simply because some gurus say that any electrolytic cap (no matter what type or brand) in the NFB loop is bad.
Cheers,
E.
I will have a look at it later on, because at the moment I'm finishing the adaption* of the schematic to the PCB version (a lot of work). Besides, LS protection will be put on a separate PCB and will be one of the next steps.
* That also means the incorporation of a DC servo, making the amp even more complex. As a matter of fact, I'm doing it with huge aversion: adding (read: wasting) needlessly a dozen extra components, simply because some gurus say that any electrolytic cap (no matter what type or brand) in the NFB loop is bad.

Cheers,
E.
Thanks Damir.
I will have a look at it later on, because at the moment I'm finishing the adaption* of the schematic to the PCB version (a lot of work). Besides, LS protection will be put on a separate PCB and will be one of the next steps.
* That also means the incorporation of a DC servo, making the amp even more complex. As a matter of fact, I'm doing it with huge aversion: adding (read: wasting) needlessly a dozen extra components, simply because some gurus say that any electrolytic cap (no matter what type or brand) in the NFB loop is bad.
Cheers,
E.
JLH used quite high values for the feedback resistors in his 80W MOSFET amp to allow use of film type cap, in particular case polycarbonate type.
What about JFET in LTP, is it possible to avoid cap all together? Some famous amps are without cap in the feedback and no DC servo eider.
all the best in your PCB design.
Damir
keep it simple, but not simpler
Hi Damir,
>Some famous amps are without cap in the feedback and no DC servo eider.
So, if I do it this way, I'm 'in good company'. In addition, I can add a trim pot, just as you did in your TT-amp.
>all the best in your PCB design.
Thank you! As already said, it will be not an easy job: a 4 layer PCB with 300+ components! (almost as complex as a motherboard)
Cheers,
E.
Hi Damir,
>Some famous amps are without cap in the feedback and no DC servo eider.
So, if I do it this way, I'm 'in good company'. In addition, I can add a trim pot, just as you did in your TT-amp.
>all the best in your PCB design.
Thank you! As already said, it will be not an easy job: a 4 layer PCB with 300+ components! (almost as complex as a motherboard)
Cheers,
E.
...That also means the incorporation of a DC servo, making the amp even more complex. As a matter of fact, I'm doing it with huge aversion: adding (read: wasting) needlessly a dozen extra components, simply because some gurus say that any electrolytic cap (no matter what type or brand) in the NFB loop is bad.![]()
Hi Edmond,
You could keep the elcap in the servo, but still isolate the servo almost completely from the amplifier, just using thermal coupling between servo an amplifier. Tandberg did that with some of their amplifiers in the past. Example: Tandberg 3000A, shown here. Q102 is the servo LTP driving two resistors R111 and R110, thermally coupled to the diodes CR101...104 of the input bias current sources.
I assume most audiophiles will not argue a servo with no electrical connections to sensitive input circuits. Also, the loading of the amplifier output with an RC filter to drive the servo will not harm any half decent amplifier.
Furthermore it is an open loop amplifier (i.e. no global feedback) with Hawksford EC for the power stage with MOSFETs.
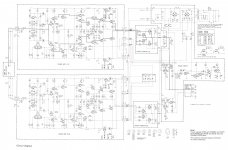
Cheers, Steven
>Are you going to use relay speaker protection on the output.
Yes, by means of a relay or low Rdson MOSFETs. Don't know yet which of the two.
Cheers,
E.
Chocoholic once posted a circuit for a MOSFET relay:
http://www.diyaudio.com/forums/solid-state/155939-mosfet-relais.html#post1997422
Distortion seemed to be virtually unmeasurable in practice.
Steven
Thanks Damir.
I will have a look at it later on, because at the moment I'm finishing the adaption* of the schematic to the PCB version (a lot of work). Besides, LS protection will be put on a separate PCB and will be one of the next steps.
* That also means the incorporation of a DC servo, making the amp even more complex. As a matter of fact, I'm doing it with huge aversion: adding (read: wasting) needlessly a dozen extra components, simply because some gurus say that any electrolytic cap (no matter what type or brand) in the NFB loop is bad.
Cheers,
E.
Hi Edmond,
I plead guilty. I like DC servos and hate electrolytics in the signal path. A decent DC sero takes only a few components and often less board space than a good electrolytic. BUT, I will admit that, as I pointed out in my book, that a non-polar electrolytic of generous voltage rating, like those used in a loudspeaker crossover, can perform (at least measure) extremely well.
Cheers,
Bob
A decent DC sero takes only a few components and often less board space than a good electrolytic.
Bob
A 220uF to 1mF capacitor is that huge.?...
Chocoholic once posted a circuit for a MOSFET relay:
http://www.diyaudio.com/forums/solid-state/155939-mosfet-relais.html#post1997422
Distortion seemed to be virtually unmeasurable in practice.
Steven
You can also use non isolated drive on the mosfets as well. If you switch the speaker ground return line, the drive is very simple: Audio Amplifier Design and Circuits | hifisonix.com a topics down from the top of the page.
A 220uF to 1mF capacitor is that huge.?...![]()
I said a GOOD electrolytic
Cheers,
Bob
Hi Edmond,
You could keep the elcap in the servo, but still isolate the servo almost completely from the amplifier, just using thermal coupling between servo an amplifier. Tandberg did that with some of their amplifiers in the past. Example: Tandberg 3000A, shown here. Q102 is the servo LTP driving two resistors R111 and R110, thermally coupled to the diodes CR101...104 of the input bias current sources.
I assume most audiophiles will not argue a servo with no electrical connections to sensitive input circuits. Also, the loading of the amplifier output with an RC filter to drive the servo will not harm any half decent amplifier.
Furthermore it is an open loop amplifier (i.e. no global feedback) with Hawksford EC for the power stage with MOSFETs.
View attachment 290036
Cheers, Steven
Hi Steven,
Thanks for providing the schematic. Indeed, a thermally isolated servo is a very clever and original solution. I've never seen this before.
BUT.... it has the same drawback as a conventional servo: over twenty additional components. It is again a trade-off between complexity and performance; that's precisely my dilemma.
BTW, maybe using optocouplers for isolation also provide a viable solution.
>Chocoholic once posted a circuit for a MOSFET relay:
Thx for the hint!
Cheers,
E.
dilemma
Hi Harry,
The problem is that other people make a problem of it.
Cheers,
E.
Hi Bob,
I'm afraid I have to disagree with your definition of a 'few'. The DC servo on page 165 of your book consists of 10 components. Add to this number 12 components for a stabilized +/- 15V PSU. So in total, 22 extra components.
As for board space, in the PGP amp a Panasonic bipolar cap was used, 470uF, 16V, diameter: 16mm, protected by two DO-35 diodes.
My aim is trying to build an amp that can withstand any kind of critic. So if I'm using an electrolytic cap in the signal path, even in case of a proven distortionless one, there will always be people who have serious objections to its use.
Now the question is: should I raise a middle finger to those people*, or should I give in to their objections and add (read: waste) 22 extra components? I would be much obliged if you help me to overcome this dilemma.
* people who also advocate using polystyrene caps for decoupling the supply rails.
Cheers,
E.
Edmond, doesn't the PGP have an electrolytic in the feedback path? Doesn't the PGP get at least -120 dB distortion across the audio band at all output powers from 1 watt to 100 watts into 8 ohms? What exactly then is the problem?
Hi Harry,
The problem is that other people make a problem of it.
Cheers,
E.
Hi Edmond,
I plead guilty. I like DC servos and hate electrolytics in the signal path. A decent DC sero takes only a few components and often less board space than a good electrolytic.
Hi Bob,
I'm afraid I have to disagree with your definition of a 'few'. The DC servo on page 165 of your book consists of 10 components. Add to this number 12 components for a stabilized +/- 15V PSU. So in total, 22 extra components.
As for board space, in the PGP amp a Panasonic bipolar cap was used, 470uF, 16V, diameter: 16mm, protected by two DO-35 diodes.
BUT, I will admit that, as I pointed out in my book, that a non-polar electrolytic of generous voltage rating, like those used in a loudspeaker crossover, can perform (at least measure) extremely well.
Cheers,
Bob
My aim is trying to build an amp that can withstand any kind of critic. So if I'm using an electrolytic cap in the signal path, even in case of a proven distortionless one, there will always be people who have serious objections to its use.
Now the question is: should I raise a middle finger to those people*, or should I give in to their objections and add (read: waste) 22 extra components? I would be much obliged if you help me to overcome this dilemma.
* people who also advocate using polystyrene caps for decoupling the supply rails.
Cheers,
E.
- Status
- This old topic is closed. If you want to reopen this topic, contact a moderator using the "Report Post" button.
- Home
- Amplifiers
- Solid State
- Has anyone seen this front-end before?