What are the requirements for safety spacing on the pcb? I do not have the en60950 spec. Although I do not have any initial intention to put my smps through testing, I'd like to at least try to meet the specs.
Mostly, I'm concerned with layer-to-layer spacing for mains runs. I have 4 layers, top, bottom, power and ground. On a .062" card, maintaining trace separation between layers is limited. What about ground/power planes? If they are on L2 and L3, then they will be close. Is the pcb material (FR4, prepreg, etc) considered sufficient? Lastly, what about spacing around vias? Seems that spacing requirements here too are important.
thanks
Mostly, I'm concerned with layer-to-layer spacing for mains runs. I have 4 layers, top, bottom, power and ground. On a .062" card, maintaining trace separation between layers is limited. What about ground/power planes? If they are on L2 and L3, then they will be close. Is the pcb material (FR4, prepreg, etc) considered sufficient? Lastly, what about spacing around vias? Seems that spacing requirements here too are important.
thanks
http://www.alternatezone.com/electronics/files/PCBDesignTutorialRevA.pdf
........youll find it in here.
If you can find it in EN60950 then youll be doing very well.
If you can find out how to actually buy a copy of EN60950 then youve done amazingly well
62 thou......that around 1.5mm............thats loads and loads of material.....no problem with that at all.
Officially, live and neutral tracks should be 3mm apart.
...if its just diy, you can get away with a lot less than that.
........youll find it in here.
If you can find it in EN60950 then youll be doing very well.
If you can find out how to actually buy a copy of EN60950 then youve done amazingly well
62 thou......that around 1.5mm............thats loads and loads of material.....no problem with that at all.
Officially, live and neutral tracks should be 3mm apart.
...if its just diy, you can get away with a lot less than that.
eem2am gave a great short answer, and a really nice PCB layout tutorial. I can elaborate on UL/IEC standards because I have some info which might be useful to anyone interested in this topic.
I have a copy of UL 60065 "Safety Requirements for Audio, Video and Similar Electronic Apparatus". 60950 is concerned with information technology equipment. UL standards can be purchased directly from UL here: http://ulstandardsinfonet.ul.com/catalog/stdscatframe.html they are very very expensive. 60065 and 60950 are being combined into 62368 "Audio/Video, Information Technology and Communications Technology Equipment Safety Requirements" Anyone who is very interested in this topic can also attend courses offered by UL: UL University
interpreting these standards is kinda like the US tax code. you cannot really know if your product is fully compliant unless you let them test it for you, because there are a thousand variables. having said that, there is a section of the standard which refers to clearance on one side of a printed circuit board. a figure is given relating "peak operating voltage" to "minimum clearance" and it says:
"The curve is defined by the formula: log d = 0.78 log (U/300) where d is the distance in mm, U is the peak voltage, with a minimum of 0.2mm"
it's slightly different than the table in PCB design tutorial above. for example : 40 volts = 0.2mm, 100 volts = 0.4mm 250 volts = 0.9mm
Further, they talk about that when directly connected to the mains, the "required withstand voltage" depends "on the combined effect of the normal operating voltage (including repetative peaks due to internal circuitry such as switch mode power supplies) and non-repetative overvoltages due to external transients" in short, most equipment should assume the possibility of 1500 volt peak transients on the line for 120 volt mains or 2500 volt peak on 240 volt mains. hence a clearance distance of about 3.5mm (138 mils) for 120V line or about 5.2mm for 240V line. and these numbers adjust upwards if your circuit produces a peak voltage higher than the nominal peak value of the line. this is all for 1 external layer of a PCB with no coating, internal layers or opposite side layers have insulation so different rules apply. but still a good idea to keep all your secondary side wiring well clear of any primary side wiring which lives on the same pcb. if in doubt you could always do a hipot test.
Another good idea for safety is to use components that are already UL certified for anything that is connected to mains, such as power inlet, power switch, fuse holder, wire, transformers, etc.
-Joel
I have a copy of UL 60065 "Safety Requirements for Audio, Video and Similar Electronic Apparatus". 60950 is concerned with information technology equipment. UL standards can be purchased directly from UL here: http://ulstandardsinfonet.ul.com/catalog/stdscatframe.html they are very very expensive. 60065 and 60950 are being combined into 62368 "Audio/Video, Information Technology and Communications Technology Equipment Safety Requirements" Anyone who is very interested in this topic can also attend courses offered by UL: UL University
interpreting these standards is kinda like the US tax code. you cannot really know if your product is fully compliant unless you let them test it for you, because there are a thousand variables. having said that, there is a section of the standard which refers to clearance on one side of a printed circuit board. a figure is given relating "peak operating voltage" to "minimum clearance" and it says:
"The curve is defined by the formula: log d = 0.78 log (U/300) where d is the distance in mm, U is the peak voltage, with a minimum of 0.2mm"
it's slightly different than the table in PCB design tutorial above. for example : 40 volts = 0.2mm, 100 volts = 0.4mm 250 volts = 0.9mm
Further, they talk about that when directly connected to the mains, the "required withstand voltage" depends "on the combined effect of the normal operating voltage (including repetative peaks due to internal circuitry such as switch mode power supplies) and non-repetative overvoltages due to external transients" in short, most equipment should assume the possibility of 1500 volt peak transients on the line for 120 volt mains or 2500 volt peak on 240 volt mains. hence a clearance distance of about 3.5mm (138 mils) for 120V line or about 5.2mm for 240V line. and these numbers adjust upwards if your circuit produces a peak voltage higher than the nominal peak value of the line. this is all for 1 external layer of a PCB with no coating, internal layers or opposite side layers have insulation so different rules apply. but still a good idea to keep all your secondary side wiring well clear of any primary side wiring which lives on the same pcb. if in doubt you could always do a hipot test.
Another good idea for safety is to use components that are already UL certified for anything that is connected to mains, such as power inlet, power switch, fuse holder, wire, transformers, etc.
-Joel
There's a rather big block of text there, but I read through it and I like this statement:
All the line-operated PCB's I've seen (such as line-operated TV's and CRT monitors, and desktop PC power supplies) have a LARGE amount of space, like at least a half inch (0.5" or 13mm), between the line traces and the isolated traces. This puts the big transients such as lightning through the UL-rated components connecting the two sides rather than it arcing between traces, so the makers of those things can be blamed instead of the maker of the PCB.
How big is your switcher? If you're making it to fit into a wall-wart and making a bazillion of them it might make sense to see how little spacing you can legally get away with, otherwise I advocate making it as big as you can.
I don't like putting a trace on the primary side over or under a trace on the secondary side on a multilayer board, it just doesn't seem right. You've got a switching transformer, and probably an optoisolator for feedback. I wouldn't get the primary and secondary side traces get any closer to one another than what it takes to run traces to the optocoupler, or whatever the smallest component is that connects to both....
but still a good idea to keep all your secondary side wiring well clear of any primary side wiring which lives on the same pcb.
All the line-operated PCB's I've seen (such as line-operated TV's and CRT monitors, and desktop PC power supplies) have a LARGE amount of space, like at least a half inch (0.5" or 13mm), between the line traces and the isolated traces. This puts the big transients such as lightning through the UL-rated components connecting the two sides rather than it arcing between traces, so the makers of those things can be blamed instead of the maker of the PCB.
How big is your switcher? If you're making it to fit into a wall-wart and making a bazillion of them it might make sense to see how little spacing you can legally get away with, otherwise I advocate making it as big as you can.
The link is really nice. I had been reading a lot on net about pcb routing. But this is a crux. For most of us this would be of help as a basic guidelines.
Thanks ,I have saved it in my collection.
Maybe my original note was not entirely clear. In my design, the primary to secondary isolation is pretty large. There's a bobbin wound transformer that has a ton of space between primary and secondary. Also, the opto-isolator that bridges the primary and secondary has a spacing of around 6.5mm - which I believe meets the creepage and clearance specs.
What I am asking, though, is on the mains side of things. With 220V (potentially up to 265Vrms) input, is there a requirement (spacing) for line-to-line or line-to-earth. Since this PCB has power planes, and another earth plane, and they are directly on top of each other spaced by maybe 0.025", is that a hazard? Also, for through-hole parts or vias, they have a clearance to the planes. If that clearance is too small, I worry that is a hazzard.
What I am asking, though, is on the mains side of things. With 220V (potentially up to 265Vrms) input, is there a requirement (spacing) for line-to-line or line-to-earth. Since this PCB has power planes, and another earth plane, and they are directly on top of each other spaced by maybe 0.025", is that a hazard? Also, for through-hole parts or vias, they have a clearance to the planes. If that clearance is too small, I worry that is a hazzard.
I thought spacing distance for Line and Neutral nodes had to be 3mm.
Thats the creepage distance. (distance along connecting surface)
You appear to be asking if its ok to have Line on one side of a 25 thou substrate, and neutral directly above/below it..........and yes, that is fine.....25 thou of pcb substrate is a lot of susbstrate.
......but as long as the creepage is not less than 3mm....creepage is the shortest distance along surfaces that are between your nodes-under-investigation.
....as we said it does depend though on whether you have conformal coating.
After the mains rectifier, you have the DC bus, which i presume is ~180-375VDC.
......this comes after the input MOV, so the spacings are less......i think its only one mm between DC Bus and DC Bus ground.
....i would buy yourself a small , offline , open frame SMPS from farnell and just look at it and see the spacings yourself.
.......i dont think you have to be terribly accurate, because no-one is going to open your product up and check the spacings.....
....but you do have to pass the hipot test.
.....but to be honest, even with spacings far smaller than the regulations allow, i never saw flashover problems in the hipot test.
Thats the creepage distance. (distance along connecting surface)
You appear to be asking if its ok to have Line on one side of a 25 thou substrate, and neutral directly above/below it..........and yes, that is fine.....25 thou of pcb substrate is a lot of susbstrate.
......but as long as the creepage is not less than 3mm....creepage is the shortest distance along surfaces that are between your nodes-under-investigation.
....as we said it does depend though on whether you have conformal coating.
After the mains rectifier, you have the DC bus, which i presume is ~180-375VDC.
......this comes after the input MOV, so the spacings are less......i think its only one mm between DC Bus and DC Bus ground.
....i would buy yourself a small , offline , open frame SMPS from farnell and just look at it and see the spacings yourself.
.......i dont think you have to be terribly accurate, because no-one is going to open your product up and check the spacings.....
....but you do have to pass the hipot test.
.....but to be honest, even with spacings far smaller than the regulations allow, i never saw flashover problems in the hipot test.
use the same spacing guidelines for all traces, not just primary to secondary, based on the expected peak voltage between traces. a via through a layer counts as an adjacent trace. dielectric breakdown between layers depends on many factors, but a good rule of thumb is 500-750 volts per 0.001 inch for FR4 laminate, or about 10000-15000 volts for 0.020 inch (4 layer 0.062 board.)
but don't forget capacitance between layers, keep an eye on leakage current and contact current.
Also, remember it's not just the PCB, you have to be mindful of all the hardware and component leads that are attached. I have seen failed hipot tests, but always due to sloppy or careless construction. your opto has 6.5mm clearance, but not if you bend the leads in before you solder them.
I found a nice article on power supply safety testing here: http://www.psma.com/ul_files/forums/safety/estguide2.pdf
and some things to consider when designing a PSU here: http://www.psma.com/HTML/FILES/make_vs_buy.pdf
but don't forget capacitance between layers, keep an eye on leakage current and contact current.
Also, remember it's not just the PCB, you have to be mindful of all the hardware and component leads that are attached. I have seen failed hipot tests, but always due to sloppy or careless construction. your opto has 6.5mm clearance, but not if you bend the leads in before you solder them.
I found a nice article on power supply safety testing here: http://www.psma.com/ul_files/forums/safety/estguide2.pdf
and some things to consider when designing a PSU here: http://www.psma.com/HTML/FILES/make_vs_buy.pdf
WWW.CREEPAGE.COM Welcome!
FR4 is classed as a class 1 insulator, so for 4 layer PCB no problem with seperation.
The creepage and clearance rules apply to all, DIY is not exempt and should not ignore these recconendations. If you ignore the rules and your board causes someone to be electrocuted or starts a fire, you will not have a leg to stand on if it goes to court. At the end of the day these were not made up for fun it is SAFETY.
Conformal coatings also do not count unless you have stringent QA prodedures to test them.
Creepage and clearance distances are different for inner layers as the conductors are considered to be isolated by a class 1 insulation, the FR4 material, so these can be much closer, it is the outer layers that you have to consider, and for DIY you must treat them as exposed conductors.
FR4 is classed as a class 1 insulator, so for 4 layer PCB no problem with seperation.
The creepage and clearance rules apply to all, DIY is not exempt and should not ignore these recconendations. If you ignore the rules and your board causes someone to be electrocuted or starts a fire, you will not have a leg to stand on if it goes to court. At the end of the day these were not made up for fun it is SAFETY.
Conformal coatings also do not count unless you have stringent QA prodedures to test them.
Creepage and clearance distances are different for inner layers as the conductors are considered to be isolated by a class 1 insulation, the FR4 material, so these can be much closer, it is the outer layers that you have to consider, and for DIY you must treat them as exposed conductors.
Last edited:
the secondary side of an offline smps does not need the same wide spacing as the pre-rectifier primary side tracks.
Most world mains is considered to have transients up to 1MegaVolt for about 1 minute per month, and these are absorbed by the MOV on the primary side....or should be.
......but this is why secondary does not need as wide spacing as primary side.
Most world mains is considered to have transients up to 1MegaVolt for about 1 minute per month, and these are absorbed by the MOV on the primary side....or should be.
......but this is why secondary does not need as wide spacing as primary side.
I designed a pcb that has live and neutral on it, and I would like to know about the proper spacing between them. Since I have read that even 1.0mm should do.
The closest distance between the copper trace of the live and the one of the neutral is 1.7mm. My pcb is single-sided, bare copper (no solder mask or tinning), FR4. Mains is 230VAC, nominally.
Is that enough? From what I read, I understand that it is, but I would like to have another opinion.
I was also thinking about "filling" the gap between these two traces with some plastic that I would adhere (using glue) to the FR4 piece of board that lies between them. That could be some cable isulation, a small piece of FR4, ordinary plastic etc. I just thought it would weaken the possibility of an arc since no longer would just air be separating them. Is this rational?
The closest distance between the copper trace of the live and the one of the neutral is 1.7mm. My pcb is single-sided, bare copper (no solder mask or tinning), FR4. Mains is 230VAC, nominally.
Is that enough? From what I read, I understand that it is, but I would like to have another opinion.
I was also thinking about "filling" the gap between these two traces with some plastic that I would adhere (using glue) to the FR4 piece of board that lies between them. That could be some cable isulation, a small piece of FR4, ordinary plastic etc. I just thought it would weaken the possibility of an arc since no longer would just air be separating them. Is this rational?
Marce,
I had a look, and for the voltages I will use (never exceed 30V DC) it calculates 1.0mm as functional safety (the one I mentioned before). I currently have 1.7mm.
The pot solution is interesting - could I just pot that point or something like that? I don't know how to actually pot, but I assume that inserting anything that is a good insulator would ameliorate the situation. Could it be some plastic I put in between etc.
Is there an easy diy way of potting two traces?
I had a look, and for the voltages I will use (never exceed 30V DC) it calculates 1.0mm as functional safety (the one I mentioned before). I currently have 1.7mm.
The pot solution is interesting - could I just pot that point or something like that? I don't know how to actually pot, but I assume that inserting anything that is a good insulator would ameliorate the situation. Could it be some plastic I put in between etc.
Is there an easy diy way of potting two traces?
I will double check later, as I'm stuck at work at the moment, there is this stuff:
Buy Potting Compounds Epoxy potting compound,500gm RS ERER1122K500G online from RS for next day delivery.
Also just thought of a rough and ready solution, mask the area and use hot melt glue, its the same as this:
Low Pressure Injection Molding - Henkel
which I have specified a lot for automotive type assemblies.
Buy Potting Compounds Epoxy potting compound,500gm RS ERER1122K500G online from RS for next day delivery.
Also just thought of a rough and ready solution, mask the area and use hot melt glue, its the same as this:
Low Pressure Injection Molding - Henkel
which I have specified a lot for automotive type assemblies.
Marce, thanks for your time. I doubt that I can get hold of something like that (especially since I don't really think I will seriously need it again), but I will see what I can do.
Could ordinary glue do the job? Just a drop of it maybe.
KatieandDad, I attach a picture of the pcb. It is ready to be etched, so you will notice that I have covered the traces I want to remain with blue paint. Separation of primary-secondary traces is at least 10mm, as can be estimated by the picture too:
So I think that the clearance can be guaranteed.
This is my situation anyway, I was thinking of filling that air gap with something plastic, glue, or epoxy as marce suggests. Depending on what I can find.
Could ordinary glue do the job? Just a drop of it maybe.
KatieandDad, I attach a picture of the pcb. It is ready to be etched, so you will notice that I have covered the traces I want to remain with blue paint. Separation of primary-secondary traces is at least 10mm, as can be estimated by the picture too:
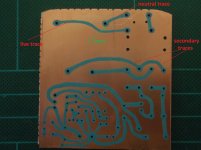
So I think that the clearance can be guaranteed.
This is my situation anyway, I was thinking of filling that air gap with something plastic, glue, or epoxy as marce suggests. Depending on what I can find.
Marce, thanks for your time. I doubt that I can get hold of something like that (especially since I don't really think I will seriously need it again), but I will see what I can do.
Could ordinary glue do the job? Just a drop of it maybe.
KatieandDad, I attach a picture of the pcb. It is ready to be etched, so you will notice that I have covered the traces I want to remain with blue paint. Separation of primary-secondary traces is at least 10mm, as can be estimated by the picture too:
View attachment 385537
So I think that the clearance can be guaranteed.
This is my situation anyway, I was thinking of filling that air gap with something plastic, glue, or epoxy as marce suggests. Depending on what I can find.
Hi I am confused as you spoke of 30 V DC and now I read Live and Neutral. If you are dealing with 230 V then 1.7 mm is not enough. You could drill a hole just between the two tracks... Air is better than epoxy. If you still can change the PCB I would do so. Make that 4 mm just to be safe.
Don't get married just to sort out PCB issue.
Best advice ever on diyaudio.com ! The first of the 2 advices that is.
Last edited:
- Status
- This old topic is closed. If you want to reopen this topic, contact a moderator using the "Report Post" button.
- Home
- Amplifiers
- Power Supplies
- pcb safety spacing