LOL, Your product looks good, really good.
You have given me some ideas.
I reckon that a really easy way of making horns and flares would be to stretch a cloth across that box like yours, and setting overall positions/shape geometry with a temporary central disc/shape, and then doping that cloth to create a rigid form, ready for back filling with polyester resin/glass fibre.
Custom straight flares really easily.
Dan.
Exactly like that. I am still thinking of doing elliptical waveguide using nylon cloth in the way you describe above.
I'm also thinking that applying a finely controllable vacuum (or pressure) whilst doing the initial doping process would be the icing on the cake....curved flares instead of straight flares.
A thin sprayed film of clear laquer would likely provide flexible and sufficient air sealing during shape forming and be the initial doping, and then apply a stronger resin to achieve mechanically stronger doping.
I have done perspex blowing in the past....the above idea is not too far removed, but would be far easier....and semi final tweakable.
With perspex blowing you get exactly one go to get it right, and perfectly reproducible is not easy/possible.
Dan.
A thin sprayed film of clear laquer would likely provide flexible and sufficient air sealing during shape forming and be the initial doping, and then apply a stronger resin to achieve mechanically stronger doping.
I have done perspex blowing in the past....the above idea is not too far removed, but would be far easier....and semi final tweakable.
With perspex blowing you get exactly one go to get it right, and perfectly reproducible is not easy/possible.
Dan.
Last edited:
Very nice work Erkki - certainly an inspiration for us all to try our own molded horns. What is nice is that the curve produced is a catenary (cosh or sinh) profile as dictated by suspension of a mass on a string or membrane - and this is much better than a conical horn.
Regards,
xrk971
Regards,
xrk971
I'm also thinking that applying a finely controllable vacuum...
Dan.
Hmm.. not impossible. You need precisely controlled vacuum but that can be achieved quite easily. Rapidly curing polyester (about 15 min work time) would also make the process easier.
Very nice work Erkki - certainly an inspiration for us all to try our own molded horns. What is nice is that the curve produced is a catenary (cosh or sinh) profile as dictated by suspension of a mass on a string or membrane - and this is much better than a conical horn.
Regards,
xrk971
Thanks! That is true, the horn is not conical but slightly curved.
Last edited:
Yes....my point is that vacuum/pressure can be used to optimise that curve.Thanks! That is true, the horn is not conical but slightly curved.
Dan.
Yes....my point is that vacuum/pressure can be used to optimise that curve.
Dan.
It would be easy to test if you already have the vacuum equipment. And I believe it would be possible to control the curvature quite precisely if the pump control is fine enough and the system doesn't have any leaks.
A salvaged fridge compressor can be used as a vacuum pump....Google it.
An Ebay pressure/vacuum gauge, and a couple of valves (one series, one shunt) could be used to reproducibly set pressure/vacuum...no biggie.
My Kef coaxial floorstanders might benefit from suitable flares by this method.
Dan.
An Ebay pressure/vacuum gauge, and a couple of valves (one series, one shunt) could be used to reproducibly set pressure/vacuum...no biggie.
My Kef coaxial floorstanders might benefit from suitable flares by this method.
Dan.
Yes....my point is that vacuum/pressure can be used to optimise that curve.
Dan.
I do not see how you will do that without destroying the shape
unless you already have a mold
the real cool thing about this is the nature of such rubber material when being drawn into making this shape
actually, I remember someone else suggeting this a long time ago, that it would be a perfect approach to create the optimal cone shape for a woofer or other drivers
To make elliptic or alike curvature, one could stretch the plastic membrane step by step, by heating it only partially. Is this possible in practise - I don't know.
If the membrane has some elastic modulus (latex/rubberdam, silicone), it gets elliptic curvature naturally.
If the membrane has some elastic modulus (latex/rubberdam, silicone), it gets elliptic curvature naturally.
Last edited:
Yes....my point is that vacuum/pressure can be used to optimise that curve.
Dan.
Yes vacuum forming this would be easy. Use to make aircraft canopies with large sheets (5' x 9') Rohm & Haas plexiglass from oven to mold, clamped, sealed and vacuum on in thirty seconds. Micro Balloons to judge depth of that fire hot plastic. Bagging to cure out aircraft wings/stabilizers. R/C plane parts same thing just on a smaller scale. Would suggest RCGroups forums for insight.
To make elliptic or alike curvature, one could stretch the plastic membrane step by step, by heating it only partially. Is this possible in practise - I don't know.
If the membrane has some elastic modulus (latex/rubberdam, silicone), it gets elliptic curvature naturally.
Naw doesn't work. Materials normally convert from solid to liquid in its narrow transistion state which causes rapid shape change (flow). Makes bulbous form due to the thinning of material once set. Cooling is very fast and doesn't allow for correction once it occurs.
Below is an arrangement that should work (without making a mould as I have done). We do not know yet if one could control the curvature with vacuum but it shouldn't be impossible.
Nylon or PE fabric would be suitable materials because they are elastic. Epoxy and polyester do not stick to these materials and the fabric can be torn off easily from the surface after the resin has set. However, the fabric passes air through and thus it would be possible to get high quality surface with this method.
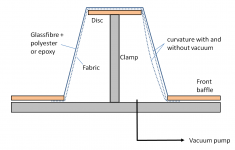
Nylon or PE fabric would be suitable materials because they are elastic. Epoxy and polyester do not stick to these materials and the fabric can be torn off easily from the surface after the resin has set. However, the fabric passes air through and thus it would be possible to get high quality surface with this method.
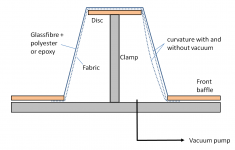
This does work, but requires an inner lip. This angle must be calculated so there is a minimum of transition from free form to molded.I expect drawing the poly into oval shaped hole will do the trick![]()
Curvature is done two ways. 1. Shape of the curve and 2. Depth of draw. Material thickness is important so not to over thin as it stretches ever thinner. Each material has its limits as to how far it will withstand before a hole forms. Acetate film is used alot due to convenience, cost and known fairly manageable characteristics. Smaller parts can be done in an average oven.Below is an arrangement that should work (without making a mould as I have done). We do not know yet if one could control the curvature with vacuum but it shouldn't be impossible.
Nylon or PE fabric would be suitable materials because they are elastic. Epoxy and polyester do not stick to these materials and the fabric can be torn off easily from the surface after the resin has set. However, the fabric passes air through and thus it would be possible to get high quality surface with this method.
View attachment 392517
ahh, it is not a LeCleach horn you want, is it
but yeah, I would also have suggested rounded edges on the shape hole
and a thicker 'hole plate' would make bigger roundings possible
and it would not be the hardest part of this
LOL naw that would actually require several more steps depending on how many rounds you go on those lips
Exactly the hole plate has a roundover like transistion. This lip would normally extend well beyond the top plate. Opposite of what you are thinking.
To make a horn like flare the material can be anchored from the center and then clamped to the former opening. Vacuum applied draws the sides in. Example Think of a vacuum box and it's opening. The material is attatched to the inside edge of the cutout. Now in the center is a wooden dowel that protrudes up and out of the box in the center. this pokes the material up like a tent. Apply vacuum. In this case the transitional roundover would be on the inside edge of the top plate. Can be done with both cloth and plastics. Plastics are easier. Cloth also requires it to be precut to shape.
To do with acetate plastic covers the opening eg top plate. Put a small marker spot in the center. Placed in an oven and removed once heated to proper temp/time. Remove and place marker dot on dowel. Dowel itself is rounded over on the end. Press down with even steady force as the plastic stretches. Once down clamp base to seal. Vacuum on til proper draw is formed, then off til cool, release vacuum and remove. There is very little time to do all this and is not something you will master even the first few times out.
Pole can be done externally and plastic pushed into a deeper vacuum box. With plastic attached from the outside edge, roundover transistion outside inward
To do with acetate plastic covers the opening eg top plate. Put a small marker spot in the center. Placed in an oven and removed once heated to proper temp/time. Remove and place marker dot on dowel. Dowel itself is rounded over on the end. Press down with even steady force as the plastic stretches. Once down clamp base to seal. Vacuum on til proper draw is formed, then off til cool, release vacuum and remove. There is very little time to do all this and is not something you will master even the first few times out.
Pole can be done externally and plastic pushed into a deeper vacuum box. With plastic attached from the outside edge, roundover transistion outside inward
This lip would normally extend well beyond the top plate. Opposite of what you are thinking.
gosh ! you really are on to the exstreme
but luckily simpler will do just fine
If I still have to wait the drivers I might try different approach. I am, after all, looking for good sound quality, and It definitely would be worth of trying different shapes, rounded edges etc.
All; I am quite impressed of the advice, help and encouragement you share here
All; I am quite impressed of the advice, help and encouragement you share here
- Status
- This old topic is closed. If you want to reopen this topic, contact a moderator using the "Report Post" button.
- Home
- Loudspeakers
- Multi-Way
- Two-way coaxial loudspeakers with molded waveguides