As Tom said, the "ideal case" is to have the driver Fs around 1.5x the TH cutoff to get the most extended response. However for PA this is a second priority compared to having a driver that can handle enough power without destroying itself. If the B&C 18SW115 is the "best" TH driver at the moment, it might be even better with a higher Fs -- but it isn't available like this.
Carbon cones are stiffer but usually have less damping than paper ones, so I'd be surprised if this is why 18sound use it. When cone failure happens at high power levels in a horn it's usually due to either the cone failing under compression and creasing, failure at the joint to the former, or going "bowl-shaped" instead of conical -- all these are cause by it being too weak/stiff, not resonances, and I've never seen any evidence that resonances are the cause of failures. This assumes that the pressure on the cone is relatively evenly spread and symmetrical, which may not be the case with a poorly-designed horn throat.
In any case the bell mode resonances of a reasonably stiff cone -- which is what you're talking about -- are at a few hundred Hz or higher, and shouldn't be excited strongly in a sub driver covering up to 100Hz.
If all this is correct then it's more important to have high stiffness and strength than high damping for a sub driver (not true for higher frequencies). So I think a very strong cone is one of the things that makes the 18SW115 good, not high internal cone damping.
I'd still like to see the TC Sounds Pro-5150 tried in a TH (1.5" deep Cu coil in 3" radial neo gap, Xmax = 31mm, Rohacell structural foam cored sandwich cone), I suspect this would surpass even the 18SW115 but it's ridiculously expensive (the Al coil Pro-5100 is $1300!) and difficult to get outside the USA.
The Ficar BTL N218 is another off-the-wall possibility, even thought it's targeted at car audio it might work extremely well in a TH, is more widely available, and I think is even a bit cheaper than the 18SW115. Since SPL competition car bassheads put these in reflex boxes and drive them at box resonance with >5000W (which puts huge stress on the cone) without them dying, I suspect they're pretty robust.
Carbon cones are stiffer but usually have less damping than paper ones, so I'd be surprised if this is why 18sound use it. When cone failure happens at high power levels in a horn it's usually due to either the cone failing under compression and creasing, failure at the joint to the former, or going "bowl-shaped" instead of conical -- all these are cause by it being too weak/stiff, not resonances, and I've never seen any evidence that resonances are the cause of failures. This assumes that the pressure on the cone is relatively evenly spread and symmetrical, which may not be the case with a poorly-designed horn throat.
In any case the bell mode resonances of a reasonably stiff cone -- which is what you're talking about -- are at a few hundred Hz or higher, and shouldn't be excited strongly in a sub driver covering up to 100Hz.
If all this is correct then it's more important to have high stiffness and strength than high damping for a sub driver (not true for higher frequencies). So I think a very strong cone is one of the things that makes the 18SW115 good, not high internal cone damping.
I'd still like to see the TC Sounds Pro-5150 tried in a TH (1.5" deep Cu coil in 3" radial neo gap, Xmax = 31mm, Rohacell structural foam cored sandwich cone), I suspect this would surpass even the 18SW115 but it's ridiculously expensive (the Al coil Pro-5100 is $1300!) and difficult to get outside the USA.
The Ficar BTL N218 is another off-the-wall possibility, even thought it's targeted at car audio it might work extremely well in a TH, is more widely available, and I think is even a bit cheaper than the 18SW115. Since SPL competition car bassheads put these in reflex boxes and drive them at box resonance with >5000W (which puts huge stress on the cone) without them dying, I suspect they're pretty robust.
Last edited:
Hi!
18NLW 9600 has triple silicon spider; in my tests beside the 18LW2400 and 18TBX100 this driver is in another league; also you spent more on it, and on the amp to power it. All the tested where 8 ohms drivers.
18NLW9600C, maybe has carbon cone due to improve water proof of the material; humidity will increase cone weight principally when used at the coast, and places where air humidity is high, causing drop of Fs and reducing SPL…
Interesting looking at the Pdfs of both the 18NLW9600 and 18NLW9600C has same Mms 261 g, despite complete different materials and 9600C owned 0.5dBs sensivity more…
B&C dealer sent a 18SW115 and a 21SW115 to a friend factory for tests; will ask if a can test it also to compare. At this time have not build the Keystone and TH18 Xoc1.
Selenium in past has developed quartz composite cone not so stiff, very light, with some loss in the sensivity, but better adapted to the Brazilian East e North coast humid air (maybe due warranty problems with paper cone fails).
Now testing the 18NLW9600 8ohms version as reported here at DIY.
Regards,
18NLW 9600 has triple silicon spider; in my tests beside the 18LW2400 and 18TBX100 this driver is in another league; also you spent more on it, and on the amp to power it. All the tested where 8 ohms drivers.
18NLW9600C, maybe has carbon cone due to improve water proof of the material; humidity will increase cone weight principally when used at the coast, and places where air humidity is high, causing drop of Fs and reducing SPL…
Interesting looking at the Pdfs of both the 18NLW9600 and 18NLW9600C has same Mms 261 g, despite complete different materials and 9600C owned 0.5dBs sensivity more…
B&C dealer sent a 18SW115 and a 21SW115 to a friend factory for tests; will ask if a can test it also to compare. At this time have not build the Keystone and TH18 Xoc1.
An externally hosted image should be here but it was not working when we last tested it.
Selenium in past has developed quartz composite cone not so stiff, very light, with some loss in the sensivity, but better adapted to the Brazilian East e North coast humid air (maybe due warranty problems with paper cone fails).
Now testing the 18NLW9600 8ohms version as reported here at DIY.
4 ohms version of them should be more adequate due Pe required to move this beasts.An externally hosted image should be here but it was not working when we last tested it.
Regards,
Other drivers for Keystone
The B&C 18SW115 and 18sound 18NLW9600 have almost identical T-S parameters and I know Tom said the performance was the same in the TH-118, they look like the best of the "conventional" 18" PA drivers -- though I did hear a rumour that he swapped from the initial 18NLW9600 to the current 18SW115 because of some reliability issues with the 18sound.
The only current 18" drivers I have in my database that might possibly be better (depending on priorities, Pe or Xmax or SPL) are (in order of Xmax):
Driver Xmax SPL Pe
TC Pro-5150 31.0 ???? 1500 -- no T/S parameters (or available?) yet
TC Pro-5100 31.0 94.5 1000 -- mega-expensive
FIcar BTL-N218 28.0 93.9 2000 -- if T-S parameters are correct...
BMS 18N860 22.0 92.6 1500 -- lowest SPL
PAsub PA460 20.2 96.5 2000 -- difficult to get hold of
BMS 18N850V2 16.0 94.9 1200 -- lowest Pe
Turbomax 1800i 14.1 97.4 1800 -- highest SPL
18NLW9600 14.0 95.0 1800
18SW115 13.5 94.7 1700
Of course how many of these are really as robust as the B&C is unknown...
The B&C 18SW115 and 18sound 18NLW9600 have almost identical T-S parameters and I know Tom said the performance was the same in the TH-118, they look like the best of the "conventional" 18" PA drivers -- though I did hear a rumour that he swapped from the initial 18NLW9600 to the current 18SW115 because of some reliability issues with the 18sound.
The only current 18" drivers I have in my database that might possibly be better (depending on priorities, Pe or Xmax or SPL) are (in order of Xmax):
Driver Xmax SPL Pe
TC Pro-5150 31.0 ???? 1500 -- no T/S parameters (or available?) yet
TC Pro-5100 31.0 94.5 1000 -- mega-expensive
FIcar BTL-N218 28.0 93.9 2000 -- if T-S parameters are correct...
BMS 18N860 22.0 92.6 1500 -- lowest SPL
PAsub PA460 20.2 96.5 2000 -- difficult to get hold of
BMS 18N850V2 16.0 94.9 1200 -- lowest Pe
Turbomax 1800i 14.1 97.4 1800 -- highest SPL
18NLW9600 14.0 95.0 1800
18SW115 13.5 94.7 1700
Of course how many of these are really as robust as the B&C is unknown...
It was not a rumor. I inquired to Ivan Beaver as to which was being used currently after noticing a photo posted by a guy who had a pair of TH-118, one with a 18NLW9600, one with a 18SW115, he told me the issues.The B&C 18SW115 and 18sound 18NLW9600 have almost identical T-S parameters and I know Tom said the performance was the same in the TH-118, they look like the best of the "conventional" 18" PA drivers -- though I did hear a rumour that he swapped from the initial 18NLW9600 to the current 18SW115 because of some reliability issues with the 18sound.
Of course how many of these are really as robust as the B&C is unknown...
The problems with the 18NLW9600 have been fixed in present production.
Hi Iand,
The reason why 18Sound is using Carbon is because of the exceptional material characteristics. Carbon provides the highest stiffness and highest suppression of internal resonances, if produced properly. The difference with earlier Carbon cone research at RCF was all about improving the weaving technique involved during production in order to lower cone losses even further. The second objective was purely from a production perspective, to build Carbon cones for large drivers under their own roof. Although it doesn’t result in much SPL improvement (yet!) compared to the 9600, it does have lower THD figures and it will keep its transients longer. If produced properly the cones become almost indestructible.
The problem with the 9600’s in the TH118 was fixed after the second production line, like Art already stated. The change was about the adhesive that couldn’t deal with the forces at extreme excursion. If needed these drivers could have been swapped under guaranty, if the dealer supported. But I heard stories that some didn’t support this possibility.
In "ideal case", cones have no losses either. I my view Thom was referring to the theory behind the TH and not specifically practical, real live, PA circumstances where drivers 'suffer' under factors that are not included in the basic theory or any model. In theory I have no argument with Tom’s statements but I sure see a difference between theory and the extremes in real situation. You only have to look what drivers Tom selects for his PA cabs. It proves he prefers low Fs drivers with strong cones of high internal damping that suppress unwanted cone movement (cone losses) supported by capable suspension and surround.
I’m not talking about bell resonances that appear way up higher, I’m talking about cone losses in the form of circle nodal and diagonal nodal, all within the bandpass of the sub range. The only other non linear movements in a cone come from the motor, more specific the loose of control by the motor. They can be seen in THD peaks and dynamic power compression spots within the bandpass. Some can be heard by the human ear although diagonal nodal is difficult to detect by the ear. That why cones can get destroyed while users claim they didn't hear anything.
Strangely enough, all your suggested drivers are perfect examples of low Fs and extreme low Fs in PA terms. Therefore I assume you do agree that at least heavy/strong cones (that result in low Fs drivers) are necessary but you have not explained why.
The reason why 18Sound is using Carbon is because of the exceptional material characteristics. Carbon provides the highest stiffness and highest suppression of internal resonances, if produced properly. The difference with earlier Carbon cone research at RCF was all about improving the weaving technique involved during production in order to lower cone losses even further. The second objective was purely from a production perspective, to build Carbon cones for large drivers under their own roof. Although it doesn’t result in much SPL improvement (yet!) compared to the 9600, it does have lower THD figures and it will keep its transients longer. If produced properly the cones become almost indestructible.
The problem with the 9600’s in the TH118 was fixed after the second production line, like Art already stated. The change was about the adhesive that couldn’t deal with the forces at extreme excursion. If needed these drivers could have been swapped under guaranty, if the dealer supported. But I heard stories that some didn’t support this possibility.
In "ideal case", cones have no losses either. I my view Thom was referring to the theory behind the TH and not specifically practical, real live, PA circumstances where drivers 'suffer' under factors that are not included in the basic theory or any model. In theory I have no argument with Tom’s statements but I sure see a difference between theory and the extremes in real situation. You only have to look what drivers Tom selects for his PA cabs. It proves he prefers low Fs drivers with strong cones of high internal damping that suppress unwanted cone movement (cone losses) supported by capable suspension and surround.
I’m not talking about bell resonances that appear way up higher, I’m talking about cone losses in the form of circle nodal and diagonal nodal, all within the bandpass of the sub range. The only other non linear movements in a cone come from the motor, more specific the loose of control by the motor. They can be seen in THD peaks and dynamic power compression spots within the bandpass. Some can be heard by the human ear although diagonal nodal is difficult to detect by the ear. That why cones can get destroyed while users claim they didn't hear anything.
Strangely enough, all your suggested drivers are perfect examples of low Fs and extreme low Fs in PA terms. Therefore I assume you do agree that at least heavy/strong cones (that result in low Fs drivers) are necessary but you have not explained why.
Hi Djk,"The -3dB point is above the driver Fs which is another contradiction"
The TH-118 is tuned to 28hz, so it's tuned below Fs.
The mouth of the TH-118 is undersized for its Sd, so it rolls off quite gradually . It looks like it would tolerate some EQ to make it flat to 30hz.
The - 3dB point is response related, and the 28Hz is 1/4WL system related. The -3dB point in the TH118 is 35Hz in the Danley specs (and hopefully without eq)
Last edited:
Hi Djim
As you say, all the drivers I picked have large Xmax and relatively stiff heavy cones -- if you've got a relatively long heavy coil for high Xmax there's no point having a light flexible cone because the coil mass will dominate -- needed for high power handling. For high power use a stiff/strong cone is an obvious requirement, you only need to calculate the huge forces on the cone to see this.
For PA-bandwidth tapped horns it would be better if they also had higher Fs (stiffer suspension) but none of them have this, because the TH is a minority application -- in a FLH with a rear chamber you want the driver to have lower Fs to allow a smaller chamber to be used and because the air compliance is more linear than suspension, in a reflex you also want lower Fs.
I suppose a driver manufacturer might produce an 18" driver optimised for TH applications but it hasn't happened so far even for Danley, which is why he uses off-the-shelf drivers in all his PA cabinets -- also means replacements are easy to come by, another reason to avoid rare exotic drivers for this application.
Woven carbon fibre/epoxy composite makes for very stiff light cones but the material itself is not well damped and can suffer from high-Q resonances, unless it's combined with other materials or has a damping layer applied (both of which add mass without increasing stiffness) -- this is well known in hi-fi drivers as well as from the material properties.
Given all this -- especially sane cost and availability -- the B&C and 18Sound drivers are the obvious choices, though if you hit them with low-frequency synthesized signals which are sinewave-like (like dubstep?) at the maximum excursion frequency they will clearly run out of excursion with the recommended amplifier power of 3.5kW or more.
If you're going to do this then you need more Xmax and high Pe and reasonable efficiency, and there aren't many candidates; the PA450 looks like one (if you can get one), but it doesn't work very well in a TH because BL and Mmd are too low. The BMS drivers also have lowish BL (very long coils in short gaps) for a TH. The TC drivers are stupidly expensive and difficult to get outside the USA.
Which leaves the Ficar BTL N218 as the only driver which might beat them, it is available in the UK and EU and last time I looked it was about £500. This assumes that the T-S parameters are correct which is not guaranteed for a car audio driver...
N218
DUAL 1 | DUAL 2
Fs: 34.0 Hz | 33.6 Hz
Re: 0.7 Ohms/coil | 1.4 Ohms/coil
Qms: 8.18 | 8.28
Qes: .32 | .32
Qts: .31 | .31
Mms: 336g | 344g
Sd: 1210cm^2 | 1210cm^2
Vas: 133.8 l | 133.8 l
Spl: 94.0dB 1W/1m | 93.8dB 1W/1m
Bl: 17.8 N/A | 25.1 N/A
Xmax: 28mm * | 28mm *
Rms: 2000W * | 2000W *
As you say, all the drivers I picked have large Xmax and relatively stiff heavy cones -- if you've got a relatively long heavy coil for high Xmax there's no point having a light flexible cone because the coil mass will dominate -- needed for high power handling. For high power use a stiff/strong cone is an obvious requirement, you only need to calculate the huge forces on the cone to see this.
For PA-bandwidth tapped horns it would be better if they also had higher Fs (stiffer suspension) but none of them have this, because the TH is a minority application -- in a FLH with a rear chamber you want the driver to have lower Fs to allow a smaller chamber to be used and because the air compliance is more linear than suspension, in a reflex you also want lower Fs.
I suppose a driver manufacturer might produce an 18" driver optimised for TH applications but it hasn't happened so far even for Danley, which is why he uses off-the-shelf drivers in all his PA cabinets -- also means replacements are easy to come by, another reason to avoid rare exotic drivers for this application.
Woven carbon fibre/epoxy composite makes for very stiff light cones but the material itself is not well damped and can suffer from high-Q resonances, unless it's combined with other materials or has a damping layer applied (both of which add mass without increasing stiffness) -- this is well known in hi-fi drivers as well as from the material properties.
Given all this -- especially sane cost and availability -- the B&C and 18Sound drivers are the obvious choices, though if you hit them with low-frequency synthesized signals which are sinewave-like (like dubstep?) at the maximum excursion frequency they will clearly run out of excursion with the recommended amplifier power of 3.5kW or more.
If you're going to do this then you need more Xmax and high Pe and reasonable efficiency, and there aren't many candidates; the PA450 looks like one (if you can get one), but it doesn't work very well in a TH because BL and Mmd are too low. The BMS drivers also have lowish BL (very long coils in short gaps) for a TH. The TC drivers are stupidly expensive and difficult to get outside the USA.
Which leaves the Ficar BTL N218 as the only driver which might beat them, it is available in the UK and EU and last time I looked it was about £500. This assumes that the T-S parameters are correct which is not guaranteed for a car audio driver...
N218
DUAL 1 | DUAL 2
Fs: 34.0 Hz | 33.6 Hz
Re: 0.7 Ohms/coil | 1.4 Ohms/coil
Qms: 8.18 | 8.28
Qes: .32 | .32
Qts: .31 | .31
Mms: 336g | 344g
Sd: 1210cm^2 | 1210cm^2
Vas: 133.8 l | 133.8 l
Spl: 94.0dB 1W/1m | 93.8dB 1W/1m
Bl: 17.8 N/A | 25.1 N/A
Xmax: 28mm * | 28mm *
Rms: 2000W * | 2000W *
The DSL TH-118 rolls off at around 24 dB per octave rate, not very gradual."The -3dB point is above the driver Fs which is another contradiction"
The TH-118 is tuned to 28hz, so it's tuned below Fs.
The mouth of the TH-118 is undersized for its Sd, so it rolls off quite gradually . It looks like it would tolerate some EQ to make it flat to 30hz.
DSLs graphs are rather "stretched" when compared to Hornresp.
The graphs below shows one of Langston Holland's TH-118 and TH-115 on top, my Keystone 18" TH below.
Frequency and phase response are similar, excursion goes up rapidly below the low corner.
Attachments
Hi Iand,
By reading your reply I begin to see where the misunderstanding comes from. I do think we are basically talking about the same thing. Theoretically you are correct and it is just like Danley stated. However, the theory doesn’t work in the real world. Drivers with very high suspension values, strong motors and low cone mass are indeed not able to suppress all unwanted forces at high excursion. Even Carbon isn’t the solution for that. New high tech 'memory fibres' have such wideband suppression that they are not (yet) usable for cone construction, as far as I know (maybe a mixture with paper perhaps?).
In your reply you say: "if you've got a relatively long heavy coil for high Xmax there's no point having a light flexible cone because the coil mass will dominate -- needed for high power handling. For high power use a stiff/strong cone is an obvious requirement, you only need to calculate the huge forces on the cone to see this".
I agree, the mass ratio between voice coil/former and cone mass are important factors in balancing drivers. So far there is no misunderstanding. I assume you mean with "flexible cone", the losses by deformation. This is where I think the misunderstanding begins.
The words: flexible, cone losses and non-linear movement are all assembly names that describe the effects of all unwanted forces that are manifesting in the cone. None of these words explain specifically what forces are responsible. The nodes in cones are the most important forces for these losses and result in non linear behaviour. This is not just an idea but a known factor over the last 50 years or so. If flexibility would be explained like some sort of uncontrolled 'flapping around', such driver wouldn’t be able to produce any decent note in the first place.
If you look carefully to the pressed rings of many LF PA drivers you will see there is some sort of pattern. This pattern is based on how these nodes manifest within the cone. Beginning with the fundamental resonance and followed by circle and diagonal nodes. You can also see that most pressed rings from different drivers have similarities between them. This is because every nodal has its own position and pattern. The fundamental Fs determines at which frequency they occur. The type of nodal determines where and how they show up in the cone (see model). However, the model is based on a flat surface of high stiffness. Therefore the patterns can show differences in a cone structure. Most industry leaders all have accurate models for each driver, often based on fancy laser measuring methods. Of course, they don't print them because it would show the mistakes.
Now back to TH's, I do think that in the last powering stage the PA drivers become unable to control the cones. The reason is simple, the lack of 'air-spring'. The results are nodes that make the cone into non linear movement and cause Dynamic Power Compression. Therefore it can lead to physical damage of the cone.
About the high-Q resonance point (or break-up point as some prefer to call them), all hard cones have such high-Q point in their response. I use the word hard because stiff doesn’t necessarily need to be hard, well... not in this matter. A 'stiff' cone, such as the cone from the 18SW115 has still quiet some 'elastic' capabilities compared to a metal alloy cone for instance. That’s why the 18SW115 still has very usable internal damping figures while some describe that cone as hard.
The same counts for Carbon but only if it is build up by small woven strips of carbon. Each cross-section between two small woven strips is a physical obstruction for developing nodes. In such construction the Carbon gets very good damping properties. Compare it with one sheet of 18mm plywood with a bunch of 18mm woven branches, both made out of birch. If you hit the sheet it will produce a tone that is relative long in time domain, because its relative hard. If you hit the woven branches there is no tone and the sound is very short in time domain. Both are examples of low internal damping versus high internal damping while both
are made from birch with the same material characteristics.
By reading your reply I begin to see where the misunderstanding comes from. I do think we are basically talking about the same thing. Theoretically you are correct and it is just like Danley stated. However, the theory doesn’t work in the real world. Drivers with very high suspension values, strong motors and low cone mass are indeed not able to suppress all unwanted forces at high excursion. Even Carbon isn’t the solution for that. New high tech 'memory fibres' have such wideband suppression that they are not (yet) usable for cone construction, as far as I know (maybe a mixture with paper perhaps?).
In your reply you say: "if you've got a relatively long heavy coil for high Xmax there's no point having a light flexible cone because the coil mass will dominate -- needed for high power handling. For high power use a stiff/strong cone is an obvious requirement, you only need to calculate the huge forces on the cone to see this".
I agree, the mass ratio between voice coil/former and cone mass are important factors in balancing drivers. So far there is no misunderstanding. I assume you mean with "flexible cone", the losses by deformation. This is where I think the misunderstanding begins.
The words: flexible, cone losses and non-linear movement are all assembly names that describe the effects of all unwanted forces that are manifesting in the cone. None of these words explain specifically what forces are responsible. The nodes in cones are the most important forces for these losses and result in non linear behaviour. This is not just an idea but a known factor over the last 50 years or so. If flexibility would be explained like some sort of uncontrolled 'flapping around', such driver wouldn’t be able to produce any decent note in the first place.
If you look carefully to the pressed rings of many LF PA drivers you will see there is some sort of pattern. This pattern is based on how these nodes manifest within the cone. Beginning with the fundamental resonance and followed by circle and diagonal nodes. You can also see that most pressed rings from different drivers have similarities between them. This is because every nodal has its own position and pattern. The fundamental Fs determines at which frequency they occur. The type of nodal determines where and how they show up in the cone (see model). However, the model is based on a flat surface of high stiffness. Therefore the patterns can show differences in a cone structure. Most industry leaders all have accurate models for each driver, often based on fancy laser measuring methods. Of course, they don't print them because it would show the mistakes.
Now back to TH's, I do think that in the last powering stage the PA drivers become unable to control the cones. The reason is simple, the lack of 'air-spring'. The results are nodes that make the cone into non linear movement and cause Dynamic Power Compression. Therefore it can lead to physical damage of the cone.
About the high-Q resonance point (or break-up point as some prefer to call them), all hard cones have such high-Q point in their response. I use the word hard because stiff doesn’t necessarily need to be hard, well... not in this matter. A 'stiff' cone, such as the cone from the 18SW115 has still quiet some 'elastic' capabilities compared to a metal alloy cone for instance. That’s why the 18SW115 still has very usable internal damping figures while some describe that cone as hard.
The same counts for Carbon but only if it is build up by small woven strips of carbon. Each cross-section between two small woven strips is a physical obstruction for developing nodes. In such construction the Carbon gets very good damping properties. Compare it with one sheet of 18mm plywood with a bunch of 18mm woven branches, both made out of birch. If you hit the sheet it will produce a tone that is relative long in time domain, because its relative hard. If you hit the woven branches there is no tone and the sound is very short in time domain. Both are examples of low internal damping versus high internal damping while both
are made from birch with the same material characteristics.

Last edited:
Accuracy depends on how accurate they have measured...The DSL TH-118 rolls off at around 24 dB per octave rate, not very gradual.
DSLs graphs are rather "stretched" when compared to Hornresp.
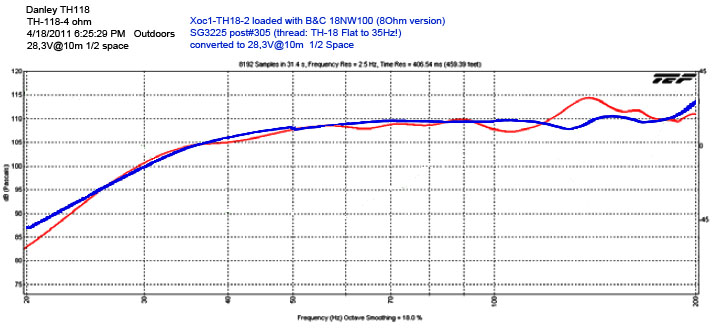
Last edited:
Hi Djim
I understand what you're saying about carbon fibre (CF) but unfortunately it's not really correct, you'd only get any damping from the "weave" if the fibres were free to move against each other, which would be the case if the cone was floppy like a basket -- which it hopefully isn't. A cone with woven CF is actually quite similar to plywood, fibres in both direction glued together with resin.
I think you're getting stiffness/elasticity and damping a bit confused -- there are some great explanations in "The New Science of Strong Materials" by J E Gordon which I'd highly recommend you (or anyone else!) reads. All stiff/strong materials tend to have low damping (high Q) pretty much by definition, metal is the worst for this but raw CF is not much better.
Carbon fibre cloth (woven) is used because it's easy to handle and has very good stiffness in both directions, but the fibers themselves don't have any significant damping (look up the material properties). When they're embedded in a matrix (either epoxy, or paper pulp, or anything else) the fibres still can't rub against each other or the material would disintegrate, so the damping comes from whatever other material is used in the cone or added surface damping goop.
If the materials are only carbon cloth and epoxy resin (like in cars or golf clubs) the result is very strong and light but also rings -- not as badly as metal, but still quite high-Q. As more highly-damped (lossy) material is added to the matrix the damping goes up but so does the weight, and stiffness drops.
Also with CF it's more difficult to add the circumferential stiffening rings which are used with pulp cones to suppress cone resonances, exactly as you describe -- anyway these rings are less effective with CF because it's so much stiffer to start off with. So a woven CF cone is very stiff but also difficult to damp and prevent resonances in, which is probably why it's not used so much (apart from the cost) -- it's difficult to get right.
The "ideal" material for subwoofer cones would be thin CF skins glued either side of a structural foam core (like Rohacell); this would be very stiff both radially and circumferentially (no ribs needed) and a suitable glue would add more damping to the relatively lossy core. It's the solution used in Formula 1 cars and aircraft wings for exactly the same reasons.
Unfortunately both Formula 1 cars and aircraft wings are a lot more expensive than speakers and so can afford to do this... :-(
Cheers
Ian
I understand what you're saying about carbon fibre (CF) but unfortunately it's not really correct, you'd only get any damping from the "weave" if the fibres were free to move against each other, which would be the case if the cone was floppy like a basket -- which it hopefully isn't. A cone with woven CF is actually quite similar to plywood, fibres in both direction glued together with resin.
I think you're getting stiffness/elasticity and damping a bit confused -- there are some great explanations in "The New Science of Strong Materials" by J E Gordon which I'd highly recommend you (or anyone else!) reads. All stiff/strong materials tend to have low damping (high Q) pretty much by definition, metal is the worst for this but raw CF is not much better.
Carbon fibre cloth (woven) is used because it's easy to handle and has very good stiffness in both directions, but the fibers themselves don't have any significant damping (look up the material properties). When they're embedded in a matrix (either epoxy, or paper pulp, or anything else) the fibres still can't rub against each other or the material would disintegrate, so the damping comes from whatever other material is used in the cone or added surface damping goop.
If the materials are only carbon cloth and epoxy resin (like in cars or golf clubs) the result is very strong and light but also rings -- not as badly as metal, but still quite high-Q. As more highly-damped (lossy) material is added to the matrix the damping goes up but so does the weight, and stiffness drops.
Also with CF it's more difficult to add the circumferential stiffening rings which are used with pulp cones to suppress cone resonances, exactly as you describe -- anyway these rings are less effective with CF because it's so much stiffer to start off with. So a woven CF cone is very stiff but also difficult to damp and prevent resonances in, which is probably why it's not used so much (apart from the cost) -- it's difficult to get right.
The "ideal" material for subwoofer cones would be thin CF skins glued either side of a structural foam core (like Rohacell); this would be very stiff both radially and circumferentially (no ribs needed) and a suitable glue would add more damping to the relatively lossy core. It's the solution used in Formula 1 cars and aircraft wings for exactly the same reasons.
Unfortunately both Formula 1 cars and aircraft wings are a lot more expensive than speakers and so can afford to do this... :-(
Cheers
Ian
Last edited:
B&W (Bowers & Wilkins - typically found in high end audiophile home theater and recording studios among other places) uses Rohacell in their 800 Series Diamond:
"Our outward looking and innovative approach to materials engineering is illustrated perfectly by the application of Rohacell® structural plastic foam in the construction of bass drivers. We found Rohacell® being used extensively in the high performance automotive and aerospace industries, where its unusual combination of very low weight and very high resistance to bending stress make it the ideal choice for a multitude of applications. Those very same characteristics also make it an ideal material for the structural heart of a bass driver.
If a bass driver cone is to perform at a level commensurate with our Kevlar® FST midrange drivers and Nautilus tweeters it must excel in three vital characteristics:
First, it must not bend significantly, even under huge dynamic loads. Second, it must have high self-damping so as not to display any significant resonance. And last, it must offer good acoustic attenuation so that sound energy within the speaker cabinet cannot leak out and muddy the music radiated forward. Combining those three characteristics, which in a multitude of respects are conflicting (light materials are rarely strong, often ring like bells and almost never resist sound transmission), is a tall order. Rohacell® is the key.
Viewed from the front, a Rohacell® driver doesnt look significantly different from many others. The real difference, where the Rohacell® foam can be found, is around the back of the cone. Rather than an overall cone thickness of perhaps one or two millimetres, typical with conventional bass drivers, a Bowers & Wilkins Rohacell® cone is significantly thicker. The Rohacell® foam is used as meat in a carbon-fibre skinned sandwich. The result is a cone that displays bending strength, self-damping and sound attenuation that are each an order of magnitude or more higher than conventionally manufactured cones. The potential downside of increased cone thickness is weight gain, but thanks to the low density of Rohacell®, that's not a problem and low frequency cut-off and sensitivity targets can still be met. Rohacell® isnt a free lunch for bass drivers, but its not far off.
Of course, while the look of a Rohacell® bass driver isnt out of the ordinary, we dont design speakers to be looked at, we design them to be listened to. Bass from a Rohacell® equipped speaker system takes on a whole new quality: deep, fast, dynamic and wholly untainted by the distortions and dynamic slurring that perhaps weve come to accept as part of the deal with moving coil speakers. In the same way that Kevlar® FST midrange drivers and Nautilus tweeters strip a layer or two of artifice from their respective segments of the audio band, so Rohacell® does for bass.
Rohacell is a registered trademark of Rhm GmbH & Co. KG"
804 Diamond
"Our outward looking and innovative approach to materials engineering is illustrated perfectly by the application of Rohacell® structural plastic foam in the construction of bass drivers. We found Rohacell® being used extensively in the high performance automotive and aerospace industries, where its unusual combination of very low weight and very high resistance to bending stress make it the ideal choice for a multitude of applications. Those very same characteristics also make it an ideal material for the structural heart of a bass driver.
If a bass driver cone is to perform at a level commensurate with our Kevlar® FST midrange drivers and Nautilus tweeters it must excel in three vital characteristics:
First, it must not bend significantly, even under huge dynamic loads. Second, it must have high self-damping so as not to display any significant resonance. And last, it must offer good acoustic attenuation so that sound energy within the speaker cabinet cannot leak out and muddy the music radiated forward. Combining those three characteristics, which in a multitude of respects are conflicting (light materials are rarely strong, often ring like bells and almost never resist sound transmission), is a tall order. Rohacell® is the key.
Viewed from the front, a Rohacell® driver doesnt look significantly different from many others. The real difference, where the Rohacell® foam can be found, is around the back of the cone. Rather than an overall cone thickness of perhaps one or two millimetres, typical with conventional bass drivers, a Bowers & Wilkins Rohacell® cone is significantly thicker. The Rohacell® foam is used as meat in a carbon-fibre skinned sandwich. The result is a cone that displays bending strength, self-damping and sound attenuation that are each an order of magnitude or more higher than conventionally manufactured cones. The potential downside of increased cone thickness is weight gain, but thanks to the low density of Rohacell®, that's not a problem and low frequency cut-off and sensitivity targets can still be met. Rohacell® isnt a free lunch for bass drivers, but its not far off.
Of course, while the look of a Rohacell® bass driver isnt out of the ordinary, we dont design speakers to be looked at, we design them to be listened to. Bass from a Rohacell® equipped speaker system takes on a whole new quality: deep, fast, dynamic and wholly untainted by the distortions and dynamic slurring that perhaps weve come to accept as part of the deal with moving coil speakers. In the same way that Kevlar® FST midrange drivers and Nautilus tweeters strip a layer or two of artifice from their respective segments of the audio band, so Rohacell® does for bass.
Rohacell is a registered trademark of Rhm GmbH & Co. KG"
804 Diamond
![]()
Thinking if it helps fix similar slots to the sides from the front/mouth to the back to avoid any vibration at that points.
Could be thinner solid wood slots as teached by Weems in Designing Building and testing your Own speakers Systems
regards,
The strips on the bottom are placed across the grain. Would it be better to place the strips on the sides across the grain as well (up & down opposed to front to back)?
Yeah, they're a grip of cash - for sure! They were the first I saw to use this material in cones. I soon after searched to find Morel and Alpine also using this material as well. Totally different end of the spectrum as far as price is concerned
Haven't followed up to study their different methods in how they use Rohacell compared to one another.
Less delamination and turbulence potential front to back.The strips on the bottom are placed across the grain. Would it be better to place the strips on the sides across the grain as well (up & down opposed to front to back)?
Since plywood grain alternates each layer, not much difference from a stiffness ratio, though side to side would probably be a tad stiffer in this configuration.
If a front grill is fitted, it will add cross stiffness.
If no screen is fitted, easier to sweep out debris the way it was done
Hi!
The grill to be attached with screws to SS15 is made so:
Front view
Back view
For TH18 could put one more screw hole to fix it directly to the slot or slots I was reffering to the sides.
Regards,
The grill to be attached with screws to SS15 is made so:
Front view
An externally hosted image should be here but it was not working when we last tested it.
Back view
An externally hosted image should be here but it was not working when we last tested it.
For TH18 could put one more screw hole to fix it directly to the slot or slots I was reffering to the sides.
Regards,
Hi Iand,Hi Djim
I understand what you're saying......
....Cheers
Ian
Oooh, you know all about this
Cheers,
Djim
Last edited:
- Home
- Loudspeakers
- Subwoofers
- TH-18 Flat to 35hz! (Xoc1's design)