Great stuff guy's thanks. Few more questions if thats ok, sorry!
1,
Now that im sorted with the Plans from Dave and buying drivers ( should be with me next week) can i run these drivers in a bit without putting in a box? Advice on how to do and what volumes and time required would be great. I have a workshop i can do this in if that is possible to do out of a speaker box.
2,
What is used to seal the driver into the recess hole? is there a foam gasket with the drivers? On my audionote E kit the drivers are sealed with blu tak, ( Audionote use this on all speakers) but once in its a bugger to remove again, if one needs to add or remove stuffing Etc.
3,
What is recomended as fasteners for the driver, screws/bolts to the cabinet. Is it screw directly to wood or metal inserts for bolts?
4,
I know speaker wire is a contentious issue i use cable talk 3 as its now cheap ( discontinued) and sounds every bit as good as anthing i have owned at 20 times the price but thats another story!
for the internal wiring is it ok to use this, or what is the norm?
Thanks
Ron
1,
Now that im sorted with the Plans from Dave and buying drivers ( should be with me next week) can i run these drivers in a bit without putting in a box? Advice on how to do and what volumes and time required would be great. I have a workshop i can do this in if that is possible to do out of a speaker box.
2,
What is used to seal the driver into the recess hole? is there a foam gasket with the drivers? On my audionote E kit the drivers are sealed with blu tak, ( Audionote use this on all speakers) but once in its a bugger to remove again, if one needs to add or remove stuffing Etc.
3,
What is recomended as fasteners for the driver, screws/bolts to the cabinet. Is it screw directly to wood or metal inserts for bolts?
4,
I know speaker wire is a contentious issue i use cable talk 3 as its now cheap ( discontinued) and sounds every bit as good as anthing i have owned at 20 times the price but thats another story!
for the internal wiring is it ok to use this, or what is the norm?
Thanks
Ron
Great stuff guy's thanks. Few more questions if thats ok, sorry!
1,
Now that im sorted with the Plans from Dave and buying drivers ( should be with me next week) can i run these drivers in a bit without putting in a box? Advice on how to do and what volumes and time required would be great. I have a workshop i can do this in if that is possible to do out of a speaker box.
You can run them free air, just be careful on over-excursion. There's been a lot discussed on break in methodology and time on other threads - in a nutshell soft music with less bass for the first 100 hours at lowish volumes, increase volume and more rhythmic music post that. Excursion during break-in period should not be more than 2 mm. You can look at some other threads if you need more details.
2,
What is used to seal the driver into the recess hole? is there a foam gasket with the drivers? On my audionote E kit the drivers are sealed with blu tak, ( Audionote use this on all speakers) but once in its a bugger to remove again, if one needs to add or remove stuffing Etc.
The MA drivers come with their own "super gasket" - no need for separate gasket/caulk material...
3,
What is recomended as fasteners for the driver, screws/bolts to the cabinet. Is it screw directly to wood or metal inserts for bolts?
The drivers come with screws and the be careful not to over tighten - there are descriptions about how to do it the right way on other thread. Ideally you should drill the pilot holes in the wood first and then screw in; I drill the pilot holes and turn the screws in once without the drivers, take them out and then install them with the drivers afterwards.
4,
I know speaker wire is a contentious issue i use cable talk 3 as its now cheap ( discontinued) and sounds every bit as good as anthing i have owned at 20 times the price but thats another story!
for the internal wiring is it ok to use this, or what is the norm?
Thanks
Ron
Dave suggests single strand Cat5 wire - works for me.
Fantastic!! your Z man!
Great stuff very very informative.
Thanks again, im actually getting excited! Big kid in a toy shop me!
regards
Ron
Ron,
Great to see your enthusiasm, and beware this hobby can get mighty addictive.
p.s. I guess you knew that already. Have fun!
Oh I know, i was a habitual box swapper for years getting up to the dizzy heights of a 30k system! the recession saw me selling everything to pay the bills, so only getting back but having a gret time with "frugal" (excuse the pun) funds.
When i had enough to get started again a hi fi dealer in Scotland ( Musicarch) was making his own 300b SE power amps and i was interested in his experiment. i had a small ( for hi fi) budget and he made me a 1 off 300b SE amp which he stated if this is not better than anything up to 10k i will give you a full refund!! so £2800 later i have yet to own or hear anything as good. he is now in full designing and making mode making 300b monos, 300b Se fixed bias power and a one off no holds barred special 300b power and mono blocks with very very nice trannies. I had some very expensive stuff through my home inc Audio note, Art, Border Patrol, Wavac, Hovland and none sound as good as my amp. his new stuff is supposed to be in another league.
my amp here.( now upgraded and superceded) im ordering a new one next year!)
very simply designed with off the shelf carcass and simple looks but new sold wood designs or CNC machined chassis to follow, im ordering my new amp with solid american black walnut case with stainless steel top and bottom plates and very well made italian potted trannies made to musicarch's spec.
Donald is so infected by these DIY amps he has sunk a lot of money and time with transformer companies getting them the way he wants. His new 300b to of the range have been put against £33k Audio note, and 100K jeff rowland amps and have trounced both with no bother Donald is an AN and JR dealer so has the kit for comparrison.
Great dealer with the best customer interaction i have never seen in my life. He is bringing his new amps over to Northern Ireland for us to play with for a day or two, i for one cant wait. I cant do electrical DIY and this is a great way for me to get it done and get great support and a life time warranty, he even serviced our amp for free collecting and delivering each one in person at great cost to him.
When i had enough to get started again a hi fi dealer in Scotland ( Musicarch) was making his own 300b SE power amps and i was interested in his experiment. i had a small ( for hi fi) budget and he made me a 1 off 300b SE amp which he stated if this is not better than anything up to 10k i will give you a full refund!! so £2800 later i have yet to own or hear anything as good. he is now in full designing and making mode making 300b monos, 300b Se fixed bias power and a one off no holds barred special 300b power and mono blocks with very very nice trannies. I had some very expensive stuff through my home inc Audio note, Art, Border Patrol, Wavac, Hovland and none sound as good as my amp. his new stuff is supposed to be in another league.
my amp here.( now upgraded and superceded) im ordering a new one next year!)
very simply designed with off the shelf carcass and simple looks but new sold wood designs or CNC machined chassis to follow, im ordering my new amp with solid american black walnut case with stainless steel top and bottom plates and very well made italian potted trannies made to musicarch's spec.
Donald is so infected by these DIY amps he has sunk a lot of money and time with transformer companies getting them the way he wants. His new 300b to of the range have been put against £33k Audio note, and 100K jeff rowland amps and have trounced both with no bother Donald is an AN and JR dealer so has the kit for comparrison.
Great dealer with the best customer interaction i have never seen in my life. He is bringing his new amps over to Northern Ireland for us to play with for a day or two, i for one cant wait. I cant do electrical DIY and this is a great way for me to get it done and get great support and a life time warranty, he even serviced our amp for free collecting and delivering each one in person at great cost to him.
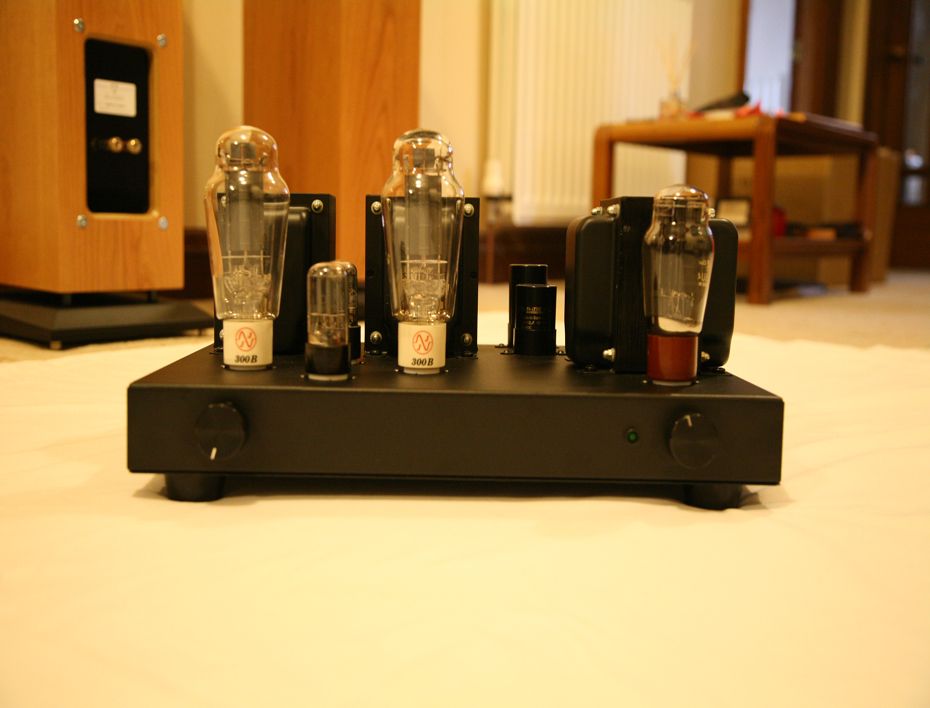
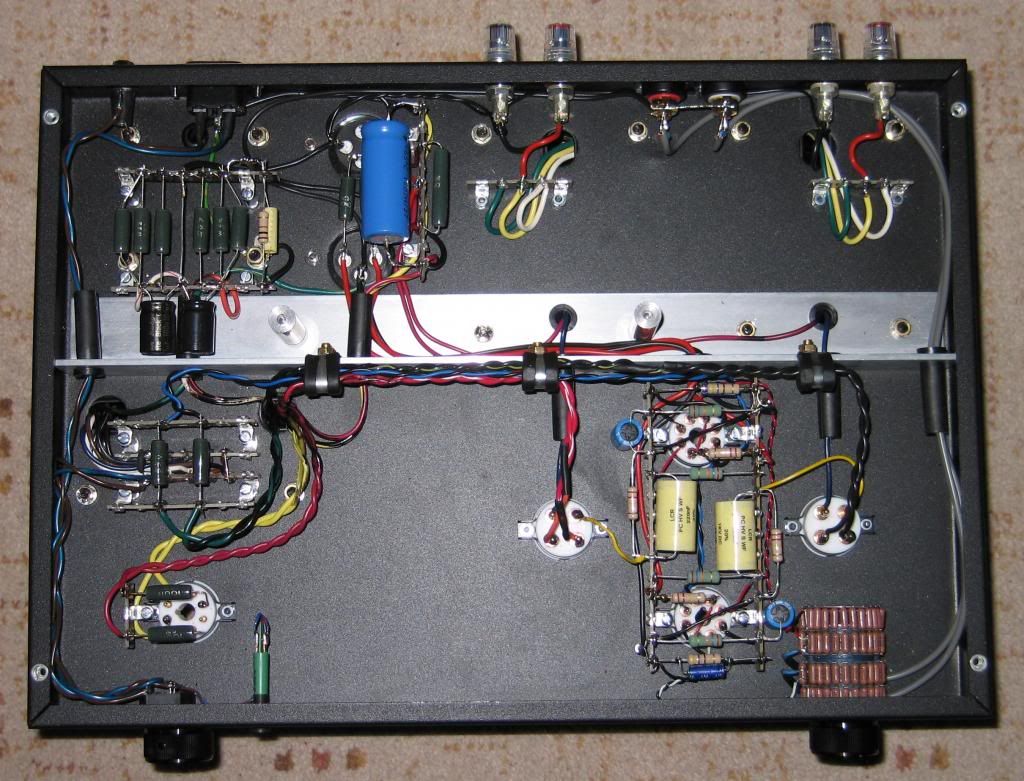
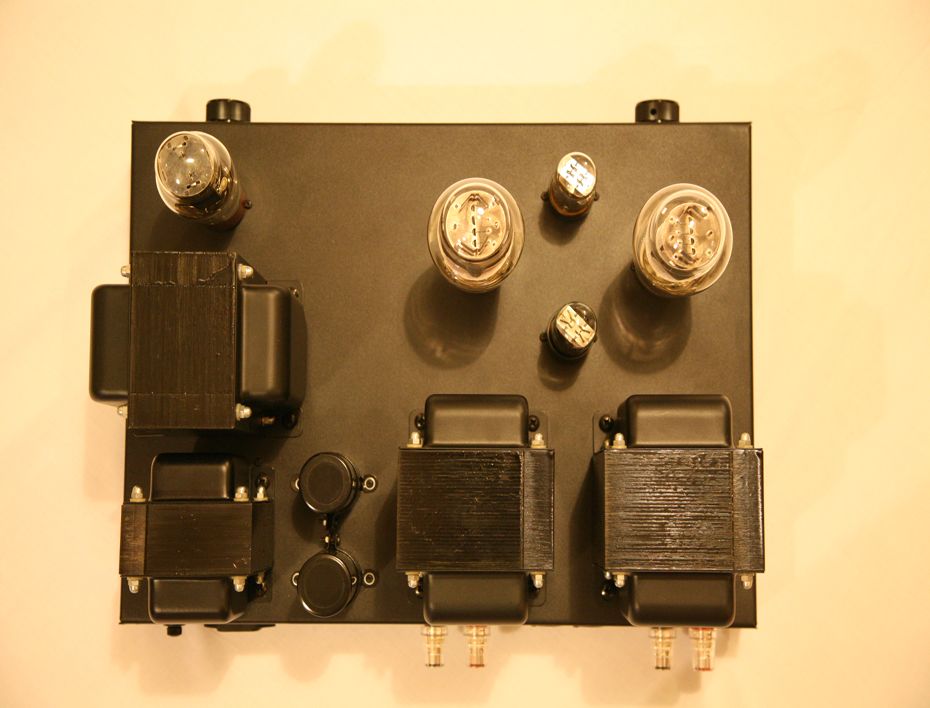
Last edited:
Ron,
Beautiful amp - slim, clean look. I think you will like the Alp 10.3... I haven't heard 'em yet but what I am reading on forum, it should be a good sounding wide-band driver. I have a pair still sitting in their boxes.
The FH-XL enclosure can elicit an impressive amount of LF performance from the Alpair 10P. Folks say that the Alp 10.3 metal is more extended on top and bottom - so I am guessing the combo will be a nice one.
When you do your build, consider having a removable top - that will make it easy for you to play around with the stuffing.
Keep us posted on your progress.
Beautiful amp - slim, clean look. I think you will like the Alp 10.3... I haven't heard 'em yet but what I am reading on forum, it should be a good sounding wide-band driver. I have a pair still sitting in their boxes.
The FH-XL enclosure can elicit an impressive amount of LF performance from the Alpair 10P. Folks say that the Alp 10.3 metal is more extended on top and bottom - so I am guessing the combo will be a nice one.
When you do your build, consider having a removable top - that will make it easy for you to play around with the stuffing.
Keep us posted on your progress.
Last edited:
When you do your build, consider having a removable top - that will make it easy for you to play around with the stuffing.
With the larger driver cutout on the XL removable top likely less useful than on FH3
dave
You could use either size really, but we've migrated to the 4x8 sheet size for the last couple of years, but I could blast out a quick cut plan for XLs in 5x5ft . I can tell you off the bat that you will need 2 sheets. Indeed, the break-out is such that even when nested for CNC routing, you can't yield all 14 pieces from a single 4x8
Note also that if not using 18mm for front baffle, to fully rebate the 10s doesn't leave a lot of core material for mounting screws - so laminating a thin layer (6-9mm) at the top of the baffle behind the through hole would be a good idea.
Note also that if not using 18mm for front baffle, to fully rebate the 10s doesn't leave a lot of core material for mounting screws - so laminating a thin layer (6-9mm) at the top of the baffle behind the through hole would be a good idea.
Thanks Dave and Chris!
I understand it would take 2 sheets of the 5' x 5'.
I am in Ohio, USA and it seems there is a much bigger selection of the 5' x 5' than the 4' x 8'. Especially within driving distance of me.
Plus 2 sheets of the smaller material is slightly less expensive than 2 of the larger.
If you had a cut plan I could use, that would certainly help a speaker noob like me!!!
Thanks!
Marshall
I understand it would take 2 sheets of the 5' x 5'.
I am in Ohio, USA and it seems there is a much bigger selection of the 5' x 5' than the 4' x 8'. Especially within driving distance of me.
Plus 2 sheets of the smaller material is slightly less expensive than 2 of the larger.
If you had a cut plan I could use, that would certainly help a speaker noob like me!!!
Thanks!
Marshall
Marshall - attached is quickie very rough layout for both sheet sizes.
Note the following:
- the curved panels are nested as tightly as possible for CNC machining, which includes dadoes for the exterior panels, as well as internal divider.
- the dadoes are 5mm deep, and you'll note that back and internal divider are only dadoed on one side, so the front top and bottom are slightly wider than those two panels
- we found out the hard way with an earlier version that dadoes on both sides made for much tougher assembly, particularly with minor variations in thickness of material for which the CNC machining didn't compensate.
These can be built without the use of dadoes, or any type of CNC machining. pocket screws work great for alignment, and are far less fiddly than dowels or biscuits. I built the first 2 pairs of these by hand drawing and fabricating an MDF template for the side panels, rough cutting with jig saw, and cleaning up to pattern with router and flush trim bit.
Drop me a PM if you have any further questions, or would like a more detailed layout pattern for the 5x5 sheets
Note the following:
- the curved panels are nested as tightly as possible for CNC machining, which includes dadoes for the exterior panels, as well as internal divider.
- the dadoes are 5mm deep, and you'll note that back and internal divider are only dadoed on one side, so the front top and bottom are slightly wider than those two panels
- we found out the hard way with an earlier version that dadoes on both sides made for much tougher assembly, particularly with minor variations in thickness of material for which the CNC machining didn't compensate.
These can be built without the use of dadoes, or any type of CNC machining. pocket screws work great for alignment, and are far less fiddly than dowels or biscuits. I built the first 2 pairs of these by hand drawing and fabricating an MDF template for the side panels, rough cutting with jig saw, and cleaning up to pattern with router and flush trim bit.
Drop me a PM if you have any further questions, or would like a more detailed layout pattern for the 5x5 sheets
Attachments
Couple of choices from Amazon.co.uk:
First one looks more compact and with smaller mounting hole requirement.
http://www.amazon.co.uk/Speaker-Squ...4674157&sr=8-11&keywords=speaker+terminal+cup
2 Way Speaker Box Terminal Cup Spring Clip Board with 2 Gold Plated Binding Post: Amazon.co.uk: DIY & Tools
First one looks more compact and with smaller mounting hole requirement.
http://www.amazon.co.uk/Speaker-Squ...4674157&sr=8-11&keywords=speaker+terminal+cup
2 Way Speaker Box Terminal Cup Spring Clip Board with 2 Gold Plated Binding Post: Amazon.co.uk: DIY & Tools
Not really a big fan of spikes for a couple of reasons, but when I do use them, it'll be the type with removable points that allow for application of felt-tack furniture glides.
The FH3 are narrow enough that extend base or outriggers etc are helpful, and depending on implementation can be either subtle, or an artistic addition to the aesthetic of the shape. We had some simple aluminum bars made to form outriggers for the FH3. As the attached photo shows, they're don't particularly call attention to themselves.
FHXL is wide enough that I've found them stable on both hard and carpeted floors, but I'd still use felt glides to prevent damage to flooring.
The FH3 are narrow enough that extend base or outriggers etc are helpful, and depending on implementation can be either subtle, or an artistic addition to the aesthetic of the shape. We had some simple aluminum bars made to form outriggers for the FH3. As the attached photo shows, they're don't particularly call attention to themselves.
FHXL is wide enough that I've found them stable on both hard and carpeted floors, but I'd still use felt glides to prevent damage to flooring.
Attachments
- Home
- Loudspeakers
- Full Range
- Frugel-Horn XL for Alpair 10.3/10p, Fostex FF165wk, more