re:singing strings (post#160)
I started out to install magnetic suspension and inverted Y strings on an old DIY WTA. results were encouraging except for the electric guitar effect with the stylus resting on a record, not spinning, and tapping the strings held taught by the magnets. In #160 above, I requested help in getting around this problem. No replies yet, but I did do some more investigating and testing. In another post it was mentioned that decoupling the counterweight from the arm tube was very important. My arm tube and CW assembly were taken straight from the WTA. For starters I hung the CW from the arm tube with a few inches of soft cloth ribbon. The electric guitar went home! So next I bored out the CW making a 1/2" dia hole. Inserted a Sorbothane plug drilled out for the 1/4" dia arm tube. Now tapping on the strings or directly on the arm tube gives but a dull thud. Rapping on the plinth gives but dull thuds and no groove jumping until I really whack it. Whacking the playing disk on the edge of the disk gives little to no sound in the playback except for right next to the cartridge, and that is slight. So there has been a major improvement. The played back sound is cleaned up significantly as well. I think I can see where decoupling the CW from the arm tube would clean up arm tube resonances. I would not expect such a great reduction of energy from the vibrating suspension strings. Perhaps the strings are still vibrating, and such vibrations are still being coupled onto the arm tube, but the sorbothane isolator is sucking them up and they are not being converted to electrical energy by the cartridge. Any thoughts on this?
Bill
BTW: I have replaced the original Perspex disk with an aluminium disk to aid in eddy current generation. Perspex does nothing for eddy currents. As yet I have some reservations about the eddy current concept in the Schroeder arm bearing. We will leave this issue for a later discussion.
I started out to install magnetic suspension and inverted Y strings on an old DIY WTA. results were encouraging except for the electric guitar effect with the stylus resting on a record, not spinning, and tapping the strings held taught by the magnets. In #160 above, I requested help in getting around this problem. No replies yet, but I did do some more investigating and testing. In another post it was mentioned that decoupling the counterweight from the arm tube was very important. My arm tube and CW assembly were taken straight from the WTA. For starters I hung the CW from the arm tube with a few inches of soft cloth ribbon. The electric guitar went home! So next I bored out the CW making a 1/2" dia hole. Inserted a Sorbothane plug drilled out for the 1/4" dia arm tube. Now tapping on the strings or directly on the arm tube gives but a dull thud. Rapping on the plinth gives but dull thuds and no groove jumping until I really whack it. Whacking the playing disk on the edge of the disk gives little to no sound in the playback except for right next to the cartridge, and that is slight. So there has been a major improvement. The played back sound is cleaned up significantly as well. I think I can see where decoupling the CW from the arm tube would clean up arm tube resonances. I would not expect such a great reduction of energy from the vibrating suspension strings. Perhaps the strings are still vibrating, and such vibrations are still being coupled onto the arm tube, but the sorbothane isolator is sucking them up and they are not being converted to electrical energy by the cartridge. Any thoughts on this?
Bill
BTW: I have replaced the original Perspex disk with an aluminium disk to aid in eddy current generation. Perspex does nothing for eddy currents. As yet I have some reservations about the eddy current concept in the Schroeder arm bearing. We will leave this issue for a later discussion.
Schroeder drawing
From post #44(fdegrove)
er where's the drawing?
I simply lack the facilities to make this tonearm, but would still like to see the drawing. Where do I get it and could it be translated (because I can barely speak my own language, let alone German...)
stew
From post #44(fdegrove)
I didn't spot it at first but from the drawing alone you can actually accurately copy the whole design. If anyone needs help translating the German text, I may be able to help out.
er where's the drawing?
I simply lack the facilities to make this tonearm, but would still like to see the drawing. Where do I get it and could it be translated (because I can barely speak my own language, let alone German...)
stew
Hi,
I have a few questions on the arm wand design:
1. What arm length should be better - a 9/10/12 inch ?
2. What should be the best tube diameter value - 1/4" inch or more ?
3. Should the arm wand be tapered towards the front end or can it maintain the same diameter ?
Regards,
Bins.
I have a few questions on the arm wand design:
1. What arm length should be better - a 9/10/12 inch ?
2. What should be the best tube diameter value - 1/4" inch or more ?
3. Should the arm wand be tapered towards the front end or can it maintain the same diameter ?
Regards,
Bins.
binspaul...go long!
12" arms have substantially better tracking accuracy compared to 9" or 10". It sort of depends what table you plan on using it with and if a 12" can be mounted on the plinth or if an external arm "pod" is to be used.
I would look at something like a Clearaudio Unify12 as a guide for O/S and O/H or perhaps use something with an adjustable O/S headshell type (as used by Clearaudio, Schroeder, etc.)
stew
12" arms have substantially better tracking accuracy compared to 9" or 10". It sort of depends what table you plan on using it with and if a 12" can be mounted on the plinth or if an external arm "pod" is to be used.
I would look at something like a Clearaudio Unify12 as a guide for O/S and O/H or perhaps use something with an adjustable O/S headshell type (as used by Clearaudio, Schroeder, etc.)
stew
Hi Stew,
Did you get the premotec motor ?
I am planning to use it on my custom build table. So, mounting won't be a major issue. As your suggestion, I will go for 12''.
The arm will be based on the Schroeder tonearm. The tube will be made of wood (ebony/teak). What should be the required tube diameter ? Is that a critical factor in the arm performance ? What about the arm shape - Round or tapered ?
Regards,
Bins.
Did you get the premotec motor ?
I am planning to use it on my custom build table. So, mounting won't be a major issue. As your suggestion, I will go for 12''.
The arm will be based on the Schroeder tonearm. The tube will be made of wood (ebony/teak). What should be the required tube diameter ? Is that a critical factor in the arm performance ? What about the arm shape - Round or tapered ?
Regards,
Bins.
Hi,
Last day, I had a talk with a musical instrument maker. What he suggested is to use teak instead of ebony; as teak is more resistant to climate changes and is much lighter.
He also suggested me to try out mahogany. Any idea on this wood ? When I did a Google search, I came to know that it is used in musical instruments making.
See the link: http://en.wikipedia.org/wiki/Mahogany
Any suggestions ?
Best regards,
Bins.
Last day, I had a talk with a musical instrument maker. What he suggested is to use teak instead of ebony; as teak is more resistant to climate changes and is much lighter.
He also suggested me to try out mahogany. Any idea on this wood ? When I did a Google search, I came to know that it is used in musical instruments making.
See the link: http://en.wikipedia.org/wiki/Mahogany
Any suggestions ?
Best regards,
Bins.
binspaul said:Hi,
Last day, I had a talk with a musical instrument maker. What he suggested is to use teak instead of ebony; as teak is more resistant to climate changes and is much lighter.
He also suggested me to try out mahogany. Any idea on this wood ? When I did a Google search, I came to know that it is used in musical instruments making.
See the link: http://en.wikipedia.org/wiki/Mahogany
Any suggestions ?
Best regards,
Bins.
Mahogany is light and stable. It is used in guitar necks, and and blocks (parts internal to the instrument) and is rot resistant. So now you CAN bring your turntable on you yacht!
Hi,
1.
What about the acoustic properties of the wood (Which one will be better: Mahogany or teak or ebony) ?
2. What will be the best tonearm diameter for this (Will 1/4" be enough) ?
3. What should be the best tonearm hole diameter (Thin walled tonearm or thick walled tonearm) ?
Best regards,
Bins.
1.
2. What will be the best tonearm diameter for this (Will 1/4" be enough) ?
3. What should be the best tonearm hole diameter (Thin walled tonearm or thick walled tonearm) ?
Best regards,
Bins.
diameter...
binspaul,
I'd consider 3/8" or so as a minimum. As most wood is somewhat self dampening, I wouldn't worry about a taper, unless you have access to either tapered pieces or a lathe or woodworker friend
Mahogany has a straighter grain and is easily worked with. Teak has less straight grain. Ebony is very dense. Unsure of working properties, but all else being equal, will resonate at a higher frequency than either teak or mahogany.
Personally, given the options listed, I'd look for a "tonewood", so mahogany would be my choice.
PS: can only get the Premotec directly out of Holland, so unlikely I will go that route.
binspaul,
I'd consider 3/8" or so as a minimum. As most wood is somewhat self dampening, I wouldn't worry about a taper, unless you have access to either tapered pieces or a lathe or woodworker friend
Mahogany has a straighter grain and is easily worked with. Teak has less straight grain. Ebony is very dense. Unsure of working properties, but all else being equal, will resonate at a higher frequency than either teak or mahogany.
Personally, given the options listed, I'd look for a "tonewood", so mahogany would be my choice.
PS: can only get the Premotec directly out of Holland, so unlikely I will go that route.
Hi,
I have access to the wood workshop. So, tapering will not be an issue. Which model will be better:
1. Drilling a fine hole through the wooden tube -> This will result in a small hole and hence the arm wand will be much heavier.
2. Splitting the tube into 2 or more small pieces and creating a cavity (Joining the pieces will give us a round hole)
Also, how can we address the tube resonance ? Do we need to damp the tube using some damping elements like foam or sad or something else ?
Best regards,
Bins.
I have access to the wood workshop. So, tapering will not be an issue. Which model will be better:
1. Drilling a fine hole through the wooden tube -> This will result in a small hole and hence the arm wand will be much heavier.
2. Splitting the tube into 2 or more small pieces and creating a cavity (Joining the pieces will give us a round hole)
Also, how can we address the tube resonance ? Do we need to damp the tube using some damping elements like foam or sad or something else ?
Best regards,
Bins.
binspaul said:
1. Drilling a fine hole through the wooden tube -> This will result in a small hole and hence the arm wand will be much heavier.
/B]
What you need is a D-Bit
(from http://www.machineconcepts.co.uk/smallpipes/tools.htm)
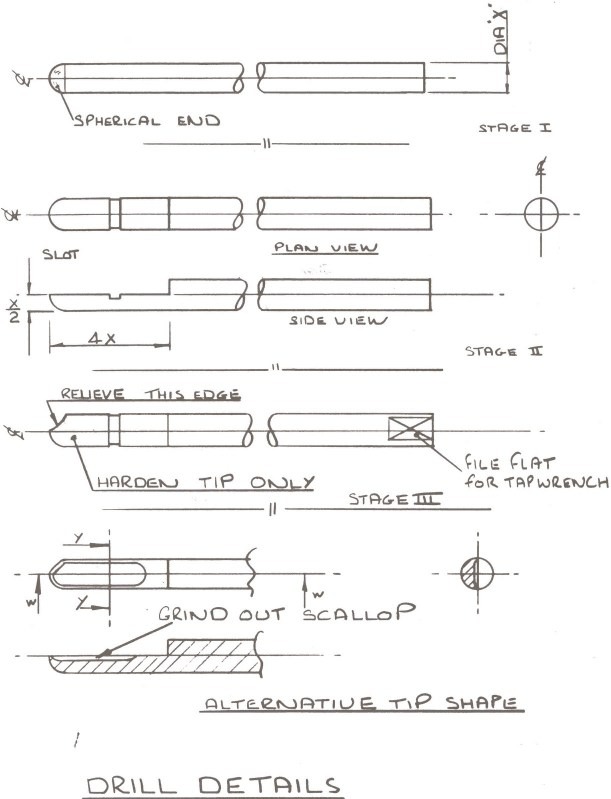
For ease of production: most likely much easier to cut a rebate in 2 halves and then glue together -and the rebate can be sqaure or even just a kerf from a table saw. I have also thought about using a carbon fibre tube up the middle of a wooden tonearm too.
You could drill it out - a long shank drill will probably get you the length required. If you want to go longer distances, the technique is more tricky and really a gun drill is the way to go. That was the only way I could reliably drill a 5mm hole through 360mm of ebony or african black.
The other thing is that I don't think you could go wrong with either ebony or african blackwood. Stable when dry - and you would want to rough turn it first and allow a week or 2 for it to settle. Finishes beautifully too.
Fran
You could drill it out - a long shank drill will probably get you the length required. If you want to go longer distances, the technique is more tricky and really a gun drill is the way to go. That was the only way I could reliably drill a 5mm hole through 360mm of ebony or african black.
The other thing is that I don't think you could go wrong with either ebony or african blackwood. Stable when dry - and you would want to rough turn it first and allow a week or 2 for it to settle. Finishes beautifully too.
Fran
Hi,
According to the original patent, the tonearm can be made of single piece of wood or a sandwich of several woods. The inner diameter of the cavity is just large enough to take the tonearm wires. It will help in avoiding the tonearm resonance.
I think, we can further address the tube resonance, if any using balsa or chalk powder filling.
Best regards,
Bins.
According to the original patent, the tonearm can be made of single piece of wood or a sandwich of several woods. The inner diameter of the cavity is just large enough to take the tonearm wires. It will help in avoiding the tonearm resonance.
I think, we can further address the tube resonance, if any using balsa or chalk powder filling.
Best regards,
Bins.
Hi,
I got some KEVLAR thread from CANSEW INC. The site link is: http://www.cansew.com/category/16.aspx.
Best regards,
Bins.
I got some KEVLAR thread from CANSEW INC. The site link is: http://www.cansew.com/category/16.aspx.
Best regards,
Bins.
Hi Bins,
Good luck with the Kevlar thread. I think this stuff presents some interesting possibilities for Schröder type arms. I am using a single length of Kevlar thread and am pleased with the results. It is the type sold by BassPro shops for tying fishing flies and the spool has no size number on it. In experiments with a test arm wand some things emerge:
The individual strands of Kevlar are very straight and flexible. Soft but strong. Taken together and twisted they become a very strong and non- stretching. Twisted they tighten up into a much smaller diameter thread but do not loose flexibility. As with other threads the more you twist them the greater the antiskating force that develops. But I see the chance of controlling the amount of antiskating force by increasing the number of strands of thread. There will be more force developed with more strands but less turns of twisting needed per unit force developed. Correct me if I'm wrong but what I see experimentally is that a much greater linearity of anti skate across the swept arc of the arm is achieved with less total twisting of the strands. Also you can do a lot of twisting before you see a significant shortening of the thread length/distance between magnets. This tends to reduce the interaction between the magnet spacing screw and the antiskate knob. The bearing is much easier to set up, and the adjustments don't change. It doesn't stretch.
Hint: Make a single knot in this stuff and the knot becomes almost microscopically small. So to prevent the need for a hundred knots to become big enough to not slip through whatever holes the knot has to get locked at, cut a small piece or two of ordinary sewing thread and tie the Kevlar knot around it. This will bulk up the knot but not affect the functionality. Please let us know what you find.
Bill
Good luck with the Kevlar thread. I think this stuff presents some interesting possibilities for Schröder type arms. I am using a single length of Kevlar thread and am pleased with the results. It is the type sold by BassPro shops for tying fishing flies and the spool has no size number on it. In experiments with a test arm wand some things emerge:
The individual strands of Kevlar are very straight and flexible. Soft but strong. Taken together and twisted they become a very strong and non- stretching. Twisted they tighten up into a much smaller diameter thread but do not loose flexibility. As with other threads the more you twist them the greater the antiskating force that develops. But I see the chance of controlling the amount of antiskating force by increasing the number of strands of thread. There will be more force developed with more strands but less turns of twisting needed per unit force developed. Correct me if I'm wrong but what I see experimentally is that a much greater linearity of anti skate across the swept arc of the arm is achieved with less total twisting of the strands. Also you can do a lot of twisting before you see a significant shortening of the thread length/distance between magnets. This tends to reduce the interaction between the magnet spacing screw and the antiskate knob. The bearing is much easier to set up, and the adjustments don't change. It doesn't stretch.
Hint: Make a single knot in this stuff and the knot becomes almost microscopically small. So to prevent the need for a hundred knots to become big enough to not slip through whatever holes the knot has to get locked at, cut a small piece or two of ordinary sewing thread and tie the Kevlar knot around it. This will bulk up the knot but not affect the functionality. Please let us know what you find.
Bill
- Home
- Source & Line
- Analogue Source
- DIY Schroeder Tonearm???