...For adjusting azimuth, I use two #6 brass screws. The top screw is in a short curved channel so the head shell can be turned to both sides while the bottom screw is fixed. The contact of head shell with carriage is very solid.
@ super10018
Clever system/concept ..... it's "super" ... I like it.
Karel
Niffy and all,
Excellent post. I am not going to comment the post in detail since it involves a lot of topics. However, the results don’t surprise me. In my opinion, tracking error is one of factors which causes problem for pivot tonearms. Skating force is the main factor to degrade the performance of pivot tonearms. I can say that nobody can get anti-skating right because skating force is not constant cross the surface of records.
For air bearing tonearms(moving bearing kind), the main problem is air supply line. Air supply line will add resistance to the movement of air bearing. Here is what I did for my air bearing tonearms.
First, I use 1/16” latex tubing. Latex is more flexible than pvc. But latex can’t resist high pressure. The maximum air pressure I can use for latex tubing is 55 psi. I also use a small spring(taking from cheap retractable pen) to hold the joint. Please see the photo. It seems to me that Kuzma airline uses 3 or 4 mm pvc tubing so they can rise the air pressure to 65 psi. I have some 1/16 pvc tubing, too. But it is not as flexible as latex tubing.
The 1/16” latex tubing I use is special one. Usually, for 1/16” latex tubing, its wall is 1/32”. It will not resist even 55 psi. I had tried to order the tubing from different sources and finally I settled on the one I bought from eBay. The latex tubing I bought from eBay has thicker wall. Although it supposes to be 1/32” wall, too, its wall is actually thicker than 1/32”. I don’t know if it is manufacture’s error or something else, it works fine for me. It can resist higher pressure than usual ones.
I thought to add a micro stepper motor to the air line so the air line will move with the carriage. To add stepper motor can reduce the resistance but it can’t completely eliminate the resistance. After many experimenting, I don’t think it is necessary at all. Please check out the video. You can see how little resistance the air line has on my latest air bearing arm.
https://www.youtube.com/watch?v=BlcrqSnh9V8
I think my solution is better than Kuzma’s. My tonearm can do up to 55 psi while Kuzma's can do 65 psi. 10 psi in air pressure will make no difference at all. I have tried all different air pressure starting from 30 psi and to 55 psi. I also tried 65 psi with 1/16” pvc tubing. I can’t hear the difference between 55 psi and 65 psi, but I can tell there was some resistance from 1/16” pvc air tubing under air pressure 65 psi.
I prefer high pressure on the moving bearing kind of tonearm. For moving shaft kind of air bearing arm, it sounds best at 45 psi and 50 psi.
I almost finish my new air bearing arm and can’t wait to hear it.
Jim
Hi Jim,
I watched your video. Stunning implementation. I have the following curiosities:
1) why is the arm oscillating left and right without anybody touching it? are you blowing air with your mouth to move it?
2) I have listened to another video of yours, I am curious to know are you still using Airy 2 cart for testing? What is your sounds system (phono, preamp, amp and speakers)?
Hi Steafno,
In the video, I pushed the air bearing once very lightly, but my hand was not in video. I had to hold my iPhone.
The airy 2 is installed on my other moving bearing tonearm. I took the moving shaft tone arm down. So, both tone arms are moving bearing kind. Yes. I may try the airy 2 on the new tone arm.
My analog system you heard in the video consists of the following equipments.
Aesthetix Io phono preamplifier. Aesthetix Io is an excellent phono. I have owned it for more than 10 years but have no desire to change it at all.
Audio Research Reference II MK2 preamplifier.
dbx 223 active crossover (bi-amping)
High/mid frequency amp: Wolcott P400 mono blocks. 400W per channel.
Low frequency amp: Spectron Musician III. 700W per channel.
Heavily modified Sound Lab Majestic 945.
The video and recording are done with Panasonic Lumix point and shoot small camera. The recording doesn’t really do justification for the actual sound.
Jim
In the video, I pushed the air bearing once very lightly, but my hand was not in video. I had to hold my iPhone.
The airy 2 is installed on my other moving bearing tonearm. I took the moving shaft tone arm down. So, both tone arms are moving bearing kind. Yes. I may try the airy 2 on the new tone arm.
My analog system you heard in the video consists of the following equipments.
Aesthetix Io phono preamplifier. Aesthetix Io is an excellent phono. I have owned it for more than 10 years but have no desire to change it at all.
Audio Research Reference II MK2 preamplifier.
dbx 223 active crossover (bi-amping)
High/mid frequency amp: Wolcott P400 mono blocks. 400W per channel.
Low frequency amp: Spectron Musician III. 700W per channel.
Heavily modified Sound Lab Majestic 945.
The video and recording are done with Panasonic Lumix point and shoot small camera. The recording doesn’t really do justification for the actual sound.
Jim
Last edited:
Very nice system indeed!
What have you modified on your speakers?
How is the stock sound compared to the modified pair?
What have you modified on your speakers?
How is the stock sound compared to the modified pair?
Hi Stefanoo,
I did the following modifications for the 945's.
Heavy duty steel frame.
Ribbon supertweeters.
Completely discarded internal crossover.
Completely get rid of grill cloth.
The sound of modified speakers is much more dynamic. Bass and high are both improved.
Jim
I did the following modifications for the 945's.
Heavy duty steel frame.
Ribbon supertweeters.
Completely discarded internal crossover.
Completely get rid of grill cloth.
The sound of modified speakers is much more dynamic. Bass and high are both improved.
Jim
Hi Jim,
I've completely failed to get any new post notifications and missed the last half dozen posts. I'm not normally a big fan of adjustable azimuth on tonearms. Not because I think correct azimuth alignment isn't important but because most adjustment mechanisms compromise the structure of the arm, you loose more than you gain. You look like you may have cracked the azimuth alignment problem. That looks like a very solid well thought out solution.
I'm still green with envy over your system. Do you still have the Martin Logan rear fill in speakers?
Niffy
I've completely failed to get any new post notifications and missed the last half dozen posts. I'm not normally a big fan of adjustable azimuth on tonearms. Not because I think correct azimuth alignment isn't important but because most adjustment mechanisms compromise the structure of the arm, you loose more than you gain. You look like you may have cracked the azimuth alignment problem. That looks like a very solid well thought out solution.
I'm still green with envy over your system. Do you still have the Martin Logan rear fill in speakers?
Niffy
Hi Niffy,
Yes. I still use a pair of ML speaker for adding ambient sound and didn’t mention in above post.
Jim
Yes. I still use a pair of ML speaker for adding ambient sound and didn’t mention in above post.
Jim
Hi Niffy,
Yes. I still use a pair of ML speaker for adding ambient sound and didn’t mention in above post.
Jim
What do you mean by adding ambient sound?
Hi Stefano,
I had very nice multi channel system before. But the problem is there are too few nice multi channel SACD’s, so I gave it up. However, I still miss the sound of multi channel. I use a pair of ML speaker to try to simulate multi channel.They act as rear speakers as in home theater. I feed these rear speakers with same signals as front main channels and add a volume control to adjust the sound level to my taste.
Hope this helps.
Jim
I had very nice multi channel system before. But the problem is there are too few nice multi channel SACD’s, so I gave it up. However, I still miss the sound of multi channel. I use a pair of ML speaker to try to simulate multi channel.They act as rear speakers as in home theater. I feed these rear speakers with same signals as front main channels and add a volume control to adjust the sound level to my taste.
Hope this helps.
Jim
Hi Stefano,
I had very nice multi channel system before. But the problem is there are too few nice multi channel SACD’s, so I gave it up. However, I still miss the sound of multi channel. I use a pair of ML speaker to try to simulate multi channel.They act as rear speakers as in home theater. I feed these rear speakers with same signals as front main channels and add a volume control to adjust the sound level to my taste.
Hope this helps.
Jim
Hi Jim...thanks for sharing this...
I am more of a "purist" in this regard. I personally prefer hi-end 2 channel listening experience without mixing and matching too many other thing.
If I understand right, you get this other set of speakers, which I am assuming you are powering with independent preamp and power amp and you adjust the volume accordingly to your taste.
Basically you are playing the same information in front and in the back at a lower volume. I never tried this so I cannot comment, but it looks like it is not simulating any more realistic situation given that in the real situation what comes from the back are noises from people or things behind you and reverbs at a specific delay.
Anyway audio tastes are really subjective....so.....I find your approach to be very original!
Jewelled bearings
Hi all,
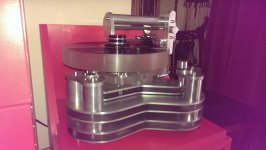
Life still has the habit of getting in the way of what's really important, listening to music and building record players. What with work and my car blowing up and having to buy a new one I've barely even had time to listen to music let alone work on my bearings. But finally I've managed to make the components to fit the jewelled bearings and pivots. I had intended to make the axles and hubs from titanium but had great difficulty working with this material with my limited and basic tools so reverted to aluminium. It was a split decision as to whether to use titanium or aluminium in the first place so I don't consider this a compromise. Accuracy was the most important thing and as the aluminium parts came out better the decision was an easy one. Here's a photo showing the new axles with tungsten carbide pivots and the sapphire vees mounted in their housings.
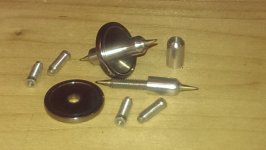
I have to admit that I am gobsmacked by how much lower friction is with these bearings. With the basic steel pin and vees the wheels would spin for 15 seconds with a gentle flick. With the jewelled bearings the wheels span for 45-50 seconds. This indicates that bearing friction is only one third of that with the steel bearings. This doesn't mean that overall friction has reduced by this much. The total lateral friction is due to a combination of the bearings friction and the rolling resistance of the wheels on the rail. The following graph shows the friction distribution for the jewelled bearings running with the tungsten carbide wheels on the tungsten carbide rail. I've included a couple of my previous versions to show the progression in performance. I have also included the plot for the Boca hybrid ball race bearings for comparison
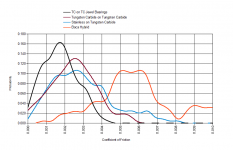
As before a narrow tall peek indicates a more consistent bearing and a peek further to the left indicates lower friction. The jewelled bearings/tungsten carbide wheels combination is clearly lower friction and more consistent than any of the previous versions. The plot is not quite as smooth as the plot for the steel bearings. I am unsure of the reason for this but it may be partially due to the resolution of the measurements. My lateral friction test rig measures side force to an accuracy/resolution of 0.02g, and measurements are taken in multiples of this. This equates to a lateral coefficient of friction with a resolution of about 0.0004. The entire range of values for the jewelled bearings covers only 12 increments and so is approaching the test rigs resolution limit.
I had expected the jewelled bearings and tungsten carbide pivots to reduce overall friction by 10 to 15% compared to the steel bearings. The overall coefficient of friction with the steel bearings was 0.00255. The overall coefficient of friction calculated for the jewelled bearings is only 0.00177. A massive 30% reduction. Very happy. The high grade ball race bearings that I had been using have well over three times as much friction and were nowhere near as consistent. The current configuration is much closer in terms of friction to an air bearing than it is to a ball race system.
Having ascertained that the friction af the jewelled bearing is one third that of the steel bearings I can now determine the proportion of the overall friction which is due to bearing friction and that which is due to rolling resistance. With the jewelled bearings 20-25% of the total friction is due to the bearings and 75-80% is due to rolling resistance.
Having made all of the components for the bearing swap I waited until I had a day off and my wife was away for a couple of days with her work. I got up early so I could start the day listening to a couple of albums to thoroughly get the sound of the deck with the old bearings in my head. Two albums turned into four. How was the sound going to EVER get better than THIS? I was soon to find out. The whole strip down, set up, testing and reassembly and alignment took about 5hrs.
The change in sound was quite dramatic. The sound was brighter. I don't mean that there was an undue emphasis on the treble. I mean it was the audible equivalent to swapping a 60watt bulb for a 100watt. Enough to fully illuminate but not enough to dazzle. The edges of everything becomes clearer. Fine surface texture becomes readably apparent. Natural colours come through vividly. You can also see what's dirty and untidy but you can also see what's clean and neat.
The leading edges of notes are sharper improving transient attack and the notes decay cleaner. Steel strings are vivid. Guitar and piano are that bit more real. Anything percussive really benefits from this transient improvement from drums to cymbals. The separation of separate voices was always a strong point of this arm and has taken another step forward. Image focus and scale are tightened. I was surprised at how much the new bearings have improved the lowest registrars, bass being tighter and faster. At first I thought that the arm had lost a bit of warmth but further listening revealed that what had actually been lost was a bit of softness. A softness that had been masking low level detail. The difference between a poor pressing and a great one is more obvious. The deck does nothing to mask the failings of a poor pressing but also does nothing to hold back a great one.
The main improvement is the way a tune is propelled along. The instances of involuntary toe tapping, head nodding and finger conducting have massively increased. It also nails music into your head, listen to an album in the morning and you'll be humming it all day.
Overall I'd say that the improvements made by upgrading to the jewelled bearings and tungsten carbide pivots are equally as great as the improvements made when I upgraded the wheels from steel to tungsten carbide and when I swapped the rail from glass to tungsten carbide combined.
I think that I have taken mechanical linear tracking tonearm bearings about as far as I can. I think I have the optimum design using the highest quality materials available. The only possible way to improve further would be to have a watch maker precision manufacturer all the components for me, and I doubt that they would be much better. The results are definitely a big step up from the use of ball race bearings. I have probably spent about £300 over about eight months developing these bearings so they are considerably more costly than even top quality ball races. It would have been quite a bit more if hottattoo hadn't given me the tungsten carbide rods. The only bearing system that is likely to improve on my current setup is air bearing and that would be much more expensive again and require an air pump and ideally a separate room to put it in. An air bearing, though having probably lower friction, does not have the same level of mechanical grounding that I believe is responsible for much of the sound quality I'm currently enjoying. Whether I could make an air bearing sound better than this I don't know.
To any of you fellow diyers who have built a linear tracking tonearm and are looking for the next step up in performance I would highly recommend trying a pin bearing design. Manufacture of the components will be easier for those of you who have access to a precision lathe but it is quite possible to make them without one.
Niffy
Hi all,
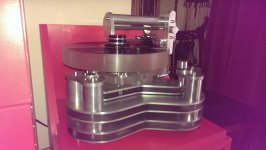
Life still has the habit of getting in the way of what's really important, listening to music and building record players. What with work and my car blowing up and having to buy a new one I've barely even had time to listen to music let alone work on my bearings. But finally I've managed to make the components to fit the jewelled bearings and pivots. I had intended to make the axles and hubs from titanium but had great difficulty working with this material with my limited and basic tools so reverted to aluminium. It was a split decision as to whether to use titanium or aluminium in the first place so I don't consider this a compromise. Accuracy was the most important thing and as the aluminium parts came out better the decision was an easy one. Here's a photo showing the new axles with tungsten carbide pivots and the sapphire vees mounted in their housings.
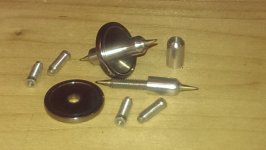
I have to admit that I am gobsmacked by how much lower friction is with these bearings. With the basic steel pin and vees the wheels would spin for 15 seconds with a gentle flick. With the jewelled bearings the wheels span for 45-50 seconds. This indicates that bearing friction is only one third of that with the steel bearings. This doesn't mean that overall friction has reduced by this much. The total lateral friction is due to a combination of the bearings friction and the rolling resistance of the wheels on the rail. The following graph shows the friction distribution for the jewelled bearings running with the tungsten carbide wheels on the tungsten carbide rail. I've included a couple of my previous versions to show the progression in performance. I have also included the plot for the Boca hybrid ball race bearings for comparison
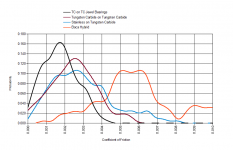
As before a narrow tall peek indicates a more consistent bearing and a peek further to the left indicates lower friction. The jewelled bearings/tungsten carbide wheels combination is clearly lower friction and more consistent than any of the previous versions. The plot is not quite as smooth as the plot for the steel bearings. I am unsure of the reason for this but it may be partially due to the resolution of the measurements. My lateral friction test rig measures side force to an accuracy/resolution of 0.02g, and measurements are taken in multiples of this. This equates to a lateral coefficient of friction with a resolution of about 0.0004. The entire range of values for the jewelled bearings covers only 12 increments and so is approaching the test rigs resolution limit.
I had expected the jewelled bearings and tungsten carbide pivots to reduce overall friction by 10 to 15% compared to the steel bearings. The overall coefficient of friction with the steel bearings was 0.00255. The overall coefficient of friction calculated for the jewelled bearings is only 0.00177. A massive 30% reduction. Very happy. The high grade ball race bearings that I had been using have well over three times as much friction and were nowhere near as consistent. The current configuration is much closer in terms of friction to an air bearing than it is to a ball race system.
Having ascertained that the friction af the jewelled bearing is one third that of the steel bearings I can now determine the proportion of the overall friction which is due to bearing friction and that which is due to rolling resistance. With the jewelled bearings 20-25% of the total friction is due to the bearings and 75-80% is due to rolling resistance.
Having made all of the components for the bearing swap I waited until I had a day off and my wife was away for a couple of days with her work. I got up early so I could start the day listening to a couple of albums to thoroughly get the sound of the deck with the old bearings in my head. Two albums turned into four. How was the sound going to EVER get better than THIS? I was soon to find out. The whole strip down, set up, testing and reassembly and alignment took about 5hrs.
The change in sound was quite dramatic. The sound was brighter. I don't mean that there was an undue emphasis on the treble. I mean it was the audible equivalent to swapping a 60watt bulb for a 100watt. Enough to fully illuminate but not enough to dazzle. The edges of everything becomes clearer. Fine surface texture becomes readably apparent. Natural colours come through vividly. You can also see what's dirty and untidy but you can also see what's clean and neat.
The leading edges of notes are sharper improving transient attack and the notes decay cleaner. Steel strings are vivid. Guitar and piano are that bit more real. Anything percussive really benefits from this transient improvement from drums to cymbals. The separation of separate voices was always a strong point of this arm and has taken another step forward. Image focus and scale are tightened. I was surprised at how much the new bearings have improved the lowest registrars, bass being tighter and faster. At first I thought that the arm had lost a bit of warmth but further listening revealed that what had actually been lost was a bit of softness. A softness that had been masking low level detail. The difference between a poor pressing and a great one is more obvious. The deck does nothing to mask the failings of a poor pressing but also does nothing to hold back a great one.
The main improvement is the way a tune is propelled along. The instances of involuntary toe tapping, head nodding and finger conducting have massively increased. It also nails music into your head, listen to an album in the morning and you'll be humming it all day.
Overall I'd say that the improvements made by upgrading to the jewelled bearings and tungsten carbide pivots are equally as great as the improvements made when I upgraded the wheels from steel to tungsten carbide and when I swapped the rail from glass to tungsten carbide combined.
I think that I have taken mechanical linear tracking tonearm bearings about as far as I can. I think I have the optimum design using the highest quality materials available. The only possible way to improve further would be to have a watch maker precision manufacturer all the components for me, and I doubt that they would be much better. The results are definitely a big step up from the use of ball race bearings. I have probably spent about £300 over about eight months developing these bearings so they are considerably more costly than even top quality ball races. It would have been quite a bit more if hottattoo hadn't given me the tungsten carbide rods. The only bearing system that is likely to improve on my current setup is air bearing and that would be much more expensive again and require an air pump and ideally a separate room to put it in. An air bearing, though having probably lower friction, does not have the same level of mechanical grounding that I believe is responsible for much of the sound quality I'm currently enjoying. Whether I could make an air bearing sound better than this I don't know.
To any of you fellow diyers who have built a linear tracking tonearm and are looking for the next step up in performance I would highly recommend trying a pin bearing design. Manufacture of the components will be easier for those of you who have access to a precision lathe but it is quite possible to make them without one.
Niffy
niffy,
You have done a fantastic job of getting the most performance out of a mechanical linear tonearm !!!
Perhaps some nice pictures of your carriage design and some measurements, and exactly where the jeweled bearings are applied and how they are adjusted. It is a bit difficult to see the jewels in your pictures although I can figure it out, others may not.
Thanks again for all the time and effort you put in to this project. Well done !!!
You have done a fantastic job of getting the most performance out of a mechanical linear tonearm !!!
Perhaps some nice pictures of your carriage design and some measurements, and exactly where the jeweled bearings are applied and how they are adjusted. It is a bit difficult to see the jewels in your pictures although I can figure it out, others may not.
Thanks again for all the time and effort you put in to this project. Well done !!!
I'll try and adapt and label up some drawings over the next couple of days. Exact dimensions would vary depending on the carriage style and design but I'll include the dimensions that I used.
Niffy
Niffy
Niffy.
A well-considered idea & built-up (& tests) with extreme skills & tech & knowledge... & time .
Chapeau bas .... for your "diapason".
If you can share some "basic" specific sketchs I appreciate ....
Thanks.
Karel
A well-considered idea & built-up (& tests) with extreme skills & tech & knowledge... & time .
Chapeau bas .... for your "diapason".
If you can share some "basic" specific sketchs I appreciate ....
Thanks.
Karel
Hi. Let's leave that jaw-dropping turntable aside for now, this linear bearing is truly excellent work. Nicely done niffy.
I would also be delighted with any drawings offered, whether it helps a group buy develop or just makes possible a nearby machine shop being able to make it.
As good as the Laadegard arms are, I think this design would very likely be a level above in all-round performance. Very cool !
I would also be delighted with any drawings offered, whether it helps a group buy develop or just makes possible a nearby machine shop being able to make it.
As good as the Laadegard arms are, I think this design would very likely be a level above in all-round performance. Very cool !
Hi Niffy,
I am impressed by the jewel bearing friction curve. It highly concentrats at 0.0017. and the slope of curve is much higher than others. It means the jewel bearing has very consistent friction.
One question. How do you determine how tight the jewel bearing should be?
Well done.
Jim
I am impressed by the jewel bearing friction curve. It highly concentrats at 0.0017. and the slope of curve is much higher than others. It means the jewel bearing has very consistent friction.
One question. How do you determine how tight the jewel bearing should be?
Well done.
Jim
Bearing adjustment
Hi Jim.
The sapphire vees are mounted at one end of a m3 threaded rod with a slot at the opposite end to allow adjustment with a small screwdriver. Two of these mounts are used per axle, one at either end. First I roughly align both axles so that both wheels are in the same plane, are at 90° to the main axis of the carriage and so the rail passes through the centre of the channel in the carriage. Each of the bearing mounts can be locked into place by a small grub screw in the carriage. I lock both of the rear mounts and adjust bearing play with just the front mounts.
This type of bearing runs best with only a VERY small amount of play. If the bearing is over tightened so that the pivots press into the vees friction Will be higher. If the bearing is to loose the pivot rides up the inside of the vee and again increases friction. The ideal amount of play (called end shake in watch making) is about 10 micron.
To adjust I wind the unlocked mount until the vee is just touching the pivot. I then slightly tightened its locking grub screw to prevent any wobble. I then back of the bearing mounts by unscrewing it by a small amount. A 5° turn on an m3 thread moves the mount by 7 micron. I keep tweaking until the wheel spins for the longest time when given a gentle flick. I then fully tighten locking grub screw and recheck to make sure nothing has shifted. Job done.
Niffy
Hi Jim.
The sapphire vees are mounted at one end of a m3 threaded rod with a slot at the opposite end to allow adjustment with a small screwdriver. Two of these mounts are used per axle, one at either end. First I roughly align both axles so that both wheels are in the same plane, are at 90° to the main axis of the carriage and so the rail passes through the centre of the channel in the carriage. Each of the bearing mounts can be locked into place by a small grub screw in the carriage. I lock both of the rear mounts and adjust bearing play with just the front mounts.
This type of bearing runs best with only a VERY small amount of play. If the bearing is over tightened so that the pivots press into the vees friction Will be higher. If the bearing is to loose the pivot rides up the inside of the vee and again increases friction. The ideal amount of play (called end shake in watch making) is about 10 micron.
To adjust I wind the unlocked mount until the vee is just touching the pivot. I then slightly tightened its locking grub screw to prevent any wobble. I then back of the bearing mounts by unscrewing it by a small amount. A 5° turn on an m3 thread moves the mount by 7 micron. I keep tweaking until the wheel spins for the longest time when given a gentle flick. I then fully tighten locking grub screw and recheck to make sure nothing has shifted. Job done.
Niffy
- Home
- Source & Line
- Analogue Source
- DIY linear tonearm