... I got mine (in DIY) for 30EURO ....
Believe me ... it's music, I like it ....
Top.
Karel
Wait..you bought a TP3 Pro here in the DIY forum for 30euros??
Wait..you bought a TP3 Pro here in the DIY forum for 30euros??
I think he meant he made it for 30 Euros....
Just like that. The cartridge mounting holes centres are 12.7mm apart and 2.5mm in diameter so you have 10.2mm between the bolts. Just enough room for a an 8mm arrow shaft.
Niffy
Last edited:
I think he meant he made it for 30 Euros....
oh he made one for 30 euros? good for him. It would cost me more to have a shop work all these parts, I wonder how he was able to get everything with with 30 euros....good for him!
At first glance it seems very complicated to implement. How are the two slides going to be installed so precisely. Carrier has X-shape and would have to be CNCed.
I don’t know how to implement the slides yet. But I think one should have kind of mechanism to adjust the distance and position between the sliders.
Why would this solution produce an improvement?
What is the armwand resting on? Ball bearings instead of spikes?
First, two air bearings can hold the carriage more stable and reduce up and down motions. Second, making the pin and v-cup this way, it will have better control of the pin(spikes). The am wand has two pins. The pins are against the v-cups. There must a mechanism to adjust the tightness of the pins and the v-cups.
Btw..congrats your hand drawing skill is amazing!
Painting and drawing is my another passion.
This might be a great idea but I don't know exactly in detail how this could work out. I would be interested to explore some improvements if you have anything in mind. Perhaps this one is really extensive. I am looking at the drawing and thinking how can the armwand freely move between the sliders.
yes your drawing skill in great I can tell you like to draw
yes your drawing skill in great I can tell you like to draw
Hi all.
The Tungsten Carbide rings arrived today.
They are sold as wedding rings. They look perfect for the task. I measured them with a micrometer and the results were pretty good. Both were circular to within about 10micron and were also the same size to within 10micron and more importantly the perfect size for the task. As a comparison I measured one of the stainless steel wheels I had made. Remember I don't possess a lathe. These were made in a pillar drill with a file and sandpaper. These were only circular to 50micron, not bad considering the production method. So as I hoped they are more circular than my current wheels. This should help make the level of friction more consistent, the plot on the graph should be taller and narrower and hopefully at a lower friction level. Now I have to make them into wheels, test them and most importantly listen to how they effect sound quality.
Happy days.
Niffy
The Tungsten Carbide rings arrived today.
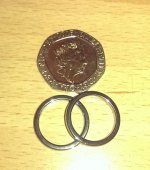
They are sold as wedding rings. They look perfect for the task. I measured them with a micrometer and the results were pretty good. Both were circular to within about 10micron and were also the same size to within 10micron and more importantly the perfect size for the task. As a comparison I measured one of the stainless steel wheels I had made. Remember I don't possess a lathe. These were made in a pillar drill with a file and sandpaper. These were only circular to 50micron, not bad considering the production method. So as I hoped they are more circular than my current wheels. This should help make the level of friction more consistent, the plot on the graph should be taller and narrower and hopefully at a lower friction level. Now I have to make them into wheels, test them and most importantly listen to how they effect sound quality.
Happy days.
Niffy
Tungten carbide wheels
Hi all,
I've had frustratingly little time for building and testing since I last posted but I have now managed to turn the tungsten carbide rings into wheels.
I'm still only using the basic pin bearings as I'm determinedly making only one change at a time so I can clearly see/hear the difference each change makes in isolation. The new wheels are titanium with the tungsten carbide rings as rims. I contemplated making the centres from aluminium in order to reduce mass and made wheels in both materials for comparison. The titanium ones had a much better feel to them and their greater hardness and stiffness should aid mechanical grounding. I also modelled the effect of the different masses in my carriage design spreadsheet to see how each would effect effective mass and the overall centre of mass and its effect on tracking force variations due to warps. I also modelled the effect of using the different materials for the axles and hubs. To be honest the variations were to small to have any real significance. When starting the whole design process I set targets for vertical and lateral cantilever compliance resonance (based on my current cartridge) and tracking force variation on an average unclamped record warps (0.3mm). My targets were 9.5hz vertical, 4.5hz lateral and less than 1% tracking force variation. The best combination of wheel materials gave me 9.45hz vertical, 4.54hz lateral and a tracking force variation of 0.75% (in reality this figure will be much lower as I have a very effective warps flattening clamp). Pretty close all round. The diagram below shows the materials selected for the wheels and rail.
I managed to avoid the temptation to put the new wheels straight onto the arm and start listening. I thoroughly tested the wheels in the same way as with the previous versions. The graph below shows the comparison between the steel wheels and the tungsten carbide wheels both on the tungsten carbide rail. The steel wheels plot looks a bit different from the previous post as I have halved the amount of smoothing. As before lower friction is to the left., a peek further to the left indicates lower friction. A taller, narrower peek with smoother sides shows a more consistent bearing.
The difference between the two types is immediately obvious. The curve for the tungsten carbide wheels is very smooth and taller showing greater consistency. The irregularities in the steel wheels plot that I had assumed were due irregularities in the pivots are now obviously due to irregularities in the steel wheels. Although the mode (the highest point) in both plots is at the same coefficient of friction, 0.0026, the mean value for the tungsten carbide wheels is much lower. The mean for the steel wheels was 0.0030 giving a composite of 0.0028. The mean for the tungsten carbide wheels is 0.0025 giving a composite of 0.00255. That's a further reduction of 17% mean and 9% composite. All moving in the right direction. The cause of the lump off the right hand side of this plot, at 0.0055, is a bit of a mystery.
As performed previously I also checked vertical friction using the simple pendulum test. This indicated that vertical friction also dropped by about 17%. This is in line with the calculated drop of 20%.
Rolling the test carriage back and forth on the rail was surprisingly noisier than with the steel wheels, still much quieter than the ball race bearings.
Now the all important sound quality bit.
On initial setup there was a noticeable richness to the sound. This was like the improved midrange presence that the tungsten carbide rail had brought but extended over the whole audio spectrum. Very nice. However the overall sound lacked the grip and drive it had possessed, it all sounded a bit recessed, diminished. I stripped the whole arm down and reset everything. A small improvement but still lacking somewhere. Despair, I had hoped for so much. Then the discovery. For consistency I try to perform critical evaluation listening always at the same volume, 10 o'clock on the dial. Somehow the grub screw that secures the volume control had come loose allowing the knob to slop on its shaft. Where I thought it was at 10 it was more like 8 o'clock. Having tightened the control I started again at the correct level. The richness remained. The grip and drive returned bringing their buddies detail and clarity with them. The soundstage is broader and deeper with even greater separation of separate instruments. It's even easier to follow a single instrument during a complex passage. If anything this is an even bigger improvement than the step from glass to tungsten carbide for the rail, it's just so clean.
I was feeling that I was approaching the limit of what I could squeeze out of my deck. These new bearings have improved things more than I ever imagined they could. For anyone considering building a mechanical linear tracking tonearm I would definitely recommend copying my current setup, pin bearings and lashings of tungsten carbide. The further I travel down this path the further and further it's leaving ball race bearings behind.
Niffy
Hi all,
I've had frustratingly little time for building and testing since I last posted but I have now managed to turn the tungsten carbide rings into wheels.

I'm still only using the basic pin bearings as I'm determinedly making only one change at a time so I can clearly see/hear the difference each change makes in isolation. The new wheels are titanium with the tungsten carbide rings as rims. I contemplated making the centres from aluminium in order to reduce mass and made wheels in both materials for comparison. The titanium ones had a much better feel to them and their greater hardness and stiffness should aid mechanical grounding. I also modelled the effect of the different masses in my carriage design spreadsheet to see how each would effect effective mass and the overall centre of mass and its effect on tracking force variations due to warps. I also modelled the effect of using the different materials for the axles and hubs. To be honest the variations were to small to have any real significance. When starting the whole design process I set targets for vertical and lateral cantilever compliance resonance (based on my current cartridge) and tracking force variation on an average unclamped record warps (0.3mm). My targets were 9.5hz vertical, 4.5hz lateral and less than 1% tracking force variation. The best combination of wheel materials gave me 9.45hz vertical, 4.54hz lateral and a tracking force variation of 0.75% (in reality this figure will be much lower as I have a very effective warps flattening clamp). Pretty close all round. The diagram below shows the materials selected for the wheels and rail.
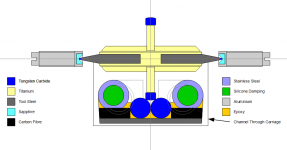
I managed to avoid the temptation to put the new wheels straight onto the arm and start listening. I thoroughly tested the wheels in the same way as with the previous versions. The graph below shows the comparison between the steel wheels and the tungsten carbide wheels both on the tungsten carbide rail. The steel wheels plot looks a bit different from the previous post as I have halved the amount of smoothing. As before lower friction is to the left., a peek further to the left indicates lower friction. A taller, narrower peek with smoother sides shows a more consistent bearing.

The difference between the two types is immediately obvious. The curve for the tungsten carbide wheels is very smooth and taller showing greater consistency. The irregularities in the steel wheels plot that I had assumed were due irregularities in the pivots are now obviously due to irregularities in the steel wheels. Although the mode (the highest point) in both plots is at the same coefficient of friction, 0.0026, the mean value for the tungsten carbide wheels is much lower. The mean for the steel wheels was 0.0030 giving a composite of 0.0028. The mean for the tungsten carbide wheels is 0.0025 giving a composite of 0.00255. That's a further reduction of 17% mean and 9% composite. All moving in the right direction. The cause of the lump off the right hand side of this plot, at 0.0055, is a bit of a mystery.
As performed previously I also checked vertical friction using the simple pendulum test. This indicated that vertical friction also dropped by about 17%. This is in line with the calculated drop of 20%.
Rolling the test carriage back and forth on the rail was surprisingly noisier than with the steel wheels, still much quieter than the ball race bearings.
Now the all important sound quality bit.
On initial setup there was a noticeable richness to the sound. This was like the improved midrange presence that the tungsten carbide rail had brought but extended over the whole audio spectrum. Very nice. However the overall sound lacked the grip and drive it had possessed, it all sounded a bit recessed, diminished. I stripped the whole arm down and reset everything. A small improvement but still lacking somewhere. Despair, I had hoped for so much. Then the discovery. For consistency I try to perform critical evaluation listening always at the same volume, 10 o'clock on the dial. Somehow the grub screw that secures the volume control had come loose allowing the knob to slop on its shaft. Where I thought it was at 10 it was more like 8 o'clock. Having tightened the control I started again at the correct level. The richness remained. The grip and drive returned bringing their buddies detail and clarity with them. The soundstage is broader and deeper with even greater separation of separate instruments. It's even easier to follow a single instrument during a complex passage. If anything this is an even bigger improvement than the step from glass to tungsten carbide for the rail, it's just so clean.
I was feeling that I was approaching the limit of what I could squeeze out of my deck. These new bearings have improved things more than I ever imagined they could. For anyone considering building a mechanical linear tracking tonearm I would definitely recommend copying my current setup, pin bearings and lashings of tungsten carbide. The further I travel down this path the further and further it's leaving ball race bearings behind.
Niffy
Thanks Joe,
I have tried to be as scientific as possible in the development of these bearings. Gathering lots of information allows me to make more informed design choices.
Heading up an R&D department sounds like a dream job. What I could do with a materials testing lab and fully equipped workshop and a bigger budget! Though would it be as much fun? Probably even more so. Though part of the joy of this deck is that it was entirely built on a workmate in the corner of my kitchen, no fancy machine shop.
Any manufacturers out there fancy giving me a shot? Lol
Niffy
I have tried to be as scientific as possible in the development of these bearings. Gathering lots of information allows me to make more informed design choices.
Heading up an R&D department sounds like a dream job. What I could do with a materials testing lab and fully equipped workshop and a bigger budget! Though would it be as much fun? Probably even more so. Though part of the joy of this deck is that it was entirely built on a workmate in the corner of my kitchen, no fancy machine shop.
Any manufacturers out there fancy giving me a shot? Lol
Niffy
Hi,
high work load, poor salary, no budgets, no glory .... You´d rather think again
jauu
Calvin
That's exactly what I was going to say!
Audio companies have very low budgets. Their business is really small! Also, they all certainly make things to fit on a very tight budget like any other commercial engineering company.
However, you will definitely have access to more tools and prototyping facility which will then simplify your own side works.
That's for sure...
Hi Niffy
These two wheels look very nice!
I also looked the chart of friction. Beside friction, the stainless steel wheels have large tolerance of roundness. Its curve is not as smooth as the titanium wheels with the tungsten carbide rings. In other words, the roundness is playing a role here, too. Anyway, it doesn’t overthrow your conclusion that the wheels with carbide rings are better than stainless ones in your case.
Congratulations!
Jim
These two wheels look very nice!
I also looked the chart of friction. Beside friction, the stainless steel wheels have large tolerance of roundness. Its curve is not as smooth as the titanium wheels with the tungsten carbide rings. In other words, the roundness is playing a role here, too. Anyway, it doesn’t overthrow your conclusion that the wheels with carbide rings are better than stainless ones in your case.
Congratulations!
Jim
Investigation into lateral tracking errors pt1
Hi all,
In between my recent spates of building I have been investigating some claims posted on various forums regarding different types of arms and their effects on lateral tracking error. Basically many people have claimed that due to their high lateral mass and the bearing friction in mechanical bearings or the stiffness of the air hose in air bearings that linear tracking arms have worse lateral tracking errors than conventional pivoted arms when having to deal with eccentric records. Lots of options were given but no one had actually investigated the validity of the claim.
To investigate this claim I created mathematical models of a variety of arm types and modelled the effect of a record with its centre 0.5mm away from its rotational centre. This would result in the arm moving left/right by 1mm every revolution of the record. This is quite a high level of eccentricity but not uncommon. In following this investigation I kept my personal bias completely out of the equations as I wanted as accurate a picture as possible.
I took into account 6 different factors that will effect lateral tracking angle. They are:
1. Arm geometry.
This only applies to pivoted arms. I chose to model this effect using a Baerwald alignment. Baerwald alignment has the null points at 66mm and 120.9mm. The inner null is located close to the inner groove to help reduce inner track distortion and gives a more consistent sound across the whole record side.
2. Skating force.
Again this only applies to pivoted arms. Skating force varies due to the location of the arm over the record and the level of groove modulation. I set anti-skate so that skating error would be at an average minimum. Of course records recorded at above or below average levels will have higher error than those recorded at average level. This was the most difficult to model but I think I have a good representation of reality.
3. Groove angle.
This error is caused by the record moving backwards and forwards. The amount of error swings from a positive maximum to a negative maximum and back to the positive once every rotation of the record. A cartridge movement of 1mm would mean that the record is misaligned by a maximum of just under a quarter of a degree at the outer groove and by almost a half degree at the inner. This error is independent of arm types and forms a baseline. No arm geometry can reduce this, the only way to reduce it is to reduce eccentricity and that's a different story.
4. Mass inertia. This error is caused by the force acting on the stylus required to accelerate the arm back and forth. This force will be largely dependent on the mass of the arm, a heavier arm mass will result in a higher force and thus greater error. This error occurs with all arm types but is normally much lower for pivoted arms as it is only the effective mass rather than the whole carriage mass that has to be accelerated. As with groove angle this error cycles from positive to negative once per revolution.
5. Bearing friction. As you probably know I have been heavily investigating bearing friction for mechanical linear tracking tonearms. The results of this testing have been extensively used in the calculation of friction in this section. A low level of friction will require less force acting on the stylus to move the carriage resulting in lower levels of lateral tracking error. Pivoted arms have a mechanical advantage as the long arm tubes act as a lever reducing the effect of bearing friction. Air bearings also offer almost zero friction, the majority of the air bearing friction for a moving bearing design is due to the flexibility of the air supply tube.
6. Bearing play. All bearings have a small amount of play. I am assuming that the pivoted arms in my model are high quality and any play will be reduced by the long armtube to insignificant levels. Also the play in a high pressure air bearing will be virtually zero. The amount of play in a mechanical linear tracking tonearm will be dependent on bearing quality. Even with low grade bearings the effect of bearing play will be very small but I have included it anyway for the sake of completeness.
Having calculated the effect of each of the above factors on lateral tracking angle they now need to be combined to yield a total tracking error. Unfortunately they cannot be simply added together. Most of the factors vary dependent on the rotational position of the record. For instance if the maximum for groove angle occurs at 0° the maximum for mass inertia occurs at about 90°. Each of the factors need to be summed taking this into account or the final result will be higher than reality.
Each of the factors were calculated to find both the maximum and the average tracking error over a full rotation of the record at all locations across the record from 60mm to 145mm from the centre. The average over a single rotation is the more revealing of the two.
I modelled 6 different arms using the above factors. I used my current cartridge, an Ortofon 2m black, as the basis for the model. This cartridge has an effective mass of 22um/mN, a recommend tracking force of 1.5g and a cantilever approximately 5mm long. All arms were modelled with this cartridge assumed to be set up perfectly. The 6 arms are:
1. 9" pivoted arm. This arm has an effective mass of 12g (which would give a compliance resonance of 9.8hz) and set up with a Baerwald alignment.
2. 12" pivoted arm. Again 12g effective mass and Baerwald alignment.
3. Mechanical linear tracking tonearm with standard grade ball bearings running on glass rods. I made this model as similar as possible to the carriages built by most of the contributors to this thread. This model has a carriage mass of 30g. (which would give a lateral compliance resonance of 6.2hz) I used my measurements for the full ceramic zirconium oxide bearings as the basis for bearing friction. These bearings are probably slightly better than the standard grade bearings used by many here but should be close enough to draw reasonable conclusions.
4. Mechanical linear tracking tonearm with high grade ball bearings running on glass rods. This model is the same as the previous at 30g but uses the measurements for the Boca hybrid bearings.
5. My arm as it currently is using tungsten carbide wheels on tungsten carbide rods and the basic pin bearings. Total carriage mass in this case is 55g. (this would give a compliance resonance of 4.5hz)
6. Air bearing design very similar to my current arm but with the wheels replaced with an air bushing. This is modelled as a moving bearing design with flexible air lines and a total carriage mass of 85g. (this would give a compliance resonance of 3.7hz)
The two graphs below show the separate factors that contribute to lateral tracking error for the 9" pivoted arm and my pin bearing linear arm. I excluded the effect of bearing play for the pivoted arm as its effect was virtually zero. Arm geometry and skating error are not present for the linear tracking tonearm as these are factors that only effect pivoted arms. Both graphs shown the average tracking error, averaged over one full revolution across the whole record. All graphs are shown with the same vertical scale to enable easier comparison. The purple line in both graphs shows groove angle and represents the minimum possible average tracking error for this level of eccentricity. Of particular interest in the pivoted arm graph is the red plot that shows skating force error. This is calculated assuming perfect anti-skate adjustment. Even perfectly set up anti-skate still leaves errors as great as those due to groove angle changes. Even if the record was perfectly concentric the level of skating error would still be at this level. The single largest contributing factor for the pivoted arm is the arm geometry as shown in dark blue.
The dark green plot in the linear tracking graph shows the level of error due to the mass inertia factor. This is at a very low level and definitely does not contribute anywhere near enough error to increase total error to be as much as that of a pivoted arm. Having said that, this is still a quite a lightweight arm and a heavier arm would have had a greater effect but not to anywhere near the level some have claimed. The red plot on this graph shows average bearing friction which is the largest contributing factor apart from groove angle.
Niffy
Hi all,
In between my recent spates of building I have been investigating some claims posted on various forums regarding different types of arms and their effects on lateral tracking error. Basically many people have claimed that due to their high lateral mass and the bearing friction in mechanical bearings or the stiffness of the air hose in air bearings that linear tracking arms have worse lateral tracking errors than conventional pivoted arms when having to deal with eccentric records. Lots of options were given but no one had actually investigated the validity of the claim.
To investigate this claim I created mathematical models of a variety of arm types and modelled the effect of a record with its centre 0.5mm away from its rotational centre. This would result in the arm moving left/right by 1mm every revolution of the record. This is quite a high level of eccentricity but not uncommon. In following this investigation I kept my personal bias completely out of the equations as I wanted as accurate a picture as possible.
I took into account 6 different factors that will effect lateral tracking angle. They are:
1. Arm geometry.
This only applies to pivoted arms. I chose to model this effect using a Baerwald alignment. Baerwald alignment has the null points at 66mm and 120.9mm. The inner null is located close to the inner groove to help reduce inner track distortion and gives a more consistent sound across the whole record side.
2. Skating force.
Again this only applies to pivoted arms. Skating force varies due to the location of the arm over the record and the level of groove modulation. I set anti-skate so that skating error would be at an average minimum. Of course records recorded at above or below average levels will have higher error than those recorded at average level. This was the most difficult to model but I think I have a good representation of reality.
3. Groove angle.
This error is caused by the record moving backwards and forwards. The amount of error swings from a positive maximum to a negative maximum and back to the positive once every rotation of the record. A cartridge movement of 1mm would mean that the record is misaligned by a maximum of just under a quarter of a degree at the outer groove and by almost a half degree at the inner. This error is independent of arm types and forms a baseline. No arm geometry can reduce this, the only way to reduce it is to reduce eccentricity and that's a different story.
4. Mass inertia. This error is caused by the force acting on the stylus required to accelerate the arm back and forth. This force will be largely dependent on the mass of the arm, a heavier arm mass will result in a higher force and thus greater error. This error occurs with all arm types but is normally much lower for pivoted arms as it is only the effective mass rather than the whole carriage mass that has to be accelerated. As with groove angle this error cycles from positive to negative once per revolution.
5. Bearing friction. As you probably know I have been heavily investigating bearing friction for mechanical linear tracking tonearms. The results of this testing have been extensively used in the calculation of friction in this section. A low level of friction will require less force acting on the stylus to move the carriage resulting in lower levels of lateral tracking error. Pivoted arms have a mechanical advantage as the long arm tubes act as a lever reducing the effect of bearing friction. Air bearings also offer almost zero friction, the majority of the air bearing friction for a moving bearing design is due to the flexibility of the air supply tube.
6. Bearing play. All bearings have a small amount of play. I am assuming that the pivoted arms in my model are high quality and any play will be reduced by the long armtube to insignificant levels. Also the play in a high pressure air bearing will be virtually zero. The amount of play in a mechanical linear tracking tonearm will be dependent on bearing quality. Even with low grade bearings the effect of bearing play will be very small but I have included it anyway for the sake of completeness.
Having calculated the effect of each of the above factors on lateral tracking angle they now need to be combined to yield a total tracking error. Unfortunately they cannot be simply added together. Most of the factors vary dependent on the rotational position of the record. For instance if the maximum for groove angle occurs at 0° the maximum for mass inertia occurs at about 90°. Each of the factors need to be summed taking this into account or the final result will be higher than reality.
Each of the factors were calculated to find both the maximum and the average tracking error over a full rotation of the record at all locations across the record from 60mm to 145mm from the centre. The average over a single rotation is the more revealing of the two.
I modelled 6 different arms using the above factors. I used my current cartridge, an Ortofon 2m black, as the basis for the model. This cartridge has an effective mass of 22um/mN, a recommend tracking force of 1.5g and a cantilever approximately 5mm long. All arms were modelled with this cartridge assumed to be set up perfectly. The 6 arms are:
1. 9" pivoted arm. This arm has an effective mass of 12g (which would give a compliance resonance of 9.8hz) and set up with a Baerwald alignment.
2. 12" pivoted arm. Again 12g effective mass and Baerwald alignment.
3. Mechanical linear tracking tonearm with standard grade ball bearings running on glass rods. I made this model as similar as possible to the carriages built by most of the contributors to this thread. This model has a carriage mass of 30g. (which would give a lateral compliance resonance of 6.2hz) I used my measurements for the full ceramic zirconium oxide bearings as the basis for bearing friction. These bearings are probably slightly better than the standard grade bearings used by many here but should be close enough to draw reasonable conclusions.
4. Mechanical linear tracking tonearm with high grade ball bearings running on glass rods. This model is the same as the previous at 30g but uses the measurements for the Boca hybrid bearings.
5. My arm as it currently is using tungsten carbide wheels on tungsten carbide rods and the basic pin bearings. Total carriage mass in this case is 55g. (this would give a compliance resonance of 4.5hz)
6. Air bearing design very similar to my current arm but with the wheels replaced with an air bushing. This is modelled as a moving bearing design with flexible air lines and a total carriage mass of 85g. (this would give a compliance resonance of 3.7hz)
The two graphs below show the separate factors that contribute to lateral tracking error for the 9" pivoted arm and my pin bearing linear arm. I excluded the effect of bearing play for the pivoted arm as its effect was virtually zero. Arm geometry and skating error are not present for the linear tracking tonearm as these are factors that only effect pivoted arms. Both graphs shown the average tracking error, averaged over one full revolution across the whole record. All graphs are shown with the same vertical scale to enable easier comparison. The purple line in both graphs shows groove angle and represents the minimum possible average tracking error for this level of eccentricity. Of particular interest in the pivoted arm graph is the red plot that shows skating force error. This is calculated assuming perfect anti-skate adjustment. Even perfectly set up anti-skate still leaves errors as great as those due to groove angle changes. Even if the record was perfectly concentric the level of skating error would still be at this level. The single largest contributing factor for the pivoted arm is the arm geometry as shown in dark blue.
The dark green plot in the linear tracking graph shows the level of error due to the mass inertia factor. This is at a very low level and definitely does not contribute anywhere near enough error to increase total error to be as much as that of a pivoted arm. Having said that, this is still a quite a lightweight arm and a heavier arm would have had a greater effect but not to anywhere near the level some have claimed. The red plot on this graph shows average bearing friction which is the largest contributing factor apart from groove angle.
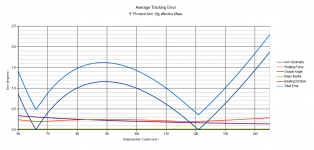
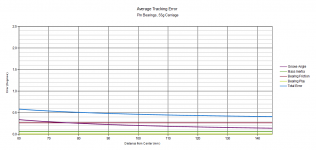
Niffy
Investigation into lateral tracking errors pt2
The two graphs in this section show the totalled lateral tracking errors for the 6 arms previously described. The first graph shows the average tracking error over a single revolution of the record. The second graph shows the maximum tracking error that is likely to occur during a single revolution of the record. I have included the error due to groove angle, dashed green line, separately in both graphs as this shows the minimum possible tracking error.
As can clearly be seen in this graph both the pivoted arms have much greater average tracking errors than any of the linear tracking arms. Only at their null points do they drop below the friction of the linear arms and even at the null points the air bearing arm is still as low. Although the pin bearing arm, light green, shows a tracking error almost as low as for the air bearing, plum, it has to be taken into consideration that the air bearing arm is considerably heavier. Likewise the ball race arm using high quality bearings, red, only gets as close to the pin bearing arm because it is much lighter still. This highlights the advantage of a low friction bearing design as it allows the use of a more massive rigid carriage without paying the price in increased lateral tracking error.
Another feature common to all of the linear arms is that the tracking error remains much more constant across the record than either of the pivoted arms. This can be highlighted further by looking at the overall average across the whole record. The overall average tracking errors are:
9" pivoted. 12g 1.202°
12" pivoted. 12g 0.912°
Std grade ball race. 30g 0.878°
High grade ball race. 30g 0.601°
Pin bearing. 55g 0.469°
Air bearing. 85g 0.407°
Even the std grade ball race arm has lower average tracking error than the 12" pivoted arm although the difference is quite small. This does seem to partially confirm the original hypothesis that bearing friction in mechanical linear tracking arms can cause tracking errors as great as those in pivoted arms. It is of course pitching the best of one breed against the worst of the other and still coming up short. When the advantage of being able to utilize short arm tubes is added into the equation the linear tracking arm moves even further ahead.
The next graph shows the maximum tracking error that can occur during a single revolution of the record
The most notable feature of this graph is that the maximum tracking error for the std grade ball race bearings exceeds that of the 12" pivoted arm for most of the record and is similar to the 9" on average. This shows that although the variations averaged over a whole record may be lower the variations within a single rotation are higher. This is due to the low consistency of this type of bearing and would recommend that anyone considering building a mechanical linear tracking tonearm with ball race bearings avoid the basic grade bearings and buy the best quality available. This was confirmed in my listening tests
All of the calculations and testing would indicate that air bearings do offer the lowest levels of lateral tracking error. This is of course only one aspect of tonearm design and in itself does not guarantee high sound quality.
On the initial premise that bearing friction can cause tracking errors as great as those in pivoted arms. This is only true if you select low grade bearings if you are using a low mass arm, so is not a fair comparison. High quality bearings in a low mass linear arm will offer significantly lower lateral tracking error than even the best pivoted arm.
On the premise that the high mass of a linear tracking arm causes tracking errors as great as a pivoted arm. I don't think that this investigation has totally debunked this or relegated it to myth. To approach the same average level as a 12" arm would require an arm mass, using the same 22um/mN cartridge, of 600g. (assuming moving air bearing with flexible air line). Remember that this is still assuming that there is a high level, 1mm peek to peek, of record eccentricity. With a record with little or no eccentricity the tracking error for the pivoted arm would drop only fractionally whereas with the air bearing it will drop to virtually zero.
However combining the two premises... If you were to be using the high grade ball race bearings the carriages mass would then only need to be 50g before the average tracking error was as great as the average for a 12" arm. This figure was derived using all the same factors as used throughout this investigation. I originally had these bearings on my carriage which had a total mass of 53g which would have meant that my average tracking error was slightly greater than that of a 12" pivoted arm. Even at this mass the linear arm would be much more consistent across the record and the absolute maximum tracking error seen would still be considerably less than that for the pivoted arm. Plus My 100mm total length carriage has better resonance control than is possible with a 300-350mm armtube so any minor losses in terms of tracking angle are more than made up for.
All this shows that the level of consideration that has to be paid to every aspect of tonearm design. So it is possible to create an linear arm with worse tracking error that a pivoted arm but it's just as easy to make one with with a lot less as well
Niffy
The two graphs in this section show the totalled lateral tracking errors for the 6 arms previously described. The first graph shows the average tracking error over a single revolution of the record. The second graph shows the maximum tracking error that is likely to occur during a single revolution of the record. I have included the error due to groove angle, dashed green line, separately in both graphs as this shows the minimum possible tracking error.
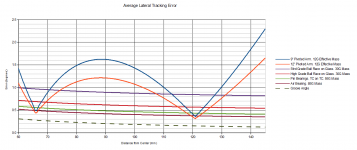
As can clearly be seen in this graph both the pivoted arms have much greater average tracking errors than any of the linear tracking arms. Only at their null points do they drop below the friction of the linear arms and even at the null points the air bearing arm is still as low. Although the pin bearing arm, light green, shows a tracking error almost as low as for the air bearing, plum, it has to be taken into consideration that the air bearing arm is considerably heavier. Likewise the ball race arm using high quality bearings, red, only gets as close to the pin bearing arm because it is much lighter still. This highlights the advantage of a low friction bearing design as it allows the use of a more massive rigid carriage without paying the price in increased lateral tracking error.
Another feature common to all of the linear arms is that the tracking error remains much more constant across the record than either of the pivoted arms. This can be highlighted further by looking at the overall average across the whole record. The overall average tracking errors are:
9" pivoted. 12g 1.202°
12" pivoted. 12g 0.912°
Std grade ball race. 30g 0.878°
High grade ball race. 30g 0.601°
Pin bearing. 55g 0.469°
Air bearing. 85g 0.407°
Even the std grade ball race arm has lower average tracking error than the 12" pivoted arm although the difference is quite small. This does seem to partially confirm the original hypothesis that bearing friction in mechanical linear tracking arms can cause tracking errors as great as those in pivoted arms. It is of course pitching the best of one breed against the worst of the other and still coming up short. When the advantage of being able to utilize short arm tubes is added into the equation the linear tracking arm moves even further ahead.
The next graph shows the maximum tracking error that can occur during a single revolution of the record
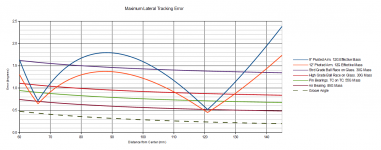
The most notable feature of this graph is that the maximum tracking error for the std grade ball race bearings exceeds that of the 12" pivoted arm for most of the record and is similar to the 9" on average. This shows that although the variations averaged over a whole record may be lower the variations within a single rotation are higher. This is due to the low consistency of this type of bearing and would recommend that anyone considering building a mechanical linear tracking tonearm with ball race bearings avoid the basic grade bearings and buy the best quality available. This was confirmed in my listening tests
All of the calculations and testing would indicate that air bearings do offer the lowest levels of lateral tracking error. This is of course only one aspect of tonearm design and in itself does not guarantee high sound quality.
On the initial premise that bearing friction can cause tracking errors as great as those in pivoted arms. This is only true if you select low grade bearings if you are using a low mass arm, so is not a fair comparison. High quality bearings in a low mass linear arm will offer significantly lower lateral tracking error than even the best pivoted arm.
On the premise that the high mass of a linear tracking arm causes tracking errors as great as a pivoted arm. I don't think that this investigation has totally debunked this or relegated it to myth. To approach the same average level as a 12" arm would require an arm mass, using the same 22um/mN cartridge, of 600g. (assuming moving air bearing with flexible air line). Remember that this is still assuming that there is a high level, 1mm peek to peek, of record eccentricity. With a record with little or no eccentricity the tracking error for the pivoted arm would drop only fractionally whereas with the air bearing it will drop to virtually zero.
However combining the two premises... If you were to be using the high grade ball race bearings the carriages mass would then only need to be 50g before the average tracking error was as great as the average for a 12" arm. This figure was derived using all the same factors as used throughout this investigation. I originally had these bearings on my carriage which had a total mass of 53g which would have meant that my average tracking error was slightly greater than that of a 12" pivoted arm. Even at this mass the linear arm would be much more consistent across the record and the absolute maximum tracking error seen would still be considerably less than that for the pivoted arm. Plus My 100mm total length carriage has better resonance control than is possible with a 300-350mm armtube so any minor losses in terms of tracking angle are more than made up for.
All this shows that the level of consideration that has to be paid to every aspect of tonearm design. So it is possible to create an linear arm with worse tracking error that a pivoted arm but it's just as easy to make one with with a lot less as well
Niffy
Niffy and all,
Excellent post. I am not going to comment the post in detail since it involves a lot of topics. However, the results don’t surprise me. In my opinion, tracking error is one of factors which causes problem for pivot tonearms. Skating force is the main factor to degrade the performance of pivot tonearms. I can say that nobody can get anti-skating right because skating force is not constant cross the surface of records.
For air bearing tonearms(moving bearing kind), the main problem is air supply line. Air supply line will add resistance to the movement of air bearing. Here is what I did for my air bearing tonearms.
First, I use 1/16” latex tubing. Latex is more flexible than pvc. But latex can’t resist high pressure. The maximum air pressure I can use for latex tubing is 55 psi. I also use a small spring(taking from cheap retractable pen) to hold the joint. Please see the photo. It seems to me that Kuzma airline uses 3 or 4 mm pvc tubing so they can rise the air pressure to 65 psi. I have some 1/16 pvc tubing, too. But it is not as flexible as latex tubing.
The 1/16” latex tubing I use is special one. Usually, for 1/16” latex tubing, its wall is 1/32”. It will not resist even 55 psi. I had tried to order the tubing from different sources and finally I settled on the one I bought from eBay. The latex tubing I bought from eBay has thicker wall. Although it supposes to be 1/32” wall, too, its wall is actually thicker than 1/32”. I don’t know if it is manufacture’s error or something else, it works fine for me. It can resist higher pressure than usual ones.
I thought to add a micro stepper motor to the air line so the air line will move with the carriage. To add stepper motor can reduce the resistance but it can’t completely eliminate the resistance. After many experimenting, I don’t think it is necessary at all. Please check out the video. You can see how little resistance the air line has on my latest air bearing arm.
https://www.youtube.com/watch?v=BlcrqSnh9V8
I think my solution is better than Kuzma’s. My tonearm can do up to 55 psi while Kuzma's can do 65 psi. 10 psi in air pressure will make no difference at all. I have tried all different air pressure starting from 30 psi and to 55 psi. I also tried 65 psi with 1/16” pvc tubing. I can’t hear the difference between 55 psi and 65 psi, but I can tell there was some resistance from 1/16” pvc air tubing under air pressure 65 psi.
I prefer high pressure on the moving bearing kind of tonearm. For moving shaft kind of air bearing arm, it sounds best at 45 psi and 50 psi.
I almost finish my new air bearing arm and can’t wait to hear it.
Jim
Excellent post. I am not going to comment the post in detail since it involves a lot of topics. However, the results don’t surprise me. In my opinion, tracking error is one of factors which causes problem for pivot tonearms. Skating force is the main factor to degrade the performance of pivot tonearms. I can say that nobody can get anti-skating right because skating force is not constant cross the surface of records.
For air bearing tonearms(moving bearing kind), the main problem is air supply line. Air supply line will add resistance to the movement of air bearing. Here is what I did for my air bearing tonearms.
First, I use 1/16” latex tubing. Latex is more flexible than pvc. But latex can’t resist high pressure. The maximum air pressure I can use for latex tubing is 55 psi. I also use a small spring(taking from cheap retractable pen) to hold the joint. Please see the photo. It seems to me that Kuzma airline uses 3 or 4 mm pvc tubing so they can rise the air pressure to 65 psi. I have some 1/16 pvc tubing, too. But it is not as flexible as latex tubing.
The 1/16” latex tubing I use is special one. Usually, for 1/16” latex tubing, its wall is 1/32”. It will not resist even 55 psi. I had tried to order the tubing from different sources and finally I settled on the one I bought from eBay. The latex tubing I bought from eBay has thicker wall. Although it supposes to be 1/32” wall, too, its wall is actually thicker than 1/32”. I don’t know if it is manufacture’s error or something else, it works fine for me. It can resist higher pressure than usual ones.
I thought to add a micro stepper motor to the air line so the air line will move with the carriage. To add stepper motor can reduce the resistance but it can’t completely eliminate the resistance. After many experimenting, I don’t think it is necessary at all. Please check out the video. You can see how little resistance the air line has on my latest air bearing arm.
https://www.youtube.com/watch?v=BlcrqSnh9V8
I think my solution is better than Kuzma’s. My tonearm can do up to 55 psi while Kuzma's can do 65 psi. 10 psi in air pressure will make no difference at all. I have tried all different air pressure starting from 30 psi and to 55 psi. I also tried 65 psi with 1/16” pvc tubing. I can’t hear the difference between 55 psi and 65 psi, but I can tell there was some resistance from 1/16” pvc air tubing under air pressure 65 psi.
I prefer high pressure on the moving bearing kind of tonearm. For moving shaft kind of air bearing arm, it sounds best at 45 psi and 50 psi.
I almost finish my new air bearing arm and can’t wait to hear it.
Jim
Attachments
Last edited:
WOW Jim,
That is one smooth running bearing! I might have over calculated the effect of the stiffness of the air supply tube in my previous post, maybe by as much as a tenth of a degree. Very impressed.
The new carriage looks fantastic. It looks much more like a single solid component than your previous versions which I think will make a positive difference. Tapering the headshell in the way you have is an excellent idea. It will take mass away from where you want it least, the end of the arm. This will definitely help to keep the vertical effective mass down but will have little effect on the overall rigidity of the arm. Tapering the arm is in this way will therefore push the resonant frequency of the carriage up even further, a very good thing indeed.
Combining the ultra rigid carriage construction with the increased rigidity of the 1" bearing and the higher than normal effective masses should keep that cartridge body rock solid. I imagine good thing will flow from your sound labs.
Niffy
That is one smooth running bearing! I might have over calculated the effect of the stiffness of the air supply tube in my previous post, maybe by as much as a tenth of a degree. Very impressed.
The new carriage looks fantastic. It looks much more like a single solid component than your previous versions which I think will make a positive difference. Tapering the headshell in the way you have is an excellent idea. It will take mass away from where you want it least, the end of the arm. This will definitely help to keep the vertical effective mass down but will have little effect on the overall rigidity of the arm. Tapering the arm is in this way will therefore push the resonant frequency of the carriage up even further, a very good thing indeed.
Combining the ultra rigid carriage construction with the increased rigidity of the 1" bearing and the higher than normal effective masses should keep that cartridge body rock solid. I imagine good thing will flow from your sound labs.
Niffy
Hi Niffy,
Thank you for encouraging words!
Actually, the bearing can run ever more resistant free. The arm lifting device on the back of carriage toucheed the back part of arm slightly. This added more friction.
For this arm, I have pay great attention to its functionality as well as cosmetically. I will post all the updates in my diy air bearing arm thread later on.
The head shell turns out to be a pretty good. I sank the cut parts in epoxy first, then, sanded them. After gluing them together, I coated two more layers of epoxy. It is pretty rigid now.
For adjusting azimuth, I use two #6 brass screws. The top screw is in a short curved channel so the head shell can be turned to both sides while the bottom screw is fixed. The contact of head shell with carriage is very solid.
Thank you for encouraging words!
Actually, the bearing can run ever more resistant free. The arm lifting device on the back of carriage toucheed the back part of arm slightly. This added more friction.
For this arm, I have pay great attention to its functionality as well as cosmetically. I will post all the updates in my diy air bearing arm thread later on.
The head shell turns out to be a pretty good. I sank the cut parts in epoxy first, then, sanded them. After gluing them together, I coated two more layers of epoxy. It is pretty rigid now.
For adjusting azimuth, I use two #6 brass screws. The top screw is in a short curved channel so the head shell can be turned to both sides while the bottom screw is fixed. The contact of head shell with carriage is very solid.
Attachments
- Home
- Source & Line
- Analogue Source
- DIY linear tonearm