Who says I’m not teachable
After busting a tap last Friday by pushing myself, I decided to quit while I was ahead this evening. I turned the 60 deg. taper on the top of my bushing, and mounted it in the top plate, and called it quits for the night…
… I ran the bushing through the heat/cool oil cycle 3 times before cutting and mounting it in the sleeve that would in turn be mounted in the plate. I then ran it through one more to bond the Slick50 to the freshly cut surface. The bushing has an interference fit of -.002” into the sleeve, and the sleeve has a interference fit of -.001” into the plate. The final bore turned out to be a smidge under .251”.
I’ll start on the new spindle to match the tapered bushing in the morning.
-Casey
After busting a tap last Friday by pushing myself, I decided to quit while I was ahead this evening. I turned the 60 deg. taper on the top of my bushing, and mounted it in the top plate, and called it quits for the night…
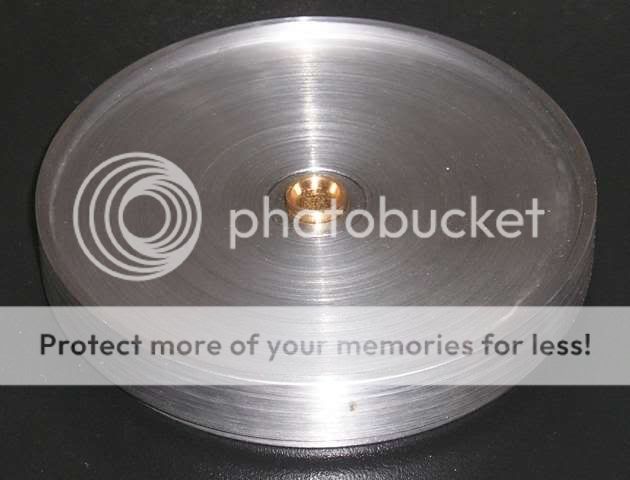
… I ran the bushing through the heat/cool oil cycle 3 times before cutting and mounting it in the sleeve that would in turn be mounted in the plate. I then ran it through one more to bond the Slick50 to the freshly cut surface. The bushing has an interference fit of -.002” into the sleeve, and the sleeve has a interference fit of -.001” into the plate. The final bore turned out to be a smidge under .251”.
I’ll start on the new spindle to match the tapered bushing in the morning.
-Casey

JesseG said:The suggestion has also provided me with a possible solution to another problem - I am building a fluid-damped string suspension tonearm. I have been looking for a source for the silicon fluid used by the factory ones, but with no success. It is very possible that a viscous fluid like Slick50 would serve just as well and offer a huge advantage - availability!
Hot digiddy! I love these forums![]()
Jess [/B]
Jess !!
Sorry to take so long to point this out for you...but I receintly came across this on Ebay (concerning the silicone you were requiring for your tonearm) :-
http://cgi.ebay.co.uk/ws/eBayISAPI....loc=closed_view_item&refwidgettype=osi_widget
You just never know when something is going to test every bit of your patience. In this case it was my new pulley spindle. On the first go, It fought me from the beginning, and after several hours of frustrating work, the cutting tool chattered and bent it. The second one took almost as long, and just as I was finishing up, it slipped and lost it’s center on the lathe, putting the pulley end slightly off the center line. I decided that this could be fixed fairly easily by turning it down a touch later and using a shim to make up the difference, so a third spindle wasn’t made.
One of the reasons I originally went with caged bearings, is that by stacking 2 or more together, you can get away without having a bearing on the other end of the shaft (provided it’s a short shaft). With bushings you can’t, so I had to re-work the design to accommodate this. I turned a spacer ring and matching cap for the back , and pressed in the bushing. Here are the three new pieces…
I attached the ring to the top plate with “JB Weld”. I didn’t trust the epoxy to hold it with just the mating surfaces glued, so I cut a small v-groove in the side of the ring, and undercut a small groove in the plate as well…It’s not coming off. To align the bushings, I rested the plate upside down on the pulley spindle so that the plate could spin freely. I then slid the back bushing assembly over it, by spinning the plate/ assembly together, the bushing found it’s center. I left it overnight to cure. Here is the front and back view of the new “bearing” with spindle…
Gentlemen..it’s as smooth as a baby’s bee-hind. I will make a small flywheel to mount between the bushings, and I’m sure it will be very q-u-i-e-t.
All the above was done on a very long Saturday, and this morning when I woke I felt it. I really didn’t feel like doing much today, so I set myself the goal of making the housing for the motor. I promised myself that this was all I would do today. I tend to make mistakes when I’m tired and sore, and I have too much time invested in this motor to roach it now.
I mounted a piece of steel pipe on my lathe, and cut a shoulder to press fit the top plate. I cut it so it’s snug, but not so tight I couldn’t knock it apart easily. While it was still mounted on the lathe, I tapped the plate in. Since the taper I cut in my bushing is 60 deg., it fits the live-center on the tail-stock perfectly. With the plate and pipe together, I turned the outside. I then cut it to length, and after removing the plate, mounted the finished piece the other way on the chuck, and finished the bottom with another shoulder for the foot plate. Here’s the housing by itself…
…and here’s the motor mocked up sitting in it’s final destination…
All that’s left is turning the flywheel, a little drilling and tapping, and the final assembly. With any luck it should be done soon.
Does anybody have a suggestion for my power cord? I need a three wire with a shield that is fairly small, and is pliable.
I think I’m going to go soak in the tub…
-Casey
One of the reasons I originally went with caged bearings, is that by stacking 2 or more together, you can get away without having a bearing on the other end of the shaft (provided it’s a short shaft). With bushings you can’t, so I had to re-work the design to accommodate this. I turned a spacer ring and matching cap for the back , and pressed in the bushing. Here are the three new pieces…
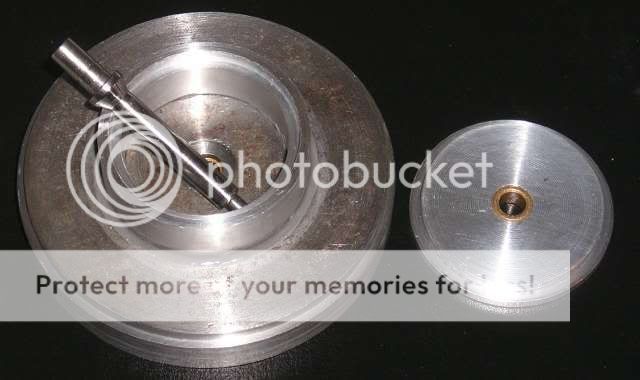
I attached the ring to the top plate with “JB Weld”. I didn’t trust the epoxy to hold it with just the mating surfaces glued, so I cut a small v-groove in the side of the ring, and undercut a small groove in the plate as well…It’s not coming off. To align the bushings, I rested the plate upside down on the pulley spindle so that the plate could spin freely. I then slid the back bushing assembly over it, by spinning the plate/ assembly together, the bushing found it’s center. I left it overnight to cure. Here is the front and back view of the new “bearing” with spindle…
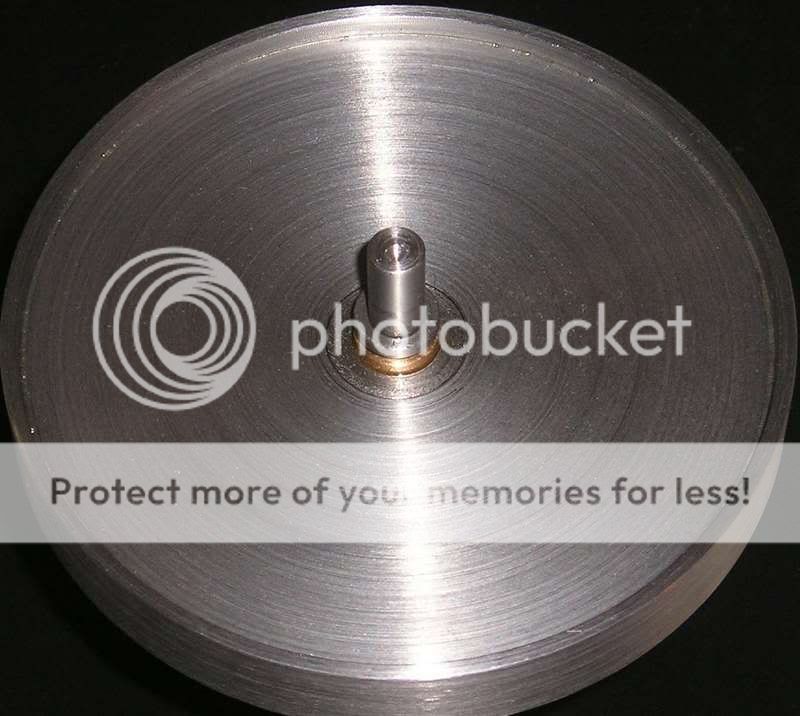
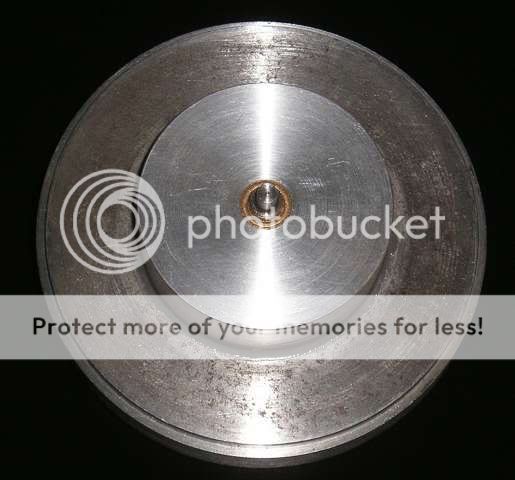
Gentlemen..it’s as smooth as a baby’s bee-hind. I will make a small flywheel to mount between the bushings, and I’m sure it will be very q-u-i-e-t.
All the above was done on a very long Saturday, and this morning when I woke I felt it. I really didn’t feel like doing much today, so I set myself the goal of making the housing for the motor. I promised myself that this was all I would do today. I tend to make mistakes when I’m tired and sore, and I have too much time invested in this motor to roach it now.
I mounted a piece of steel pipe on my lathe, and cut a shoulder to press fit the top plate. I cut it so it’s snug, but not so tight I couldn’t knock it apart easily. While it was still mounted on the lathe, I tapped the plate in. Since the taper I cut in my bushing is 60 deg., it fits the live-center on the tail-stock perfectly. With the plate and pipe together, I turned the outside. I then cut it to length, and after removing the plate, mounted the finished piece the other way on the chuck, and finished the bottom with another shoulder for the foot plate. Here’s the housing by itself…
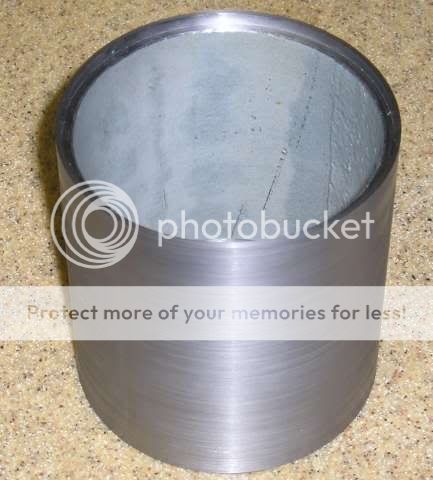
…and here’s the motor mocked up sitting in it’s final destination…
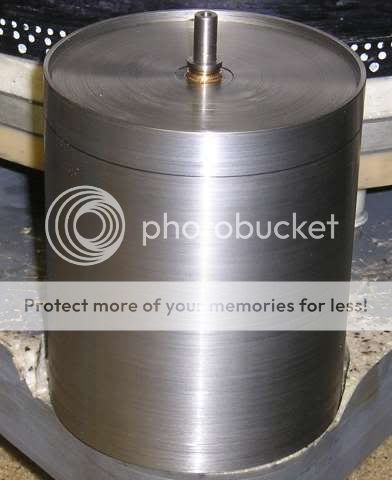
All that’s left is turning the flywheel, a little drilling and tapping, and the final assembly. With any luck it should be done soon.
Does anybody have a suggestion for my power cord? I need a three wire with a shield that is fairly small, and is pliable.
I think I’m going to go soak in the tub…
-Casey
Help...
After thumbing the catalogs for a suitable wire for my motor, I'm no closer than before I started.
What I need is a small (under 1/4") pliable (like mic/headphone cable) 3 or 4 (preferably 4) conductor with a shield seperate from the conductors. It only needs to handle 100ma, but needs an insulator jacket rated at 120vac.
Oh ya...I would like to buy something less than a 500' roll.
Thoughts ?
-Casey
After thumbing the catalogs for a suitable wire for my motor, I'm no closer than before I started.
What I need is a small (under 1/4") pliable (like mic/headphone cable) 3 or 4 (preferably 4) conductor with a shield seperate from the conductors. It only needs to handle 100ma, but needs an insulator jacket rated at 120vac.
Oh ya...I would like to buy something less than a 500' roll.
Thoughts ?
-Casey
valveitude said:Help...
After thumbing the catalogs for a suitable wire for my motor, I'm no closer than before I started.
What I need is a small (under 1/4") pliable (like mic/headphone cable) 3 or 4 (preferably 4) conductor with a shield seperate from the conductors. It only needs to handle 100ma, but needs an insulator jacket rated at 120vac.
Oh ya...I would like to buy something less than a 500' roll.
Thoughts ?
-Casey
I googled mic cable and got these guys first:
http://www.gigcables.com/CNbulkmic.html
They sell by the foot too!
Jeff
NJoyTheMUSIC - Thanks for the link - I emailed them and bought some silicon fluid direct - me happy 
Velvitude - beautiful job (expected nothing less
)
email me and I will send you some cable: I have the perfect stuff -German-made, 2 conductors with 2 layers of shielding, rated at 250VAC, light and very flexible. about 1/4" OD. I will be happy to contribute 15' to this very exciting project.
Christmas coming - not ready
Jess
Velvitude - beautiful job (expected nothing less
email me and I will send you some cable: I have the perfect stuff -German-made, 2 conductors with 2 layers of shielding, rated at 250VAC, light and very flexible. about 1/4" OD. I will be happy to contribute 15' to this very exciting project.
Christmas coming - not ready

Jess
Jeff-
Thanx for the link..a quick look shows it's promising, I'll look a little deeper when I get home.
rdf-
Cast linear crystal power buss..hmm
Jess-
Thats a very generous offer, and I thank you. The problem is I need at least 3 conductors plus the shield. In a normal setup using a phase shifting capacitor, it would indeed be perfect..naturally my approach aint normal. I want to change the speed without changing the pulley, and with an AC motor the way to do this is to change the AC frequency...a description of my speed control is here . Bottom line, I need to feed the motor coils seperately. At a min. I need a common and 2 coil wires plus the shield.
-Casey
Thanx for the link..a quick look shows it's promising, I'll look a little deeper when I get home.
rdf-
Cast linear crystal power buss..hmm

Jess-
Thats a very generous offer, and I thank you. The problem is I need at least 3 conductors plus the shield. In a normal setup using a phase shifting capacitor, it would indeed be perfect..naturally my approach aint normal. I want to change the speed without changing the pulley, and with an AC motor the way to do this is to change the AC frequency...a description of my speed control is here . Bottom line, I need to feed the motor coils seperately. At a min. I need a common and 2 coil wires plus the shield.
-Casey
valveitude said:
... The problem is I need at least 3 conductors plus the shield....
-Casey
god, is there no pleasing some people ?!?!?!
Don't you just cringe when you hear these over-fussy, pernikity types ??
HAAA HAAAA ...!!!
Only Kidding Case !
Just keep those ideas & high standards going mate !
JesseG said:NJoyTheMUSIC - Thanks for the link - I emailed them and bought some silicon fluid direct - me happy
Hi Jess !
That's great - Glad I can be of some help to someone !
I was thinking that maybe the 'Slick50' wasn't quite what you really needed for your tonearm project.
Please let me know how the project gets on - I'm looking to do something similar in the future..
-Andy-
Hey Andy,
Apparently not
Hello pixpop,
An intriguing idea..I don't think they are shielded though. It is about the size and pliability I'm looking for...hmm, maybe adding the shield would be worth it...I'll give it some thought. Thanx.
-Casey
god, is there no pleasing some people ?!?!?!
Apparently not
Hello pixpop,
I reckon you'd get away with using a mouse cable
An intriguing idea..I don't think they are shielded though. It is about the size and pliability I'm looking for...hmm, maybe adding the shield would be worth it...I'll give it some thought. Thanx.
-Casey
USB 1 cable is a quad of twisted wire surround by a heavy foild shield. I've played around with it for interconnect, technically it's ideal. Not sure of the voltage rating though. The best made I found came from the low-end Microsoft Intellimouse. (No, really.) If you want to be tweaky+, leave the ferrite RFI filter on the cable at the input to the motor.
rdf-
Egg-suh-lent , It does sound ideal. As far as the voltage rating goes, it would actually be pretty hard to make an insulator that wouldn't hold up to 125vac ( it is a insulator after all), not to mention that the shield would be connected to earth ground. If a fault occured, it would blow the planned 100ma fuse in short order.
Anybody got a dead Microsoft Intellimouse they want to donate to the cause?
Thanx guys,
Casey
USB 1 cable is a quad of twisted wire surround by a heavy foild shield. I've played around with it for interconnect, technically it's ideal. Not sure of the voltage rating though.
Egg-suh-lent , It does sound ideal. As far as the voltage rating goes, it would actually be pretty hard to make an insulator that wouldn't hold up to 125vac ( it is a insulator after all), not to mention that the shield would be connected to earth ground. If a fault occured, it would blow the planned 100ma fuse in short order.
Anybody got a dead Microsoft Intellimouse they want to donate to the cause?
Thanx guys,
Casey
FROM valvitude
Guess what Casey, I got some of that too
The 3-conductor I have (about 20') is 16ga, also rated for 250V @ 1A. It has a single foil shield around all 3 conductors (white, black, green). It came from a government tube transmitter installation - Coast Guard, I think. It is not a flexible as the other, but still not bad. OD of the cable is just under 3/8". If you want it it's yours.
Please don't use mouse wire, USB cable or network cable. There may be enough copper in them, but the insulation will not tolerate 120VAC. The cables will arc between them right thru the insulator. Please believe me! I am a computer network eng. in my daytime life and I had to learn all about the ratings of these cables. Being the subborn SOB I am, I tried powering a phono stage with some of this (<15ma) and it melted itself and kicked the house breaker in about 15 sec.
If you want to go look for some cable, find a local marine electronics store and ask them for a length of power cable from an old (>20yrs) radar set. Best power cable on the planet - rated to 20Kv. If no marine dealers near you, try military surplus.
FROM NjoyTHEMUSIC
It will be my pleasure to post the project as soon as there is something to show. I have been inspired by Caseys detailed documentation of his work to take lots of pictures. I get a 2-week break over xmas, so will get some work done then (and listening) I hope
Cheers all
Jess
The problem is I need at least 3 conductors plus the shield.
Guess what Casey, I got some of that too
Please don't use mouse wire, USB cable or network cable. There may be enough copper in them, but the insulation will not tolerate 120VAC. The cables will arc between them right thru the insulator. Please believe me! I am a computer network eng. in my daytime life and I had to learn all about the ratings of these cables. Being the subborn SOB I am, I tried powering a phono stage with some of this (<15ma) and it melted itself and kicked the house breaker in about 15 sec.
If you want to go look for some cable, find a local marine electronics store and ask them for a length of power cable from an old (>20yrs) radar set. Best power cable on the planet - rated to 20Kv. If no marine dealers near you, try military surplus.
FROM NjoyTHEMUSIC
Please let me know how the project gets on - I'm looking to do something similar in the future..
It will be my pleasure to post the project as soon as there is something to show. I have been inspired by Caseys detailed documentation of his work to take lots of pictures. I get a 2-week break over xmas, so will get some work done then (and listening) I hope
Cheers all
Jess
I missed the comment about the 120V motor, I thought Casey was going to use a low voltage dc motor with the proposed cables.
I have to go with JesseG on this one, all those choices are highly inappropriate for the application. Nothing like watching the cable burn which might happen even with the fuse. There has got to be a more appropriate choice. Perhaps Belden makes a small power cable with a belfoil shield. I know there are 18 gauge computer power cables that are shielded and pretty flexible too. (eBay) They are even UL approved.
Set something on fire with non approved wire and your insurance company might take a pretty dim view of your hobby..
I have to go with JesseG on this one, all those choices are highly inappropriate for the application. Nothing like watching the cable burn which might happen even with the fuse. There has got to be a more appropriate choice. Perhaps Belden makes a small power cable with a belfoil shield. I know there are 18 gauge computer power cables that are shielded and pretty flexible too. (eBay) They are even UL approved.
Set something on fire with non approved wire and your insurance company might take a pretty dim view of your hobby..
.kevinkr said:Set something on fire with non approved wire and your insurance company might take a pretty dim view of your hobby..
...and I for one would not like to see Casey's machine workshop go up in flames [well, at least not B4 he duplicates some of those lovely parts fur us, eh ?!?]

Only kidding !
- Status
- This old topic is closed. If you want to reopen this topic, contact a moderator using the "Report Post" button.
- Home
- Source & Line
- Analogue Source
- Corian Turntable Fun