Waveguide shape
how do you calculate this oval variant
A 40 x 90 with some Kentucky windage LOL
Waveguide shape
Im not sure which shape you have calculated, but looks OS Gedlee inspired
If so, how do you calculate this oval variant
I suppose you know all about that, but just fore the record, if a round OS shape is "pushed" to oval, its been mathematically changed to someting different
Thank you!
It probably seems as though I just randomly picked the shape but I did do quite a bit of research:
The shape is an elliptical (not oval) cone inspired by constant directivity rectangular horns. Some basic design elements were taken from this paper and adapted to this shape. The throat radius is as described in that paper to maintain the wavefront at 90 degrees to the wall. The mouth radius is meant to control the midrange beaming issue.
I assume OS is oblate spheroid? This is definitely not that shape, an oblate spheroid would have concave walls:
it is a squished ball. The mouth would be the same elliptical shape as mine but I can't see any advantage to having the walls concave.
John, In the case of an OS waveguide, the profile of the wall is a part section of the picture from the equator to the pole on any longitudinal line.
So concave like I said - bowl shaped?
I'm not getting it.
I've seen Geddes waveguide and the sides appear straight.
OK, I just figured it out. It's slightly ridiculous to name something after a 3D geometrical object (spheroid) when you are only using a portion of the curvature of what is, in fact, an ellipse.
Last edited:
Material suggestion for your horn
Very interesting casting you have made. Check out the website for Abatron to look at some really good casting and molding compounds. It is more expensive than plaster, but is also extremely strong, can be machined.
It is commonly used for restoration work, even for exterior columns, etc.
Good luck!
Very interesting casting you have made. Check out the website for Abatron to look at some really good casting and molding compounds. It is more expensive than plaster, but is also extremely strong, can be machined.
It is commonly used for restoration work, even for exterior columns, etc.
Good luck!
Abatron to look at some really good casting and molding compounds. It is more expensive than plaster, but is also extremely strong, can be machined.
Thanks for the suggestion.
Really the only drawback with using the plaster is dry time - it literally takes days to dry a casting out enough to do anything with. Other than that it is perfect: sets fast (in minutes), is very smooth, is strong and is easily sanded and filled to fix problems. Did I mention cheap?
Ok, I got some stuff done. I split the negative in half and did a little machining on it to open the throat and route in the recess that casts the CD mounting flange:
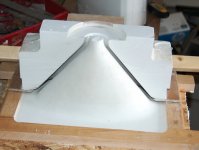
You can see the space where the casting resin will go to form the horn flare. It's coming together nicely now and is nearly complete.
Last edited:
Hope you use enough bond breaker. When we were doing boats, we used twice the recommended coats of wax then had a beer (or maybe two) so we'd forget and start again.
Drinkin' on de job, eh?
I'll grease 'er up good when the time comes.
(BTW, nice surgical work to excise the extra spheroid pic

Yes indeed that really does look very nice. I just hope it measures well when you attach a tweeter to it.![]()
If it doesn't I'll just shove some foam in there - works for Earl...
Seriously, I expect great things.
If it doesn't I'll just shove some foam in there - works for Earl...
Seriously, I expect great things.
:rimshot:

If it doesn't I'll just shove some foam in there - works for Earl...
Ha, good one
It was my impression that the foam George is using isnt the expanding kind, or very little expanding, more "tight", and tougher, made fore casting
There have been direct insructions about which kind, so maybe it is what you are using, I dont know, but it looks more like ordinary foam
It looks like your outer negative mold half is cast directly on the positive part, and "raised" a bit, to make the casting
Which causes a slightly thinner casting
Maybe you need to cast a new negative mold part that will make your waveguide cast a bit thicker, more massive, and stronger
More work, sure
It looks good tho
Or maybe I just dont understand it
Is it maybe the mold your are casting right now ?
There have been direct insructions about which kind, so maybe it is what you are using, I dont know, but it looks more like ordinary foam
It looks like your outer negative mold half is cast directly on the positive part, and "raised" a bit, to make the casting
Which causes a slightly thinner casting
Maybe you need to cast a new negative mold part that will make your waveguide cast a bit thicker, more massive, and stronger
More work, sure
It looks good tho
Or maybe I just dont understand it
Is it maybe the mold your are casting right now ?
It was my impression that the foam George is using isn't the expanding kind, or very little expanding, more "tight", and tougher, made fore casting
It looks like your outer negative mold half is cast directly on the positive part, and "raised" a bit, to make the casting
Which causes a slightly thinner casting
First off, who's George?
I first made the cardboard/bondo positive. From that I made the plaster negative. From the plaster negative I made a new plaster positive - these two parts (positive and negative make up the mold for the horn. The negative was cut and resized to provide the space between it and the positive:
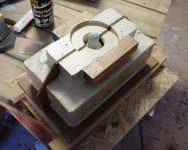
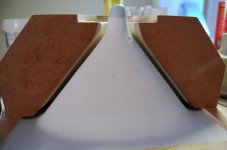
The horn casting will be polyurethane resin, not foam. Solid black plastic.
As shown I've done some work on the positive - reinforced the throat with a long screw and bondo. This should prevent it from breaking. I've also put several coats of urethane on the negative, inside and out.
Getting closer.
That looks good,
Last edited:
The horn casting will be polyurethane resin, not foam. Solid black plastic.
Ok, then your mold makes sense to me
I wasnt aware you could buy fluid 2-component plastic stuff just like that
Thats interesting, and good luck with casting the waveguide
The innovation, speed, and quality of this speaker build is the best I have seen on DIY Audio.
I appreciate all the pics.
I have a couple of questions:
1. for you horn mold, why didn't you leave the back side as a solid block?
2. It seems like the walls are fitting together perfectly. Can you say a bit more about math, measuring, and cutting that allowed you to get such a nice fit.
I appreciate all the pics.
I have a couple of questions:
1. for you horn mold, why didn't you leave the back side as a solid block?
2. It seems like the walls are fitting together perfectly. Can you say a bit more about math, measuring, and cutting that allowed you to get such a nice fit.
I wasnt aware you could buy fluid 2-component plastic stuff just like that
Thats interesting, and good luck with casting the waveguide
It is available HERE. Too late I found that they also sell expanding foam and it would have probably been cheaper for me to get it from them.
The innovation, speed, and quality of this speaker build is the best I have seen on DIY Audio.
1. for you horn mold, why didn't you leave the back side as a solid block?
2. It seems like the walls are fitting together perfectly. Can you say a bit more about math, measuring, and cutting that allowed you to get such a nice fit.
Thanks
I want to make these with as little plastic as possible. It is larger than it appears in the pics - the front mounting flange is 11" wide, 6" tall. I can't afford to use $100 worth of plastic in one horn.
I left out some of the "figuring" on the way to getting the shape I wanted. Math is not my strong suit and that is probably a good thing - you can lose yourself in numbers and never get anything done.
First I wanted the mouth to be an elliptical shape, not an oval and it would need to be a minimum size but wouldn't need to be too big - the crossover point for this being ~2k. So I decided on a width of 9 inches on the horizontal axis. This measurement does not include the radius at the mouth. On the horizontal axis, the horn was supposed to flare 90 degrees but in the end I settled for ~85 degrees (to get the 90* x 40* through trial and error I produced 5 paper cones - the last one was the best compromise). On the vertical axis the horn flares 40 degrees and the depth from front to mounting flange is 5.25 inches.
Like I said, this is done by trial and error - I cut out the ellipse based on measurements I drew in Sketchup, the paper cones were a best guess until I had one that was close enough.
I suppose there are more sophisticated and accurate ways of doing this but learning those doesn't sound like fun.
John,
I am following your progress with great interest! looking at the tech sheet for the ONYX resin that you will be using I see that it has a pot life of only 2.5 minutes. Wow that is short! I presume you plan on building up the horn doing several pours. I presume that you have worked with this system before. How deep can you pour this resin before it becomes a problem? Will you be using a filler?
I am following your progress with great interest! looking at the tech sheet for the ONYX resin that you will be using I see that it has a pot life of only 2.5 minutes. Wow that is short! I presume you plan on building up the horn doing several pours. I presume that you have worked with this system before. How deep can you pour this resin before it becomes a problem? Will you be using a filler?
Hi Carl,
I haven't used it before but I've watched some demos and it seems very straightforward.
It is my plan to cast the horn in one shot, using no fillers. The resin sets quick but is low viscosity and should flow into the mold uniformly. The thickest part of the horn is where the CD mounts - 3/8" thick, the rest of it is ~1/4" thick. I don't foresee any problems.
Time will tell and I'm eager to give it a try.
I haven't used it before but I've watched some demos and it seems very straightforward.
It is my plan to cast the horn in one shot, using no fillers. The resin sets quick but is low viscosity and should flow into the mold uniformly. The thickest part of the horn is where the CD mounts - 3/8" thick, the rest of it is ~1/4" thick. I don't foresee any problems.
Time will tell and I'm eager to give it a try.
- Status
- This old topic is closed. If you want to reopen this topic, contact a moderator using the "Report Post" button.
- Home
- Design & Build
- Construction Tips
- Casting Experiment: Elliptical Horn Flare