Now that I've had some fun with the new version of the glass lathe I thought that it was time to get back and finish up the WE 101D project that was places onto the back burner a couple of weeks ago. Today was spent putting together a grid structure. Since the plate structure was already done it pretty much defines the size that the grid needs to be. I spent far to much time in the last month thinking about how to build a fixture to help shaping, assembling and welding the ladder structure together. I finally decided to just sit down and bend the frame into shape with an assortment of hand tools. The ladder structure of the grid is relatively easy to build, but the process is tedious. If this tube works properly after it's processed I 'll commit to building fixtures for future versions.
The next part that needs attention is the filament. The original WE 101D's that I've looked at on eBay show an 'M' shaped filament. This is a simple arrangement if you're using a glass arbor to support and position the electrodes. I'm going to avoid using an arbor and just utilize the extra pins in the button pinch that the Workshop uses and run the filaments in parallel. I'm looking forward to getting one of these tubes processed and tested.
The next part that needs attention is the filament. The original WE 101D's that I've looked at on eBay show an 'M' shaped filament. This is a simple arrangement if you're using a glass arbor to support and position the electrodes. I'm going to avoid using an arbor and just utilize the extra pins in the button pinch that the Workshop uses and run the filaments in parallel. I'm looking forward to getting one of these tubes processed and tested.
Attachments
If anyone here is interested in delving into the hobby of building their own triode vacuum tubes, there's a new forum dedicated to DIY tubes. It's just getting started, but will hopefully become a good source of information for tip and techniques. Here's the link: diyvacuumtubes.com
What an amazing site Sir,
your work is artisan and your words are almost those of my father - he was Ground Radar in the R.A.F. before Aircrew in the early 70's
I now know that I should have taken more in but the whole missiles / aircraft thing got in the way
Anyway, I'll definitely be taking a longer look.
Sippy - Thank you for the positive comment about the website. The link you provided will undoubtedly be helpful in this thread. I want to say up front here that I seem to be getting credit for what is actually Trevor's forum site. He has done all the work involved in getting the site up and running. My own website detailing the attempt to get the Vacuum Tube Workshop website up and going is as far into web designs as I've ventured. For the record, Trevor was one of the early attendees of the VTW and got bitten by the DIY vacuum tube bug. I'm not sure if there's an antivenom yet.
The main issue about the VTW site is that it doesn't lend itself to interactive exchanges with interested visitors. Trevor's forum bridges the gap between me and my total lack of skills when it comes to 21st Century communication on the internet. It's all about settling into the comfort(?) of becoming an old man. When younger folks want to carry the torch, I'm more than pleased to hand it off. They say that when an old person dies a library burns down. My hope is to distribute as many volumes as I can before the conflagration!
The main issue about the VTW site is that it doesn't lend itself to interactive exchanges with interested visitors. Trevor's forum bridges the gap between me and my total lack of skills when it comes to 21st Century communication on the internet. It's all about settling into the comfort(?) of becoming an old man. When younger folks want to carry the torch, I'm more than pleased to hand it off. They say that when an old person dies a library burns down. My hope is to distribute as many volumes as I can before the conflagration!
I had a chance to do some machining over the weekend. What I have now is the first attempt to make a fixture for aligning and spot welding the grids for the the new triode. The material for the ladder is a 20 mil wire called Blendalloy which is an alloy of nickel and iron. The side posts are 40 mil nickel plated steel wire. Fortunately both wires are magnet.
I was able to machine a piece of 1/4" thick mild steel plate into a suitable shape and add a series of slots into the plate to accommodate the grid parts. A magnet on the underside of the fixture was used to keep the wires in their assigned slots. A piece of aluminum (nonmagnetic) could then be clamped down on the wires to keep them in place for welding. The aluminum was clamped down with nonmagnetic SS bolts. This arrangement, when assembled, dramatically increases the ease and speed with which the grids can be welded and then shaped to fit between the plates.
I was able to machine a piece of 1/4" thick mild steel plate into a suitable shape and add a series of slots into the plate to accommodate the grid parts. A magnet on the underside of the fixture was used to keep the wires in their assigned slots. A piece of aluminum (nonmagnetic) could then be clamped down on the wires to keep them in place for welding. The aluminum was clamped down with nonmagnetic SS bolts. This arrangement, when assembled, dramatically increases the ease and speed with which the grids can be welded and then shaped to fit between the plates.
Attachments
The new fixture works very well for making grids to install into the current triode design. The yield and reproducibility of grids have gone way up. I plan to make a fixture for the next plates and filaments. It should be a reasonable task to build tubes with very similar characteristics when everything is in place.
The photos show the ladder grids before and after spot welding the two sections together. There is some variation in the support post wire bending.
The assembled tube is made from parts that were just spot welded together without the use of any fixtures. As long as it's welded up I might as well use it to practice fusing the envelope to the stem. That process alone is going to be a real test for the next iteration of glass lathe that I've been experimenting with. Doing this on a small budget is a challenge in itself. Fortunately I have plenty of beer to see me through this project.
The photos show the ladder grids before and after spot welding the two sections together. There is some variation in the support post wire bending.
The assembled tube is made from parts that were just spot welded together without the use of any fixtures. As long as it's welded up I might as well use it to practice fusing the envelope to the stem. That process alone is going to be a real test for the next iteration of glass lathe that I've been experimenting with. Doing this on a small budget is a challenge in itself. Fortunately I have plenty of beer to see me through this project.
Attachments
Be nice if one of these independent tube builders could duplicate the Telefunken AC701 tube which is used in condenser mics....A very special tube...low self grid current (like 300 pA), high grid resistance (>150 meg ohms), extremely low noise, indirectly heated cathode...extremely low microphonics...
The new fixture works very well for making grids to install into the current triode design. The yield and reproducibility of grids have gone way up. I plan to make a fixture for the next plates and filaments. It should be a reasonable task to build tubes with very similar characteristics when everything is in place.
The photos show the ladder grids before and after spot welding the two sections together. There is some variation in the support post wire bending.
The assembled tube is made from parts that were just spot welded together without the use of any fixtures. As long as it's welded up I might as well use it to practice fusing the envelope to the stem. That process alone is going to be a real test for the next iteration of glass lathe that I've been experimenting with. Doing this on a small budget is a challenge in itself. Fortunately I have plenty of beer to see me through this project.
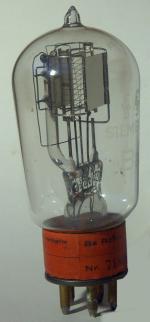
hpeter - The tubes that I'm putting together right now are following a generic design geometry that was common in the 20's and early 30's. The other most common geometry was the cylindrical electrode type. I've built both types and find the parallel electrodes much easier to make and align. This makes it much easier to make tubes with consistent and predictable characteristics.
I've chosen to use the WE 101D as a designated model because anyone following this thread can easily find representative examples of that tube on eBay. There are some good photos that people have put up to show what they're selling. My tubes are just a variant of these classic designs.
I've chosen to use the WE 101D as a designated model because anyone following this thread can easily find representative examples of that tube on eBay. There are some good photos that people have put up to show what they're selling. My tubes are just a variant of these classic designs.
Now that I've gotten a lot of crazy tube designs out of the way, I'm pleased that I was finally able to settle on the planar element design and ladder grids. It wasn't worth making fixtures to help in the assembly of 1-off tubes because of the time and effort needed for designing and building fixtures. Having one basic geometry that can be tweaked in small increments will make it fairly straight forward to develop and built reliable and reproducible triodes.
I've been reading up on the early WE 101D type tubes and it has been reported that the direct-heated thoriated tungsten filaments and ladder grids have some intrinsically desirable traits. The reported downside is their tendency to propagate hum through the system. Others report that the hum can be eliminated with good, clean, power supplies. Do any of you folks have experience with the use of these old planar style DHT tubes?
I've been reading up on the early WE 101D type tubes and it has been reported that the direct-heated thoriated tungsten filaments and ladder grids have some intrinsically desirable traits. The reported downside is their tendency to propagate hum through the system. Others report that the hum can be eliminated with good, clean, power supplies. Do any of you folks have experience with the use of these old planar style DHT tubes?
Having decide to use the WE 101D as a starting point for building a basic tube I thought it might be interesting to make a tennis ball envelope as a practice exercise on the glass lathe. I'm getting the hang of the new lathe design and its skill set requirement. This first specimen took about 5 minutes to make. I use the small bunsen burner mounted behind the lathe to do the preheating and then to anneal the glass when I'm finished.
It was an enjoyable task to make the spherical bulb, but for the time being I'm going to stick with using the straight walled envelopes for the tubes. The tennis ball bulbs look cool, but they won't fit into the oven that I'm currently using and I don't need to start another bakeout oven project right now.
Also, I've pieced together a polariscope by using a liquid crystal display and a polarizing filter to evaluate the level of strains left in the glass once it cools down. I'll post some pictures of that project soon. Viewing the strains in these glass parts is as revealing as being able to use x-rays to see inside opaque objects.
It was an enjoyable task to make the spherical bulb, but for the time being I'm going to stick with using the straight walled envelopes for the tubes. The tennis ball bulbs look cool, but they won't fit into the oven that I'm currently using and I don't need to start another bakeout oven project right now.
Also, I've pieced together a polariscope by using a liquid crystal display and a polarizing filter to evaluate the level of strains left in the glass once it cools down. I'll post some pictures of that project soon. Viewing the strains in these glass parts is as revealing as being able to use x-rays to see inside opaque objects.
Attachments
The button presses that the tubes are built with have a diameter smaller than the bulb ID. This wouldn't be an issue for someone with a lot of experience working with glass, but I decided to use a graphite tool to help with closing the diameter to fit the button. This will minimize the amount of torch work that I'll need to do. When the glass is at working temperature it will naturally close down onto the graphite. I know that it's a sissy way to do the seal, but I have no issues with using training wheels.
Attachments
Now that I've decided to focus on planar element designs I'm making fixtures to keep the parts reproducible. This is how the plates are made. It's a simple device and easy to make compared to the grid fixture, though the grid device is fairly easy to make once I figured out how I wanted the parts to go together. All of the anode parts are made from nickel plated steel. Here are some photos of the arrangement.
Attachments
- Status
- This old topic is closed. If you want to reopen this topic, contact a moderator using the "Report Post" button.
- Home
- Amplifiers
- Tubes / Valves
- Build Your Own Vacuum Tubes