the world has suddenly become a better place
hollowboy, thank you for accepting my apology. I reckon between us we have both made the world a slightly better place than what it was a week ago, and I am grateful for that.
The operation on Monday was a success. Today we are resting up before the next stage of the treatment, and my depression is finally beginning to lift. We are lucky to live surrounded by love and support. What gets to me is caring for someone who is suffering, often in agony, while at the same time feeling that my own empathy is never quite enough to be truly effective - no matter how hard I try. Such is the lot of the carer. It is something I have learnt to accept.
I would also like to thank tsmith1315, what you wrote was very comforting. I kept on reading your words with a sense of the miraculous. Yes, our suffering can be infinite, but so is our sense of compassion, and your words prove that. Good luck, the world needs you.
Don't worry about it, the ad-hominem stuff was mostly just odd (rather than offensive).
I hope the operation goes well.
Where I am, hospitals can hook you up with stuff like social workers, home nurse visits (to assist with things like changing dressings), free equipment and counseling. Also: many of the consultants will happily write letters that help to cut red tape, such as supporting applications for benefits, requesting early access to superannuation funds, stuff like that.
If you make your needs (and stress / fatigue) known, there may be similar resources you can tap into.
hollowboy, thank you for accepting my apology. I reckon between us we have both made the world a slightly better place than what it was a week ago, and I am grateful for that.
The operation on Monday was a success. Today we are resting up before the next stage of the treatment, and my depression is finally beginning to lift. We are lucky to live surrounded by love and support. What gets to me is caring for someone who is suffering, often in agony, while at the same time feeling that my own empathy is never quite enough to be truly effective - no matter how hard I try. Such is the lot of the carer. It is something I have learnt to accept.
I would also like to thank tsmith1315, what you wrote was very comforting. I kept on reading your words with a sense of the miraculous. Yes, our suffering can be infinite, but so is our sense of compassion, and your words prove that. Good luck, the world needs you.
That's how this chap does it:
The Grand Monument Reference features heavy lead lining to all exterior surfaces. The same heavy bracing is used, but all areas between the bracing are covered by a unique sandwich lining. Heavy acoustic felt is used to separate the heavy lead sheet from the cabinetry. A further layer of heavy acoustic felt is placed over the lead and the entire sandwich is stapled to the walls of the cabinet. This result is what is effectively a box within a box. Wrapping the outside of the speaker is similar to knocking on a brick. This totally inert cabinet construction results in the ultimate sound reproduction.
Monument | Osborn Loudspakers | World's Best
Not quite sure why this comes to mind, but sometimes at night I see our local tawny owl hunting for mice and voles by moonlight while hovering a few feet above the ground on wings completely silent. In the morning the grass beneath is knocked flat by vortices from the downbeats of displaced air. So beautifully efficient.
I am convinced that lead and felt is also very effective for absorbing vibration, but I do wonder about other ways of doing the same - albeit with a lot less weight.
Last edited:
I'm thinking in terms of "small" horns, like Art's Keystone, or Danley's TH112.
Take the latter. Very intriguing to me, but still about 145 lbs. I assume he's using a Neo magnet 12, so the cabinet itself must weigh at LEAST 130 lbs.
<RANT>
NO, Danley is NOT using a neo 12" woofer, and I can't figure out for the life of me why the hell not. A friend of mine built some clones of the TH-Mini using Eminence Kappalite 3012LF drivers, and I could lift one over my head using just one hand. With so many people complaining about the size and weight of PA speakers, it's like Danley just decided they don't want to sell that many subwoofers. Or something. I mean, the benefits and marketability of a TH-Lite should be obvious to them. It's ridiculous, but if you want a TH-Mini that you can lift, you'll need to build it yourself.
</RANT>
For something lighter than plywood, you're probably looking at a plastic foam of some type. I wonder if there is a hard PVC foam board product out there that would work. I know there's polystyrene foam, but it's not rigid enough.
Last edited:
For something lighter than plywood, you're probably looking at a plastic foam of some type. I wonder if there is a hard PVC foam board product out there that would work.
Art described exactly that in post 54.
Foam core such as the brand named "Divinycell" cross-linked PVC foam core is typical of boat construction and available at boat supply companies
I know there's polystyrene foam, but it's not rigid enough.
I dunno if I'd rule it out - this chap does finds it to be rigid enough for kayaks. Very light. Downsides seem to be bulk (thick walls = wasted volume) and effort - his project looks like a lot more work than a simple ply box. He has a few different instructables, such as:
Sawfish, an Unsinkable, Lightweight, Foam Kayak (23 Lbs). Free DIY Kayak Plans, the Hardware Store Boat: 32 Steps (with Pictures)
I think the step where he scores the foam with a spiky tool is very clever - "I prefer to think of the holes as becoming thousands of tiny nails that pin the glued joints together."
I think another decent option is sandwich construction that uses an aluminium honeycomb or plastic lattice as the 'filling' of the sandwich. A benefit of using this sort of core (open cells) rather than a rigid foam would be that, if you perforate the inner skin, the wall thickness would not be wasted volume. Some ideas are in this thread:
Alu honeycomb panel
I have also come to the conclusion that rigidity is much over-rated and some cabinet flex isn't terrible.
I agree, but it matters a lot what the flex contributes to sound. Panels made of stiff and dense materials tend to have higher resonance frequencies than flex... flexier... more flexible and/or less dense materials.
Also, a lot of flex adds extra vibrations even when not in resonance, a loudspeaker enclosure is a very large radiator compared to the drive unit, hornmouth or port. When making a design for birch ply out of something else, the end result may sound very different.
I had fine experience with pretty lossy sealed boxes (thin ply with soft 9mm fiberboard lining) and a backloaded horn made entirely of soft 18mm fiberboard. Only for subwoofer duties. The basic non-resonant panel vibrations simply merged with the driver sound and there weren't obvious/loud resonances in the pass band. Cross over higher (particularly the drive unit in the backloaded horn was usable to well above 1.5kHz) and it sounded off.
I also built some fulrange open baffles with the fiberboard. While it was not horrible (certainly no obvious/loud resonances), the massive panel vibrations at midrange frequencies made it sound muddled and heavy.
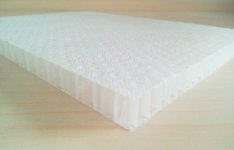
If you have access to a vacuum bag and vacuum pump. Or even a good vacuum cleaner and a valve to hold the vacuum you can take wood backed veneer on polypropylene honeycomb. There is 3M brand that has a fleece backing bonded to the skins and easily makes up a stiff panel. I consulted on a few lightweight designs and this stuff really works well. You have to add in rings of plywood where you mount drivers or solid edges where you want to join panels. But otherwise it is a very strong very lightweight method of making enclosures.
Just not cheap!
CladTuff(R) HC – Honeycomb Core Products | Fiber-Tech Industries
Plastic Honeycomb – Sheets | Carbon-Core Corporation
- Status
- This old topic is closed. If you want to reopen this topic, contact a moderator using the "Report Post" button.
- Home
- Loudspeakers
- Subwoofers
- Better ($$) alternative to plywood?