Ted205: From the onsemi datasheet: "This capacitor (CAdj) prevents ripple from being amplified as the output voltage is increased. A 10uF capacitor should improve ripple rejection about 15 dB at 120 Hz in a 10 V application."
They used 22uF in their final schematic, but I don't think the value is particularly important. I didn't think using 100uF there would improve things any appreciable amount, maybe?
Even though the star ground makes perfect sense, it's not sinking in fast enough because of all I thought I knew about grounding. Every commercial power amp I own has all grounds returning to the center point between the filter caps. Thanks for your help, and patience. Hopefully I have the right idea now:
So, the gnd connection from the preamp board and the chassis gnd wire will also connect to the star gnd point, right? The input rca gnd connections should also return to this point, correct? Connect them all together on the back panel, isolated from chassis, and then one wire connects to the star gnd on the PS board?
They used 22uF in their final schematic, but I don't think the value is particularly important. I didn't think using 100uF there would improve things any appreciable amount, maybe?
Even though the star ground makes perfect sense, it's not sinking in fast enough because of all I thought I knew about grounding. Every commercial power amp I own has all grounds returning to the center point between the filter caps. Thanks for your help, and patience. Hopefully I have the right idea now:
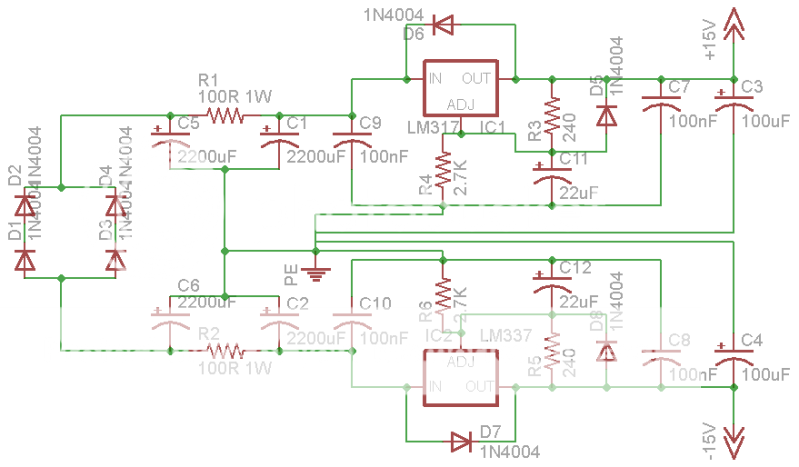
So, the gnd connection from the preamp board and the chassis gnd wire will also connect to the star gnd point, right? The input rca gnd connections should also return to this point, correct? Connect them all together on the back panel, isolated from chassis, and then one wire connects to the star gnd on the PS board?
AndrewT will remember this.
Have a read here, look at diagram post #45. Although this was all related to a power amp the theory is sound and it all applies,
http://www.diyaudio.com/forums/solid-state/101321-3-stage-lin-topology-nfb-tappings-3.html
Have a read here, look at diagram post #45. Although this was all related to a power amp the theory is sound and it all applies,
http://www.diyaudio.com/forums/solid-state/101321-3-stage-lin-topology-nfb-tappings-3.html
Ted205: From the onsemi datasheet: "This capacitor (CAdj) prevents ripple from being amplified as the output voltage is increased. A 10uF capacitor should improve ripple rejection about 15 dB at 120 Hz in a 10 V application."
They used 22uF in their final schematic, but I don't think the value is particularly important. I didn't think using 100uF there would improve things any appreciable amount, maybe?
Even though the star ground makes perfect sense, it's not sinking in fast enough because of all I thought I knew about grounding. Every commercial power amp I own has all grounds returning to the center point between the filter caps. Thanks for your help, and patience. Hopefully I have the right idea now:
![]()
So, the gnd connection from the preamp board and the chassis gnd wire will also connect to the star gnd point, right? The input rca gnd connections should also return to this point, correct? Connect them all together on the back panel, isolated from chassis, and then one wire connects to the star gnd on the PS board?
A while back I did a lot of reading and measuring of a lt1033 and lt1085 based dual supply. The testing I did was transient load as well as output impedance. Here is what I remember.
1. If you are using point to point (which i think you plan to?) I agree with the use of a star ground. If you are using a circuit board I recommend a ground plane. With a star ground, use heavy gauge wire between the ground of the main filter caps and the output caps. Resistance here degrades regulation.
2. Place the filter caps as close as possible to each other. Choosing really nice low esr caps is a waste if the traces/wires connecting them have appreciable resistance.
3. The adjust pin bypass cap had no effect on transient response above 10uF.
4. The adjust pin ground should be run to the point of greatest load for lowest output impedance. Using a 10 ohm resistor, also connect the adjust pin ground to the star ground on board. This will protect against fault.
5. For lowest output impedance, use between 700 and 1000uF for output caps.
6. Use heavy gauge wire to connect the supply output to the load. I have seen power supplies where significant effort has been put into maintaining low output impedance and it is ruined by using a thin wire that runs to a distant load (running the adjust pin ground to load only partially compensates for this, it is not a true external sense)
If you decide to use two pairs of filter caps consider putting a 1 ohm 3 watt resistor in series for filtering.
If you want better regulation, use an external precision voltage reference (see lt1033 data sheet)
If you want improved noise rejection use a tracking preregulator.
Finally, I also recall reading that noise can get across the input/output protection diode. I've seen a 1n4148 with a series 24R as the recommended alternative.
1. I'll be making a PCB, but probably single sided.
2. Good point.
3. Good to know the 22uF Cadj is fine. I have more 22uf than 10uF around so I'll leave it alone.
4. Interesting, the LM317 data/application sheet mentions this, remote ground sensing.
5. I was wondering about this, and how much of an improvement more (470uF-1000uF) capacitance would make there. It would seem unnecessary with such a small load (a few opamps...) But, 1000uF/25V to 35V caps are small...
6. 16ga?
Are you talking about the output filter caps? The main filter caps already have a 100R in series between them.
Replacing the 1N4002 with 1N4148/27R is easy enough. Makes sense.
2. Good point.
3. Good to know the 22uF Cadj is fine. I have more 22uf than 10uF around so I'll leave it alone.
4. Interesting, the LM317 data/application sheet mentions this, remote ground sensing.
5. I was wondering about this, and how much of an improvement more (470uF-1000uF) capacitance would make there. It would seem unnecessary with such a small load (a few opamps...) But, 1000uF/25V to 35V caps are small...
6. 16ga?
Are you talking about the output filter caps? The main filter caps already have a 100R in series between them.
Replacing the 1N4002 with 1N4148/27R is easy enough. Makes sense.
Last edited:
6. Use heavy gauge wire to connect the supply output to the load. I have seen power supplies where significant effort has been put into maintaining low output impedance and it is ruined by using a thin wire that runs to a distant load (running the adjust pin ground to load only partially compensates for this, it is not a true external sense)
wire resistance has almost nothing to do with this.6. 16ga?
Inductance in the flow and return leads is the main problem and it gets much worse with increasing length and increasing gap between the wires.
Keep the wires short and very close together.
wire resistance has almost nothing to do with this.
Inductance in the flow and return leads is the main problem and it gets much worse with increasing length and increasing gap between the wires.
Keep the wires short and very close together.
Andrew is correct, I misspoke when I said resistance and I should have said inductance. Andrew is also correct in pointing out that length more than trace width or wire gauge effects inductance,however, when we are worried about 0.001R you might find that maximizing either can help once you've made things as short as possible.
Stormrider said:Are you talking about the output filter caps? The main filter caps already have a 100R in series between them.
Another error on my part.
It's been awhile; I'm hoping to get back into this project. Once I get back to work I can start buying parts and the equipment I still need to make the PCB's.
Instead of Rod Elliot's balanced driver circuit I'm going to use DRV134's from TI. They offer better performance than anything I could create with standard opamps, but are still cheaper to implement than transformers.
The preamp circuit itself is still the same one I've been messing with throughout this thread. The DRV134 circuit is pulled directly from the datasheet.
This is the final version:
Here is where I'm at with the board design. It's staying single sided for ease of construction. The jumpers are just for the power rails. I can still improve this somewhat, but this will be the basic idea.
Instead of Rod Elliot's balanced driver circuit I'm going to use DRV134's from TI. They offer better performance than anything I could create with standard opamps, but are still cheaper to implement than transformers.
The preamp circuit itself is still the same one I've been messing with throughout this thread. The DRV134 circuit is pulled directly from the datasheet.
This is the final version:
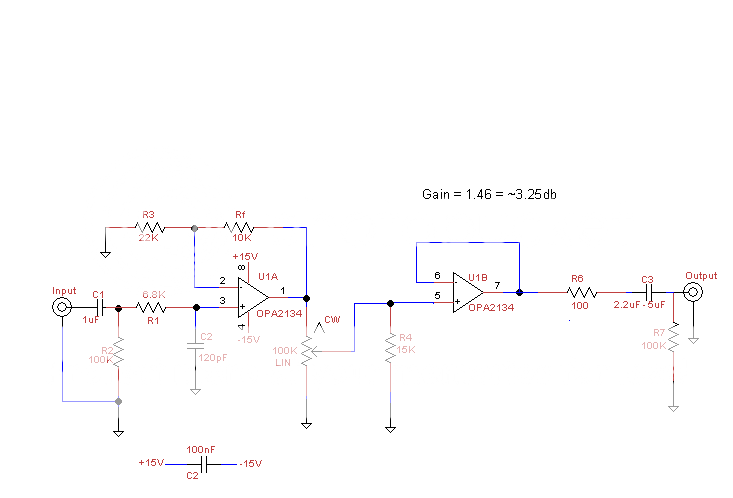
Here is where I'm at with the board design. It's staying single sided for ease of construction. The jumpers are just for the power rails. I can still improve this somewhat, but this will be the basic idea.
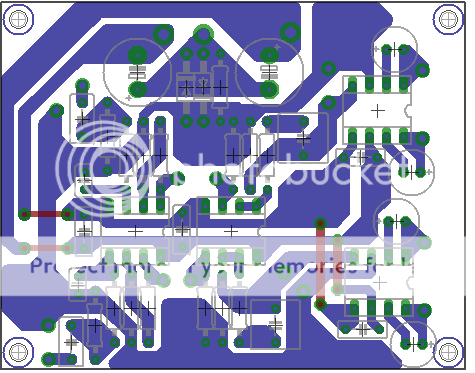
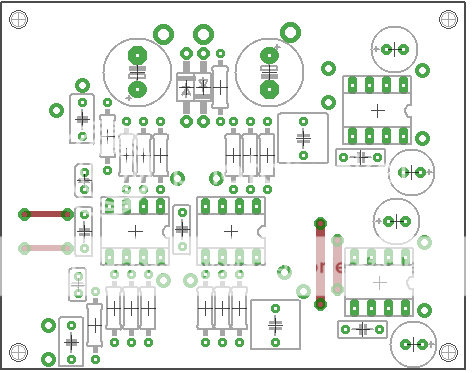
Glad to hear you're getting back into it.
You could have the other side be mostly a ground plane with not much more effort at all. It could GREATLY aid your layout, and might also significantly improve performance, especially since you're not using star grounding.
By the way, it would help (me) if your schematic matched your description and your boards. And it would help if your boards were properly labeled.
Not knowing your board-size constraints, would it be possible to pull the power and ground connections from the top to the left side, and to make everything more symmetrical top vs bottom? I would guess that equal length and identically-shaped power traces and ground returns (and everything else) for the two channels would be best, if possible.
But if you do, instead, keep the layout basically the same, I would at least try to keep the V+ and V- traces the same size as each other, everywhere. (Or maybe you're compensating for their different lengths?) And why not narrow the gap between them, everywhere, as you have in some places? Added trace-to-trace capacitance (and smaller enclosed loop area) between them couldn't hurt.
You could have the other side be mostly a ground plane with not much more effort at all. It could GREATLY aid your layout, and might also significantly improve performance, especially since you're not using star grounding.
By the way, it would help (me) if your schematic matched your description and your boards. And it would help if your boards were properly labeled.
Not knowing your board-size constraints, would it be possible to pull the power and ground connections from the top to the left side, and to make everything more symmetrical top vs bottom? I would guess that equal length and identically-shaped power traces and ground returns (and everything else) for the two channels would be best, if possible.
But if you do, instead, keep the layout basically the same, I would at least try to keep the V+ and V- traces the same size as each other, everywhere. (Or maybe you're compensating for their different lengths?) And why not narrow the gap between them, everywhere, as you have in some places? Added trace-to-trace capacitance (and smaller enclosed loop area) between them couldn't hurt.
Last edited:
Right, now that I've gotten more into power amp design I see 200Khz is limited for a preamp these days, even though any higher really seems pretty unnecessary to me.
I recalculated the RF filter, reduced C to 50pF for ~500KHz bandwidth. The input cap will be 2.2uF. That's 1.4Hz with the 100K resistor. The output cap will be 5uF, that's .31Hz with the 100K.
Sorry for posting that old schematic. This is the one I'm working from in Eagle. It shows everything except the Vol. pot, which is off board, and the power supply.
As far as the board goes I'm going to start over. Too many things I didn't like. For one, I don't think I need the two 100uF filter caps on board, so I'm dropping them to 22uF. The power supply board is going to be pretty close anyway, inside the 1U case.
I really wanted to make the boards myself, but I may just plunk down the money to have some professional ones made. I found one company that charges 72$ for four two layer boards under 6.3"x4". I figure I'll probably keep two and sell two if anyone wants them.
Here it is: PCB Prototypes
Is there anything else I really should change before having another go at the board design?
I recalculated the RF filter, reduced C to 50pF for ~500KHz bandwidth. The input cap will be 2.2uF. That's 1.4Hz with the 100K resistor. The output cap will be 5uF, that's .31Hz with the 100K.
Sorry for posting that old schematic. This is the one I'm working from in Eagle. It shows everything except the Vol. pot, which is off board, and the power supply.
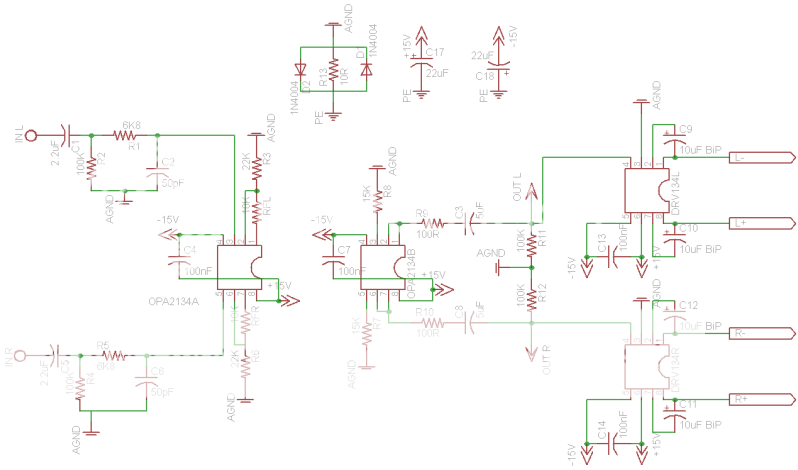
As far as the board goes I'm going to start over. Too many things I didn't like. For one, I don't think I need the two 100uF filter caps on board, so I'm dropping them to 22uF. The power supply board is going to be pretty close anyway, inside the 1U case.
I really wanted to make the boards myself, but I may just plunk down the money to have some professional ones made. I found one company that charges 72$ for four two layer boards under 6.3"x4". I figure I'll probably keep two and sell two if anyone wants them.
Here it is: PCB Prototypes
Is there anything else I really should change before having another go at the board design?
Last edited:
two 50 Ohm esistors are making sure the output current divides equally between the 2 op amps - a way of doubling the output current
I'd use a genuinely high output current op amp in a multiloop composite
CFA op amps designed for A/DSL line driving make excellent outputs for audio line levels
I'd use a genuinely high output current op amp in a multiloop composite
CFA op amps designed for A/DSL line driving make excellent outputs for audio line levels
Hi Stormrider,
Yes, it's kind of a "poor man's" buffer. I needed a little more current drive capability for the three active filter inputs than a single LM4562 could deliver and didn't want to mess with a separate buffer chip or discretes, plus there are already two Opamps right there in the chip ready to use. The 49.9 ohm resistors are there to equalize the output currents from each chip so they won't "see" each other's outputs, and because they're both in the feedback loop, only penalty is slightly reduced output voltage. It works really well, sounds good.
Mike
Yes, it's kind of a "poor man's" buffer. I needed a little more current drive capability for the three active filter inputs than a single LM4562 could deliver and didn't want to mess with a separate buffer chip or discretes, plus there are already two Opamps right there in the chip ready to use. The 49.9 ohm resistors are there to equalize the output currents from each chip so they won't "see" each other's outputs, and because they're both in the feedback loop, only penalty is slightly reduced output voltage. It works really well, sounds good.
Mike
Cool. Like I said I've never seen anything like that, but then I've only been at it for a few years now.
The DRV134 has more than enough drive capability for what I need, so I'm good with the circuit I'm working with now. They are kind of expensive though, ~5$ea at mouser, but not bad compared to signal transformers.
The DRV134 has more than enough drive capability for what I need, so I'm good with the circuit I'm working with now. They are kind of expensive though, ~5$ea at mouser, but not bad compared to signal transformers.
- Status
- This old topic is closed. If you want to reopen this topic, contact a moderator using the "Report Post" button.
- Home
- Amplifiers
- Chip Amps
- Basic opamp based preamp