I use rubber (chlorprene rubber) cement for most of my builds and for all my lamination. For some joints I use hot glue. I also seal all my inside seams with a bead of hot glue just to make sure the boxes are air tight. I might switch to a silicone calk for seals, but for now the hot glue works good for this.
Rubber cement makes excellent bonded joins with EVA foam and for lamination it adds a rubber damping layer to help with sound absorption and damping.
And yes I also use rubber cement for most of my edge joins. When I have an edge that is being curved/bent and is under pressure, for those I will use hot melt since it sets much faster. But in general I prefer a slow setting style of glues. I personally don't like spray glues (needs ventilation, masks, upsets my allergies, nasty volatiles).
I don't use any mechanical fasteners for joins. Just for mounting drivers and for my removable baffles.
I use this rubber glue which is super strong and used for repairing shoes and other professional applications. I live in Japan so it is a Japanese brand, but I am certain you can find a local equivalent. I am not talking about the rubber cement kids use for crafts (Elmers with the brush). This G17 comes with adapters to lay lines/beads of glue or to lay it down in thin wide layers.
SELECT TOOL SHOP | Rakuten Global Market: Konishi bond G17 50 ml
sometimes I use their G10 formula. Seems to be stronger, slower cure times.
http://global.rakuten.com/en/store/select-tool/item/bond-018/
I just noticed on this page that it is not recommended for styrofoam, so it might not work well for foam-core. But it works perfectly for EVA foam.
Rubber cement makes excellent bonded joins with EVA foam and for lamination it adds a rubber damping layer to help with sound absorption and damping.
And yes I also use rubber cement for most of my edge joins. When I have an edge that is being curved/bent and is under pressure, for those I will use hot melt since it sets much faster. But in general I prefer a slow setting style of glues. I personally don't like spray glues (needs ventilation, masks, upsets my allergies, nasty volatiles).
I don't use any mechanical fasteners for joins. Just for mounting drivers and for my removable baffles.
I use this rubber glue which is super strong and used for repairing shoes and other professional applications. I live in Japan so it is a Japanese brand, but I am certain you can find a local equivalent. I am not talking about the rubber cement kids use for crafts (Elmers with the brush). This G17 comes with adapters to lay lines/beads of glue or to lay it down in thin wide layers.
SELECT TOOL SHOP | Rakuten Global Market: Konishi bond G17 50 ml

sometimes I use their G10 formula. Seems to be stronger, slower cure times.
http://global.rakuten.com/en/store/select-tool/item/bond-018/
I just noticed on this page that it is not recommended for styrofoam, so it might not work well for foam-core. But it works perfectly for EVA foam.
Last edited:
yeah that E6000 looks very similar. they don't say what it is made of, but the properties and cure times are similar,
they also say this :
Note: E6000 is not recommended for use on Styrofoam[emoji769], polystyrene, polyethylene or polypropylene plastics.
but G17 and G10 works great with EVA. I think this warning is because the solvent in this glue cause the foam to slightly melt, but it actually makes the bond stronger. But it is not the prettiest glue edge, especially with the white foam since the yellow of the glue shows. But I don't mind
they also say this :
Note: E6000 is not recommended for use on Styrofoam[emoji769], polystyrene, polyethylene or polypropylene plastics.
but G17 and G10 works great with EVA. I think this warning is because the solvent in this glue cause the foam to slightly melt, but it actually makes the bond stronger. But it is not the prettiest glue edge, especially with the white foam since the yellow of the glue shows. But I don't mind
Last edited:
Be careful when using silicone calk to seal enclosures, especially if it contains acetyl (the ones that smell like vinegar).
You have to make sure it is completely dried up before sealing it up with drivers, as the acetyl will corrode and rust any metal in there.
I was a bit in a hurry to hear a box I had just sealed and put some cheap drivers while it was still a little smelly. The drivers' magnets corroded and rusted so fast.
You have to make sure it is completely dried up before sealing it up with drivers, as the acetyl will corrode and rust any metal in there.
I was a bit in a hurry to hear a box I had just sealed and put some cheap drivers while it was still a little smelly. The drivers' magnets corroded and rusted so fast.
Duco is different. It's an old fashioned cement like Ambroid or Sigment: basically celluloid dissolved in acetone (or other solvent).
I'd think Barges cement would be the equivalent to that Konishi stuff. It's also used to repair shoes. I don't know E6000 but I'd guess it's vaguely similar but a more modern formulation of some sort of rubbery plastic polymer in solvent.
Always test this sort of thing beforehand. Hard to say what's in any commercial product. I kind of hate proprietary formulas, but such is modern life.
I'd think Barges cement would be the equivalent to that Konishi stuff. It's also used to repair shoes. I don't know E6000 but I'd guess it's vaguely similar but a more modern formulation of some sort of rubbery plastic polymer in solvent.
Always test this sort of thing beforehand. Hard to say what's in any commercial product. I kind of hate proprietary formulas, but such is modern life.
greg, you are right the Konishi glue is the same as Barge original contact cement. Thanks!
Barge original is a Neoprene rubber with solvent glue
Barge Products - Barge Cement
The konishi G17 lists the ingredients as simply: Organic solvent (70%), Chloroprene rubber (30%)
Chloroprene rubber is the same as Neoprene and is a synthetic rubber
https://en.wikipedia.org/wiki/Chloroprene
Barge original is a Neoprene rubber with solvent glue
Barge Products - Barge Cement
The konishi G17 lists the ingredients as simply: Organic solvent (70%), Chloroprene rubber (30%)
Chloroprene rubber is the same as Neoprene and is a synthetic rubber
https://en.wikipedia.org/wiki/Chloroprene
Last edited:
Here is the chart for materials you can use with the different Barge contact cement formulas.
The original contact cement formula (neoprene base like the konishi G17) is OK for EVA, but not PVC, vinyl or polyurethane. I really don't know if it would work for foam-core or XPS foam.
I will call this G17 "neoprene based contact cement" from now on. It is not really rubber cement.
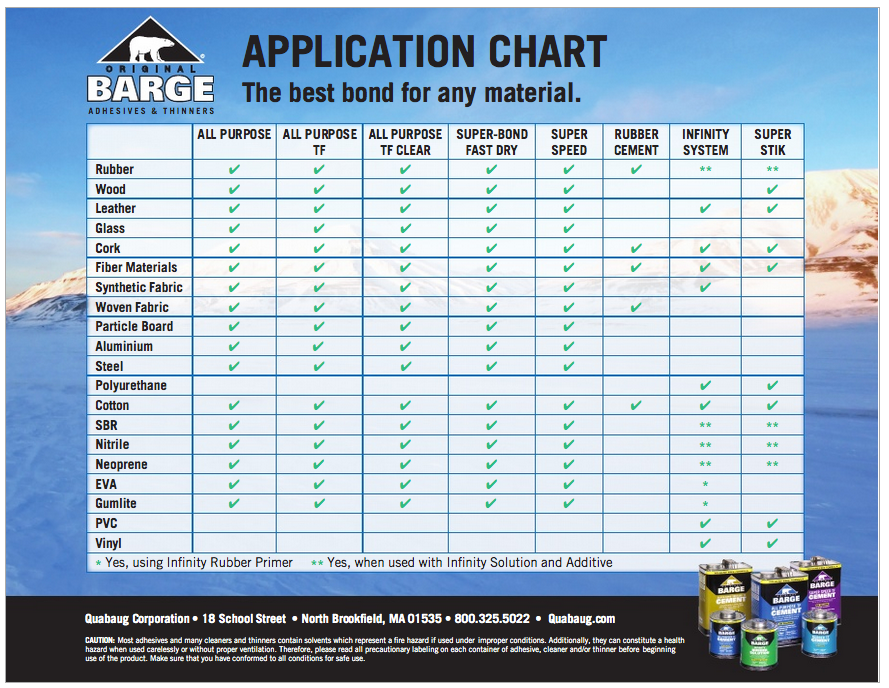
The original contact cement formula (neoprene base like the konishi G17) is OK for EVA, but not PVC, vinyl or polyurethane. I really don't know if it would work for foam-core or XPS foam.
I will call this G17 "neoprene based contact cement" from now on. It is not really rubber cement.
Attachments
Last edited:
I have started a new thread and asked the moderators to move the current 3way discussion (from post #288) over there.
http://www.diyaudio.com/forums/mult...mpact-3way-nearfield-monitor.html#post4481603
Please lets wait until the threads are split before continuing the discussion.
http://www.diyaudio.com/forums/mult...mpact-3way-nearfield-monitor.html#post4481603
Please lets wait until the threads are split before continuing the discussion.
I have started a new thread and asked the moderators to move the current 3way discussion (from post #288) over there.
http://www.diyaudio.com/forums/mult...mpact-3way-nearfield-monitor.html#post4481603
Please lets wait until the threads are split before continuing the discussion.

All posts moved over.
Is there much to be gained by laminating two layers of EVA together, rather than just buying a sheet twice as thick in the first place?
at this point I am not 100% certain there is much difference between laminating and just using a thicker piece of EVA.. But in theory the lamination will add another material (I use a rubbery contact cement) which might absorb sound and vibrations at different frequencies. But on the other side, I don't see any detriment to using lamination.
But for me it is more of a practical thing since the 10mm thick EVA is cheaper and easier for me to get and it allows me to laminate up to 20mm and 30mm very easily. In general I use 20mm (2x laminate) for structural walls and 30mm (3x laminate) for front baffles, but sometimes 20mm front baffles are fine. I have used 10mm for wings on open-baffles which works fine. Also for very small speakers (2-3" drivers) 10mm seems ok.
I can only find 20mm and 30mm thick EVA in much smaller "block" style pieces which are too small for my projects.
Thank you for suggestion. I tried making a 402mm x 522mm x 200mm speaker from 40mm EVA foam. It's a two-way speaker with 8'' woofer and 1'' tweeter.
I kept a layer of plywood for the front baffle to get a clean look. So, the front baffle is 18mm plywood + 20mm EVA foam. All other walls are 40mm EVA foam. The EVA foam density is 100kg/m3. I sourced EVA foam in form of judo-mats.
I previously built these speakers from a sandwich of 18mm plywood + 3mm rubber + 18mm plywood. The speaker walls were almost inert when touching but I didn't like the sound and spectrogram was awful.
Speaker made of EVA foam sound much better.
Here are spectrograms of original speaker made of 39mm plywood-rubber sandwich and 40mm EVA foam:
I gave up making plywood cabinets sound clean. Thought about making them from MDF, but learned about EVA foam here on forum and gave it a try. The difference in one word is WOW.
Here is a spectrogram of speaker cabinets made from 40mm EVA-foam:
Please ignore everything below 70Hz. There is a high-pass filter at 70Hz in both cases, but the sub was working during plywood measurements. The spectrogram of the EVA speaker is much cleaner looking and so it sounds.
I really like the result and thank you for pointing me to this direction.
The difference in sound is most noticeable in vocals. With EVA foam they are much more clean and natural. I made a quick video showing how do the speakers sound:
YouTube
I kept a layer of plywood for the front baffle to get a clean look. So, the front baffle is 18mm plywood + 20mm EVA foam. All other walls are 40mm EVA foam. The EVA foam density is 100kg/m3. I sourced EVA foam in form of judo-mats.
I previously built these speakers from a sandwich of 18mm plywood + 3mm rubber + 18mm plywood. The speaker walls were almost inert when touching but I didn't like the sound and spectrogram was awful.
Speaker made of EVA foam sound much better.
Here are spectrograms of original speaker made of 39mm plywood-rubber sandwich and 40mm EVA foam:
I gave up making plywood cabinets sound clean. Thought about making them from MDF, but learned about EVA foam here on forum and gave it a try. The difference in one word is WOW.
Here is a spectrogram of speaker cabinets made from 40mm EVA-foam:
Please ignore everything below 70Hz. There is a high-pass filter at 70Hz in both cases, but the sub was working during plywood measurements. The spectrogram of the EVA speaker is much cleaner looking and so it sounds.
I really like the result and thank you for pointing me to this direction.
The difference in sound is most noticeable in vocals. With EVA foam they are much more clean and natural. I made a quick video showing how do the speakers sound:
YouTube
Chebum,
Thanks for sharing the result. Very nice. I and many others have noticed a huge improvement in sound quality when using foam core Karlsonator vs wood. It must have something to do with how foam absorbs the radiation decay to give a cleaner sound. Less boxy sounding.
I wish Jeshi was still active on DIYA - she would have gotten a kick out of this news. Any photos?
Thanks for sharing the result. Very nice. I and many others have noticed a huge improvement in sound quality when using foam core Karlsonator vs wood. It must have something to do with how foam absorbs the radiation decay to give a cleaner sound. Less boxy sounding.
I wish Jeshi was still active on DIYA - she would have gotten a kick out of this news. Any photos?
Any photos?
There is not much to brag about at the moment. I didn't make any finishing at all.
This photo shows speaker construction. EVA foam is glued to a plywood. There is another layer of EVA foam on the inside on the plywood wall.
An externally hosted image should be here but it was not working when we last tested it.
I had some difficulties cutting the foam. It's too thick and stiff to be cut with a knife. A seesaw gave quite unpleasant side which I hope to cover when finishing the speaker.
I though about veneering the plywood and covering the foam into a cloth. Probably, it will be a combination of olive-sourced veneer and lightly violet cloth.
thanks to XRK for sending me an email and letting me know about this.
chebum I am so glad to hear about your speaker and that the EVA foam worked so well in your case. Good to know that judo-mats are another good source for EVA. I tried some cheap EVA floor mats from a home-improvement store but was not too pleased with them (too soft and low density) so I went back to the white EVA I started with.
My problem with hot glue is that it cools so quickly that it is hard to get clean joints. It does work really well as a seam sealer though. I use a contact cement which has over 1hr cure time and I usually let it outgas for a few days after glueing. I then go over the inner seams with hot glue to make sure it is very well sealed.
This does bring a big smile to me. It might even motivate me to come back
chebum I am so glad to hear about your speaker and that the EVA foam worked so well in your case. Good to know that judo-mats are another good source for EVA. I tried some cheap EVA floor mats from a home-improvement store but was not too pleased with them (too soft and low density) so I went back to the white EVA I started with.
My problem with hot glue is that it cools so quickly that it is hard to get clean joints. It does work really well as a seam sealer though. I use a contact cement which has over 1hr cure time and I usually let it outgas for a few days after glueing. I then go over the inner seams with hot glue to make sure it is very well sealed.
This does bring a big smile to me. It might even motivate me to come back
Last edited:
I find this very very interesting and wonder about a few things (with future builds in mind):I gave up making plywood cabinets sound clean. Thought about making them from MDF, but learned about EVA foam here on forum and gave it a try. The difference in one word is WOW.
- does this mean that most speaker enclosures (Sealed, BR, MLTL, BLH) will sound better in EVA as opposed to plywood or MDF?
- if one would to make an enclosure from plywood or MDF and only clad or cover the inside walls with EVA (or even foam core), would that give the same results? Obviously one would need to increase the inside dimensions to compensate for the thickness of the EVA or foam core.
- Status
- This old topic is closed. If you want to reopen this topic, contact a moderator using the "Report Post" button.
- Home
- Loudspeakers
- Full Range
- EVA foam for performance speaker enclosures