That looks very good. I think the standard 3 in 1 would be OK. SAE 30 sometimes is better. If nothing else I suspect normal 3 in 1 would clean out any gunge. The thing to understand is the original Thorens oil is almost impossible to wash out of the phosphor bronze. Mostly what we are doing is adding to the blend or cleaning. The heat of the motor causes a tidal flow of oil. If you want to do the very best you can I would try standard 3 in 1 and then never switch the unit off. The BBC didn't and old PYE ( Telstar ) records never switched their 301 off ( I serviced it ) . That way the tidal flow is near zero. The bad bit of the tidal flow ( heat high to low ) is if the wrong oil it gets drawn in after a few cycles. Whilst I shouldn't have believed the sewing machine people it was best to ask about 3 in 1 as it is so common. It invites that it will be used.
I built a turntable without a pully and set the speed by an oscillator, shaft was 6 mm instead of usual 6.33 of the pully and 4.91mm shaft ( Garrards own size, seems to be 5 mm polished ). The oil regarless of how little always went up the shaft and we got wow. The cure was simple. I fitted a device much like a pully to stop it. I now use that for 78's and to stop the oil climbing the shaft. Still get the better flutter of direct on the shaft as a bonus. It looks good also. This allows the use of stock bearings ( Oilite ). The Garrard can be drilled with oil ways and let into the original. It must be a push fit and not forced in. Be very careful if replacing a shaft. It will retain balance if you are. The shaft I used was a Thorens supplier. Also, static balance is best. Dynamic balancing machines seem to damage the shafts.
Once the motor is fully lubricated ( washed ) and kept running any oil added to the top bearing will in time find it's way down to the bottom bearing. If never switched off this oil will mostly do what was hoped for. The switching off is a small risk. You will also find idlers seem to last forever. Power used is not great.
Interesting info.
re: Phosphor Bronze.
Thorens is using Oilite sintered bronze bushings in their main platter bearing. I think most of us presume that the unique bushings within the E50 motor are also of that same alloy. I did.
The Oilite bronze bushing composition:
87 - 90% Copper,
~0 to .3% graphite,
~10% tin,
and some other stuff
Phosphor bronze composition:
Zinc – 9.9%
Tin – 2.2%
Iron – 1.9%
Phosphorus – 0.03%
Copper – 85.97%
Just so we know that the two metals discussed are not the same. A key difference being that the Oilite is a porous, oil-impregnated and so-called 'self-lube', kind of bushing, ---- while the Phosphor bronze is not at all porous, Unless you know of a source for such. That said, all available info suggests that it would make an excellent bushing material provided that a source of lubrication can be maintained. The crux of the matter.
The Oilite porous bronze material (SAE 841) comes impregnated with 30 wt mineral oil. Although I believe it is possible to specify otherwise if buying directly from that mfr.
So, yes, we diy'ers are mixing and blending oils as we rebuild our 60 year old record players.
Fwiw, I'm experimenting with some Delrin bushing sleeves in my TD124 Platter bearing that I lathe-turned from solid Delrin round rod. I'm using the 20 wt. "Thorens Oil", as previously described. I've filled the bearing housing with enough lube so that when displaced by the 14mm shaft, the lube reaches to the top and over-flows just a bit. (A precaution and also a reason for caution) An experiment.
Result: very long free-spin times. SQ seems no different from using the previously installed Oilite bushing sleeves.
-Steve
Last edited:
Oilite is an abused term. Delrin has given problems in motors. The standard so called Oilite whilst being pennies is usually one of the most perfect things one can buy. This is because to make a bad one costs the same as to make an excellent one. Look out for oval ones. This is due to someone doing something bad to them. People say if careful Oilite can be reamed. I never found that.
For the platter bearings many things can be used. Nylon types should be grown in a bucket of water to ensure they don't go tight. PTFE seems to be out of favour. The reason why Oilite types were used is if the customer was too timid to check the turntable it would work for many years with what it had. One old engineer suggested Navy bearings. These were wood. No reason why it shouldn't work. Gum metal also.
For the platter bearings many things can be used. Nylon types should be grown in a bucket of water to ensure they don't go tight. PTFE seems to be out of favour. The reason why Oilite types were used is if the customer was too timid to check the turntable it would work for many years with what it had. One old engineer suggested Navy bearings. These were wood. No reason why it shouldn't work. Gum metal also.
snip ..... One old engineer suggested Navy bearings. These were wood. No reason why it shouldn't work. Gum metal also.
re: Gum metal. I had to google that. A registered trademark of Toyota Central R&D Labs, Inc.
Wow. A titanium alloy, ductile and elastic. And, most likely, costly.
I'm not certain I'd want to try it, though.
re: Gun Metal. Was that it? An old composition of bronze used by various Navy's for their canon barrels. The idea for it in turntables seem to come out of Asia as near as I can tell. High copper composition. But current examples of this material can be a close, but not exact, match to the chemistry of the older (18th century) Gun Metal bronze.
re: Motor bushing materials versus platter brg. sleeve materials. As you note, the platter brg bushings are less fussy. It makes me want to try some Lignum Vitae (as a sleeve material) in the platter bearing housing....or not.
Platter brg thrust pad materials. In this application, harder seems to work well when mated properly to the composition of the thrust ball at the tip of the shaft. Example, sapphire ball against sapphire thrust plate, or ceramic ball against hardened steel thrust plate, or..... etc.
-Steve
Last edited:
I thought that " wood " get people thinking. My favourite thrust was graphite. I used brush grade for motors. The sound was softer which might be correct. The spot where it touches was not as worn a I thought it would be some months later. Not sure I liked it although it seemed it should be correct. If my friend from Thorens Kurt is right we hear shaft resonance usually at about 1.5 kHz.Ceramic balls make it worse at about 6 kHz. He fancied a cracked glass shaft to be an idea on a standard ball. He designed the latter reference Thorens.
I thought that " wood " get people thinking. My favourite thrust was graphite. I used brush grade for motors. The sound was softer which might be correct. The spot where it touches was not as worn a I thought it would be some months later. Not sure I liked it although it seemed it should be correct. If my friend from Thorens Kurt is right we hear shaft resonance usually at about 1.5 kHz.Ceramic balls make it worse at about 6 kHz. He fancied a cracked glass shaft to be an idea on a standard ball. He designed the latter reference Thorens.
I guess it wood've had to
re: graphite thrust on....301/401/501? I'd like to see a cad cross-section view of all of those bearings. I haven't had a 301/401 to look at up close.
re: shaft resonance. Interesting bit. Kurt. Is he still alive? I'd like to know by what methodology he was able to determine those values. We should get into such subjects.
-Steve
Kurt is about 50. He is a matamatician. I remember he and I discussing most people and maths in the London Science Museum. He pointed to a globe and said " most people see maths as getting from here to here, what they miss is the journey between". I took him to a Silverston FI test day when Red Bull were just starting to beat Renault with the same Renault engine ( I have a friend who works for Renault ). Kurt told Renault why the Red Bull was faster. He was right. They just looked at him as they do at me and assume we haven't a clue. We saw Frank Derney at then Toyota that day who was the designer of the improved Garrard Zero 100 arm. Really nice man and a real Garrard fan. His fame was the Williams Honda of Nigel Mansell.
Why I get a bit angry with high density materials and plinth design is resonace is caused by uniformity ( as a bearing ). Concrete at least can have fake chaos. Kurt points out you must mix the concrete until the last possible minute if wanting that. I use ply + MDF sheets, the glue being a big deal. It will curl so keep it clamped . Both help the other. MDF is very good. Problem with speakers is no one uses if properly.
Why I get a bit angry with high density materials and plinth design is resonace is caused by uniformity ( as a bearing ). Concrete at least can have fake chaos. Kurt points out you must mix the concrete until the last possible minute if wanting that. I use ply + MDF sheets, the glue being a big deal. It will curl so keep it clamped . Both help the other. MDF is very good. Problem with speakers is no one uses if properly.
Interesting info.
re: Phosphor Bronze.
Thorens is using Oilite sintered bronze bushings in their main platter bearing. I think most of us presume that the unique bushings within the E50 motor are also of that same alloy. I did.
The Oilite bronze bushing composition:
87 - 90% Copper,
~0 to .3% graphite,
~10% tin,
and some other stuff![]()
Phosphor bronze composition:
Zinc – 9.9%
Tin – 2.2%
Iron – 1.9%
Phosphorus – 0.03%
Copper – 85.97%
Just so we know that the two metals discussed are not the same. A key difference being that the Oilite is a porous, oil-impregnated and so-called 'self-lube', kind of bushing, ---- while the Phosphor bronze is not at all porous, Unless you know of a source for such. That said, all available info suggests that it would make an excellent bushing material provided that a source of lubrication can be maintained. The crux of the matter.
...
-Steve
Just as a demo of the difference, here's a picture of oilite bushes for the td124 and td125, along with motor bushes for the E50 motor, all immersed in a low viscosity ATF fluid on which I've drawn a vacuum. You can easily see the bubbles of air flowing from the oilite, while there are non from the motor bushes. Proof if proof were needed of the importance of external lubrication of the motor bushes.
Attachments
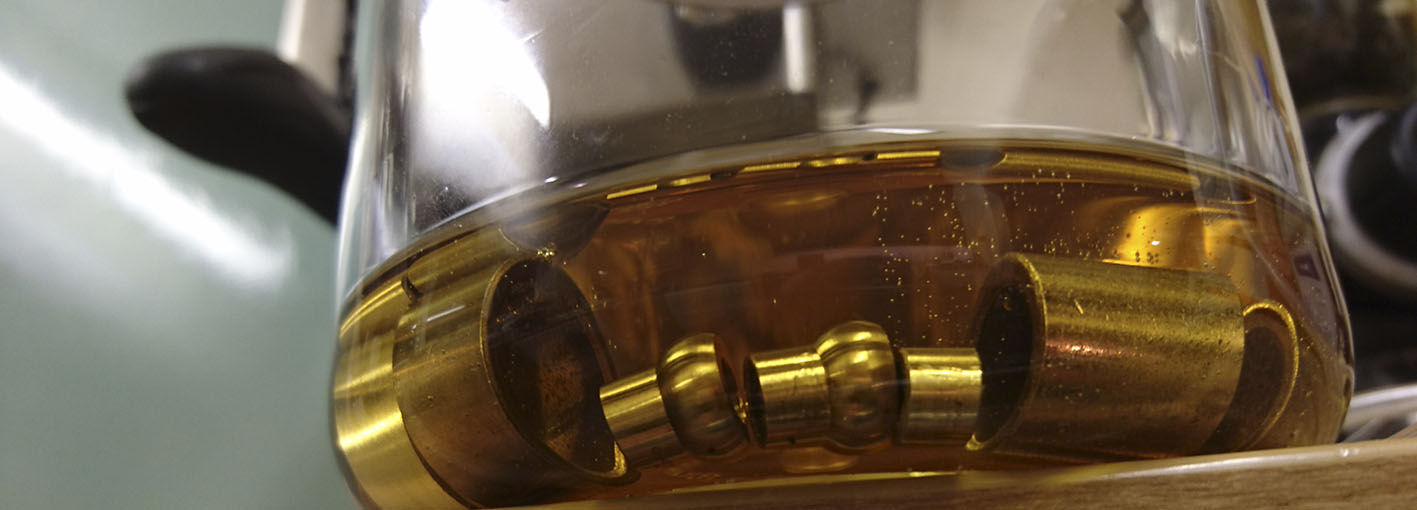
Are those motor bushes from Schopper?
I'm positive I'd prefer to use the porous bronze (Oilite), not whatever that is in the photo.
Did you say you had some TD125 bushing sleeves in there? That would be for a 10mm shaft. Impossible to service the TD125 bearing housing unless you want to do as the factory did; ..... Swage the bottom plate onto the housing. To rebuild one, you would need to destroy the bottom plate getting it off, debur-clean the end of the housing and then swage a 'new' bottom plate into position. It takes some tooling and a fairly decent drill press to swage.
-Steve
Hi Steve,
The motor bushes were purchased from Audiosilente as part of the E50 motor rebuild kit. I ended up reusing the original motor bushes as I wasn't happy with the replacements.
Replacing the bushes in the td125 bearing housing is tricky, but not impossible.
I used a No.1 12mm tap to cut a thread in the old bushing (top one first), then screwed in a piece of 12mm studding. By using a sleeve slightly larger than the outside of the bush, along with a large washer and a nut it's quite easy to extract the bush. As the bearing housing is machined all the way through its exactly the same process for the bottom bush. ( in the US I would expect 7/16 to be good replacement for the 12mm)
After extraction I removed and replaced the bearing support plate ( actually I simply turned it over and reused it) and thoroughly cleaned the inside of the bearing housing to remove any swarf produced by the tap.
Installing the new bushes is easy, I used a 100mm piece of hardwood, turned to just fit in the housing, then further turned down at one end to fit into the bush. It's then just a matter of pushing each bush into place, having well lubricated both the bushes and the housing.
This whole operation is much easier if you have the Mk1 td125, with its removable bearing housing, in fact I bought a replacement mk1 bearing housing and did the work on the bench before pressing out the mk2 housing and modifying the hole to take the earlier housing.
The motor bushes were purchased from Audiosilente as part of the E50 motor rebuild kit. I ended up reusing the original motor bushes as I wasn't happy with the replacements.
Replacing the bushes in the td125 bearing housing is tricky, but not impossible.
I used a No.1 12mm tap to cut a thread in the old bushing (top one first), then screwed in a piece of 12mm studding. By using a sleeve slightly larger than the outside of the bush, along with a large washer and a nut it's quite easy to extract the bush. As the bearing housing is machined all the way through its exactly the same process for the bottom bush. ( in the US I would expect 7/16 to be good replacement for the 12mm)
After extraction I removed and replaced the bearing support plate ( actually I simply turned it over and reused it) and thoroughly cleaned the inside of the bearing housing to remove any swarf produced by the tap.
Installing the new bushes is easy, I used a 100mm piece of hardwood, turned to just fit in the housing, then further turned down at one end to fit into the bush. It's then just a matter of pushing each bush into place, having well lubricated both the bushes and the housing.
This whole operation is much easier if you have the Mk1 td125, with its removable bearing housing, in fact I bought a replacement mk1 bearing housing and did the work on the bench before pressing out the mk2 housing and modifying the hole to take the earlier housing.
Audiosilente now has bushings made of sintered bronze which are supposed to be about as good as the OEM bushings when new. They've been available for a comparatively short period of time - I have a set I am planning to install during the next upgrade to my old MKI table which will include the MKII motor mounts, HanzeHiFi springs, different bearing end cap.. Etc.
Hi Steve,
The motor bushes were purchased from Audiosilente as part of the E50 motor rebuild kit. I ended up reusing the original motor bushes as I wasn't happy with the replacements.
Replacing the bushes in the td125 bearing housing is tricky, but not impossible.
I used a No.1 12mm tap to cut a thread in the old bushing (top one first), then screwed in a piece of 12mm studding. By using a sleeve slightly larger than the outside of the bush, along with a large washer and a nut it's quite easy to extract the bush. As the bearing housing is machined all the way through its exactly the same process for the bottom bush. ( in the US I would expect 7/16 to be good replacement for the 12mm)
After extraction I removed and replaced the bearing support plate ( actually I simply turned it over and reused it) and thoroughly cleaned the inside of the bearing housing to remove any swarf produced by the tap.
Installing the new bushes is easy, I used a 100mm piece of hardwood, turned to just fit in the housing, then further turned down at one end to fit into the bush. It's then just a matter of pushing each bush into place, having well lubricated both the bushes and the housing.
This whole operation is much easier if you have the Mk1 td125, with its removable bearing housing, in fact I bought a replacement mk1 bearing housing and did the work on the bench before pressing out the mk2 housing and modifying the hole to take the earlier housing.
Great ingenuity in that bushing sleeve extraction process. I never would have thought of that method. But thanks to your description I'm certain it will work.
As it turns out I have a mk1 housing that I've been saving for a future project turntable using Thorens parts.
I'm happy to be proved wrong, but the ones I bought back in March this year do not appear to have been made of sintered bronze and the current advert does state that they are made on a CNC machine from bronze.
Yes, and those are not the ones I am talking about which became available late this summer.
I'm happy to be proved wrong, but the ones I bought back in March this year do not appear to have been made of sintered bronze and the current advert does state that they are made on a CNC machine from bronze.
These are the old CNC bronze bushings.
Thorens TD 124 E50 Thorens 135 121 184 Complete Motor Rebuild Kit Made in Italy | eBay
These are the new sintered bushings.
New Sintered Heat Pressed Bronze Bushings Thorens TD124 E50 Complete Motor Kit | eBay
These are the old CNC bronze bushings.
Thorens TD 124 E50 Thorens 135 121 184 Complete Motor Rebuild Kit Made in Italy | eBay
These are the new sintered bushings.
New Sintered Heat Pressed Bronze Bushings Thorens TD124 E50 Complete Motor Kit | eBay
That makes sense, I guess they're just selling of the last of the old design along with the new.
The more I read this thread I feel the old saying " if it's not broken don't fix it " should be applied. Many reading this will assume their motors are mostly broken when they are mostly like new if what I see is typical. If you wiggle the motor shaft in the bearings it is very obvious if there is trouble. 90% plus I have ever seen are fine. Even when green oil comes out often all is not lost.
To be a bit brutal. The TD124's greatest technical advantage is also it's greatest weakness. That is the small belt. To my mind the Lenco is a slightly better compromise, it puts all the others to shame in the motor design and watch like precission whilst being powerful. It's as if Thorens chickened out and went for safe. They would have needed to spend a bit more money on the motor to get a better result. The Garrard 501 gets to - 79dB weighted without a belt. I think what might have happened is Garrard got the 301 out slightly before and lets be frank for stereo use 301 is a bit noisey. Thorens possibly took the 301 too much to heart and thought it's engineering suspect. As 401 proves the 301 can be bettered with subtle changes. Strangely the 301 is prefered even though it has more rumble. What troubles me is the Lenco has only been heard to be good in recent years. This casts a big cloud over the hi fi industry. Not those who make things, the ones we turn to for advice.
All I am trying to say to most people is leave well alone. At least we found we could use 3 in 1 oil. Now that's a victory.
The big problem with the TD124 motor is nothing is really bad about it. It's penny pinched.
One thing you could try is a cascaded set of passive mains filters. If you have 230 V you might be in luck with how easy it is. Use the 110 V windings of the motor and loose what you think is best ( 126 down to 90 V, 120 V my guess ). I did this for something completely different the other day and got from 6 % THD down to about 0.3%. I lost a bit more than here ( 40 down to 13 V ). I haven't a clue what values you use. Maybe someone here would want to find out. The conjecture is you will loose 20 watts. This will give the motor what it really needs. I assume the person doing this would know how to get the measurements. You will be suprised how quiet the bearings are if you do this. I didn't make a mistake, that's what I said.
To be a bit brutal. The TD124's greatest technical advantage is also it's greatest weakness. That is the small belt. To my mind the Lenco is a slightly better compromise, it puts all the others to shame in the motor design and watch like precission whilst being powerful. It's as if Thorens chickened out and went for safe. They would have needed to spend a bit more money on the motor to get a better result. The Garrard 501 gets to - 79dB weighted without a belt. I think what might have happened is Garrard got the 301 out slightly before and lets be frank for stereo use 301 is a bit noisey. Thorens possibly took the 301 too much to heart and thought it's engineering suspect. As 401 proves the 301 can be bettered with subtle changes. Strangely the 301 is prefered even though it has more rumble. What troubles me is the Lenco has only been heard to be good in recent years. This casts a big cloud over the hi fi industry. Not those who make things, the ones we turn to for advice.
All I am trying to say to most people is leave well alone. At least we found we could use 3 in 1 oil. Now that's a victory.
The big problem with the TD124 motor is nothing is really bad about it. It's penny pinched.
One thing you could try is a cascaded set of passive mains filters. If you have 230 V you might be in luck with how easy it is. Use the 110 V windings of the motor and loose what you think is best ( 126 down to 90 V, 120 V my guess ). I did this for something completely different the other day and got from 6 % THD down to about 0.3%. I lost a bit more than here ( 40 down to 13 V ). I haven't a clue what values you use. Maybe someone here would want to find out. The conjecture is you will loose 20 watts. This will give the motor what it really needs. I assume the person doing this would know how to get the measurements. You will be suprised how quiet the bearings are if you do this. I didn't make a mistake, that's what I said.
I just use a 60Hz crystal control sinusoidal source I designed a couple of years ago, ignoring transformer core distortion thd % is on the order of 0.1% the step up transformer increases it considerably, but still under 0.5% - mains distortion here can be >10% with flat topping so this is a considerable difference.
I have found that the table looses most of its mojo once the line voltage drops more than about 5% or so from the nominal voltage for the tap, noise is also reduced, and brake setting is easier, but I ended up not liking the result. I use the 100 - 125V tap with about 112V applied - works relatively well on both tables.
I have found that the table looses most of its mojo once the line voltage drops more than about 5% or so from the nominal voltage for the tap, noise is also reduced, and brake setting is easier, but I ended up not liking the result. I use the 100 - 125V tap with about 112V applied - works relatively well on both tables.
The more I read this thread I feel the old saying " if it's not broken don't fix it " should be applied. Many reading this will assume their motors are mostly broken when they are mostly like new if what I see is typical.
To be a bit brutal. The TD124's greatest technical advantage is also it's greatest weakness. That is the small belt. To my mind the Lenco is a slightly better compromise, it puts all the others to shame in the motor design and watch like precission whilst being powerful. It's as if Thorens chickened out and went for safe. All I am trying to say to most people is leave well alone. At least we found we could use 3 in 1 oil. Now that's a victory.
The big problem with the TD124 motor is nothing is really bad about it. It's penny pinched.
re: penny pinched motor. The E50. In Bung's book he does mention that the TD124 designer did intentionally choose a weaker motor for the TD124 in his quest to keep drive train vibes/noise to a minimum. Some might think he went a little too far in the direction of 'weak'. 10 watts.
I could also complain that the case work on the E50 does not assemble accurately. It requires some alignment in order to accomplish two things; 1: get the self aligning bushings in-line with the rotor shaft once all the pieces are in place...and....2: to get the rotor cerntered to the stator core.
3rdly, a gripe. I have seen some stator core laminates so severely warped that it becomes quite difficult to get a good rotor shaft-to-bushing alignment once the upper and lower casings are assembled and tightened down. Other examples, however, appear nearly perfect in condition and assemble with hardly any need of 'tuning' the alignment of rotor to bushings and rotor to stator core.
So, yes. There was obviously too much cost cutting going on with the motor. And once that motor maker got their production up to full speed it seems likely, if not apparent, that there was some defective product that escaped whatever their quality processes were and found their way into a finished product.
If I wanted to create a "super" TD124, the first component I'd look into improving would be that E50. And by improving I mean replacing with another example of the shaded pole induction motor. One with greater output and with a more precise build. Got any?
re: 3-in-One oil. I've no doubt that many different sorts of lubes may work in the motor. and if 3-in-one is mineral based, it should match with what's already in the Oilite bronze bushings when it comes out of that foundry in The UK, where Oilite bronze gets produced.
Perhaps Thorens custom ordered their porous bronze stock to be impregnated with a lube of their choice before any machining was done. Detailed information like that is lost with the people who worked at Thorens in Sainte-Croix. People who had worked there and lived out their life spans and are now mostly lost to the ages.
I have replaced motor bushings with new replacements and I have made use of the existing bushings after a thorough cleaning. These days I lean toward keeping the old bushings in use.
I have tried some different lubes within the E50. From thick to thin. I know that differential lube (for spiral bevel gears) is too viscous. (the motor came upt to speed far too slowly) I also tried some red and runny ATF (like 5 wt)...and that seemed to work fine...but I did not leave it that way for long. The 20 wt turbine oil I'm using now seems to be problem free. But different thinner lubes seem possible provided there is compatibility with those porous bronze bushings. I'm not certain about minimum viscosities. How thin is too thin....maybe 5wt was pushing the limits of thin.
re: the belt. Yes, this does introduce an inaccuracy into the drive. The stretch of the belt with every cog pulse of the motor. (keep in mind that the shaded pole motors do slip their cogging a bit) I suspect that the audible end effect of the belt is a slight 'softness' to the leading edge of transients. And I don't take that as a negative. The sound reproduction of a healthy TD124 doing its thing is quite beguiling to my ears.
So, if I were to work toward creating a 'super' TD124, as noted above, I would retain the belt and stepped pulley arrangement just as Thorens produced it. But that motor just seems to be its biggest weakness. And I would work on that before looking at alternate platter materials...which is another worthwhile topic.
-Steve
I could also complain that the case work on the E50 does not assemble accurately. It requires some alignment in order to accomplish two things; 1: get the self aligning bushings in-line with the rotor shaft once all the pieces are in place...and....2: to get the rotor cerntered to the stator core.
To get the rotor cerntered to the stator core on a recent rebuild, I used four .014"shims cut the long way from a glossy business card. They fit very nicely through the 4 large holes in the top and bottom plate and were extracted after snugging up the frame bolts.
Once the rotor is centered, the bushings are, as you noted, 'self aligning', though that alignment is helped immensely by a few sharp raps on the sides of the motor with a mallet or hammer and wood block.
I am currently running in the motor and this weekend will see if I can improve on the noise level using the traditional methods. I'm hoping the shims got me where I needed to be.
- Home
- Source & Line
- Analogue Source
- Restoring and Improving A Thorens TD-124 MKII