What's the most practical way of implementing a tight bracing for the driver magnet?
I cant think of any
other than maybe inserting a solid and heavy steel shaft, from outside, through back panel
a steel shaft with about the size of the magnet assembly
At Fb, the cone movement is at minimum, while acoustic output often is at maximum. That acoustic output can resonate the floor, which allows you to feel it in your feet.if my 12" woofers arent moving much, but mostly just vibrating, what kind of pressure am I dealing with ?
tho I still got ressonances to deal with
and even at this moderate SPL, bass is still felt my feet, and room pressure is there too
wonder how this can be, when woofers arent visibly moving
The 12" cone and voice coil moving in and out can cause mechanical movement like a lightweight version of a jackhammer, depending on the speaker cabinet and floor connection, that can cause your footsie feel without any acoustical connection.
ButtKicker transducers also work on feet...
Planet10, Thanks for making me think and admit there's a whole lot of shakin' goin' on here that I wasn't recognizing.
And the clamshell isobarics I'm building now have a removable front baffle board, which I'd better mount darn sturdy. Your "energy" example sure shows there's a lot of energy put into the baffleboard; it's 1" MDF painted with that cabinet paint. Besides the bolts around the cabinet edges, I also have one bolt thru the middle of the baffleboard into the cabinet's thick center bulkhead brace (I put a large cross-hole thru the 1" MDF center brace so I could insert a T-nut for the center baffleboard screw). I'd sure like to come up with some cheap large sheet rubber gasket material for mounting the baffleboard, otherwise it's down to foam weatherstripping or rope caulk or ??? Someone recommended Blue Tack, is that appropriate and cheap? I definitely want to be able to take it apart again. I'm going to have the same issues mounting the drivers; I had to modify cardboard gaskets to back-mount the drivers (I guess the drivers' rims are just a little smaller in diameter than a standard 12"), and I'm not sure how much the cardboard gaskets leak at each mounting screwhole.
And the clamshell isobarics I'm building now have a removable front baffle board, which I'd better mount darn sturdy. Your "energy" example sure shows there's a lot of energy put into the baffleboard; it's 1" MDF painted with that cabinet paint. Besides the bolts around the cabinet edges, I also have one bolt thru the middle of the baffleboard into the cabinet's thick center bulkhead brace (I put a large cross-hole thru the 1" MDF center brace so I could insert a T-nut for the center baffleboard screw). I'd sure like to come up with some cheap large sheet rubber gasket material for mounting the baffleboard, otherwise it's down to foam weatherstripping or rope caulk or ??? Someone recommended Blue Tack, is that appropriate and cheap? I definitely want to be able to take it apart again. I'm going to have the same issues mounting the drivers; I had to modify cardboard gaskets to back-mount the drivers (I guess the drivers' rims are just a little smaller in diameter than a standard 12"), and I'm not sure how much the cardboard gaskets leak at each mounting screwhole.
Last edited:
there's a lot of energy put into the baffleboard; it's 1" MDF
So not all that strong ... 1" MDF ~ 15mm Baltic Birch
I'd sure like to come up with some cheap large sheet rubber gasket material for mounting the baffleboard
With a lossy gasket, you keep more of the energy in the baffle instead of sharing it with the rest of the box. With the baffle being the weakest panel in the box, you have a worst case situation.
dave
This is all a bit more complicated than I hoped. I liked bbggg's suggestion of an oval cutout brace behind the baffle and parallel to it which must stop the sides vibrating a lot:
In fact my MA R300 oldies have a couple of braces down the sides which must be the same idea:
Having just bought several metres of pine battening for the edges and for cross-bracing behind the woofer, I am now questioning if it is the right road to go down. Some triangles of timber, perhaps even just softwood rather than hard wood might be good. Am also thinking about the way they couple to the floor through the bottom, perhaps the front baffle should be diagonally braced to the bottom panel more?
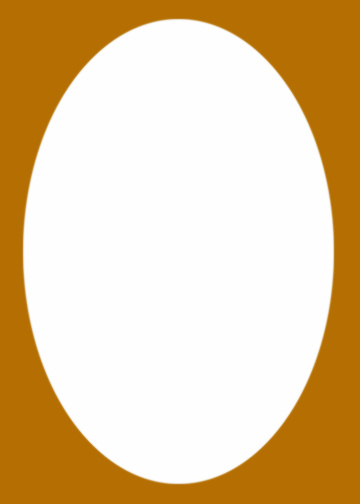
In fact my MA R300 oldies have a couple of braces down the sides which must be the same idea:
An externally hosted image should be here but it was not working when we last tested it.
Having just bought several metres of pine battening for the edges and for cross-bracing behind the woofer, I am now questioning if it is the right road to go down. Some triangles of timber, perhaps even just softwood rather than hard wood might be good. Am also thinking about the way they couple to the floor through the bottom, perhaps the front baffle should be diagonally braced to the bottom panel more?
This is all a bit more complicated than I hoped. I liked bbggg's suggestion of an oval cutout brace behind the baffle and parallel to it which must stop the sides vibrating a lot:
![]()
My Paradigm Monitor 7's and Acoustic Energy AE105's use a similar scheme to this. The cabinets are very rigid indeed.
1" MDF ~ 15mm Baltic Birch
With a lossy gasket, you keep more of the energy in the baffle instead of sharing it with the rest of the box. With the baffle being the weakest panel in the box, you have a worst case situation.
dave
By lossy, do you mean loose, rubbery, or literally burning up energy?
OK I'd like it firm but I want it to disassemble/reassemble easily and I'd like something to imrove the seal and bond. I'm also concerend that if I bolt it down really tight, painted surface to painted surface, the two paint surfaces will eventuall bond to each other. What could I put between which will help the uneven surfaces bond, couple, and seal, yet part easily for disassembly? In the past I hand-rolled rope caulk into skinny snakes, and laid down concentric sealing lines which flattened considerably during tightening. But there must be something better.
So how are you defining 'strong'?? Before failure or resisting deflection? The 1" MDF certainly seems to resist deflection better than thinner plywood. The MDF also seems to have much better internal damping than the plywood. Considerable strength also comes from the 8 thick coats of commercial enclosure paint, especially when that's got the greater 1" thickness of the MDF sandwiched between the coats of plasticized paint. The plywood rings like a bell (or used to before coating) with the knuckle-wrap test, but the MDF seemed much more dead right from the start. I spaced the drivers apart (close enough for long wavelengths yet approx even spacing when cabinets are stacked), so between drivers the baffle board is very strong and there is also a bolt there thru the middle of the baffle board into a similar 1" thick MDF bulkhead type brace. The baffle board bolts to a plywood front plate with a large oval cut into it for clearance to the drivers bolted to both sides of the removable baffle board.
OK I'd like it firm but I want it to disassemble/reassemble easily and I'd like something to imrove the seal and bond.
If you have to make it removable, the skinniest closed cel, neoprene foam gaskets (weather stripping) you can get. I feel glue is better.
So how are you defining 'strong'?? Before failure or resisting deflection? The 1" MDF certainly seems to resist deflection better than thinner plywood.
Always in terms of how it afects cabinet resonance. The 1" to 15mm data is the stiffness of the material -- the ability to resist deflection.
The MDF also seems to have much better internal damping than the plywood.
It does not. Every transition from one ply to the next is an impedance transition which gives plywood greater damping and less energy storage.
Considerable strength also comes from the 8 thick coats of commercial enclosure paint, especially when that's got the greater 1" thickness of the MDF sandwiched between the coats of plasticized paint.
Same as it would on any sybstrate.
The plywood rings like a bell (or used to before coating) with the knuckle-wrap test, but the MDF seemed much more dead right from the start.
Most people do not know how to interpret a knuckle wrap test -- quite an artificial method of excitation.
For a woofer in particular, rings like a bell is good. High frequency & high Q. High frequency means that the music will not ever provide energy to excite the resonance because it is above the passband of the woofer (so it never resonates), and it has been shown that high Q resonances are less audiable than low Q ones.
Worth reading: http://www.diyaudio.com/forums/cons...ussion-what-materials-build-speakers-out.html
dave
If I follow what Dave is saying, plywood made of layers of timber with the grain in alternating directions is relatively strong and damping then. 
Is solid pine worse then? That always seems pretty sturdy to me, at least along the grain. Plywood always feels like flimsy stuff, but maybe it's better damped. For sure, my chipboard boxes have the strength of weetabix breakfast biscuits by comparison.
Still don't know what to do to them exactly. You're not helping me...
Is solid pine worse then? That always seems pretty sturdy to me, at least along the grain. Plywood always feels like flimsy stuff, but maybe it's better damped. For sure, my chipboard boxes have the strength of weetabix breakfast biscuits by comparison.
An externally hosted image should be here but it was not working when we last tested it.
Still don't know what to do to them exactly. You're not helping me...

Is solid pine worse then? That always seems pretty sturdy to me, at least along the grain. Plywood always feels like flimsy stuff, but maybe it's better damped.
We had the opportunity to directly compare 2 Mar-Kel12T, one made of solid Douglas Fir (a pine), and one made of 13 ply BB of the same thickness.
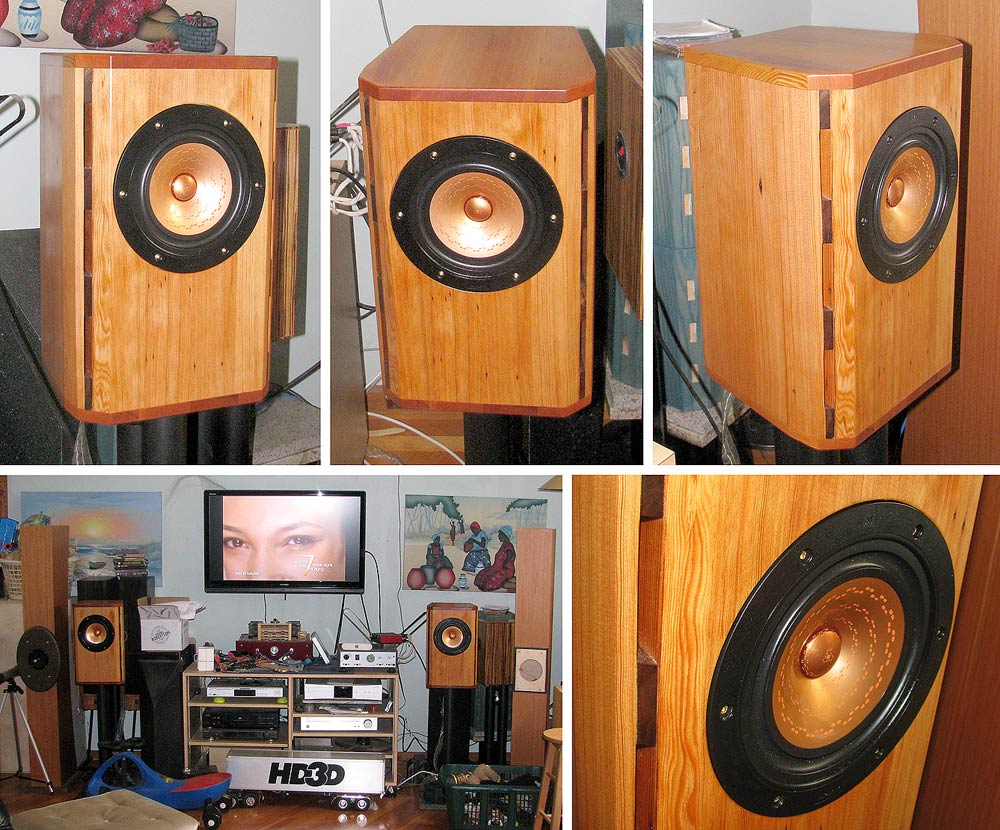
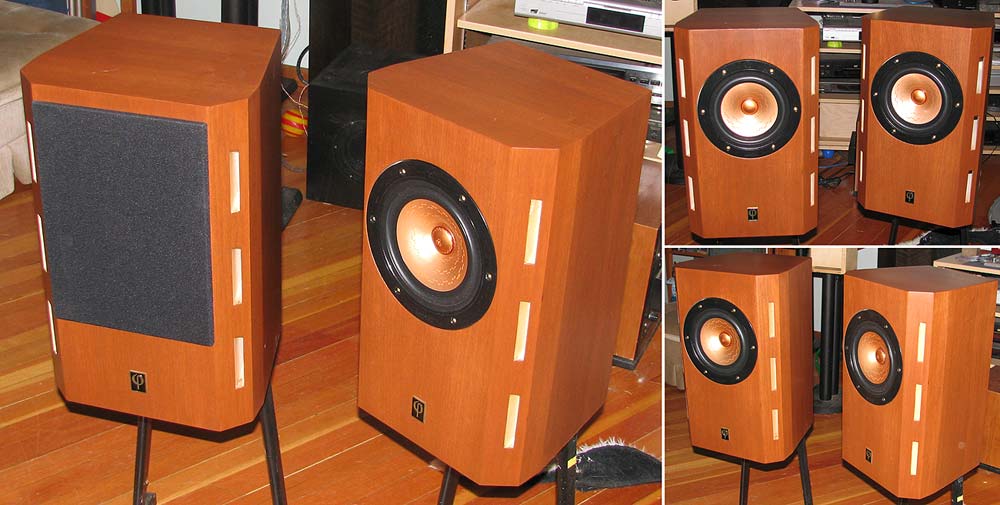
The fir had some colourations that the BB did not,
dave
hi,
I did some work about this subject at a fairly high level some time ago:
http://www.diyaudio.com/forums/multi-way/67142-new-floorstander-project-3.html#post773333
also to expose the complexity of the issue:
http://nsa28.casimages.com/img/2011/11/29/111129040559589370.png
Damping (blue versus un-damped black)
http://nsa28.casimages.com/img/2011/12/16/111216061449327178.png
and to be read:
http://downloads.bbc.co.uk/rd/pubs/reports/1977-03.pdf
but Fahy, Ingard, Lesueur are higher level...
BTW I mostly agree with Dr Geddes and at the end of the day it is what is scientifically heard that counts and the box makes a difference but the diminishing return wall is hit quite quickly.
I personally advocate for a lighttish box with curved and tension constrained sides (think “U”) with decent damping applied within the thickness and a front panel made of Aluminium, so called “Briggs” and braces to eject the main resonances outside the bandwidth of the speaker put inside and finally conjugated with mineral wool. This is already truly over killed and the absolute limit that the craziest DYI should aim. Anything above that is pure jewellery. You can make do without aluminium by stacking several layers of stiff woods...
The shape can save a lot of efforts and also deal with diffraction...
M
I did some work about this subject at a fairly high level some time ago:
http://www.diyaudio.com/forums/multi-way/67142-new-floorstander-project-3.html#post773333
also to expose the complexity of the issue:
http://nsa28.casimages.com/img/2011/11/29/111129040559589370.png
Damping (blue versus un-damped black)
http://nsa28.casimages.com/img/2011/12/16/111216061449327178.png
and to be read:
http://downloads.bbc.co.uk/rd/pubs/reports/1977-03.pdf
but Fahy, Ingard, Lesueur are higher level...
BTW I mostly agree with Dr Geddes and at the end of the day it is what is scientifically heard that counts and the box makes a difference but the diminishing return wall is hit quite quickly.
I personally advocate for a lighttish box with curved and tension constrained sides (think “U”) with decent damping applied within the thickness and a front panel made of Aluminium, so called “Briggs” and braces to eject the main resonances outside the bandwidth of the speaker put inside and finally conjugated with mineral wool. This is already truly over killed and the absolute limit that the craziest DYI should aim. Anything above that is pure jewellery. You can make do without aluminium by stacking several layers of stiff woods...
The shape can save a lot of efforts and also deal with diffraction...
M
You're probably thinking of cheap ply. Baltic birch ply is very different
Yes, these flat-pack kit enclosures are made of the cheapest plywood ever made; I didn't even know they made stuff this lousy. Very different from the 12-ply birch from Finland I use for guitar cabinets. Some plywoods are so saturated with glue they act more like one solid than layered. Same goes for chipboard or MDF, some is made from fine sawdust and others from large chips. We probably should be careful making too-broad statements without considering the exact material.
Planet10, please where did you get this info comparing 1" MDF to 15mm birch ply?
Too bad these materials don't come with some spec for 'internal damping' but stiffness increases with dimension more than linearly, so its difficult to believe the thicker MDF doesn't have better internal damping (or "amortization internal coefficient epsilon' as Ralphs99 calls it).
Too bad these materials don't come with some spec for 'internal damping' but stiffness increases with dimension more than linearly, so its difficult to believe the thicker MDF doesn't have better internal damping (or "amortization internal coefficient epsilon' as Ralphs99 calls it).
1" MDF is closer to 25mm+.
Theoretically, the denser the material, the less effect it will have on the calculated design. So I'm guessing solid granite (which I've seen), or cast iron for that matter, would be ideal. I've built the same design using 18mm/13 ply baltic birch, and 3/4" MDF. I am unable to tell the difference between the two.
Theoretically, the denser the material, the less effect it will have on the calculated design. So I'm guessing solid granite (which I've seen), or cast iron for that matter, would be ideal. I've built the same design using 18mm/13 ply baltic birch, and 3/4" MDF. I am unable to tell the difference between the two.
Last edited:
Very different from the 12-ply birch from Finland
Even number of plies is hard to find, odd numbers is the order of the day so that the grain on the outer faces.
dave
please where did you get this info comparing 1" MDF to 15mm birch ply?
Extrapolated from GM's 1 1/4" MDF the same stiffness as 18mm BB.
Too bad these materials don't come with some spec for 'internal damping' but stiffness increases with dimension more than linearly, so its difficult to believe the thicker MDF doesn't have better internal damping (or "amortization internal coefficient epsilon' as Ralphs99 calls it).
stiffness increases with the cube of thickness. stiffness has nothing to do with internal damping. MDF is a homogenous material, and IME not suitable for building quality speaker boxes.
dave
MDF is a homogenous material, and IME not suitable for building quality speaker boxes.
dave
I think you mean to say "homogeneous", as "homogenous" has a different definition in this application.
- Status
- This old topic is closed. If you want to reopen this topic, contact a moderator using the "Report Post" button.
- Home
- Loudspeakers
- Multi-Way
- Bracing overkill yay or nay ?