Apparently SL believes it helps.
Thanks John,
I was going to ask Dave why he feels Linkwitz is wrong on this myself. Regardless of the laughter it will provoke, I'm going to try it. I want to see the difference, if it makes any.
Only problem is how long it takes for the silicone to cure - probably a full day before I can actually put the driver back in for testing.
If it still smells of vinegar then it's still emitting acetic acid and indicates it's still curing.
A thin layer bewteen two porous and damp substrates will cure in an hour.
Thicker layer with one impervious substrate and little humidity could take more than a week to cure.
Most of these silicone sealers are a two part chemical reaction.
One part comes out of the container, the second part is water from the substrate or from the air. If both are dry it will never cure. It needs the second part.
A thin layer bewteen two porous and damp substrates will cure in an hour.
Thicker layer with one impervious substrate and little humidity could take more than a week to cure.
Most of these silicone sealers are a two part chemical reaction.
One part comes out of the container, the second part is water from the substrate or from the air. If both are dry it will never cure. It needs the second part.
Last edited:
...it will never cure...
Such negativity Andrew

I will build it in layers - 3 or 4 allowing each to skin before applying the next or not, it is afterall just a 1/4" x 1/2" bead. It will probably be cured enough by later this evening to test, otherwise there is tomorrow
If it still smells of vinegar then it's still emitting acetic acid and indicates it's still curing.
A thin layer bewteen two porous and damp substrates will cure in an hour.
Thicker layer with one impervious substrate and little humidity could take more than a week to cure.
Most of these silicone sealers are a two part chemical reaction.
One part comes out of the container, the second part is water from the substrate or from the air. If both are dry it will never cure. It needs the second part.
For large sections or volumes of silicon, a 2-part silicon molding rubber is best. However, it is expensive, but available in a wide number of durometers.
RTV Silicon available at the hardware store in a tube needs air and moisture to cure. If the depth or volume is too much the interior will not cure for days or weeks.
If the depth or volume is too much the interior will not cure for days or weeks.
This is true on an impervious material like plastic or metal but not on wood - it will cure quickly.
MJL,
look at the range of curing periods that are being quoted for different scenarios.
1hour to never. Both ends of the scale are true for the conditions applicable to that scenario.
Working with wood that is porous and has been stored/used in a humid atmosphere will certainly provide the water required for a cure.
You need to read what is being said in response to your question and try to estimate where in the range your conditions fall.
The magnet to board will be different from the T assembly with pervious damp materials on both sides.
You can even spray on a fine mist of water before starting to reduce cure time.
I am not being negative, simply accepting the laws of nature, in this case the chemistry of a two part formula that use the humidity for the second part. Have a think for a moment. How long has the tube of two part silicone been in stock before you decided to cut open the dispensing end? Had it cured when you want to use it? It's chemistry.
The smell will tell you a lot!
look at the range of curing periods that are being quoted for different scenarios.
1hour to never. Both ends of the scale are true for the conditions applicable to that scenario.
Working with wood that is porous and has been stored/used in a humid atmosphere will certainly provide the water required for a cure.
You need to read what is being said in response to your question and try to estimate where in the range your conditions fall.
The magnet to board will be different from the T assembly with pervious damp materials on both sides.
You can even spray on a fine mist of water before starting to reduce cure time.
I am not being negative, simply accepting the laws of nature, in this case the chemistry of a two part formula that use the humidity for the second part. Have a think for a moment. How long has the tube of two part silicone been in stock before you decided to cut open the dispensing end? Had it cured when you want to use it? It's chemistry.
The smell will tell you a lot!
Andrew, my friend, relax. You are preaching to the choir - I have used more silicone than many have seen in their lifetimes. No exaggeration. 
Onward...here's the "work in progress:
Previous to this I tested the box as it was (it is the MDF box from the discussion on building materials thread). I then added the centre brace to support the driver magnet and tested again.
Finally, when the silicone that forms the isolator cures I'll test it again and we shall see if it is worth the bother.
Onward...here's the "work in progress:
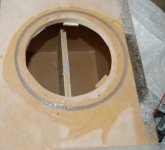
Previous to this I tested the box as it was (it is the MDF box from the discussion on building materials thread). I then added the centre brace to support the driver magnet and tested again.
Finally, when the silicone that forms the isolator cures I'll test it again and we shall see if it is worth the bother.
Hi John, i see everything is coming along quite nicelyAlso I would like to develop a way to mechanically isolate the driver frame from the enclosure. I'm convinced that much of what I'm seeing on the measurements are direct mechanical contribution from the drivers.
Here is a suggestion for you (having noticed you have a welder). I see you are already attempting to effectively disconnect the driver from the baffle by using silicone between the driver & cabinet. However you'll still need to bolt the speaker to the cabinet itself.
You could try the following
I think you can see that if you had some kind of foam rubber on the front of the steel plate (around the cylindrical spacer) that once the driver is bolted up it'll effectively be floating but also sealed
E2A:- Kind of like a T nut with an oversized back & no teeth but with a longer collar...
Hope it helps chap, if you need it explaining further i'd be happy to. However i feel pretty sure you'll grasp what i'm getting at!
Bests, Mark.
Last edited:
Previous to this I tested the box as it was (it is the MDF box from the discussion on building materials thread). I then added the centre brace to support the driver magnet and tested again.
Before you added the silicone did you test driver output? My premise is that isolating the driver will keep the excess energy in the driver (plus whatever you rigidly attach it to).
dave
Hope it helps chap, if you need it explaining further i'd be happy to. However i feel pretty sure you'll grasp what i'm getting at!
Bests, Mark.
Hi mark,
I understood perfectly, in fact I thought of doing it that way first but consider that the driver needs to make a tight seal to the cabinet, it needs to be solidly bolted to something. The ring of wood that it is bolted to is now really a part of the driver (and moves with it) while the silicone isolates it from the rest of the cabinet.
Before you added the silicone did you test driver output? My premise is that isolating the driver will keep the excess energy in the driver (plus whatever you rigidly attach it to).
dave
No, I just did accelerometer measurements. What I'm doing here is done in mechanical systems all the time. The ductwork in my house has a similar isolator between the furnace and the main plenum - it reduces mechanical vibration from the furnace in the ductwork.
I know what you are saying Dave, what happens to the mechanical energy that is normally transfered to the box? It is my guess that with this method part of the energy is damped by the silicone, part is transfered to the box and part is dissipated by the driver itself. When you consider that no mechanical transfer is 100% efficient, the driver will probably need to dissipate no more energy with the silicone as without.
Doesn't the driver rely on being attached to a fixed structure to keep the motor from moving the driver frame instead of the piston/cone?
By uncoupling the driver from the baffle with silicone you lose a driver fixation point and degrade driver transient response.
Put another way, you gain driver isolation but degrade driver performance.
By uncoupling the driver from the baffle with silicone you lose a driver fixation point and degrade driver transient response.
Put another way, you gain driver isolation but degrade driver performance.
I don't think he's decoupling the driver from the baffle. He's using silicone on the magnet to damp the basket against a brace. I think you are correct John that adding silicone just damps it slightly as the frame is still carrying most of the resonance. Dave's point being that without a firm mechanical attachment, you aren't transferring that much into the brace. Dave, did I read you right?
Doesn't the driver rely on being attached to a fixed structure to keep the motor from moving the driver frame instead of the piston/cone?
If you consider the mass of the cone as opposed to the mass of the frame/magnet/structure of the driver you can see that one massively outweighs the other, therefore inertia is on the motors side.
Liken it to a gunshot, by preventing the rifles recoil will the bullet travel further and faster? If so, by how much.
These things can be investigated and quantified but the focus now is the amount of energy that is being transfered to the box from the driver and how to reduce that.
What a mess ! If I missed something ,forgive me 
The driver is attached to the baffle with screws (with retro fitted bolts),so to improve rigidity a circular steel clamp would make the whole thing stiffer.
This ,to make the magnet really pressing the brace . For me ,elastic materials such silicon should be avoided , better to use some high-tech ultra rigid materials ,just to avoid micro-friction between the two parts .
The driver is attached to the baffle with screws (with retro fitted bolts),so to improve rigidity a circular steel clamp would make the whole thing stiffer.
This ,to make the magnet really pressing the brace . For me ,elastic materials such silicon should be avoided , better to use some high-tech ultra rigid materials ,just to avoid micro-friction between the two parts .
Its funny
Right now I have a couple of 15" woofers standing on the floor, on their magnet only, nothing else
The whole room rumbles, and loose items rattle, depending on signal ofcourse
Otherwise very fine bass
Tho, if I lift it just one bit from the floor, NO bass whatsoever
Right now I have a couple of 15" woofers standing on the floor, on their magnet only, nothing else
The whole room rumbles, and loose items rattle, depending on signal ofcourse
Otherwise very fine bass
Tho, if I lift it just one bit from the floor, NO bass whatsoever
If I missed something ,
You certainly did.
The silicone is set enough to mount the driver (the driver needs silicone between the magnet and the brace and that needs to cure also) so I will not be able to test it today.
By tomorrow evening (whenever I get home) it will be ready to go.
Wish me luck, comrades!
First, somehow I missed an entire page of this thread - the Battlestar Gallactica reference is exactly what i was thinking.
I am not sure the bullet analogy holds up - but I see where you are trying to go.
My thinking is that loudspeaker distortion is usually about 50dB down, 100 000 X less than the signal, it is not difficult (for me) to imagine driver frame movements making a negative contribution to performance when thought about in this context.
What is the resonant frequency of silicone? A while back I measured the RF of sorbothane and it was impressively low. I think this could work in your favor.
Finally there is also reductions in efficiency to consider, which would not be linear. I really don't know how big they would be. A reduction in efficiency could be overcome with more power which I have a feeling is something that you might have a good grasp on
Your are correct to point out that the effect can be measured and quantified - I can't wait to see the results! I would love to be proven wrong because the approach you are taking is so simple it would be great if it worked well.
Do you have the means to construct a baffle out of 1 inch thick aluminum? That is my (distant) plan.
If you consider the mass of the cone as opposed to the mass of the frame/magnet/structure of the driver you can see that one massively outweighs the other, therefore inertia is on the motors side.
Liken it to a gunshot, by preventing the rifles recoil will the bullet travel further and faster? If so, by how much.
These things can be investigated and quantified but the focus now is the amount of energy that is being transfered to the box from the driver and how to reduce that.
I am not sure the bullet analogy holds up - but I see where you are trying to go.
My thinking is that loudspeaker distortion is usually about 50dB down, 100 000 X less than the signal, it is not difficult (for me) to imagine driver frame movements making a negative contribution to performance when thought about in this context.
What is the resonant frequency of silicone? A while back I measured the RF of sorbothane and it was impressively low. I think this could work in your favor.
Finally there is also reductions in efficiency to consider, which would not be linear. I really don't know how big they would be. A reduction in efficiency could be overcome with more power which I have a feeling is something that you might have a good grasp on
Your are correct to point out that the effect can be measured and quantified - I can't wait to see the results! I would love to be proven wrong because the approach you are taking is so simple it would be great if it worked well.
Do you have the means to construct a baffle out of 1 inch thick aluminum? That is my (distant) plan.
Its funny
Right now I have a couple of 15" woofers standing on the floor, on their magnet only, nothing else
The whole room rumbles, and loose items rattle, depending on signal ofcourse
Otherwise very fine bass
Tho, if I lift it just one bit from the floor, NO bass whatsoever
I think this is quite relevant. Have you tried placing the drivers on some silicone or something with similar properties. I would be curious to hear your results.
- Status
- This old topic is closed. If you want to reopen this topic, contact a moderator using the "Report Post" button.
- Home
- Loudspeakers
- Multi-Way
- Large 3-ways design / build