Hi,
I observed degrading solder joins of the power transistors of my Accuphase amp. The Amp is thirty years old.
When I re-soldered them, they even crackled.
Has anybody experienced this phenomenon?
I think it's due to mechanical stress between the heat sink and the PCB. It could be caused by warming and cooling of the transistor.
What do you thing?
Stephan
I observed degrading solder joins of the power transistors of my Accuphase amp. The Amp is thirty years old.
When I re-soldered them, they even crackled.
Has anybody experienced this phenomenon?
I think it's due to mechanical stress between the heat sink and the PCB. It could be caused by warming and cooling of the transistor.
What do you thing?
Stephan
funny you mention that just now. I noticed the same thing on an old amp I'm redoing. Not really sure what's up with that. It stinks too,..might being the wiring insulation though.
Some of the old solder I used in the late 60's did have a funny smell and I too have noticed it when repairing old stuff.
I put it down to the type of flux used rather that old wiring.
I think the problem, which i too have seen in some old Armstrong amps, is due to thermal stress.
A similar phenomenon is found in old computers or any old equipment with socketed chips. In old IBM PCs, the memory chips would get so loose they would fall out !!!!
Andy
I put it down to the type of flux used rather that old wiring.
I think the problem, which i too have seen in some old Armstrong amps, is due to thermal stress.
A similar phenomenon is found in old computers or any old equipment with socketed chips. In old IBM PCs, the memory chips would get so loose they would fall out !!!!
Andy
there are hundreds of solder flux "recipes" used around the world.... some are pretty bad, smelling like cat urine in some cases...... especially bad are the water soluble fluxes..... kester fluxes aren't bad, most of them smell like pine. i suppose also, like vegetable oils do, that some fluxes could become rancid after a long time. organic chemistry isn't my strong suit, but a lot of organic oils and resins slowly oxidize over time, usually making them smell very bad.
yes, the thermal cycling of transistors causes stress failures in solder connections. you will notice most of the time, it's the collector leads that have stress rings in their solder joints, since it's the collector lead that's got a direct thermal connection to the transistor die, and expands/contracts the most.
yes, the thermal cycling of transistors causes stress failures in solder connections. you will notice most of the time, it's the collector leads that have stress rings in their solder joints, since it's the collector lead that's got a direct thermal connection to the transistor die, and expands/contracts the most.
Hi,
Remelting the solder with a tiny smear of paste or liquid flux over the joint should renew the connection and take out ALL the fatigue stress/strain.
gas escaping from within the solder?When I re-soldered them, they even crackled
Remelting the solder with a tiny smear of paste or liquid flux over the joint should renew the connection and take out ALL the fatigue stress/strain.
reins said:Hi,
I observed degrading solder joins of the power transistors of my Accuphase amp. The Amp is thirty years old.
When I re-soldered them, they even crackled.
Has anybody experienced this phenomenon?
I think it's due to mechanical stress between the heat sink and the PCB. It could be caused by warming and cooling of the transistor.
What do you thing?
Stephan
A part from thermal stressing, the main cause for this occurrence is poor quality of solder which require higher melting temperature (and consequent higher stress of PCB when the equipment was build) and it's more stiff than good solder, with
subsequents cracks when equipment go in thermal cycle for years. Usually this defect come up after some or many, when warranty is abundantly gone for good...
Hi
Piercarlo
AndrewT said:Hi, gas escaping from within the solder?
No, gas hasn't escaped. The crackling was mechanical.
Stephan
that implies strain, followed by release as the area resisting became less as the melt proceeded.reins said:
No, gas hasn't escaped. The crackling was mechanical.
Stephan
I may be wrong but from my experience I tink they have trouble to set wave or automated soldering process for all types of component at same time if they set process for light pins or wire it will not work on heavy component ( many times I saw connectors pins or relay with poor solders and cracks ).
I think they have not be heated to correct temperature in automated process, this is why they dont last.
If they set process for heavy component it may be too hot for light components, this is why you may have trouble with heavy components when they are soldered on automated machines.
I think they have not be heated to correct temperature in automated process, this is why they dont last.
If they set process for heavy component it may be too hot for light components, this is why you may have trouble with heavy components when they are soldered on automated machines.
i've occasionally seen thermally stressed solder that gets "crunchy" and has the consistency of wet concrete when melted. i usually suck this junk off with a solder sucker (it doesn't wick well, either) and replace it with fresh solder. if it's in a part of the board where there's enough heat to discolor the board, i add a little bit of silver solder, or use straight silver solder to prevent that from happening again. silver solder has a higher melting point, and will look like a "cold solder" joint compared to lead based solder, but as long as you flux it properly, it will make a good connection. btw a good flux for badly oxidized connections is ASPIRIN (not tylenol or ibuprophen) tablets, it even works on steel.... just make sure you clean it off completely afterwards, as it is an acid flux...... and don't get the fumes in your face. or you can use zinc chloride flux, which works very well, it also is an acid flux. ZnCl flux usually comes in the package with silver solder.
It's correct that warming and cooling do stress the solder joints. As you say resolder them may be the solution, especailly when you have a bad connection somewhere. If you also add vibrations this degrading may become faster. Heavy parts like transformers, big caps are more sensitive for this.reins said:Hi,
I observed degrading solder joins of the power transistors of my Accuphase amp. The Amp is thirty years old.
When I re-soldered them, they even crackled.
Has anybody experienced this phenomenon?
I think it's due to mechanical stress between the heat sink and the PCB. It could be caused by warming and cooling of the transistor.
What do you thing?
Stephan
actually, the aspirin thing i picked up when i worked at NAD. if you look at a 3140 that has the stability mod done to it, you will see caps soldered directly to the steel chassis. aspirin works as a flux for soldering to steel.
the ZnCl flux paste, i used when building prototypes for a military contract. the soldering for that equipment had to be all silver soldered with ZnCl flux paste. rosin flux was not used because it does not reconstitute the silver metal from tarnish, the ZnCl does. it's a chemical reduction AgO2+ZnCl=Ag+ZnClO2 (silver oxide + zinc chloride = metallic silver + zinc chlorate) with the heat accelerating the reduction.
the ZnCl flux paste, i used when building prototypes for a military contract. the soldering for that equipment had to be all silver soldered with ZnCl flux paste. rosin flux was not used because it does not reconstitute the silver metal from tarnish, the ZnCl does. it's a chemical reduction AgO2+ZnCl=Ag+ZnClO2 (silver oxide + zinc chloride = metallic silver + zinc chlorate) with the heat accelerating the reduction.
When the flux isn't removed completely all sorts of bad things happen. Thermal stress just accelerates it.

UNACCEPTABLE
OVERHEATED SOLDER
Overheated solder has a dull, gray, frosty and/or crystallized appearance and is the result of excessive exposure to heat.
NASA-STD-8739.3 [13.6.2.b.2]
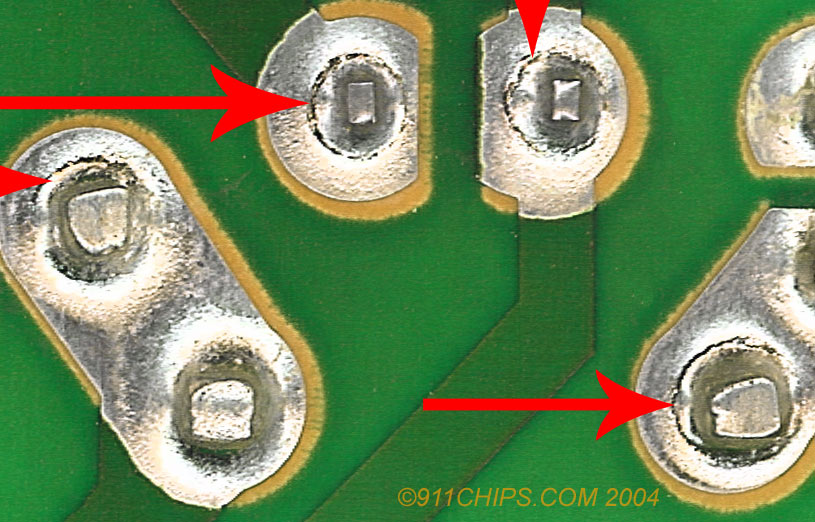
heat from thermal cycling causing re-crystallized into Sn and Pb separately, then fracturing.
Hi Djk,
nice pic!
What service conditions lead to this type of failure?
What steps should builders/designers take to avoid the problem?
nice pic!
What service conditions lead to this type of failure?
What steps should builders/designers take to avoid the problem?
Great pics ! nice work.
I saw same type of failure on circuits where heat dissipation is not present or almost not.
I was shure that the soldering process was the cause of the problem, but I suspect cooling process to be too quick so leaving too much stress in joint.
Do you agree or I am wrong ?
I saw same type of failure on circuits where heat dissipation is not present or almost not.
I was shure that the soldering process was the cause of the problem, but I suspect cooling process to be too quick so leaving too much stress in joint.
Do you agree or I am wrong ?
The first joint was simply overheated during soldering.
The second photo is actually of a high current relay, and looks close to what I have seen on TO-3 sockets on large PA amplifiers.
As to the other questions, I am going to try and talk to the guy in the lab that runs the SEM and does failure analysis of this stuff (hopefully later today).
When I see this I generally add fresh solder, then wick the joint dry, then re-solder with Ag/Pb/Sn, about %2~%4 on the Ag (silver).
The second photo is actually of a high current relay, and looks close to what I have seen on TO-3 sockets on large PA amplifiers.
As to the other questions, I am going to try and talk to the guy in the lab that runs the SEM and does failure analysis of this stuff (hopefully later today).
When I see this I generally add fresh solder, then wick the joint dry, then re-solder with Ag/Pb/Sn, about %2~%4 on the Ag (silver).
- Status
- Not open for further replies.
- Home
- Amplifiers
- Solid State
- Aging solder joins of power transistors