I built Jeff Bagby's Kairos in Baltic Birch. It is a great speaker, btw. But I did not follow his window bracing advice on cabinet construction and instead, I have a lot of corner braces of 3/4 x 3/4" BB sticks inside and some cross braces, making the max distance between braces <3", but the brace points are just a single point, not a beam. Above 300 it is pretty dead, the normal 400Hz BB ring is gone. But the LF is vibrating and distorting the sound. It must be some complex bending to get around all those braces, but there it is. I can feel some vibration on the sides when playing music. The audible resonance peak is at 220Hz. Below the resonance in the low bass it sounds a little cleaner.
I bought some heavy 18" true porcelain floor tiles to use as exterior stiffening or dampers. Each tile weighs 10+ pounds and rings high and long like a crystal goblet, very stiff, high Q. I intend to glue this onto the exterior surfaces of the speaker box on sides top and rear. I am hoping that the different resonant frequencies of the materials (BB and tile) will damp each other and the added stiffness of the tile will stop the LF ringing.
My question is about the adhesive to join them. Should I use PL polyurethane construction adhesive, which is super strong and rigid? Or should I use Green Glue which is soft but it's a true engineered damping material?
I have used green glue in this way before, laminating layers of MDF together on a planet10 Maiko2 where it worked very well with a couple staples at the edges to prevent sliding. Green Glue Company advised me that the BB will be able to absorb enough moisture to dry the green glue, but it might take a little longer than if it was 2 sheets of wood.
My question is should I think of this as a constrained layer damping situation to damp LF vibration, or should I look at it as a stiffening mod to raise the resonant freq of the cabinet to stop the LF vibes?
Thanks for any advice.
Rich
I bought some heavy 18" true porcelain floor tiles to use as exterior stiffening or dampers. Each tile weighs 10+ pounds and rings high and long like a crystal goblet, very stiff, high Q. I intend to glue this onto the exterior surfaces of the speaker box on sides top and rear. I am hoping that the different resonant frequencies of the materials (BB and tile) will damp each other and the added stiffness of the tile will stop the LF ringing.
My question is about the adhesive to join them. Should I use PL polyurethane construction adhesive, which is super strong and rigid? Or should I use Green Glue which is soft but it's a true engineered damping material?
I have used green glue in this way before, laminating layers of MDF together on a planet10 Maiko2 where it worked very well with a couple staples at the edges to prevent sliding. Green Glue Company advised me that the BB will be able to absorb enough moisture to dry the green glue, but it might take a little longer than if it was 2 sheets of wood.
My question is should I think of this as a constrained layer damping situation to damp LF vibration, or should I look at it as a stiffening mod to raise the resonant freq of the cabinet to stop the LF vibes?
Thanks for any advice.
Rich
If you haven't yet bought your drivers I suggest getting dual drivers in the bass in an opposed PP fashion. It would cancel almost all mechanical forces which is nice. If you are going sealed then you still have to worry about stiffening the box but at least vibration isn't a problem anymore =)
If you oppose one of the drivers you also get a massive distortion reduction too, which is even more nice.
If you oppose one of the drivers you also get a massive distortion reduction too, which is even more nice.
It's a good point about drying. With solid wood or MDF or sheetrock there is a lot of absorbent material to absorb the moisture. With BB ply, there is the surface wood layer 1.5mm thick then a glue layer which is probably waterproof, so all the moisture has to migrate through that thin top birch layer. Hmmm, thanks for the insight puppet. Anybody ever use GG with BB?
I don't want to invest a lot of money in this box, like buying special damping sheet material. I'd rather start from scratch with a vibration aware box design if GG won't work. on this one. This was the easy and cheap solution, but maybe not doable. The nice thing about PL is it cures with moisture, so no problem curing under the tile. But it isn't a true damper like GG.
Other ideas?
I don't want to invest a lot of money in this box, like buying special damping sheet material. I'd rather start from scratch with a vibration aware box design if GG won't work. on this one. This was the easy and cheap solution, but maybe not doable. The nice thing about PL is it cures with moisture, so no problem curing under the tile. But it isn't a true damper like GG.
Other ideas?
Adding bracing willy-nilly is a recipe for disaster, IMO.
You don't say if this is closed box or reflex which affects your options for dealing with standing waves which are quite distinct from cabinet resonances, but the 12mm thin birch plywood approach is really to avoid bracing and battening. You might get away with a plywood window brace, but really the trick is to LET the ply walls flex below 100Hz here. Then the rubberised/bitumenised sidepanels control everything cabinet related above that.
You are evidently using a thicker grade of ply than is strictly BBC, but that just means it resonates higher, perhaps to 200Hz. You can't make a decent cabinet by later adding mass to it, because you really aren't improving rigidity. Where the BBC used light beech battens, it was actually for strength, not rigidity.
Your cabinet is just plain muddled between two concepts here. The BBC concept is that the vibration can freely travel around the cabinet, and get damped everytime it passes the rubberised side, top and bottom panels. The cabinet is meant to flex. The removeable front panel in BBC designs is also a deliberate feature designed to be a "Cracked Bell" that doesn't ring.
http://www.diyaudio.com/forums/multi-way/223174-interesting-read-i-found-lossy-cabinet-designs-harbeth.html#post3234256
You don't say if this is closed box or reflex which affects your options for dealing with standing waves which are quite distinct from cabinet resonances, but the 12mm thin birch plywood approach is really to avoid bracing and battening. You might get away with a plywood window brace, but really the trick is to LET the ply walls flex below 100Hz here. Then the rubberised/bitumenised sidepanels control everything cabinet related above that.
You are evidently using a thicker grade of ply than is strictly BBC, but that just means it resonates higher, perhaps to 200Hz. You can't make a decent cabinet by later adding mass to it, because you really aren't improving rigidity. Where the BBC used light beech battens, it was actually for strength, not rigidity.
Your cabinet is just plain muddled between two concepts here. The BBC concept is that the vibration can freely travel around the cabinet, and get damped everytime it passes the rubberised side, top and bottom panels. The cabinet is meant to flex. The removeable front panel in BBC designs is also a deliberate feature designed to be a "Cracked Bell" that doesn't ring.
http://www.diyaudio.com/forums/multi-way/223174-interesting-read-i-found-lossy-cabinet-designs-harbeth.html#post3234256
Forget the nay sayers. Go with the green glue. I have experimented extensively with constrained layer damping and it is the best way to get really dead wall panels, I.e. to kill your resonances.
Although your tiles are heavy, you will have huge surface area for gluing and they won't fall off. At this point it is also an easy mod for you to do, so give it a try.
David
Although your tiles are heavy, you will have huge surface area for gluing and they won't fall off. At this point it is also an easy mod for you to do, so give it a try.
David
Thanks for the replies gents!
The speakers are sealed, Q~.65. The walls are vibrating, so it's not just cone retransmission. Porcelain tile is extremely stiff, gluing it to almost anything would add stiffness, but only with hard glue. Soft glue would not move the resonant freq, methinks.
I can tack 2 corners of each tile with a small dab of silicone to keep them from moving. I'll probably wrap the tile edges in wood anyway for decoration.
I'm mostly concerned whether the GG would actually dry with BB, or stay wet under the tile. I'll do some testing on scrap BB to see how water moves through it.
The speakers are sealed, Q~.65. The walls are vibrating, so it's not just cone retransmission. Porcelain tile is extremely stiff, gluing it to almost anything would add stiffness, but only with hard glue. Soft glue would not move the resonant freq, methinks.
I can tack 2 corners of each tile with a small dab of silicone to keep them from moving. I'll probably wrap the tile edges in wood anyway for decoration.
I'm mostly concerned whether the GG would actually dry with BB, or stay wet under the tile. I'll do some testing on scrap BB to see how water moves through it.
It'll stick very well with LN.Try Liquid Nails for Subfloors. It's cheap and damps well. Test to see if it sticks to tile first.
If you are trying to mitigate moisture loss Zinnser B*I*N to seal up the wood first.
With GG losing its moisture causing issue I question the long term stability?
I've used Sikaflex a one-component polyurethane-based, non-sag elastomeric sealant. It's a very strong adhesive yet it maintains a slightly flexible property indefinitely. It'll easily glue the tiles to the exterior of your cabinet while simultaneously adding constrained layer damping. It doesn't cure to be hard like Liquid Nails. It's available in slow or fast cure.
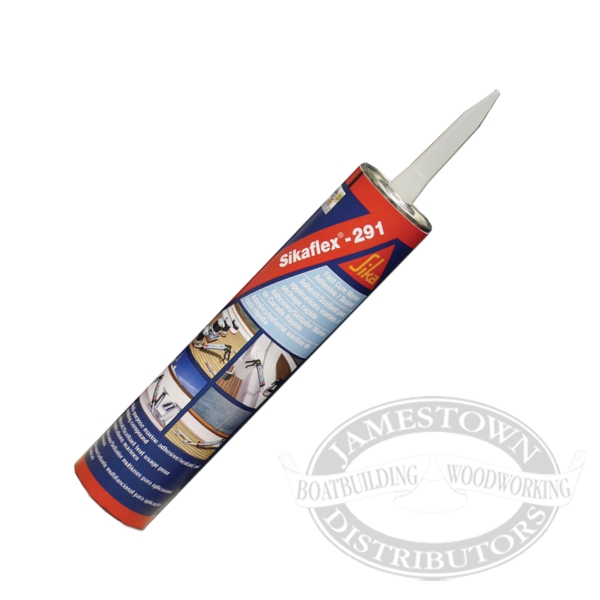
Last edited:
Well.... let's see the facts!Dave please stop with the facts! We thrive on opinions!
Constrained layers can be effective with a number of materials not just Green Glue.
Check out some of the high end speaker builders such as Vandersteen for their use of CLD. Sand is effective too.
The only reason I brought it up ... the apparent knock against green glue ... was because it won't hold the tile. Contrary to the name, it's not glue. It's damping material.
Maybe the OP can use the silicone in the corners and the GG everywhere else. GG Inc. doesn't recommend using liquid nails as it gets too hard and links both layers to acoustic vibration. (a damping short circuit)
Maybe the OP can use the silicone in the corners and the GG everywhere else. GG Inc. doesn't recommend using liquid nails as it gets too hard and links both layers to acoustic vibration. (a damping short circuit)
Last edited:
Thanks rajacat, I'll check that out. Boaters get all the cool chems!
I don't know about Vandersteen, but Von Schweikert uses CL construction in their speakers now. MDF outer shell then sheet polymer damping material then quartz countertop material, all glued together, probably with solvent contact cement. The damping layer is ~6mm iirc?
A Whitepaper: The Audibility Of Cabinet Panel Resonances and Pat. Pend. Method Of Reduction Of Audible Coloration | Dagogo | A Unique Audiophile Experience
GG would be my first choice if I can be convinced it will dry under the tile. Should I drill some 1/4" thru holes to allow air up to the GG layer from inside the speaker? Should I just not worry about it?
I don't know about Vandersteen, but Von Schweikert uses CL construction in their speakers now. MDF outer shell then sheet polymer damping material then quartz countertop material, all glued together, probably with solvent contact cement. The damping layer is ~6mm iirc?
A Whitepaper: The Audibility Of Cabinet Panel Resonances and Pat. Pend. Method Of Reduction Of Audible Coloration | Dagogo | A Unique Audiophile Experience
GG would be my first choice if I can be convinced it will dry under the tile. Should I drill some 1/4" thru holes to allow air up to the GG layer from inside the speaker? Should I just not worry about it?
Recomendation
If the bond, ceramic tile to wood, is resilient, you will lower wall resonant frequencies due to the predominating mass increase. If the bond is stiff (non-resilient) instead, the bond will undergo fatigue stress due to the movement of the underlying wood caused by vibration and the effects of seasonal humidity changes. If you want a tile finish, use lightweight concrete as the substrate. For the existing wood enclosures, use a thin concrete wallboard first with a resilient bond. Then bond the tile to that using a thin-set mortar. The use of mesh mounted mosaic tile can deliver a unique visual effect to your enclosures.
The first mode of panel resonance will be across corners. Bracing placed at the diagonals will kill that mode.
Regards,
WHG
If the bond, ceramic tile to wood, is resilient, you will lower wall resonant frequencies due to the predominating mass increase. If the bond is stiff (non-resilient) instead, the bond will undergo fatigue stress due to the movement of the underlying wood caused by vibration and the effects of seasonal humidity changes. If you want a tile finish, use lightweight concrete as the substrate. For the existing wood enclosures, use a thin concrete wallboard first with a resilient bond. Then bond the tile to that using a thin-set mortar. The use of mesh mounted mosaic tile can deliver a unique visual effect to your enclosures.
The first mode of panel resonance will be across corners. Bracing placed at the diagonals will kill that mode.
Regards,
WHG
Good points WHG, thanks.
I think the construction adhesives mentioned here are recommended by mfg for gluing wood to masonry outside. I guess they are just vouching for adhesion success, not the tensile stress resistance of the masonry... All the broken bits of masonry will stay stuck to the wood.
The first mode is diagonal because that is the longest linear dimension?
I think the construction adhesives mentioned here are recommended by mfg for gluing wood to masonry outside. I guess they are just vouching for adhesion success, not the tensile stress resistance of the masonry... All the broken bits of masonry will stay stuck to the wood.
The first mode is diagonal because that is the longest linear dimension?
Last edited:
Thanks rajacat, I'll check that out. Boaters get all the cool chems!
I don't know about Vandersteen, but Von Schweikert uses CL construction in their speakers now. MDF outer shell then sheet polymer damping material then quartz countertop material, all glued together, probably with solvent contact cement. The damping layer is ~6mm iirc?
A Whitepaper: The Audibility Of Cabinet Panel Resonances and Pat. Pend. Method Of Reduction Of Audible Coloration | Dagogo | A Unique Audiophile Experience
GG would be my first choice if I can be convinced it will dry under the tile. Should I drill some 1/4" thru holes to allow air up to the GG layer from inside the speaker? Should I just not worry about it?
My mistake.
- Home
- Loudspeakers
- Multi-Way
- Constrained layer damping adhesive