I have a Philips 212 turntable that I bought new in the 70’s. Now, 40 years later, it has developed all the well known controller ailments, so I’ve decided to gut the control board and convert it to Arduino control for the touch buttons and motor. I want to retain all the original functions but I don’t know what the adjustment range of the fine-tune speed knobs should be. What normal? +/-2% ?
Most older turntables used a synchronous motor and the speed was dictated by the frequency of the mains supply, which was held within a very close tolerance. A lot closer than most turntables using an electronic loop system.
Specifications
Drive method: belt drive
Speed control: electronic
Speeds: 33 and 45rpm
Speed adjustment range: +-3%
Wow and flutter: 0.1%
Rumble: 62dB
Arm friction: 15 mgf
Stylus force: 0.75 to 4g
Specifications
Drive method: belt drive
Speed control: electronic
Speeds: 33 and 45rpm
Speed adjustment range: +-3%
Wow and flutter: 0.1%
Rumble: 62dB
Arm friction: 15 mgf
Stylus force: 0.75 to 4g
Thanks for the specs. +/-3% is the number I’m looking for. The 212 definitely has a DC motor with a feedback loop, so I can’t change to synchronous.
Out of curiosity, in a turntable with synchronous drive licked to the line frequency, how is +/-3% adjustment implemented?
Usually by having a tapered motor shaft - see Dual 10/12xx models.
Hi wiseoldtech
Do you work in turntables?
I have a old Sansui RF2060 and I have the same speed problems with it
Do you know if it works the same as this guys Philips table? I’ve done all the things people have said. Clean the pulley. Maybe it has the 50hz pulley instead of the 60hz
Well it has both with it and I tried both of the
When I cleaned the 60hz pulley that was on the motor it all of sudden start to work at the right speed, well at lest for 3 or 4 LP’s and then the speed dropped down to 23/25 rpm
How do check the motor or the power supply system? I have a scope and I’m a somewhat newbie with it
Any help would be great
Thanks
Carl
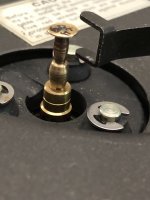
Do you work in turntables?
I have a old Sansui RF2060 and I have the same speed problems with it
Do you know if it works the same as this guys Philips table? I’ve done all the things people have said. Clean the pulley. Maybe it has the 50hz pulley instead of the 60hz
Well it has both with it and I tried both of the
When I cleaned the 60hz pulley that was on the motor it all of sudden start to work at the right speed, well at lest for 3 or 4 LP’s and then the speed dropped down to 23/25 rpm
How do check the motor or the power supply system? I have a scope and I’m a somewhat newbie with it
Any help would be great
Thanks
Carl
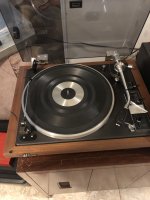
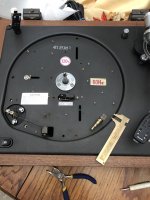
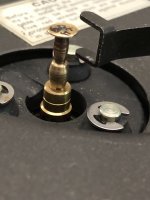
I will have to check that. If I remember, it did have some resistance to it. It’s not like if I was to spin in with my fingers it would just free spin
Those motors require a teardown and thorough soaking/flushing of the bronze sintered bearings - sometimes a repeat is needed.
ALL of that old gummy oil needs to be removed.
The tip of a clean soldering iron in the bearing makes the gummy oil boil out - then must be flushed quickly away.
Afterwards, the bearing has to be saturated with fresh "Zoom Spout" turbine oil including any felt oil retainers.
It's the only way.
Once reassembled and the bearings centered, a quick twist of the shaft will make it spin down, and then "rock" back and forth to a stop as the rotor magnet locks it.
Been there done that, hundreds of times for customer service.
^^ Exactly.
Old turntable motors with 'oilite' bearings (porous bronze) dry out and gum up. Same with the platter bearings.
Get a drop of oil (any light oil is fine, even motor oil, which has the advantage of high surface energy, meaning it wants to move around a lot) and get the bearings oiled. See if things free up. They most likely will, but it's a temporary fix, you need to remove them and re-oil.
The best way to do it, that will last another 40yr, is either, 1) submerge them in a pool of oil and place in a toaster oven and heat to about 250F for 20-30 min, or 2) submerge them in a jar of oil and evacuate the air above for 20-30min or until bubbles stop. (Vacuum pump of some kind, brake bleeder, canning jar, etc...)
Old turntable motors with 'oilite' bearings (porous bronze) dry out and gum up. Same with the platter bearings.
Get a drop of oil (any light oil is fine, even motor oil, which has the advantage of high surface energy, meaning it wants to move around a lot) and get the bearings oiled. See if things free up. They most likely will, but it's a temporary fix, you need to remove them and re-oil.
The best way to do it, that will last another 40yr, is either, 1) submerge them in a pool of oil and place in a toaster oven and heat to about 250F for 20-30 min, or 2) submerge them in a jar of oil and evacuate the air above for 20-30min or until bubbles stop. (Vacuum pump of some kind, brake bleeder, canning jar, etc...)
^^ Exactly.
Old turntable motors with 'oilite' bearings (porous bronze) dry out and gum up. Same with the platter bearings.
Get a drop of oil (any light oil is fine, even motor oil, which has the advantage of high surface energy, meaning it wants to move around a lot) and get the bearings oiled. See if things free up. They most likely will, but it's a temporary fix, you need to remove them and re-oil.
The best way to do it, that will last another 40yr, is either, 1) submerge them in a pool of oil and place in a toaster oven and heat to about 250F for 20-30 min, or 2) submerge them in a jar of oil and evacuate the air above for 20-30min or until bubbles stop. (Vacuum pump of some kind, brake bleeder, canning jar, etc...)
The trouble is, once the old oil gets gummed up, I've found that the only way to completely remove it from the pores of the bearings is to use the soldering iron method that I mentioned.
A clean, preferrably new iron tip (that I only use for this procedure) inserted carefully into the bearing center heats it quickly and causes all that gummy oil to actually boil right out in a few seconds.
While on the tip, use the iron on a cloth pad to wipe repeatedly until no more bubbles out of the bearing.
Let the bearing cool down by slipping it off the iron tip into a fresh oil bath.
Repeat again.
This insures that the pores will soak up and "wick" the new oil as it cools.
I've done this procedure many times for "old vintage motors" and have never seen it published anywhere, yet it's common sense and works.
- Status
- This old topic is closed. If you want to reopen this topic, contact a moderator using the "Report Post" button.
- Home
- Source & Line
- Analogue Source
- Proper turntable speed adjust range?