Dear All.... I do not know much about ss, tubes or audio in general. Just an amateur builder who is eager and happy to learn from thos who know and are willing to share.
I do however have some extensive experience in alternative methods of cooling especially in the area of PC, overclocking and benchtesting.
I would like to open a thread and submit some ideas I have (some currenly under testing) to alternatively cool large and powerful amps (like pure A pass amplifiers).
These are the main techniques I have tried with PCs
1. watercooling
2. TEC (peltier modules which need extensive and additional cooling)
3. Phase change
Computer cooling - Wikipedia, the free encyclopedia
Some of these techniques have obvious downsides. Phase change for example is extreme (multiple stages can achieve almost absolute 0 temperatures) and are bound to create interference both on the main lines, around the compressors.
However Liquid cooling, I believe, can effectively be used to help keep size, weight, cost and temeprature at bay.
Watercooling is based on the simple yet effective idea that water is used to transfer heat from the source to radiators which are designed and operate in conjuntion with fans (even undervolted) to eliminate heat.
The system usually works by using small electric 12v pumps which can be extremely effective, low noise, low power and still keep a good flow rate.
In some casewatercooling can yield asonshing results. I have personally rigged 2 audi tt radiators to passively cool an extremely overclocked CPU (putting out heaps of heat)
The heat is generate by a very small die which can put out several hundreds of watts of heat
(my e6600 with the HIS removed)
Now the essential part of the system is the waterblock.
This can bel made out in several shapes, sizes and materials. Obviousl specific designs are required for high efficiency systems which have to achiev tremendous performance in small packages.
For example this a modern waterblock:
however blocks can be much simpler....infact they can be as simple as this:
or even simpler...
right now I am experimenting with simple rectangular extrusions of pure copper wich will be interposed between an ordinary finned heatsink (like the ones we normally use in audio) and the common heatspreader of a generic array of devices
The extrsuion would behave as a simple channel for flowing water, offer almost no resistance and yet help to divert most of the heat to radiators possibily mounted on top or at the bottom of a chassis.
Imagine radiators like this:
In essence I am exploring the possibility of using watercooling as an effective way to deal with increasing power consumptions, costs and weight which for some of us can and do present serious problems.
If you have any thought on the matter please post here..
I will keep you updated with diagrams, photos of my work etc.
🙂
I do however have some extensive experience in alternative methods of cooling especially in the area of PC, overclocking and benchtesting.
I would like to open a thread and submit some ideas I have (some currenly under testing) to alternatively cool large and powerful amps (like pure A pass amplifiers).
These are the main techniques I have tried with PCs
1. watercooling
2. TEC (peltier modules which need extensive and additional cooling)
3. Phase change
Computer cooling - Wikipedia, the free encyclopedia
Some of these techniques have obvious downsides. Phase change for example is extreme (multiple stages can achieve almost absolute 0 temperatures) and are bound to create interference both on the main lines, around the compressors.
However Liquid cooling, I believe, can effectively be used to help keep size, weight, cost and temeprature at bay.
Watercooling is based on the simple yet effective idea that water is used to transfer heat from the source to radiators which are designed and operate in conjuntion with fans (even undervolted) to eliminate heat.
The system usually works by using small electric 12v pumps which can be extremely effective, low noise, low power and still keep a good flow rate.
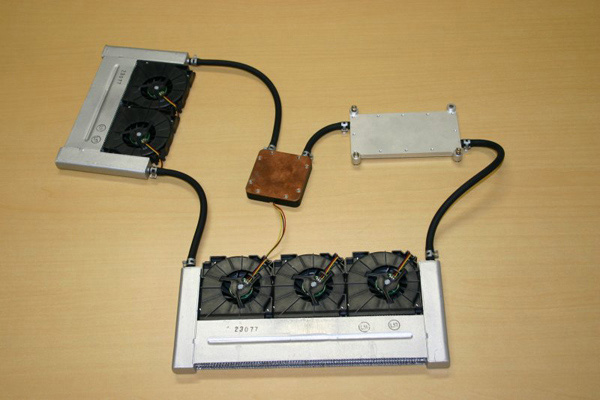
An externally hosted image should be here but it was not working when we last tested it.
In some casewatercooling can yield asonshing results. I have personally rigged 2 audi tt radiators to passively cool an extremely overclocked CPU (putting out heaps of heat)
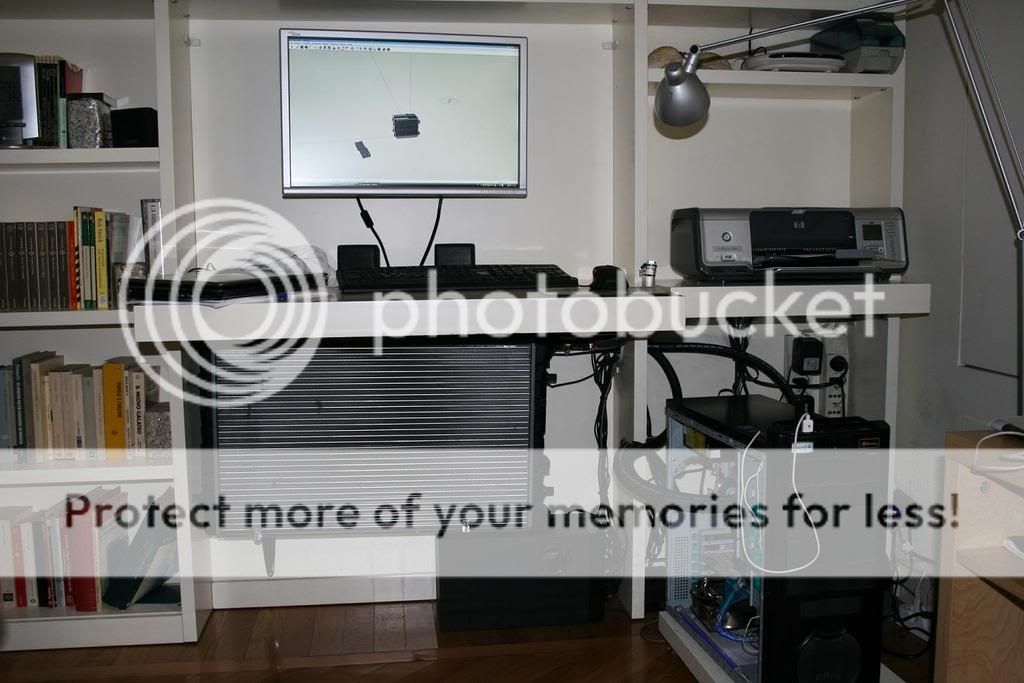
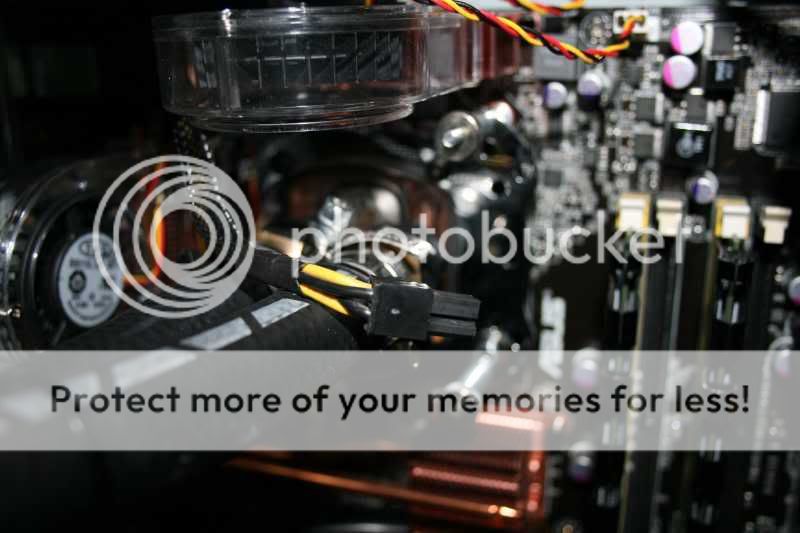
The heat is generate by a very small die which can put out several hundreds of watts of heat
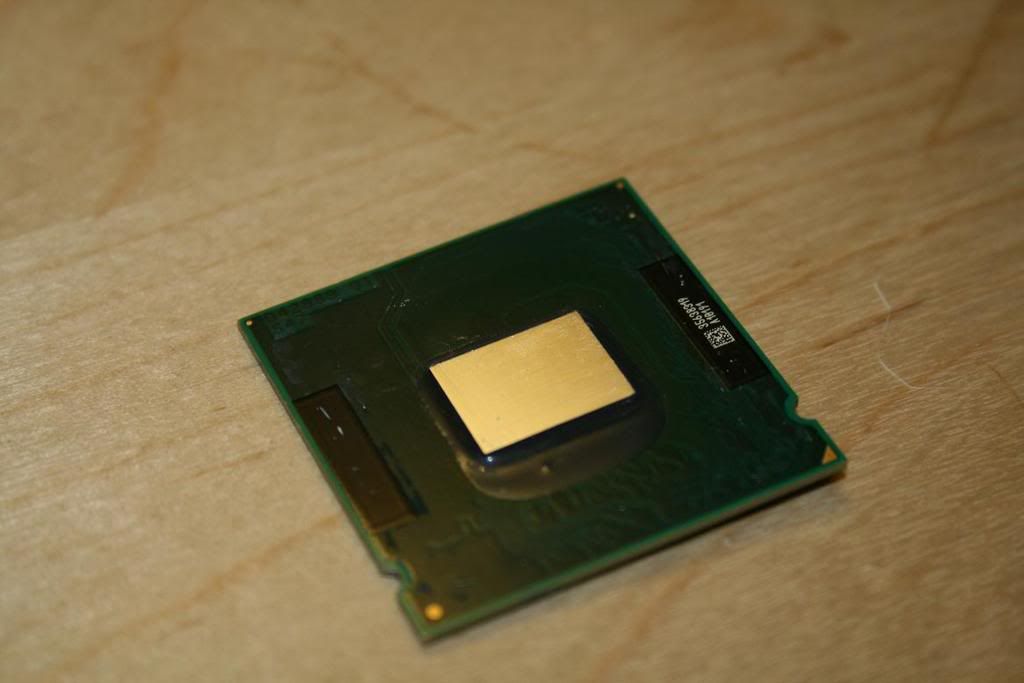
Now the essential part of the system is the waterblock.
This can bel made out in several shapes, sizes and materials. Obviousl specific designs are required for high efficiency systems which have to achiev tremendous performance in small packages.
For example this a modern waterblock:
An externally hosted image should be here but it was not working when we last tested it.

however blocks can be much simpler....infact they can be as simple as this:
An externally hosted image should be here but it was not working when we last tested it.
or even simpler...
right now I am experimenting with simple rectangular extrusions of pure copper wich will be interposed between an ordinary finned heatsink (like the ones we normally use in audio) and the common heatspreader of a generic array of devices
An externally hosted image should be here but it was not working when we last tested it.
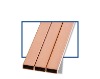
The extrsuion would behave as a simple channel for flowing water, offer almost no resistance and yet help to divert most of the heat to radiators possibily mounted on top or at the bottom of a chassis.
Imagine radiators like this:
An externally hosted image should be here but it was not working when we last tested it.
In essence I am exploring the possibility of using watercooling as an effective way to deal with increasing power consumptions, costs and weight which for some of us can and do present serious problems.
If you have any thought on the matter please post here..
I will keep you updated with diagrams, photos of my work etc.
🙂
Last edited:
I forgot to mention that a 12v pump can be regulated thermically to provide stable tempertures under the most extreme situations. In turn temperature stability would provide longer component life, stable output figures and a more predictable device behaviour.
Obviously the amps can be made smaller in dimensions and still provide room and cooling capacity for large amplifier modules.
Obviously the amps can be made smaller in dimensions and still provide room and cooling capacity for large amplifier modules.
Here is what I am doing...
I believe this could be an effective design given that we would not be seeking low temperatures rather reducing the amount of heat exchanged by the ordinary finned heatsink.
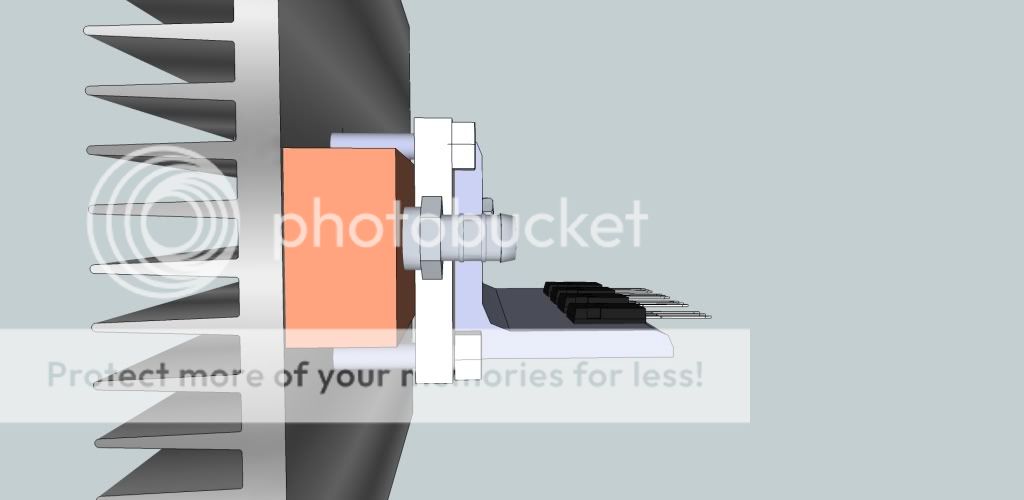
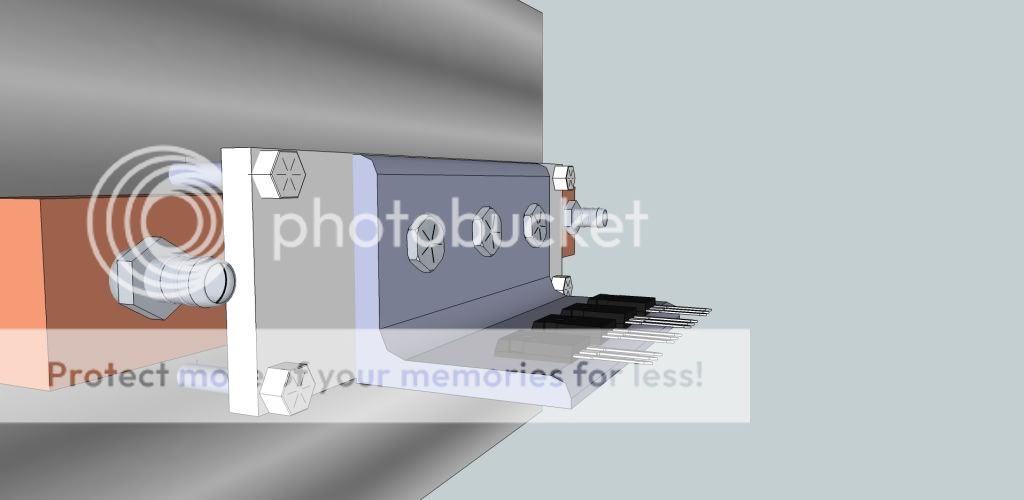
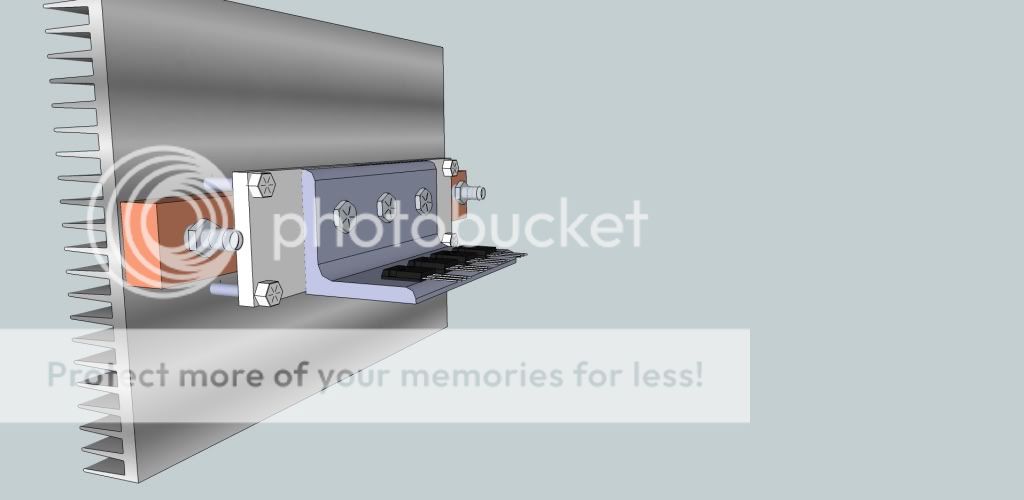
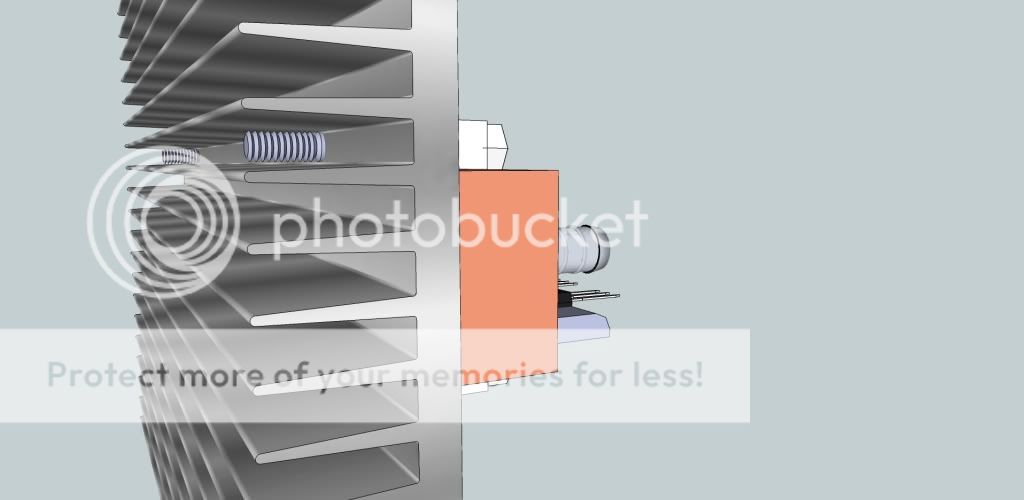
I believe this could be an effective design given that we would not be seeking low temperatures rather reducing the amount of heat exchanged by the ordinary finned heatsink.
Can you not clamp the copper tube with the angle aluminum directly, so that you can bypass the aluminum bar? Or rather, get rid of the angle and keep the bar, but drill/tap it so that you can screw the chips into it. I see some ways you can reduce the thermal resistance there... Also, if you set up the loop properly, there will be no need for those fins.
Water cooling is definitely a solution more people need to explore, though.
Water cooling is definitely a solution more people need to explore, though.
Once you go through the complexity and expense of a water system one of the offsetting features is the lack of need for convection cooling at all. Unless you are looking for failsafe protection, added convection cooling is a waste. It just makes it bulkier and more expensive.
As previously mentioned , you want the dissipation to be as close to the water as possible. Get rid of any additional interfaces if possible, especially angles or tabs that force conduction through a thin length of material.
As previously mentioned , you want the dissipation to be as close to the water as possible. Get rid of any additional interfaces if possible, especially angles or tabs that force conduction through a thin length of material.
Drilling on a pipelike structure is tricky and I would not do it unless an alternative is actually impossible...
However take into account the fact that low temperatures are not what we are looking for...infact we have two opposing objectives. Keep the temperatures high enough for optimal output (the multiple surfaces will actually work towards such a goal by providing a suboptimal situation for heat transfer) and obviously we seek some form of cooling which will be provided by the moving water. Also once the water temperature stabilizes the temperature itself will be regulated by the speed of the fans..
Other pics to show the rest of the project:
However take into account the fact that low temperatures are not what we are looking for...infact we have two opposing objectives. Keep the temperatures high enough for optimal output (the multiple surfaces will actually work towards such a goal by providing a suboptimal situation for heat transfer) and obviously we seek some form of cooling which will be provided by the moving water. Also once the water temperature stabilizes the temperature itself will be regulated by the speed of the fans..
Other pics to show the rest of the project:
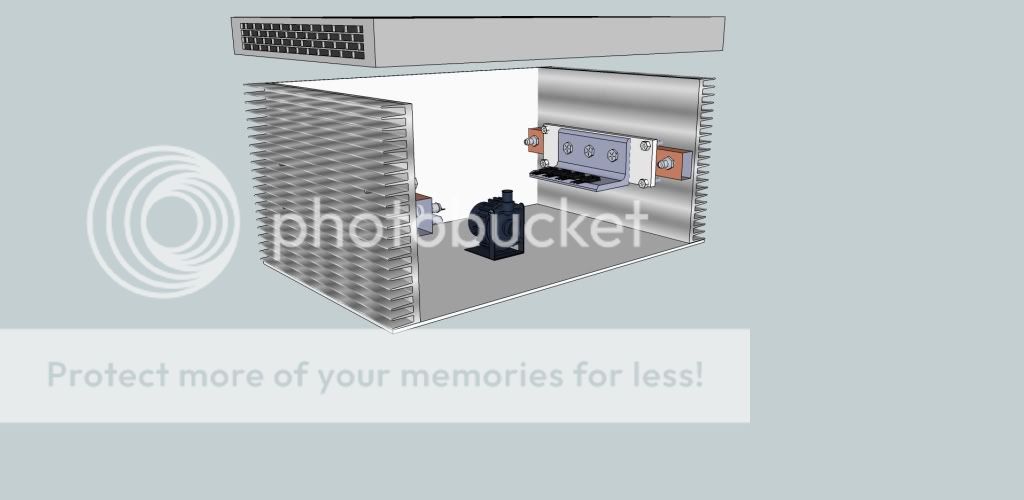
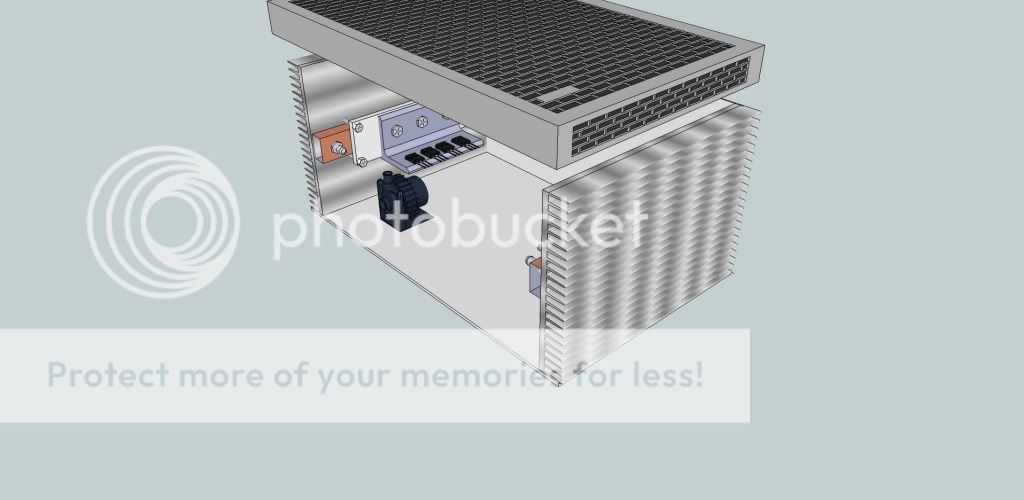
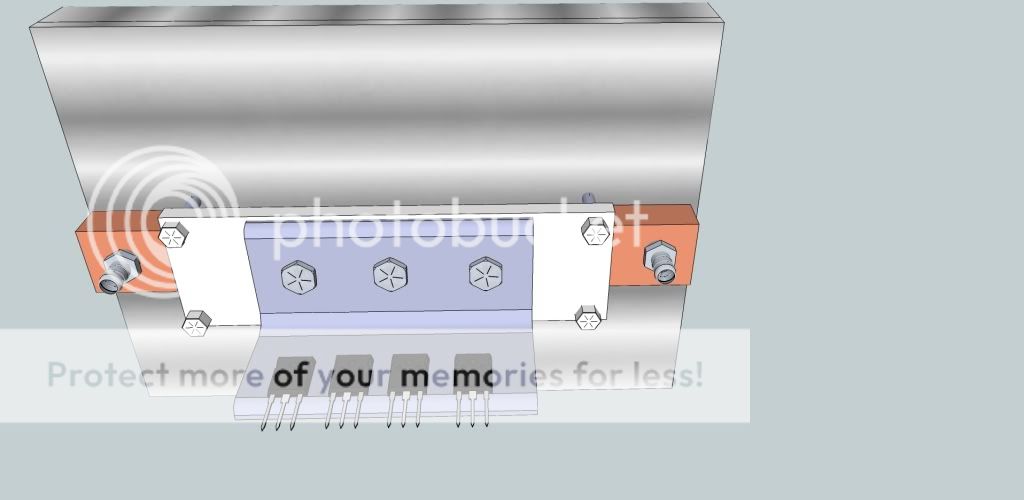
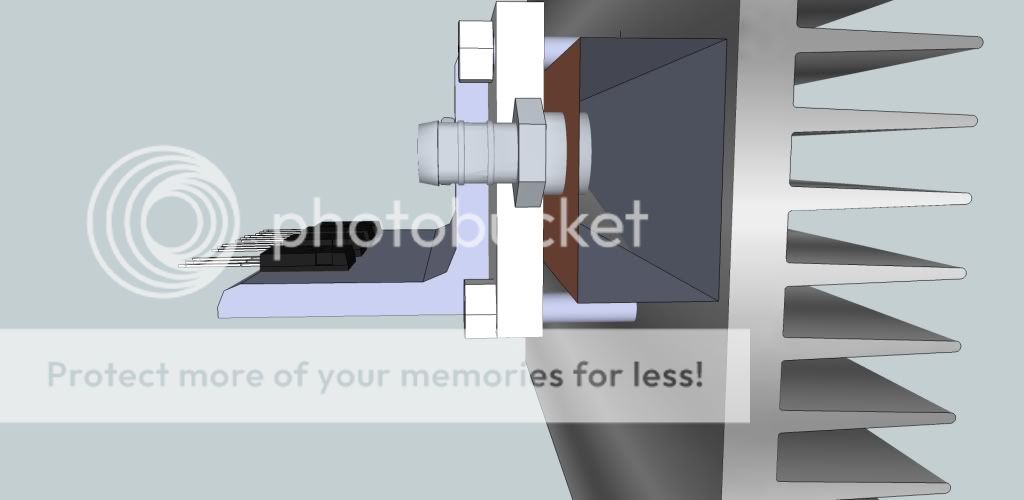
Once you go through the complexity and expense of a water system one of the offsetting features is the lack of need for convection cooling at all. Unless you are looking for failsafe protection, added convection cooling is a waste. It just makes it bulkier and more expensive.
As previously mentioned , you want the dissipation to be as close to the water as possible. Get rid of any additional interfaces if possible, especially angles or tabs that force conduction through a thin length of material.
I was actually thinking of a failsafe. In case waterpumps stop the water inside will act as a conductive core (a pretty good one)
So in essence some time will be pass before the underdimensioned convection heatsinks will fail and temperatures begin rising beyond tollerable levels.
I agree that less is better however dilling inside a tube structure is just not feasable.
I could look into this:
http://www.aavidthermalloy.com/site...pdf/liquid-cold-plate-datasheet-hicontact.pdf
but really it would be less flexibile than just using extrusions cut to requirements.
Of course one could rig a flowmeter to powerdown the amp if flow goes under a specific value. Shouldn't be too hard!
can the four devices be clamped direct to the water pipe/tube by the bolted on clamp plate?
This dispenses with the angle completely.
Another clamp plate instead of the heatsink and one could clamp up twice as many devices with the leads just the thickness of the water tube apart (+3mm).
The usual temp switch on the sink to power down on overtemperature, with or without a latch.
This dispenses with the angle completely.
Another clamp plate instead of the heatsink and one could clamp up twice as many devices with the leads just the thickness of the water tube apart (+3mm).
The usual temp switch on the sink to power down on overtemperature, with or without a latch.
Yes Andrew infact I was just working on this option... thanks for spotting this out! 😉
This is a small rendering of what the case could look like once we reduce the dimensions to the bare minimum....
This is a small rendering of what the case could look like once we reduce the dimensions to the bare minimum....
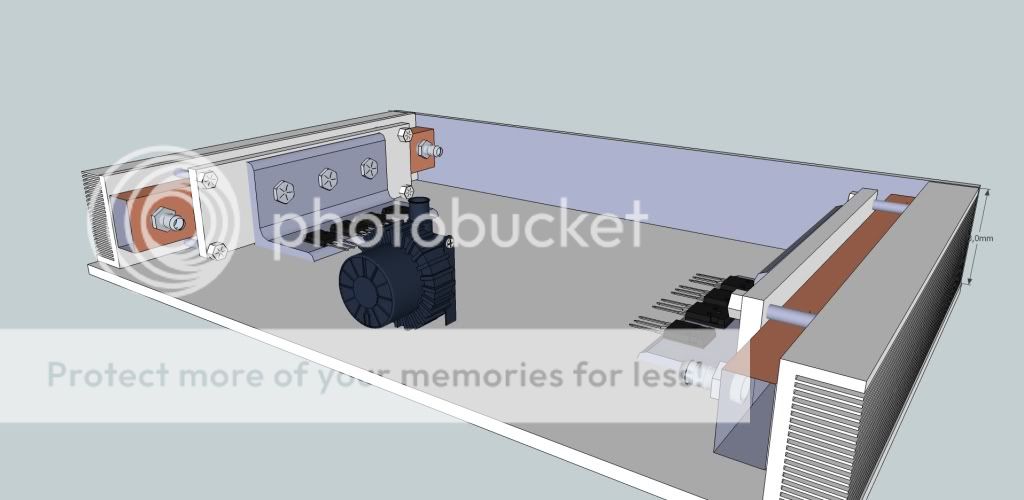
I am not sure you completely understood what I meant in my last post; none of my suggestions involve actually drilling into the water conduit. Also, there is never any reason to keep the temperature above what is reasonably achievable as a minimum.
Is this it?
If it is then I understood you correctly the first time..
Mr Pass states in all his Aleph manual that best performance is achieved after the temperature reaches a specific level and is "stable". This can take up to an hour in the biggest builds (like aleph 1.2 ecc)
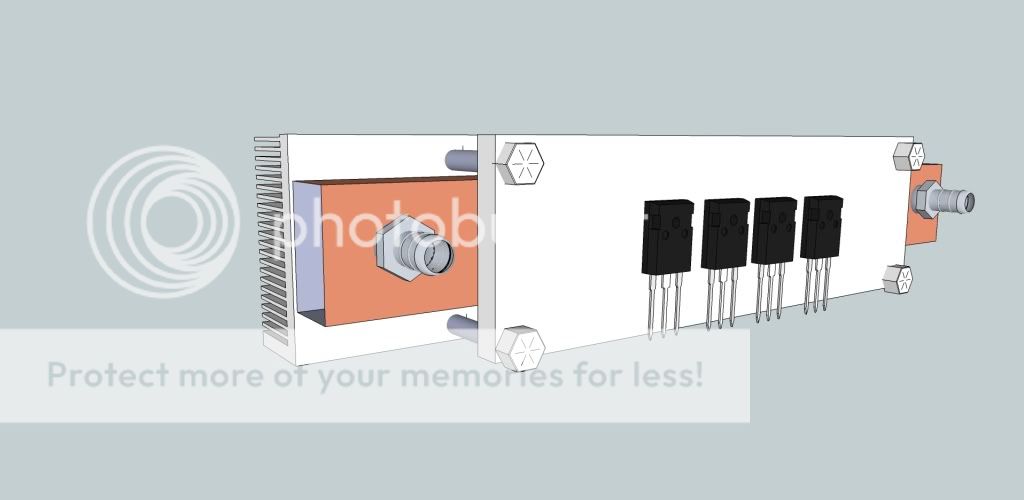
If it is then I understood you correctly the first time..
Mr Pass states in all his Aleph manual that best performance is achieved after the temperature reaches a specific level and is "stable". This can take up to an hour in the biggest builds (like aleph 1.2 ecc)
the bottom or top casing could be made out of this sort of radiators...
http://img28.imageshack.us/img28/9623/005fzq.jpg
those are 38mm fans but 19mm fans would just as well.. the system would still be quiet and yet provide excellent cooling even with a stereo aleph 1.2 unit.
http://img28.imageshack.us/img28/9623/005fzq.jpg
those are 38mm fans but 19mm fans would just as well.. the system would still be quiet and yet provide excellent cooling even with a stereo aleph 1.2 unit.
IMHO it's a good idea but I like my amps silent, not quiet but 0 noise from them. My other hobby is watercooling and modding comps but that stays with comps. Noisy complex case builds stay with comps silent elegant and simple stays in audio for me!
May latest amp build, will be three Wire amps at 300W a channel. (only want that power for dynamic peaks not continuous before you get on my back andrewt for the size of my sinks!). Home made of course!
May latest amp build, will be three Wire amps at 300W a channel. (only want that power for dynamic peaks not continuous before you get on my back andrewt for the size of my sinks!). Home made of course!

Last edited:
I understand your point of view. However if you have built watercooling systems with undervolted pumps and fans you must know that it gets pretty close to silent if all parts are well chosen and matched.
In some setups a radiator with adequate surface area and positioned horizontally may actually achieve a great deal. Add a single 12v fan underpowered to 6v to slightly force air movement and temperatures would drop greatly.
In my previous setup my cpu was happy at 40°C with only passive radiators (1.6v overclocked e6600). Once you turned fans on (just a couple under the large radiators) anche the temperatures would rop to a Delta of 5°C over ambient.
However I like simple things...but sometimes simple means very expensive and watercooling can (moderately) help in that department.
In some setups a radiator with adequate surface area and positioned horizontally may actually achieve a great deal. Add a single 12v fan underpowered to 6v to slightly force air movement and temperatures would drop greatly.
In my previous setup my cpu was happy at 40°C with only passive radiators (1.6v overclocked e6600). Once you turned fans on (just a couple under the large radiators) anche the temperatures would rop to a Delta of 5°C over ambient.
However I like simple things...but sometimes simple means very expensive and watercooling can (moderately) help in that department.
if you have built watercooling systems with undervolted pumps and fans you must know that it gets pretty close to silent.
.
My personal experience: I owned a pair of Krell KMA100 100W Class A monoblocks which use a small fan driven at a reduced voltage(fig. 1). To avoid any direct sound path to the listener the fan is horizontal and very close to the floor. The KMA100's are very sweet sounding high powered amps that proved to me that GREAT audio was possible. BUT...BUT...BUT... I COULD ALWAYS HEAR THE FANs, even when they were 20 feet from my ears. Because of fan noise I had to sell the musical KMA100s and bought Krell KSA250 passive cooled amps as a replacement. The treble on the KSA250 was a little harsher than the KMA100, but NO FAN NOISE was more important to me. When the KMA100's were idling between CD's my wife would often say, "what's that noise?...is that on the recording?" I will never own an amplifier with a fan or a water pump. For DIY, there are excellent passive solutions.
Heat sinks like the KL-271 profile can provide under 0.25 C/watt. It helps cooling to also use a large aluminum bar across the backside of all transistors to both provide even pressure against the heatsink, and also a second cooling sink.
My real DIY audio education came when I started to build 95db/watt 3-way speakers. I think this higher level of efficiency offers dynamics and details that are impossible from normal 85db/watt speakers, and SPL linearity without funky breakup or horn honk that 100+ db/watt speaker drivers typically generate. With tri-amping, each low wattage amp is easy to convection cool.
Attachments
I know it is hard to believe, but there are fans out there pumping out 30+ CFM that cannot be heard outside of 1-2 feet away.My personal experience: I owned a pair of Krell KMA100 100W Class A monoblocks which use a small fan driven at a reduced voltage(fig. 1). To avoid any direct sound path to the listener the fan is horizontal and very close to the floor. The KMA100's are very sweet sounding high powered amps that proved to me that GREAT audio was possible. BUT...BUT...BUT... I COULD ALWAYS HEAR THE FANs, even when they were 20 feet from my ears. Because of fan noise I had to sell the musical KMA100s and bought Krell KSA250 passive cooled amps as a replacement. The treble on the KSA250 was a little harsher than the KMA100, but NO FAN NOISE was more important to me. When the KMA100's were idling between CD's my wife would often say, "what's that noise?...is that on the recording?" I will never own an amplifier with a fan or a water pump. For DIY, there are excellent passive solutions.
Heat sinks like the KL-271 profile can provide under 0.25 C/watt. It helps cooling to also use a large aluminum bar across the backside of all transistors to both provide even pressure against the heatsink, and also a second cooling sink.
My real DIY audio education came when I started to build 95db/watt 3-way speakers. I think this higher level of efficiency offers dynamics and details that are impossible from normal 85db/watt speakers, and SPL linearity without funky breakup or horn honk that 100+ db/watt speaker drivers typically generate. With tri-amping, each low wattage amp is easy to convection cool.
wouldn't it be more efficient (heatwise) to just bolt the trannies to the heatsink bypassing all that other metalwork? It is easily done, I have done it and I have seen full production amplifiers use this method.
- Status
- Not open for further replies.
- Home
- Design & Build
- Construction Tips
- Some thoughts on alternative cooling