I'm looking for another port configuration for my tall 4 way cabinets w/ integrated subwoofers. I'm interested in making 2 ports that run vertically in a tall speaker cabinet, and exit out the sides of the cabinet with a flare somewhat resembling a NACA duct.
For reference, the speaker cabinet is 16"x 16"x 52". The subwoofer cavity is an "L" shape, allowing for a long and straight port. If I can figure out how to design it!
I already did a prototype with dual vertical ports positioned on either side of the sub driver. They exited out a notch in the bottom back corner of the cabinet. It worked well enough. But there is some audible distortion/ noise from the enclosed port exit.
I would like to improve on the same concept, with the ports running vertically in the tall cabinet section, but then venting them out to either side. (I have also thought about a vertical slot port against the back panel, that would exit right above the rear facing woofer...)
I haven't actually made these designs yet because I'm unsure about how to find the effective length and the end correction factor.
Photo of the concept:
![2025-03-14 16_20_35-Rhino 7 Commercial - [Top].jpg 2025-03-14 16_20_35-Rhino 7 Commercial - [Top].jpg](https://www.diyaudio.com/community/data/attachments/1343/1343123-c157b9074acd1be31f6f77d3b3cd8fa1.jpg?hash=wNBTB7vW5K)
I'm curious if anyone has tried something like this? I'm looking for a theory to calculate the "effective" length of such a port. Of course I will have to do some prototyping, but it would be good to start with an educated guess?
The drawing below is the speaker as designed with a 10" subwoofer driver. I built this one and used a curved port that fit neatly around the 10" driver. But it will be difficult to re-use the same curved port with the 12" subwoofer. Before I build molds to make a new curved port, I'd like to investigate the possibility of a simpler straight port...with a complicated port exit/ flare!
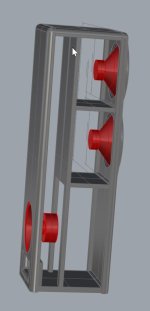
For reference, the speaker cabinet is 16"x 16"x 52". The subwoofer cavity is an "L" shape, allowing for a long and straight port. If I can figure out how to design it!
I already did a prototype with dual vertical ports positioned on either side of the sub driver. They exited out a notch in the bottom back corner of the cabinet. It worked well enough. But there is some audible distortion/ noise from the enclosed port exit.
I would like to improve on the same concept, with the ports running vertically in the tall cabinet section, but then venting them out to either side. (I have also thought about a vertical slot port against the back panel, that would exit right above the rear facing woofer...)
I haven't actually made these designs yet because I'm unsure about how to find the effective length and the end correction factor.
Photo of the concept:
![2025-03-14 16_20_35-Rhino 7 Commercial - [Top].jpg 2025-03-14 16_20_35-Rhino 7 Commercial - [Top].jpg](https://www.diyaudio.com/community/data/attachments/1343/1343123-c157b9074acd1be31f6f77d3b3cd8fa1.jpg?hash=wNBTB7vW5K)
I'm curious if anyone has tried something like this? I'm looking for a theory to calculate the "effective" length of such a port. Of course I will have to do some prototyping, but it would be good to start with an educated guess?
The drawing below is the speaker as designed with a 10" subwoofer driver. I built this one and used a curved port that fit neatly around the 10" driver. But it will be difficult to re-use the same curved port with the 12" subwoofer. Before I build molds to make a new curved port, I'd like to investigate the possibility of a simpler straight port...with a complicated port exit/ flare!
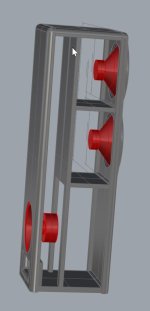
I have always made the ports adjustable after the fact to adjust as needed. Don't all the box design programs have an end correction formula?
Yes, they correct for an outward flare, for a port that exits perpendicular to the cabinet wall.Don't all the box design programs have an end correction formula?
But in the sketch above, the port is parallel to the cabinet wall, and the flare re-directs it outward. So it seems very different to me!
The proposed design might generate significant turbulence in the region circled in red. The air in the duct needs to change direction very significantly in that region.I'm looking for another port configuration for my tall 4 way cabinets w/ integrated subwoofers. I'm interested in making 2 ports that run vertically in a tall speaker cabinet, and exit out the sides of the cabinet with a flare somewhat resembling a NACA duct.
But would it be more turbulence than a straight port without a flare?The proposed design might generate significant turbulence
As this is just a rough sketch, the possibilities are essentially unlimited. I can move the port away from the side wall, which would allow a radius at the point you are concerned about. That is just one idea.
Alternatively, is it even a problem? In car aerodynamics, the concept of a spoiler or sharp edge can be used to causes laminar flow to detach at a desired point, reducing turbulence and drag. But ports don't really have a constant laminar flow like a car, since the flow is constantly oscillating....
I'm just asking questions to see if there is any precedent for a design like this, or to see if anyone has experimented with it. I think a NACA intake as a port flare on both sides would be cool. It would definitely be unique.
It is most important that the entry/exit airflow conditions of the port be identical at both ends. Failure to observe symmetry of airflow will result in 'port rectification' whereby the driver will be pushed from its rest position by net positive or negative pressure inside the enclosure (in relation to the surrounding air). The problem becomes worse the harder the speaker is driven.
FWIW, etc., I studied engine intake/exhaust design to do various pipe/horn apps.But ports don't really have a constant laminar flow like a car, since the flow is constantly oscillating....
That is a bad example for a comparison. Sharp edges introduce much chuffing, exciting longitudinal port resonances.straight port without a flare
It would look cool but it's absolutely not the right solution for a port. NACA intake is optimized for a high speed airflow surface air intake.I think a NACA intake as a port flare on both sides would be cool. It would definitely be unique.
Just in case, you can find some slow motion port opening videos here (and further videos and measurements in the thread) - see second part of the video for flange air turbulence part:
Post in thread 'Investigating port resonance absorbers and port geometries'
this was my response regarding @Tenson 's sound recordings.here the exterior termination has the advantage of being flush mounted to the enclosure, thus less turbulent airflow "around the port edge".
To confirm my assumption of internal port end usually being more susceptible to chuffing I made some tests with flanges inside, outside and on both ends of a 4 cm cardboard tube port, using input signals between 1 and 16 V ...
flange variant video
... here is a video with the recorded sound including the respective real time analyzer graphs. the absolute level of the RTA...
Then you must know about pressure pulses travelling in both directions in an inlet manifold, much like in a speaker port, but superimposed upon a net fluid flow...FWIW, etc., I studied engine intake/exhaust design...
Absolutely true, but if the mass of air in the port can move more freely in one direction than the other, the air inside the enclosure will become either compressed or rarefied.But ports don't really have a constant laminar flow like a car, since the flow is constantly oscillating...
The typical 'pipe glued into the baffle' is the absolute worst example of this.
I would think the poor aspect ratio rectangular vent would be a worse example as they always have different restriction between the inside and outside portion of the vent.The typical 'pipe glued into the baffle' is the absolute worst example of this.
https://drive.google.com/file/d/1SU...Kf7FMwieWD3m7LNtyQ_aem_10iCV1Li6UneK0HMWnfWJw
Last edited:
I'm only here for solutions! Saying it is just wrong lacks imagination!It would look cool but it's absolutely not the right solution for a port.
As I said, this is a very rough sketch, and I posted it because I don't waste time trying to explain the basic configuration. All the design details are TBD.
In theory, I think a straight port will perform better than the radius port. But given the configuration of my speaker, designing how a straight port exits the cabinet is a challenge.
I have considered a port that exits out the top, which is the simplest/ most obvious solution, but I don't want to periodically remove the driver to remove objects that have fallen into the speaker.
You'll find the optimized port geometry (found through experimentation and measuring) at the end of the thread linked above!I'm only here for solutions! Saying it is just wrong lacks imagination
I didn't want to shoot down your plans, but since you asked:I'm only here for solutions!
A single circular port, length no more than three times its diameter, with an area as close as possible to Sd and an inside flange with large entry radii both ends.
Or is a radius port with the largest possible radius going to be the best solution?
I am not limiting myself to simple shapes! When I say that details are TBD, I'm saying that I can make a port exit that is any shape that we can imagine! Making molds for fiberglass/ carbon fiber parts has been my hobby for the last ~5 years. If it can be drawn, I can find a way to machine it on my CNC.
With that said, it should be clear that I can make the internal port exit to match the external port exit.
"If you can adequately size your port for a reasonable area, a straight round port, cut flush to the
baffle with a moderate interior flange is a very safe bet for performance. For simplicity
eliminating the interior flange appears to decrease output before chuffing sets in, but otherwise
the performance of the two ports are very similar."
Loudspeaker Port Nonlinearity Copyright 2019 Scott Hinson
I think we need to move on. I'm asking this question because I am exploring the use of a "straight, round port", as prescribed in this paper.
Unfortunately, there isn't a good way to make this port exit perpendicular to the cabinet walls. Which brings us back to my first post.
I am not limiting myself to simple shapes! When I say that details are TBD, I'm saying that I can make a port exit that is any shape that we can imagine! Making molds for fiberglass/ carbon fiber parts has been my hobby for the last ~5 years. If it can be drawn, I can find a way to machine it on my CNC.
With that said, it should be clear that I can make the internal port exit to match the external port exit.
I didn't study the whole thing yet, but the conclusion of the "Speaker Port Nonlinearity Testing" paper concludes:You'll find the optimized port geometry (found through experimentation and measuring) at the end of the thread linked above!
"If you can adequately size your port for a reasonable area, a straight round port, cut flush to the
baffle with a moderate interior flange is a very safe bet for performance. For simplicity
eliminating the interior flange appears to decrease output before chuffing sets in, but otherwise
the performance of the two ports are very similar."
Loudspeaker Port Nonlinearity Copyright 2019 Scott Hinson
I think we need to move on. I'm asking this question because I am exploring the use of a "straight, round port", as prescribed in this paper.
Unfortunately, there isn't a good way to make this port exit perpendicular to the cabinet walls. Which brings us back to my first post.
A single circular port, length no more than three times its diameter, with an area as close as possible to Sd and an inside flange with large entry radii both ends.
Are you calling that a subwoofer port? How does that achieve a tuning frequency that is anywhere close to what is needed for a subwoofer?
A "solution" requires that you work within the requirements.
And to think I liked your previous comment...
Port installed vertically with opening towards the (elevated) speaker bottom, perhaps?Unfortunately, there isn't a good way to make this port exit perpendicular to the cabinet walls.
The question here is: what is "adequately sized" and the answer can be found with the excel port optimizer tool I developed here.can adequately size your port for a reasonable area
The tool is based on papers by Roozen (Philips) and Salvatti/Devantier/Button (JBL) and several test results made by augerpro and me.
The optimizer tool will lead to a flared geometry that has the advantage of minimizing port diameter in the central port section which is less prone to turbulent airflow. Minimizing (central) port diameter very effectively reduces necessary port length, reducing occupied enclosure volume, facilitating installation and raising the first longitudinal tube resonance frequency, possibly outside woofer passband.
You will also find parametric fusion360 and freecad files to generate 3d-printable models. The first post in the thread includes an index where you will find links to those models.
Yes and relevant to the OP's venting and again in my learning path of researching the pioneers I found the simple solution is to cut the pipe at whatever angle that works best for the app, which creates a large, rapid pressure change still used in some forms of racing.Then you must know about pressure pulses travelling in both directions in an inlet manifold, much like in a speaker port, but superimposed upon a net fluid flow...
Please accept my sincerest apologies - my intention was never to offend.And to think I liked your previous comment...
I was simply stating some rules I've learnt after nearly half a century in the audio-related field, put out there to inform and inspire; for others here to take up and to do the simulations for you to achieve what I believe to be the best possible result.
Sorry, my friend.
I think so.But would it be more turbulence than a straight port without a flare?
Although the radius would be helpful, the flow still needs to rotate a lot in that region. That's not ideal.As this is just a rough sketch, the possibilities are essentially unlimited. I can move the port away from the side wall, which would allow a radius at the point you are concerned about. That is just one idea.
- Home
- Loudspeakers
- Subwoofers
- Side Exit Subwoofer Ports? Calculate End Correction Factor