Can anyone suggest how best to attach circuit boards/transistors to an aluminium heatsink? Obviously some sort of screw is needed but i don't want to use self-tappers because i know it's going to get cross threaded at some point. Should i be using machine screws? Is it best to tap the hole first? I'd like a reliable fix that can be done/undone without degrading. Any advice much appreciated, thanks.
Aluminium is a soft material - best is to use screws with nut and washers to tighten the Transistor. also try using a torque adjustable screw driver would be better to apply correct force
sk
sk
If you're mounting cases that tolerate redrilling to a larger hole (TO-3, TO-220 (non-IsoTab), TO-247) and the heatsink is thick enough, you can drill and tap the sink for 6-32 and the case to clear (5/32" or 9/64" is better).
If it needs to be electrically isolated or your skills aren't up to par, just drill the sink to clear a #4 screw (1/8" hole does nice) and use a proper mounting kit as kannan_s suggests.
Cheers!
If it needs to be electrically isolated or your skills aren't up to par, just drill the sink to clear a #4 screw (1/8" hole does nice) and use a proper mounting kit as kannan_s suggests.
Cheers!
Dip the tap in spirit/alcohol when cutting the threads
Unbraco or torx screws are nice
Unfortunately not available in brass, which is my preferred
When drilling holes and cutting threads there will be a very small raise in the aluminium around the hole
Its important to remove that carefully
The easy way is to countersink the hole before cutting the threads
But countersinking may also result in a small raise of material around the hole, depending on your tools and skills
Unbraco or torx screws are nice
Unfortunately not available in brass, which is my preferred
When drilling holes and cutting threads there will be a very small raise in the aluminium around the hole
Its important to remove that carefully
The easy way is to countersink the hole before cutting the threads
But countersinking may also result in a small raise of material around the hole, depending on your tools and skills
Last edited:
tap
Ah, the most pain-in-the-a$$ part of diy audio, drilling and tapping your heat sinks! I HATE doing this but you cannot avoid it.
Most of the time I drill a hole and tap it for a 4-40 thread; then use a machine screw, lockwasher and washer. A 4-40 will fit most semiconductors and gives you a margin of error in placement if you are not so accurate. I use normal household oil on the drill and tap by hand (using regular oil). Then when done wash with normal dishwashing liquid and the garden hose. Do it slowly and you minimize the chances of snapping the tap inside the hole. When this happens -- and it will -- you are in trouble!
If there is a slight raise in the metal around the tap I just leave it (most times) because the hole is usually a wider diameter than the raised part.
If you happen to drill into the spaces between fins, no problem, the hole can be cleared out and any length screw will fit in there. If you happen to drill into a fin the long way, you will have trouble with tapping all the way through, so I just make sure the hole is deep and use shorter screws. A 4-40will hold pretty good even at a short length.
So yes- drill and tap first then clean up the heatsink. It makes an awful mess.
Ah, the most pain-in-the-a$$ part of diy audio, drilling and tapping your heat sinks! I HATE doing this but you cannot avoid it.
Most of the time I drill a hole and tap it for a 4-40 thread; then use a machine screw, lockwasher and washer. A 4-40 will fit most semiconductors and gives you a margin of error in placement if you are not so accurate. I use normal household oil on the drill and tap by hand (using regular oil). Then when done wash with normal dishwashing liquid and the garden hose. Do it slowly and you minimize the chances of snapping the tap inside the hole. When this happens -- and it will -- you are in trouble!
If there is a slight raise in the metal around the tap I just leave it (most times) because the hole is usually a wider diameter than the raised part.
If you happen to drill into the spaces between fins, no problem, the hole can be cleared out and any length screw will fit in there. If you happen to drill into a fin the long way, you will have trouble with tapping all the way through, so I just make sure the hole is deep and use shorter screws. A 4-40will hold pretty good even at a short length.
So yes- drill and tap first then clean up the heatsink. It makes an awful mess.
You won't find any of the screws mentioned here in England 🙂 Use an M3 machine screw and yes you should tap the hole. Be aware though that the base material is aluminium and will not take much undoing/doing cycles before the threads get too worn.
I use self tapping sheetmetal screws, some lube and driven into the correct size hole:
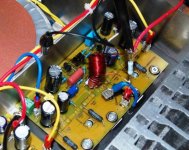
Lots of the old in-out and no stripping. The key to not stripping the holes is not being so damn brutal and make sure the screw is going in correctly in the first place. A tip: before re-driving the screw, back it off until you feel it "click" - that means it's on the correct thread and will go in easily.
Trying to remove a broken tap from a heatsink can be very frustrating...🙂
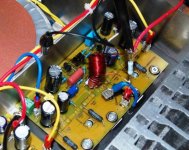
Lots of the old in-out and no stripping. The key to not stripping the holes is not being so damn brutal and make sure the screw is going in correctly in the first place. A tip: before re-driving the screw, back it off until you feel it "click" - that means it's on the correct thread and will go in easily.
Trying to remove a broken tap from a heatsink can be very frustrating...🙂
There are many methods that will work but be aware that heat sinks are made out what some machinists refer to as "pink eraser #3". The stuff is gummy and the inexperienced often break taps in it. Whatever size tap you use, be sure it's sharp; the junk from the local hardware store might not be up to the task. Next, use the correct size tap drill. If you need a #43, that's what you need, not some fractional size that appears close. Best bet is to order from a machine shop supply company and get good name brands of exactly what you need. You can also order spiral flute taps that send the chips out the back, rather than the front- my choice if tapping gummy aluminum, especially blind holes.
Now, if you really want to do it like a pro, it's going to cost you, but not that much. Order a Balax thread forming tap (no substitutes) and the correct size tap drill for it- this will *not* be the same size as for a cutting tap and once you drill the hole you *must* use the Balax. Drill the hole and run the thread forming tap in with some oil. It will go in quite easily, leaves no chips to worry about, and produces work-hardened threads that are tougher and longer lasting than cut threads. Not having grooves cut in the sides, the tap is way stronger. Not having cutting edges, they don't get dull. The downside? They cost about $15 each. OTOH, you'll likely never replace it. File or chamfer the hole to remove the burr and you're good to go. For any ductile material, these are all I use.
Best,
Conrad
Now, if you really want to do it like a pro, it's going to cost you, but not that much. Order a Balax thread forming tap (no substitutes) and the correct size tap drill for it- this will *not* be the same size as for a cutting tap and once you drill the hole you *must* use the Balax. Drill the hole and run the thread forming tap in with some oil. It will go in quite easily, leaves no chips to worry about, and produces work-hardened threads that are tougher and longer lasting than cut threads. Not having grooves cut in the sides, the tap is way stronger. Not having cutting edges, they don't get dull. The downside? They cost about $15 each. OTOH, you'll likely never replace it. File or chamfer the hole to remove the burr and you're good to go. For any ductile material, these are all I use.
Best,
Conrad
Hey Conrad, not being a machinist- how do you order their taps? Looks like there is an "H" number that corresponds to how much tolerance you want in the threads, but what is a happy medium for your average hobbyist or non-production application?
Hi,
You don't need anything fancy. Go to Lowes, Home Depot, or local hardware and get a 6-32 tap, 7/64 drill bit, and Tap handle. Grab some short (1/2") 6-32 screws, washers, and cutting oil.
Have Fun,
Kevin
50 bucks later...
H3 or H4 (or even H5) is fine- the larger the number the larger the tap and these are middle-of-the-road general purpose classes. Here's an example of what I might choose from MSC:
MSC Item Detail
BTW, if you buy cutting taps don't confuse spiral pointed with spiral fluted. You want spiral fluted for stringy gummy materials like heat sinks.
Best,
Conrad
MSC Item Detail
BTW, if you buy cutting taps don't confuse spiral pointed with spiral fluted. You want spiral fluted for stringy gummy materials like heat sinks.
Best,
Conrad
Self-Clinching Captive Fastener or threaded insert is the way to go, no taping and you won’t have any problems with steel threads on an aluminum heat sink and if you get cross threaded just punch out the insert and replace it.
More thoughts- as above, any way you can avoid the whole problem and not tap the gummy heatsink is good. I like molded sockets for TO-3 devices so all you need are some holes with the right spacing.
One of the first things they do with soft aluminum parts on a race car is drill out the threads, re-tap and install Heilcoils. I've also seen this done with heatsinks. Gets expensive. Gives you an almost indestructable thread- great if you blow a lot of output devices.
More on the Balax forming taps- be sure to get their drill size chart and stick to the larger end of the range. The top of the thread will have a "butt crack" where the metal is displaced. If this is too wide, use a smaller drill so there's less tendency to cross thread the fasteners. Too narrow and you risk breaking the tap, so usually one sneaks up on it in a production situation. I've never had to deviate from the published chart.
There's a certain joy in accurately locating holes so the parts fit together and the screws just spin in. It's how you separate good and bad metal workers. The method is simple and once you learn never to skip a step, works every time. 1) Using a scribe holder with a machinists scale, or height gage, lay out the hole location. Use Dykem Blue or a Magic Marker prior to scribing if you need better visibility or don't want to put deep scratches in the metal. If you don't have a surface plate, use a sheet of plate glass. 2) Center punch the marks. Check with a magnifier and readjust as necessary by striking again with the punch at an angle. Yes, you can "move" a center punch divot. 3) Start the hole using a short solid center drill that picks up on the mark. Use oil. Never ever skip this step. 4) Now, drill the hole! Use oil. The hole should be within a few thousandths of where it's supposed to be.
Best,
Conrad
One of the first things they do with soft aluminum parts on a race car is drill out the threads, re-tap and install Heilcoils. I've also seen this done with heatsinks. Gets expensive. Gives you an almost indestructable thread- great if you blow a lot of output devices.

More on the Balax forming taps- be sure to get their drill size chart and stick to the larger end of the range. The top of the thread will have a "butt crack" where the metal is displaced. If this is too wide, use a smaller drill so there's less tendency to cross thread the fasteners. Too narrow and you risk breaking the tap, so usually one sneaks up on it in a production situation. I've never had to deviate from the published chart.
There's a certain joy in accurately locating holes so the parts fit together and the screws just spin in. It's how you separate good and bad metal workers. The method is simple and once you learn never to skip a step, works every time. 1) Using a scribe holder with a machinists scale, or height gage, lay out the hole location. Use Dykem Blue or a Magic Marker prior to scribing if you need better visibility or don't want to put deep scratches in the metal. If you don't have a surface plate, use a sheet of plate glass. 2) Center punch the marks. Check with a magnifier and readjust as necessary by striking again with the punch at an angle. Yes, you can "move" a center punch divot. 3) Start the hole using a short solid center drill that picks up on the mark. Use oil. Never ever skip this step. 4) Now, drill the hole! Use oil. The hole should be within a few thousandths of where it's supposed to be.
Best,
Conrad
I have always used M3 screws like DIN 84. Drill a hole, countersink it, use a M3 screw tap and ready...🙂Can anyone suggest how best to attach circuit boards/transistors to an aluminium heatsink? Obviously some sort of screw is needed but i don't want to use self-tappers because i know it's going to get cross threaded at some point. Should i be using machine screws? Is it best to tap the hole first? I'd like a reliable fix that can be done/undone without degrading. Any advice much appreciated, thanks.
The equipment is reasonable cheap, but you need some basic metal working skills.
Regards
Threaded Holes
Can't see that this has been mentioned, but I use thread forming screws. These are different in that they in effect, forge a thread, in a plain drilled hole, as opposed to a self tapping screw which cuts one. The resultant thread is stronger and suitable for use by standard screws as well. As with all standard tapping it is important to have an accurately drilled hole of the correct size .
Taptite is one well known trade name.
REMINC CONTI TAPTITE® Thread Forming Products
Regards.
Can't see that this has been mentioned, but I use thread forming screws. These are different in that they in effect, forge a thread, in a plain drilled hole, as opposed to a self tapping screw which cuts one. The resultant thread is stronger and suitable for use by standard screws as well. As with all standard tapping it is important to have an accurately drilled hole of the correct size .
Taptite is one well known trade name.
REMINC CONTI TAPTITE® Thread Forming Products
Regards.
If you don't have a surface plate,
What kind of DIYer wouldn't have a surface plate? I just stick the heat sink in my CNC mill to spot drill, drill through and tap. 😉
- Status
- Not open for further replies.
- Home
- Design & Build
- Construction Tips
- Screwing into Heatsink - advice needed