Having had the recent fortune to obtain a good pile of 3/4 furniture grade plywood, I began construction of MJK's 18" H frames and the two 20" square OB baffle boards that sit on top.
I'm not a very good furniture maker and can eek out a "C" grade cob-struction at best. I shoot myself in the foot at least a few times during any such project, which adds hours onto the task to correct.
This time I cut the rear chamfer flare for my 4" MarkAudio Pluvia 7 HD speakers on the wrong side of the baffle board. Cut it on both before realizing. As I was so lucky that the pile yielded enough for two H frames plus two 20 X 20" baffles, I cant just flip them and use the backside...
It's salvageable. However it occurred to me that I could turn the mis-sided flare into a short circular waveguide - I've seen them where folks mount a driver front flange against the back of the baffle, letting the driver project through the baffle and flare. This would leave the back of the driver wide open for OB purposes.
I have no idea how to do this on a 4" round hole, offset in a 20" square board. Except file and sandpaper away, until it looks about right. The only tool I have which might help is a Craftsman table router, where I suppose I could remove the fence, get a bead bit with the bearing on the end and chase the somewhat square edge of the somewhat circlular cutout. Sounds like a disaster...
Maybe I'm better off just mounting the speaker however I can; there's enough material for the screws to sink into if I dont flare the back side too wildly - or at all.
1. Would a circular flare of unknown "looks about right" shape ruin the sound of the Pluvia HD, when mounted to the back of the baffle?
2. Should I bother to flare the backside, risk losing the two pieces for mounting the PHDs? I can still cut 8" holes and run a set of Visaton BG 20s I have.
3. I have enough wood stock that I could enlarge the holes to, say, 6" and put the drivers on a suprabaffle. My mistake doubles the effort...
Thanks for any insight you'd care to share.
I'm not a very good furniture maker and can eek out a "C" grade cob-struction at best. I shoot myself in the foot at least a few times during any such project, which adds hours onto the task to correct.
This time I cut the rear chamfer flare for my 4" MarkAudio Pluvia 7 HD speakers on the wrong side of the baffle board. Cut it on both before realizing. As I was so lucky that the pile yielded enough for two H frames plus two 20 X 20" baffles, I cant just flip them and use the backside...
It's salvageable. However it occurred to me that I could turn the mis-sided flare into a short circular waveguide - I've seen them where folks mount a driver front flange against the back of the baffle, letting the driver project through the baffle and flare. This would leave the back of the driver wide open for OB purposes.
I have no idea how to do this on a 4" round hole, offset in a 20" square board. Except file and sandpaper away, until it looks about right. The only tool I have which might help is a Craftsman table router, where I suppose I could remove the fence, get a bead bit with the bearing on the end and chase the somewhat square edge of the somewhat circlular cutout. Sounds like a disaster...
Maybe I'm better off just mounting the speaker however I can; there's enough material for the screws to sink into if I dont flare the back side too wildly - or at all.
1. Would a circular flare of unknown "looks about right" shape ruin the sound of the Pluvia HD, when mounted to the back of the baffle?
2. Should I bother to flare the backside, risk losing the two pieces for mounting the PHDs? I can still cut 8" holes and run a set of Visaton BG 20s I have.
3. I have enough wood stock that I could enlarge the holes to, say, 6" and put the drivers on a suprabaffle. My mistake doubles the effort...
Thanks for any insight you'd care to share.
Last edited:
mini-horn
I made a little speaker with a TC9FD running full range, and I elected to rear mount it. It was on 3/4" ply, I made the cutout with a hole saw and used a router with a 45 deg angle bit with bearing on it to get a nice looking chamfer. I had to leave enough thickness for the screw to bite into as I screwed it in from behind.
But yeah, it worked as a small horn. I ended up with a little nose poking up in the FR, I think it was about 2 kHz but don't recall exactly. I had a little dayton smartphone measurement mic (uh.... IMM-6 at PE) and in conjunction with a woofer tester for an impedance sweep I was able to design a little notch filter to pull it back out. Not too bad to do if you have some measurement gear, but perhaps frustrating to guess at if you don't. I don't know which camp you're in.
I made a little speaker with a TC9FD running full range, and I elected to rear mount it. It was on 3/4" ply, I made the cutout with a hole saw and used a router with a 45 deg angle bit with bearing on it to get a nice looking chamfer. I had to leave enough thickness for the screw to bite into as I screwed it in from behind.
But yeah, it worked as a small horn. I ended up with a little nose poking up in the FR, I think it was about 2 kHz but don't recall exactly. I had a little dayton smartphone measurement mic (uh.... IMM-6 at PE) and in conjunction with a woofer tester for an impedance sweep I was able to design a little notch filter to pull it back out. Not too bad to do if you have some measurement gear, but perhaps frustrating to guess at if you don't. I don't know which camp you're in.
Thanks! I have a measurement mic, a Tascam ADC and REW.
Sounds like any structure in the path of the driver radiation is going to goof up the FR. It's an all digital system, so I dont have the lux of building an analog filter and inserting it into the signal path.
Now if someone said this specific horn profile works well with the P7 HD, it's the darling of OB makers because it allows the full, unencumbered rear cone of the driver to freely radiate; here's the profile and some links on how people made it, then I'd be in business.
But I'm guessing I'll be mounting it flat on the baffle face and working the actual rear side away until I hit the screws coming through from the font side. Perhaps these cone profiles are intended for flat baffle mount and putting any shaped surface in front of them is just going to effect the driver's sound negatively.
I'd like to sink the driver flange into the baffle by, say, 3/8" - but I just dont have the tooling to do that. Question the possibility w/o owning a free, not table bound, router.
Sounds like any structure in the path of the driver radiation is going to goof up the FR. It's an all digital system, so I dont have the lux of building an analog filter and inserting it into the signal path.
Now if someone said this specific horn profile works well with the P7 HD, it's the darling of OB makers because it allows the full, unencumbered rear cone of the driver to freely radiate; here's the profile and some links on how people made it, then I'd be in business.
But I'm guessing I'll be mounting it flat on the baffle face and working the actual rear side away until I hit the screws coming through from the font side. Perhaps these cone profiles are intended for flat baffle mount and putting any shaped surface in front of them is just going to effect the driver's sound negatively.
I'd like to sink the driver flange into the baffle by, say, 3/8" - but I just dont have the tooling to do that. Question the possibility w/o owning a free, not table bound, router.
A radius might have less effect than a flare.. or in the case you've already cut the flare and have it facing forward, some rounding of the outer front edge.
I mounted it to the baffle face, non-flush as I dont have a normal router. Unsure if I can flare the backside and still have any meat for the driver mounting screws.
It's OK, as these boards may not be the final baffle for this. I'm interested in custom DIY laminations, that are thin and dont ring like a stock piece of plywood. I've started a separate thread.
It's OK, as these boards may not be the final baffle for this. I'm interested in custom DIY laminations, that are thin and dont ring like a stock piece of plywood. I've started a separate thread.
Attachments
Another option would be to widen this opening to the driver maximum diameter then attach another sheet from from the back with a normal driver cutout. Then radius the front.
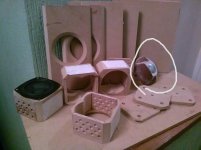
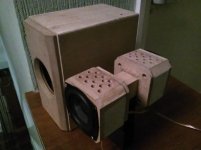
I needed to make a deep chamfer on the front baffle of some speakers, I just glued ( with contact adhesive ) some cloth backed aluminium oxide paper onto a wooden cone with a coach bolt going through ( the white/red thing circled in the picture ), it worked much better than expected, I was expecting to have to peal off the abrasive and replace it as it was used, and have to replace it with a finer grade to get a good finish, but the first pieces of 60 grit did 4 holes easily.
- Home
- Design & Build
- Construction Tips
- Circular Flare in Plywood.