I currently have four 3D printers, and every one of them is failing in one way or another.
Out of frustration, I decided to dust off my K40 laser cutter and try making something.
The idea with this project is to make a Unity horn that has pattern control down to about 500Hz, same as the Danley SH50.
I don't see any scenario where my life allows an SH50 in our living room, so what I did with this project is limit the depth dramatically. The idea I had, is that I can achieve a look that's similar to a Quad ESL if I keep the depth down to a minimum.
Here's what a Quad looks like, I'm trying for a look like this.
All the pieces of the waveguide are laser cut. I used hot melt glue to hold it together long enough to fiberglass some of it. Then added foam to make it sturdier. It will require a lot more fiberglass and more foam to make it ready for prime time.
Also, don't mind the weird Halloween decorations, the kids did that. And no, that roach isn't real 😛
Out of frustration, I decided to dust off my K40 laser cutter and try making something.
The idea with this project is to make a Unity horn that has pattern control down to about 500Hz, same as the Danley SH50.
I don't see any scenario where my life allows an SH50 in our living room, so what I did with this project is limit the depth dramatically. The idea I had, is that I can achieve a look that's similar to a Quad ESL if I keep the depth down to a minimum.

Here's what a Quad looks like, I'm trying for a look like this.






All the pieces of the waveguide are laser cut. I used hot melt glue to hold it together long enough to fiberglass some of it. Then added foam to make it sturdier. It will require a lot more fiberglass and more foam to make it ready for prime time.
Also, don't mind the weird Halloween decorations, the kids did that. And no, that roach isn't real 😛
A ton. I'm actually trying to decided on which one will be best. I'll probably end up using the TF0410MR but it's not set in stone yet.

The Danley horn is about 22" deep, which is deep enough to load the drivers down to about 153hz. This is one of the reasons the efficiency is so high: about 100dB.
The BMSA horn will be about 10" deep, enough to load the drivers down to about 337Hz. The graph above shows the difference between the two horns, when loaded with a set of four Celestion five inch midranges. (I would've used the TF0410MR in this sim, but Celestion hasn't published the Thiele Small parameters and I was too lazy to measure mine last night.)
Long story short: the dramatically smaller footprint of this horn will cause it to have an efficiency of around 93-96dB. But that should be sufficient to get up to about 115dB.
From my 'back of the napkin' estimate, it looks like the midranges may be the limiting factor in this design, because the wider angle of BMSA means that they'll be working harder to cover a wider angle. For instance, the SH50 has an advantage of about 7dB at 300Hz and the gap widens as you go lower.
Due to this, I'll need to decide if:
1) Can I live with a maximum output of about 110-115dB?
2) If not, what mid could be used instead?
There's some B&C mids that could get louder than the Celestion.
I used to run Kali LP6s in my living room, and they couldn't get loud enough to make me happy. According to their spec sheet, their maximum SPL is 112dB. This seems hard to believe; they have an 80 watt amp. In order for that spec sheet to be truthful, the Kali would have to have an efficiency of 94dB, which seems difficult to believe. My Infinity IL10s are a little louder than the Kalis, and according to their spec sheet, their max output is about 111dB.
Based on all that, I'd argue that a targeted maximum of 115dB SPL is probably about right.
You're planning for a compression driver at the throat or dome?
Do you still have those small B&C coaxials?
Do you still have those small B&C coaxials?
The idea here, is to basically make the waveguide in two parts:
1) The big part out of wood
2) the throat out of 3D printed plastic
Very similar to the idea here:
Synergy horn - 3d printing entry?
I've been 3D printing for about five years now. Each printer that I've purchased is progressively larger.
At this point, I can print waveguides that are as large as 18" x 18". A really big waveguide isn't impossible to print now.
The big issue is print failures. I started using the laser cutter again, after I did a 3D print that took two days and failed.
It's unbelievably maddening to have a 3D print fail after 36 hours, it literally makes me want to take the printer and throw it in the trash. Because when you're doing a print, you kinda have to put your life on hold. 3D printers have been known to catch on fire, so I'm not going to do a print when I'm away from home. On top of that, if a print goes wrong and you catch it within about ten or twenty minutes, you can generally "save" the print.
So when I do a really long print, it feels like I'm basically baby-sitting the printer. It's nerve wracking.
I don't want to jinx myself, but my laser cutter is a workhorse. It can finish a cut in around five minutes and it works like clockwork. About my only real complaint is that it makes the garage smell like a campfire.
So this seems like a viable to get the best of both worlds:
1) Use the 3D printer for the throat, where you really need to get the curve perfect. Mabat's software is amazing, and it's shown us that a difference of even five degrees makes a big difference at the throat. Even worse, the response of a waveguide varies from tweeter to tweeter. IE, I have two different dome tweeters that look nearly identical, but one performs well on a waveguide and the other one doesn't.
2) A laser cutter can cut the large parts of the horn quickly. But a laser cutter isn't ideal for the level of detail that's required at the throat.
1) The big part out of wood
2) the throat out of 3D printed plastic
Very similar to the idea here:
Synergy horn - 3d printing entry?
I've been 3D printing for about five years now. Each printer that I've purchased is progressively larger.
At this point, I can print waveguides that are as large as 18" x 18". A really big waveguide isn't impossible to print now.
The big issue is print failures. I started using the laser cutter again, after I did a 3D print that took two days and failed.
It's unbelievably maddening to have a 3D print fail after 36 hours, it literally makes me want to take the printer and throw it in the trash. Because when you're doing a print, you kinda have to put your life on hold. 3D printers have been known to catch on fire, so I'm not going to do a print when I'm away from home. On top of that, if a print goes wrong and you catch it within about ten or twenty minutes, you can generally "save" the print.
So when I do a really long print, it feels like I'm basically baby-sitting the printer. It's nerve wracking.
I don't want to jinx myself, but my laser cutter is a workhorse. It can finish a cut in around five minutes and it works like clockwork. About my only real complaint is that it makes the garage smell like a campfire.
So this seems like a viable to get the best of both worlds:
1) Use the 3D printer for the throat, where you really need to get the curve perfect. Mabat's software is amazing, and it's shown us that a difference of even five degrees makes a big difference at the throat. Even worse, the response of a waveguide varies from tweeter to tweeter. IE, I have two different dome tweeters that look nearly identical, but one performs well on a waveguide and the other one doesn't.
2) A laser cutter can cut the large parts of the horn quickly. But a laser cutter isn't ideal for the level of detail that's required at the throat.
lol that last post was really long and rambling. The TLDR is that building the waveguide in two pieces means that I can try a series of different tweeters, without having to 3D print the whole thing. The throat is interchangeable.

Here's a comparison of how BMSA performs, as I built it, versus if I cut the height in half. You can see that reducing the height of the horn nearly doubles the output on axis. This is because we have the same four drivers radiating into an angle that is half as large. On the downside, the horn would suffer from pattern flip.
This is a tricky one; a horn that's half as tall would definitely *look* better.
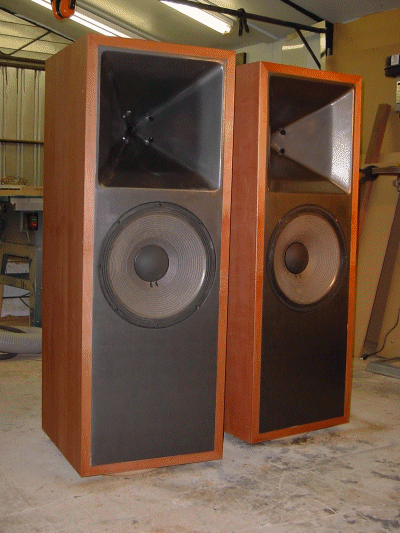
It might be optimum to do something like the Lambda Unity horn. Basically put the woofer below the horn, and then use an interference pattern to extend the vertical beamwidth control down to 500Hz.
If I put a Unity horn on top, and used a center to center spacing of ten inches, with a woofer below it, I could maintain a vertical beamwidth of 72 degrees down to about 700Hz. Another 'neat' thing is that the midranges in the Unity horn would only be playing down to 743Hz. Because of this, the power handling should be unreal, because they will never get anywhere close to their xmax with such a high xover point.
Have you considered something like this; Pseudo-coaxial with narrow directivity (and Horbach-Keele filters)
He probably did ;-)
From: Pseudo-coaxial with narrow directivity (and Horbach-Keele filters)
From: Pseudo-coaxial with narrow directivity (and Horbach-Keele filters)
Some random observations about this speaker here : Combating Pattern Flip
It's downright embarassing how many times I've read the Horbach Keele paper, it's definitely one of my favorites of all time.
I jumped into this project with a goal that was largely "how do I make a waveguide in two pieces" but on further reflection, I think it probably makes sense to put the woofers *outside* of the waveguide.
Very similar to my Nexus projects here: Nexus - World's Easiest Controlled Directivity Loudspeaker
And the Sound Physics Labs SPL-TRIK.
In the link that I posted above, check out the video and compare it to some of my other projects. From what I hear in that video, I think it's one of the best sounding speakers I've made. I admittedly make a lot of weird stuff, and I think the reason that the Nexus speaker sounds good is that it doesn't have anything in it that's particularly weird. For instance, there's no Paralines in the mix, there's no pattern flip, no weirdly asymmetrical waveguides.
I notice with my own projects that I have a tendency to try and figure out how far I can push the rules of loudspeaker design, but sometimes it just makes sense to build what is largely an MTM.
I jumped into this project with a goal that was largely "how do I make a waveguide in two pieces" but on further reflection, I think it probably makes sense to put the woofers *outside* of the waveguide.
Very similar to my Nexus projects here: Nexus - World's Easiest Controlled Directivity Loudspeaker
And the Sound Physics Labs SPL-TRIK.
In the link that I posted above, check out the video and compare it to some of my other projects. From what I hear in that video, I think it's one of the best sounding speakers I've made. I admittedly make a lot of weird stuff, and I think the reason that the Nexus speaker sounds good is that it doesn't have anything in it that's particularly weird. For instance, there's no Paralines in the mix, there's no pattern flip, no weirdly asymmetrical waveguides.
I notice with my own projects that I have a tendency to try and figure out how far I can push the rules of loudspeaker design, but sometimes it just makes sense to build what is largely an MTM.
Attachments
-
1711209-66e32bac-tom-danley-sound-physics-labs-spltrik-synergy-horn-speakers.jpg71 KB · Views: 366
-
1711207-78c736a2-tom-danley-sound-physics-labs-spltrik-synergy-horn-speakers.jpg95.7 KB · Views: 378
-
1711214-29f277bb-tom-danley-sound-physics-labs-spltrik-synergy-horn-speakers.jpg51.9 KB · Views: 363
-
1711208-09836895-tom-danley-sound-physics-labs-spltrik-synergy-horn-speakers.jpg51.1 KB · Views: 360
Have you considered something like this; Pseudo-coaxial with narrow directivity (and Horbach-Keele filters)
Agreed, it's the 'flatten a synergy concept', probably as well done as any.
I think it works, but at the price of focusing to a measurably tighter area at expense of off-axis, ...when compared to a synergy.
When width is increased, as happens with flattening, angles to listening distance get more crucial.
Or so my limited amount of testing the flattened syn idea leads me to believe.
hey Patrick, any less depth and we will have to call it a ring-radiator 😀
btw, how do you get the SH-50 wil load to 153Hz ?

Here's a design I threw together, that measures 27" wide by 48" tall.

Layout is very similar to the Donald North Audio DNA Sequence

My design is aiming for a vertical beamwidth of seventy degrees and a horizontal beamwidth of 120 degrees. This is why the midbasses are arranged ellipitically instead of in a circle. (A circle would yield a symmetrical beamwidth.) Crossover points and spacing are basically identical to the Horbache Keele paper: the vertical spacing of the midbasses is approximately 25". The horizontal spacing is reduced to 20", to widen the beamwidth of the array on the horizontal axis.


Here's the vertical and horizontal directivity. Looks pretty good I'd say.

Here's the predicted directivity index
There was a mistake with the sims in the last post. I had the woofers wired wrong in Vituixcad.
Here's the corrected predictions. Everything else is identical: spacing, geometry, etc.
Here's the corrected vertical and horizontal polar response.
Here's the corrected predictions. Everything else is identical: spacing, geometry, etc.


Here's the corrected vertical and horizontal polar response.
Good idea. I guess you can just make up the loss in SPL by adding more mids and the horn is still sufficient to load the tweeter.
Patrick why do you keep on barking up the wrong tree
Danley has not exactly spelt it out but he has given more than enough away.
You really will never get the concept even though handed on a plate for you.
Dogs chase there tails
Danley has not exactly spelt it out but he has given more than enough away.
You really will never get the concept even though handed on a plate for you.
Dogs chase there tails
Patrick why do you keep on barking up the wrong tree
Danley has not exactly spelt it out but he has given more than enough away.
You really will never get the concept even though handed on a plate for you.
Dogs chase there tails
You think I don't understand how the concept works?
Is this satire?
If you did you would stop chasing rainbows 🙂
The last thing I want to do, is publish a "how to make a Synergy Horn thread." If I did that, it would be a blueprint for any clone manufacturer in China to take what I published, and compete with Danley Sound Labs head-to-head.
I've met Danley, I've met the entire crew over there, I'd like to see them making cool American made products for a long time.
It has nothing to do with a lack of understanding.
But don't listen to me, here's what Danley thinks of my projects:
Square Pegs
- Home
- Loudspeakers
- Multi-Way
- Big Mouth Strikes Again