Let's create this thread with the same purpose as the tube photo gallery thread, but about transformers. We can show off pictures, measurements, explanations, etc, mostly for fun and potential sharing of knowledge.
I'm starting with my most recent project of freshly wound coils, that are specially made for SE high Rp output stages with Rp ranging from 10k to 24k in series primaries and 2,5k to 6k with paralleled primaries.
I'm starting with my most recent project of freshly wound coils, that are specially made for SE high Rp output stages with Rp ranging from 10k to 24k in series primaries and 2,5k to 6k with paralleled primaries.
Attachments
Nice work!
OT's seem more complicated to wind than PT's, due to necessary wide frequency range needed w/ OT's.
What is your design process before acquiring parts? Did you make those bobbins or purchase?
I purchased mine from here- shipping is high $, but this vendor has wide variety:
https://www.aliexpress.us/item/3256805029501795.html?
My PT project is on separate thread. Started it for same reason- info sharing- raw materials readily available, not much tech discussion, tho.
I'm rewinding a 350W, 114x65mm core received for 230vac (only) primary- near useless in North America.
First was to unwind, divide & rewind primary into 2 coils for parallel operation. I'm not sure which windings will be next- (3) 6.3v filament (4a, 4a,1.5a ct) -
or a single 340V B+ w/ tap for fixed bias. Have 625' spool of 23ga for that, instead of rewinding the original 720v ct from 26ga.
First 4 pics below are of unwind procedure, last is rewound primary(s).
Subscribing-
Jim
OT's seem more complicated to wind than PT's, due to necessary wide frequency range needed w/ OT's.
What is your design process before acquiring parts? Did you make those bobbins or purchase?
I purchased mine from here- shipping is high $, but this vendor has wide variety:
https://www.aliexpress.us/item/3256805029501795.html?
My PT project is on separate thread. Started it for same reason- info sharing- raw materials readily available, not much tech discussion, tho.
I'm rewinding a 350W, 114x65mm core received for 230vac (only) primary- near useless in North America.
First was to unwind, divide & rewind primary into 2 coils for parallel operation. I'm not sure which windings will be next- (3) 6.3v filament (4a, 4a,1.5a ct) -
or a single 340V B+ w/ tap for fixed bias. Have 625' spool of 23ga for that, instead of rewinding the original 720v ct from 26ga.
First 4 pics below are of unwind procedure, last is rewound primary(s).
Subscribing-
Jim
Attachments
I purchased mine from here- shipping is high $, but this vendor has wide variety:
https://www.aliexpress.us/item/3256805029501795.html?
No reasons to purchase bobbins in small qty at these horrible prices, just cut and assemble by yourself from any suitable plastic (e.g. FR4, CEM) whatever you need. Short visual instruction in attachment. If you will use CNC milling cutter don't forget to make corner clearance for most common 3.175mm (1/8") mill.
Attachments
It would seem the material overhang in your Pic 2 would be in the way of of the EI core??
Does that extension get trimmed after cement dries?
Your point is well taken about cost- But if I were to do more of these wraps- would generate 3D bobbin file & print ABS or Nylon
Jim
Does that extension get trimmed after cement dries?
Your point is well taken about cost- But if I were to do more of these wraps- would generate 3D bobbin file & print ABS or Nylon
Jim
Here is finished transformer, 60W PP, 33%UL, 12%CFB, 1165H primary inductance @200V/50Hz, 3.28mH leakage inductance, 67KHz -3dB top frequency, primary R=67.5 Ohm, CFB R=7.7 Ohm, Secondary R<=0.2 Ohm. I tested it in Williamson and HK Citation II circuits, both are known to be quite demanding to the quality of output iron. Frequency response of the last is flat up to 50KHz, as with original output iron.
Bobbin laser cut from 2mm composite epoxy laminate, sheet material is cemented before cutting. Design of the bobbin is universal, it can be manufactured with laser, CNC mill (with corner clearance for 3.175mm mill), or 3D printed.
@gordon53 - bobbin from China is not expensive, shipping is very costly because of dimensions. As per link of oemcar, 7.5 Euro bobbin price, 25.98 Euro shipping cost (for 1 bobbin). For 2 bobbins everything is even worse - can't be shipped to Europe by China Post, so DHL transport is 94.86 Euro.
Bobbin laser cut from 2mm composite epoxy laminate, sheet material is cemented before cutting. Design of the bobbin is universal, it can be manufactured with laser, CNC mill (with corner clearance for 3.175mm mill), or 3D printed.
@gordon53 - bobbin from China is not expensive, shipping is very costly because of dimensions. As per link of oemcar, 7.5 Euro bobbin price, 25.98 Euro shipping cost (for 1 bobbin). For 2 bobbins everything is even worse - can't be shipped to Europe by China Post, so DHL transport is 94.86 Euro.
Attachments
"bobbin from China is not expensive, shipping is very costly because of dimensions. As per link of oemcar, 7.5 Euro bobbin price, 25.98 Euro shipping cost (for 1 bobbin). For 2 bobbins everything is even worse - can't be shipped to Europe by China Post, so DHL transport is 94.86 Euro."
Very true. This vendor is small volume, so his shipping cost is higher. Different vendor below is bit cheaper- $24 vs $30, but 2nd vendor didnt have size needed when I started project. Had to purchase new bobbin because original was cracked- chose not to try repair.
Very true. This vendor is small volume, so his shipping cost is higher. Different vendor below is bit cheaper- $24 vs $30, but 2nd vendor didnt have size needed when I started project. Had to purchase new bobbin because original was cracked- chose not to try repair.
richoemcar ....are you using recovered E&I stampings (tedious) or new ones for power transformers? One is lucky if one can recover without too many damaged stampings, as the varnish these days is hard to get rid of, without heating the core up for several hours in an oven to soften. In most cases with european made transformers, the impregnation is too complete, so generally I have to snip through the windings to the primary and re-start the winding process. Counting the turns is then lost. As to recalculating the number of turns, this is where the physics with expected iron core area has to be redone with tolerance and required Bmax. Quite often I have to roughly reassemble a party wound core in order to check the expected voltages under load aren´t too far off. Reassembling A 1kW lump is a torrid evenings work. Re-assembly will never be the same to how manufacturers force assemble with machines, this to avoid a buzzing core. I use a small drop of poly/ethane varnish on final re-assembly. There is also the dreadful practice of using E&I laminations and welding the lump up. This spews out enormous stray flux often worse than toroids.
Rich,
Yes- laminates in this core came apart very easily with exacto knife. There was some kind of spotty liquid (maybe residual oil from laminate production??) that didn't harden. Only damaged first E core laminate, as it was tight fit in bobbin. Hoping to reuse- may have to wipe them off with mineral spirits or something.
Jim
Yes- laminates in this core came apart very easily with exacto knife. There was some kind of spotty liquid (maybe residual oil from laminate production??) that didn't harden. Only damaged first E core laminate, as it was tight fit in bobbin. Hoping to reuse- may have to wipe them off with mineral spirits or something.
Jim
Linuksguru, i bougth some SU90b bobbins (german made Weissmueller) from a local winder for 3 euro a piece and importing from germany to finland is just as expensive as from china, often even more. Gotta remember that in china peoples salaries are peanuts. I know, i once also worked for peanuts, something like 7USD20c a month (45h+ a week)
Thanks, I know about Weisser, but I used cores of custom size, so factory with a line of standard dimensions was not an option.Linuksguru, i bougth some SU90b bobbins (german made Weissmueller) from a local winder for 3 euro a piece and importing from germany to finland is just as expensive as from china, often even more.
Yeah, coresize sets a limit to the choice one has. I looked for a long time for SG89/38 bobbins because i have more than a dozen silectron quality cores of this size, no luck, did not find anyone supplying bobbins for them. The price thingy would not bother me a bit if workers would get payed accordingly, but as long as a factory workers monthly salari is the equivalent to the price of at most a few dozen bobbins i find it a rip off.
Btw, congrats to your transformer built and the very promising measuring results, what impedance and coresize is it?
Btw, congrats to your transformer built and the very promising measuring results, what impedance and coresize is it?
Anyone contemplating reusing and rewinding an old mains tranny need to be armed with the right tools, that is to avoid unnecessary lamination damage. I use a thin but short steel ruler with one end rounded off similar to a wood chisel to prise open stuck laminations and a small brass ended hammer.. A steadfast flat plinth to eventually knock the laminations into one another on re-assembly; squareness is crucial on rebuild. Expect to loose the first pairs of laminations.
It may seem putting off but I find the bigger the transformer, the easier it gets, may because I am a handworker with strong fingers. A 1kW beast will be using around 1.2-1.5mm diam for the primary, easy with no bunching but the bobbin pile will soon start a round/oval shape, further reducing the window availability. The 6.35V 25A winding is made up of 3x 2.5mm dia wire to fill exactly 7 turns i.e the bobbin width.The integer from this determines the turns/volt for the remainder plus a fraction more to compensate for the regulation factor. This winding after the safety interwinding screen is a hard one, hence several single conductors are used rather than trying to coherce a strip of 5mm x 2.5mm.
rj
It may seem putting off but I find the bigger the transformer, the easier it gets, may because I am a handworker with strong fingers. A 1kW beast will be using around 1.2-1.5mm diam for the primary, easy with no bunching but the bobbin pile will soon start a round/oval shape, further reducing the window availability. The 6.35V 25A winding is made up of 3x 2.5mm dia wire to fill exactly 7 turns i.e the bobbin width.The integer from this determines the turns/volt for the remainder plus a fraction more to compensate for the regulation factor. This winding after the safety interwinding screen is a hard one, hence several single conductors are used rather than trying to coherce a strip of 5mm x 2.5mm.
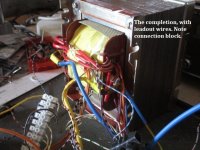
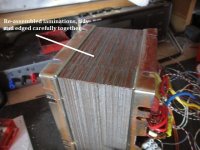
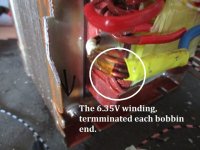
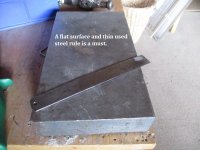
rj
Its 3.9K for KT88/6550 PP, core is custom made, similar to Q10.2 but with larger window size. Standard C-size are designed for 220V/50Hz (or 110V/60Hz) in mind, so while cross-section may be OK, window is usually too small to accommodate winding. EI core have an advantage from this side, you can make EI stack of any meaningful thickness even out of surplus, e.g. disassemble 3 units for 2 transformers.Yeah, coresize sets a limit to the choice one has. I looked for a long time for SG89/38 bobbins because i have more than a dozen silectron quality cores of this size, no luck, did not find anyone supplying bobbins for them. The price thingy would not bother me a bit if workers would get payed accordingly, but as long as a factory workers monthly salari is the equivalent to the price of at most a few dozen bobbins i find it a rip off.
Btw, congrats to your transformer built and the very promising measuring results, what impedance and coresize is it?
Attachments
I design the bobbins on CAD and then lasercut them. I've made 50-60 bobbin sizes so far, some of them redesigned for some additional extras, like glue insertion holes, terminals, etc.What is your design process before acquiring parts? Did you make those bobbins or purchase?
I purchased mine from here- shipping is high $, but this vendor has wide variety:
Pre-design is done carefully and is complex to explain, due to the reason different customers can require different prime criteria. I've optimized transformer designs around the choice of core, wire gauges, footprint, frequency response, power output, aesthethics, and all of that requires some switching in the way of designing.
One of my hardest challenges was squeezing maximum performance for a limited footprint, or commercial transformer enclosure available. With time I learned some cheats, mostly for optimizing the high-frequency response region.
All transformer types and geometries differ in interleaving configuration, and the interleaving itself can be optimized further for different frequency response behaviors. So transformer design basically becomes a very colorful cookbook.
Your knowledge of the subject seems quite extensive. Are you self-taught, or are/were you employed in the industry?
I started as a winder to be taught by another transformer geek, though after some period of time having passed, I became obsessed by transformer design and I quickly overpassed my teacher and quit the company. Mostly self taught, I acquired as many books as I could find on transformers, but I'd say, literature represents a maximum of 30% on my transformer knowledge. All else I had to find through trial, error and empirical studies on my own.
- Home
- Amplifiers
- Tubes / Valves
- Show your transformer work (gallery)