I'm not sure whether this idea makes sense, so perhaps some of you with better physics understanding can weigh-in.
I'm making some speakers and wanted to brace between the back of some drivers and the back of the cabinet. I did this in a previous set, by having some plywood stiffeners come up behind the woofer magnets and wedge-ing some thick felt in there as the woofer got pushed in. The felt gave it something to kind-of adjust with and still give an air tight seal around the woofer. That seemed to work pretty well (at least according to the time-honored, but not likely very meaningful, "knuckle-rap test"..... I really need to get another accelerometer to test this stuff with again).
So, the first question: as the felt probably helps to dissipate panel energy (rather than just retune-in), might that actually be a better way to brace front to back in the box than would just having a solid rod or block? I used the felt to allow some tolerance in the fit, but I wonder whether it might have an advantage in damping. The back of the box certainly seemed to deaden after I did it.
Second question: I found some of these online (available at big-box hardware stores) --
They're made for leveling furniture, but it looks to me like they might provide a nice adjustable way to apply damping or coupling to the back of a driver to a board or panel behind. If you can get your hand into the box (maybe through a waveguide hole or a port?) after the drivers are mounted, its tightness could even be adjusted by to a desired degree. Does that seem like it could be a good thing, or are there problems with this whole idea.?
If the felt isn't a helpful thing (the first question,above), then it could be removed and replaced with something else to give a more solid connection; an adjustable driver brace.
The little levelers ("Threaded Stem Furniture Glides with Felt Base") are quite cheap, about a buck each.
I'm making some speakers and wanted to brace between the back of some drivers and the back of the cabinet. I did this in a previous set, by having some plywood stiffeners come up behind the woofer magnets and wedge-ing some thick felt in there as the woofer got pushed in. The felt gave it something to kind-of adjust with and still give an air tight seal around the woofer. That seemed to work pretty well (at least according to the time-honored, but not likely very meaningful, "knuckle-rap test"..... I really need to get another accelerometer to test this stuff with again).
So, the first question: as the felt probably helps to dissipate panel energy (rather than just retune-in), might that actually be a better way to brace front to back in the box than would just having a solid rod or block? I used the felt to allow some tolerance in the fit, but I wonder whether it might have an advantage in damping. The back of the box certainly seemed to deaden after I did it.
Second question: I found some of these online (available at big-box hardware stores) --
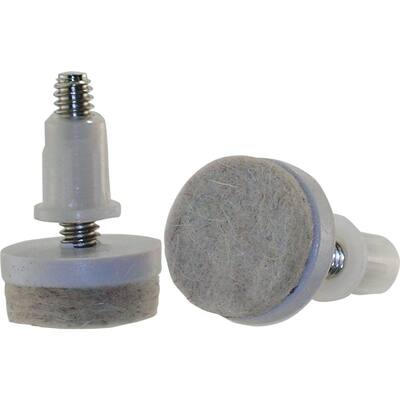
They're made for leveling furniture, but it looks to me like they might provide a nice adjustable way to apply damping or coupling to the back of a driver to a board or panel behind. If you can get your hand into the box (maybe through a waveguide hole or a port?) after the drivers are mounted, its tightness could even be adjusted by to a desired degree. Does that seem like it could be a good thing, or are there problems with this whole idea.?
If the felt isn't a helpful thing (the first question,above), then it could be removed and replaced with something else to give a more solid connection; an adjustable driver brace.
The little levelers ("Threaded Stem Furniture Glides with Felt Base") are quite cheap, about a buck each.
Attachments
Last edited:
Utterly theoretical opinion: what about infusing silicone into the felt feet? I'd *think* I'd want better mechanical coupling between the feet/brace structure and the back of the driver than squished felt would provide. The softness of the silicone *might* help with both dampening and provide an alternate route for vibration energy out of the motor.
Even if we were experts there are so many variables. The priority problems wouldn't be the same in each case.Utterly theoretical opinion
One idea I like is the theory of establishing a 'ground' point. Just like with electronics. Ie, although the entire cabinet and driver should be one whole, this thread is about how this isn't the case.
The magnet should probably be the ultimate ground point. The shown brace does go a ways to establishing a good connection point to the cabinet.
Where I would have a concern is with the driver moving freely between this brace and the otherwise rogue front baffle. I would make the distinction between lower frequency structural integrity and higher frequency 'buzzing', but these can be separated for practical purposes.
Agreeing with you also on the idea of bonding the front and rear because I doubt using the driver basket as a stressed member of the enclosure. It's also been suggested around here.
Panel resonances and overall cabinet integrity issues are crossing purposes that can have a converging solution.
Where I would have a concern is with the driver moving freely between this brace and the otherwise rogue front baffle.
But, that's why the felt --- because the driver can be bolted firmly to the baffle and still have buffered? damped? bracing to the back panel.
Last edited:
Utterly theoretical opinion: what about infusing silicone into the felt feet? I'd *think* I'd want better mechanical coupling between the feet/brace structure and the back of the driver than squished felt would provide. The softness of the silicone *might* help with both dampening and provide an alternate route for vibration energy out of the motor.
Silicone might be a good midway point between felt and a solid surface, and would have some "give" so the driver still could be firmly on the baffle.
For "adjustable-after-mounting" use, though, I'd think silicone wouldn't put up well with being twisted/rotated against the back of a driver. It has a lot of friction when rubbed against something (unlike felt). Maybe a teflon squishy thing, but teflon itself is very non-squishy. Though it does have low grabbiness.
(do you like my technical terminology?)
Love the terminology, Bill. 😀
Yes, the logic I was running as far as a soft, albeit decently adhesive (sticky) material as a coupling membrane is as you described.
As far as adjustability, these are essentially felt pads on a threaded rod, no? Any reason you couldn't use two nuts and a slot in the brace (with a hole to pass the rod through), and just thread the nuts in such a fashion that they're compressing the walls of the slot? Then you just locate the nuts on the threaded rod (using a wrench) without twisting the silicone surface.
(Essentially like a ball screw drive for a cnc table except you're fixing the nut and not the screw if that makes sense)
Yes, the logic I was running as far as a soft, albeit decently adhesive (sticky) material as a coupling membrane is as you described.
As far as adjustability, these are essentially felt pads on a threaded rod, no? Any reason you couldn't use two nuts and a slot in the brace (with a hole to pass the rod through), and just thread the nuts in such a fashion that they're compressing the walls of the slot? Then you just locate the nuts on the threaded rod (using a wrench) without twisting the silicone surface.
(Essentially like a ball screw drive for a cnc table except you're fixing the nut and not the screw if that makes sense)
I THINK I follow that. Might also need some big washers, too, to keep the nuts from sinking into the brace.
Given this constraint, I see a couple of remaining concerns. One per the link..the driver can be bolted firmly to the baffle
..and maybe in addition the method of attaching to a CLD front piece (which layer etc.). Additionally, I believe Earl uses normal (basket) mounting.structure to structure vibrations, which are actually most effective at higher frequencies. These can be a real problem in an enclousre where something is not done to damped them. But a simple contrained layer damping (CLD) front baffle and rear baffle (which are rigidly attached together)
I probably don't/didn't see the felt material in the same light as you had intended it.
Secondly basket resonances (link) . This is one place I suspect your plan has merit. As to how, whether putting the basket under stress, stiffening it, damping it or damping a stress mounting will probably dictate the design of the brace.
Last edited:
With the driver firmly connected to the baffle, isnt the basket transferring most of the reaction force directly onto the baffle? But i do like the idea of the felt tipped member in the cabinet bracing the driver as it gets fastened into the baffle.
How about the magnet connecting to a plate of wood floating on a damping material which in turn is attached to another plate rigidly connected to the cabinet. Basically creating a CLD dissipating energy from the magnet through shear force.
How about the magnet connecting to a plate of wood floating on a damping material which in turn is attached to another plate rigidly connected to the cabinet. Basically creating a CLD dissipating energy from the magnet through shear force.
Last edited:
But wouldnt a cld panel require very tight tolerance between driver, baffle, and back panel? Or do you have a way to make it adjustable?
I was looking for a way to use something like a turnbuckle, but connecting that to a panel or driver would require a lot of custom metalwork. It might be neat to use something like the screw and socket -plate of a C-clamp, maybe have it adjustable via screw from the back of the cabinet, have that push onto the cld board? But getting those screwdrives from C clamps could get expensive... I'll have to check Harbor Freight maybe.
In the boxes I'm making there isn't really a place to cross brace the back panel to other than to the backs of drivers. The bsffle is nearly all waveguixe and woofers.
I was looking for a way to use something like a turnbuckle, but connecting that to a panel or driver would require a lot of custom metalwork. It might be neat to use something like the screw and socket -plate of a C-clamp, maybe have it adjustable via screw from the back of the cabinet, have that push onto the cld board? But getting those screwdrives from C clamps could get expensive... I'll have to check Harbor Freight maybe.
In the boxes I'm making there isn't really a place to cross brace the back panel to other than to the backs of drivers. The bsffle is nearly all waveguixe and woofers.
I have used CLD baffles, lossy braces, sorbothane magnet cradles, and sorbothane driver gaskets.
They all have their place in dampening cabinet resonances.
Most of my techniques as documented in my threads here, some have supporting measurements.
They all have their place in dampening cabinet resonances.
Most of my techniques as documented in my threads here, some have supporting measurements.
Sorbothane gasket for tweeter in an old sealed three way project:
Sorbothane covered magnet cradles in a more recent synergy horn build.
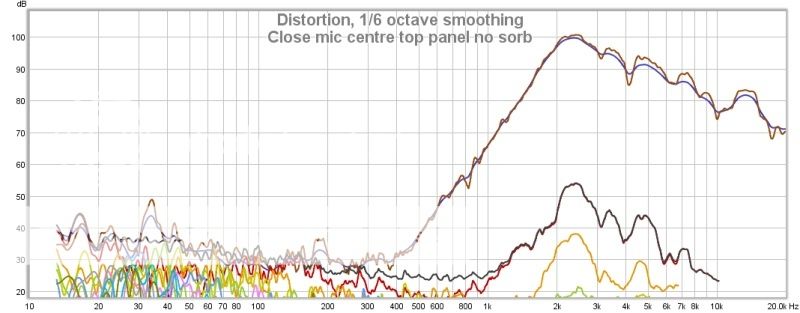
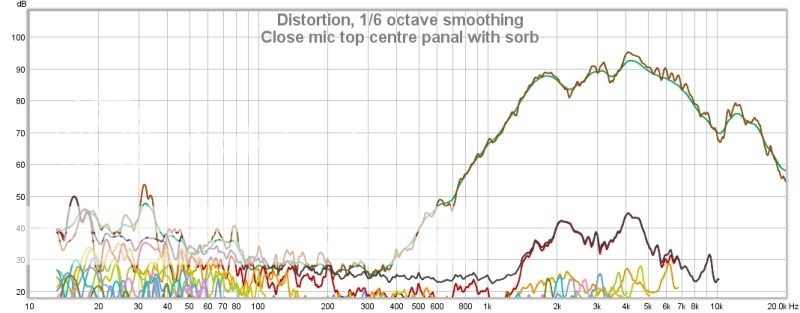
Sorbothane covered magnet cradles in a more recent synergy horn build.
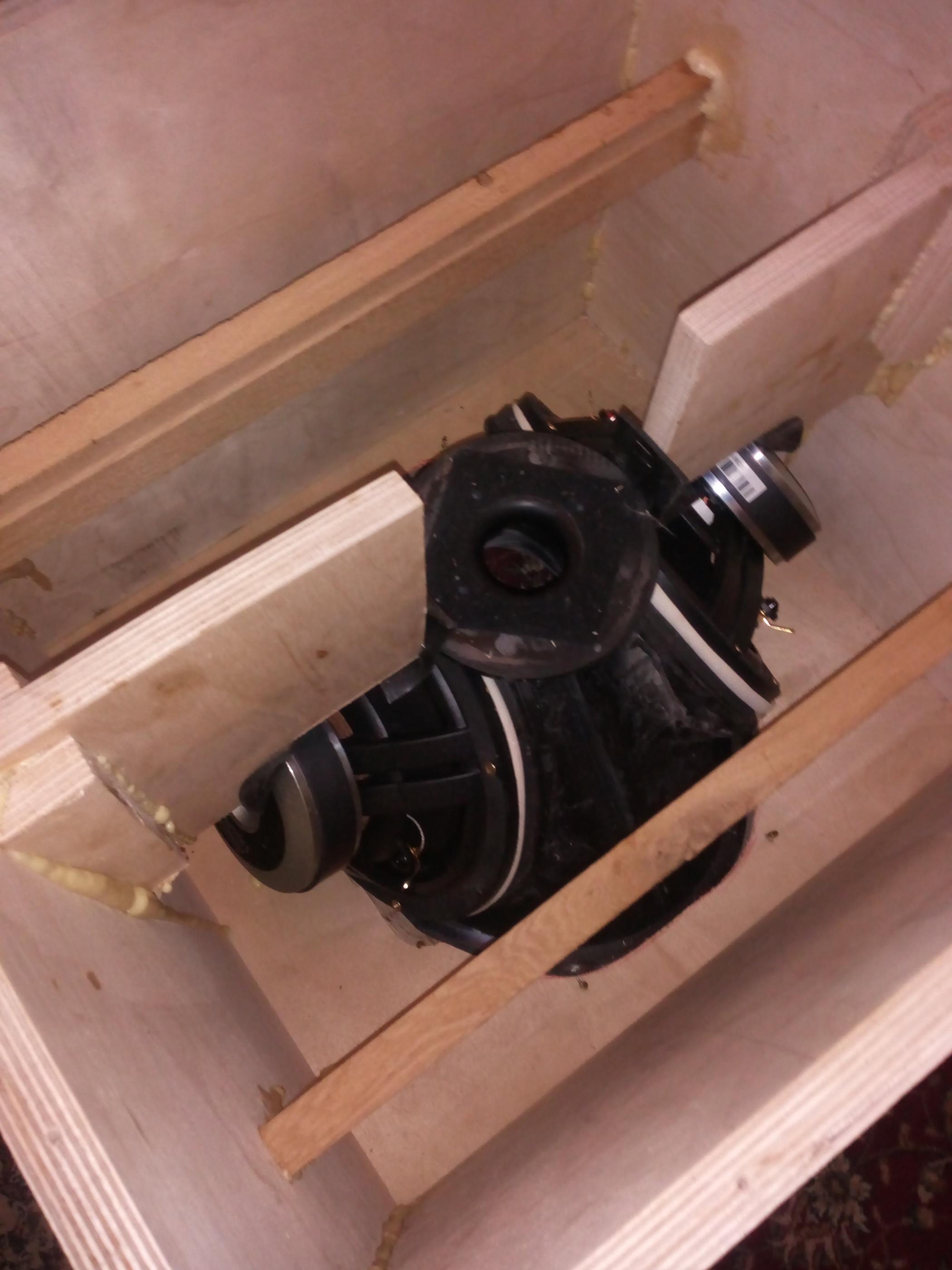
If this is the small syns, the driver mounting is not symmetrical, (although this could be remedied). Ie, the front panel moves hinged by the corners.The felt gave it something to kind-of adjust with and still give an air tight seal around the woofer. That seemed to work pretty well (at least according to the time-honored, but not likely very meaningful, "knuckle-rap test".....
I used the felt to allow some tolerance in the fit, but I wonder whether it might have an advantage in damping. The back of the box certainly seemed to deaden after I did it.
Hypothetically, if the drivers were wedged within the front and rear panels, the first cabinet (breathing) mode will cause the upper inner woofer mounting region to move further outward than the lower outer edges. Depending on which parts were solidly connected this might cause the basket to rock and warp, or the magnet to slip diagonally across the felt.
By establishing symmetry, the felt brace against the back panel would become limited in duty to influencing the basket resonance (notwithstanding the lesser dipole mode unless they are tied to the sides as well.).
Last edited:
I think the CLD damped window brace is used in the kef LS50, it's described in the white paper with measurements. I'd imagine it would be similarly beneficial as a damped magnet brace as shared by Bushmeister.
For at least a decade know we have been building speakers with a holey brace that is tightly coupled to the driver magnet and the back (and at least 2 other box sides).
The goal is to shunt as much driver energy to the other panels & away from the baffle (usuually the weakest panel due to the holes in it) as possible.
We try to keep the coupling as rigid as possible. Perhaps a bit fiddly but Chris (and Bernie) don't seem to have many issues with making the brace fit.
dave
The goal is to shunt as much driver energy to the other panels & away from the baffle (usuually the weakest panel due to the holes in it) as possible.
We try to keep the coupling as rigid as possible. Perhaps a bit fiddly but Chris (and Bernie) don't seem to have many issues with making the brace fit.
dave
Tannoy has been doing this since at least 2001 with the Saturn series. They used material similar to this: http://www.parts-express.com/parts-express-12-speaker-sealing-caulk-box-of-72-pcs--260-400 rolled into a ball between the bracing and magnet.
If this is the small syns, the driver mounting is not symmetrical
Not clear -- why would I want it to be symmetrical? (or is it just to minimize any expanse between bracing?)
I was actually most concerned about the back panel resonating (it's the largest panel, and made the most hollow sounds when you rap on it). The front panel seems pretty rigid, as it is several laminated layers and has a rigid waveguide structure dominating it. The compression driver is similarly braced to the back wall, with felt layers between it and the back panel in the currently built version. For the next (shelf ported) version, I'm planning something like the sketch in the first post above, with the back of the woofers braced to stiffeners and horizontal braces. The brace behind the woofers (which also connects to side walls as well as back) would also help the upper center area where the woofers and waveguide both mount, though, but that wasn't the original concern...
Bushmeister,
Thanks for the suggestions. But how are you interpreting the tweeter response plots with/without sorbothane? -
The distance (or percentage) between the fundamental and desired curves doesn't seem to have improved much if at all, and if the level in the 'without' curve were reduced/EQd to the same curve as the 'with' I'd expect the harmonic distortion curves for 'without' to drop faster than 1:1? There also seems to be in increase in higher order distortions for the 'with (that might just be different background noise in the measurement though...). There is also loss in output near the driver's lower frequencies, and about a 15dB loss near 20kHz! Is the sorbothane thicker than the original gasket, maybe affecting the throat dimensions?
Edit: Or maybe I'm interpreting wrong -- are those panel output measurements, as opposed to tweeter response measurements?
Thanks for the suggestions. But how are you interpreting the tweeter response plots with/without sorbothane? -
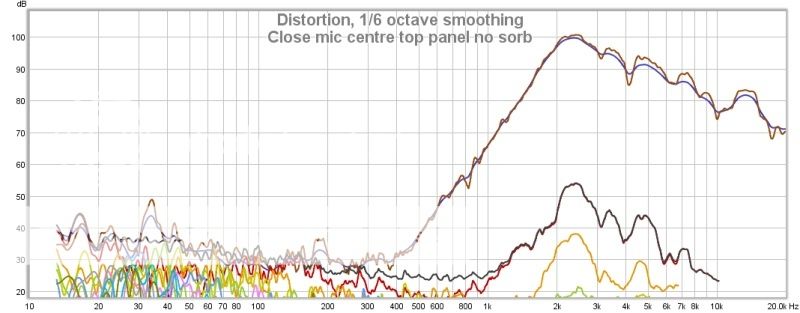
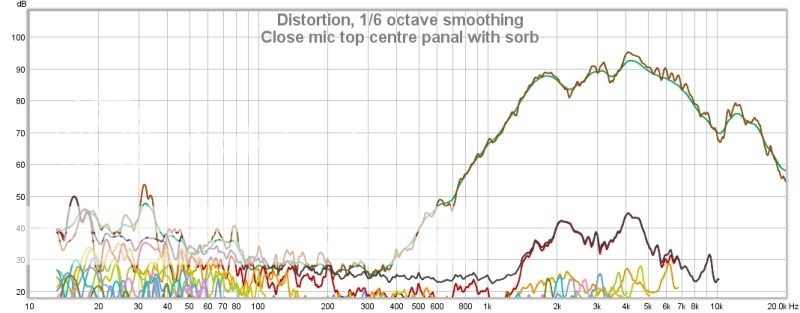
The distance (or percentage) between the fundamental and desired curves doesn't seem to have improved much if at all, and if the level in the 'without' curve were reduced/EQd to the same curve as the 'with' I'd expect the harmonic distortion curves for 'without' to drop faster than 1:1? There also seems to be in increase in higher order distortions for the 'with (that might just be different background noise in the measurement though...). There is also loss in output near the driver's lower frequencies, and about a 15dB loss near 20kHz! Is the sorbothane thicker than the original gasket, maybe affecting the throat dimensions?
Edit: Or maybe I'm interpreting wrong -- are those panel output measurements, as opposed to tweeter response measurements?
Last edited:
Hi Bwaslo - those are panel output measurements!
Tweeter measurements were unchanged with and without sorbothane!
Tweeter measurements were unchanged with and without sorbothane!
Ah, ok, that makes sense then, sorry. I'm surprised the panel could radiate anything measurable at the higher frequencies, but I guess there'd be no way to keep tweeter output out of the measurement entirely (it's a mic, not an accelerometer, right?)
- Status
- Not open for further replies.
- Home
- Loudspeakers
- Multi-Way
- Box damping/bracing question... and maybe an idea?