Gafhenderson, if you don't mind, I would use your 3d to add a question to yours..
Is it possible to take off the 'head' of the dallas II, makind it a kind of dallas III?
![]()
![]()
thats exactly what i was thinking of doing!
Very pretty - in fact it already has been done with the Austin:
Other than the obvious significant complication of fabricating curved shapes (regardless of materials/method used), don't automatically assume that "fairing" the length of internal pathway will improve sonic performance over hard/sharper folds.
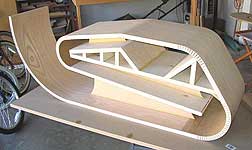
Other than the obvious significant complication of fabricating curved shapes (regardless of materials/method used), don't automatically assume that "fairing" the length of internal pathway will improve sonic performance over hard/sharper folds.
Very pretty - in fact it already has been done with the Austin:
![]()
Other than the obvious significant complication of fabricating curved shapes (regardless of materials/method used), don't automatically assume that "fairing" the length of internal pathway will improve sonic performance over hard/sharper folds.
i've found a local man with one of those electronic shape cutter contraptions who will give me very good rates, so whichever design + driver i finally commit to, it actually will work out easier for me to have it fabricated in single stacked sheets. the curved shape may also allow it to pass unnoticed under the WAF radar.
i've found a local man with one of those electronic shape cutter contraptions who will give me very good rates, so whichever design + driver i finally commit to, it actually will work out easier for me to have it fabricated in single stacked sheets. the curved shape may also allow it to pass unnoticed under the WAF radar.
if you're talking about fabricating a front mouthed horn with a pretty enough finish to pass unnoticed under the WAF-dar using the stacked lamination ( "layertone" ) method, you might want consider not only the substantial time involved in prepping for a decent paint or veneer finish, but also the outrageously poor material yield on a shape such as this one, that has very few parts that can be nested
the electronic shape cutter contraption ( I assume you mean CNC) could be much better utilized in fabricating jigs around which Kerf-core, rubber ply, etc could be wrapped
if it sounds like I'm not a fan of this technique, which often employs MDF - yep, and no apologies for that
if you're talking about fabricating a front mouthed horn with a pretty enough finish to pass unnoticed under the WAF-dar using the stacked lamination ( "layertone" ) method, you might want consider not only the substantial time involved in prepping for a decent paint or veneer finish, but also the outrageously poor material yield on a shape such as this one, that has very few parts that can be nested
the electronic shape cutter contraption ( I assume you mean CNC) could be much better utilized in fabricating jigs around which Kerf-core, rubber ply, etc could be wrapped
if it sounds like I'm not a fan of this technique, which often employs MDF - yep, and no apologies for that
all i know is that it's a laser, and it needs to be special treated wood that is suitable for use with lasers.
i'd not pay the extra expense for practise boxes that i'm messing around with now but for the finally design i'd be happy to pay for it.
Just a thought...........
Think of a ring of wood, multiples stacked to make a cylinder, to cut this using cnc / laser is wasteful........
Divide each ring into segments, glue the segments so the joints at say 45deg to each other, from curves to strait sections can be formed as 'J' sections, the majority of the straits can then be cut on a table saw. Yes its slightly more complex to make / glue up a horn enclosure in this manner.
Thinking about it a little more, one could have just the curved sections cnc/laser'd and flat material joined in to make the strait sections........BIG saving in cost there.
Think of a ring of wood, multiples stacked to make a cylinder, to cut this using cnc / laser is wasteful........
Divide each ring into segments, glue the segments so the joints at say 45deg to each other, from curves to strait sections can be formed as 'J' sections, the majority of the straits can then be cut on a table saw. Yes its slightly more complex to make / glue up a horn enclosure in this manner.
Thinking about it a little more, one could have just the curved sections cnc/laser'd and flat material joined in to make the strait sections........BIG saving in cost there.
Chrisb, what do you think abouy simply taking off the head of the dallas II? I guess it want be detrimental from a sound point of view, since the dallas III does the same thing.
Ervin
I can't see any problem with that
Just a thought...........
Think of a ring of wood, multiples stacked to make a cylinder, to cut this using cnc / laser is wasteful........
Divide each ring into segments, glue the segments so the joints at say 45deg to each other, from curves to strait sections can be formed as 'J' sections, the majority of the straits can then be cut on a table saw. Yes its slightly more complex to make / glue up a horn enclosure in this manner.
Thinking about it a little more, one could have just the curved sections cnc/laser'd and flat material joined in to make the strait sections........BIG saving in cost there.
start doing the math on the programming, machining and assembly time for the tight nesting required for high yield on any curved shape, and most particularly horns such as these, and you quickly gain appreciation for rubberply / Kerfore and vacuum bagging
no matter how you do it - CCM
Don't you think it would affect the sound?
not detrimentally so, compared to the diffraction effects at edges of front baffles cabinet
does this look approximate to kirishima's tuning/performance?
its got a AN super 8 neo in this sim. if this is approx, i'll put the numbers into the MJK worksheet.
its got a AN super 8 neo in this sim. if this is approx, i'll put the numbers into the MJK worksheet.
An externally hosted image should be here but it was not working when we last tested it.
start doing the math on the programming, machining and assembly time for the tight nesting required for high yield on any curved shape, and most particularly horns such as these, and you quickly gain appreciation for rubberply / Kerfore and vacuum bagging no matter how you do it - CCM
true enough Chrisb, the other way, if cost is 'no object' would be to buy veneer and bag over forms, a friend and i did this a few years ago to make a small run of custom skateboard decks, though in the end it turned out easier to make them with an ultra high density foam core, Pu at 240kg m/3, skinned in glass/carbon.
On my 'to do' list is a pair of 'bookshelf' speakers for my bedroom using this foam, though I've got to get the Emken out the way first
http://www.homeblown.co.uk/HD/
Very pretty - in fact it already has been done with the Austin:
![]()
That is actually a variation on Dallas II. I'm pretty sure that Ron had little or no input into that one, unlike the Austin 166 that layertone did.
dave
all i know is that it's a laser, and it needs to be special treated wood that is suitable for use with lasers.
I talked with a fellow that had access to that CNC techto do FH flat-paks and we decided that the materials limitation made it impractical to proceed.
dave
Chrisb, what do you think abouy simply taking off the head of the dallas II? I guess it want be detrimental from a sound point of view, since the dallas III does the same thing.
I would do that as a matter of course -- removing all of the redundant voids. Taking the big chunk off the front should decrease the diffraction signature.
dave
- Status
- This old topic is closed. If you want to reopen this topic, contact a moderator using the "Report Post" button.
- Home
- Loudspeakers
- Full Range
- Dallas II vs Kirishima