I know Mr Bung.
I think the advice I gave is good. 120 V at low distortion will be ideal. A RC chain should do it ( 3 x I suspect is a minimum ). Loose about 30 V per section. Not really sure what the best corner frequecy should be. I am tempted to say 40 Hz. That might mean less sections. Alas I don't have a motor handy to try. People who build valve amps should be able to do this. Also the reliability should be excellent. LC might be expensive without real need. The distortion of the motor core is about 0.5%, that sort of dictates where you should be or a bit lower ( Synchronous 8% +, that is why TD124 is begining to be better ). The motor hates 1/3rd and odd harmonics ( causes bearing chatter ).You can use a lamp or a number of lamps to be the R. That will give you some voltage regulation. In the old days iron filement lamps were used. You can use a single lamp into the transfomer if in USA and using step up, it also protects the transformer. Dull red glow usually is ideal, same principle as a Wien Oscillator. Most USA houses have 230 V if required. BTW the 230 V US voltage is cleaner as it hasn't the Neutral shift of the 115-0-115.
Never believe the Folklaw about flat top waves on the mains. It's just how it is regulated. The transformers are allowed to saturate a bit. Doubtless how we draw current is the extra distortion.
I think the advice I gave is good. 120 V at low distortion will be ideal. A RC chain should do it ( 3 x I suspect is a minimum ). Loose about 30 V per section. Not really sure what the best corner frequecy should be. I am tempted to say 40 Hz. That might mean less sections. Alas I don't have a motor handy to try. People who build valve amps should be able to do this. Also the reliability should be excellent. LC might be expensive without real need. The distortion of the motor core is about 0.5%, that sort of dictates where you should be or a bit lower ( Synchronous 8% +, that is why TD124 is begining to be better ). The motor hates 1/3rd and odd harmonics ( causes bearing chatter ).You can use a lamp or a number of lamps to be the R. That will give you some voltage regulation. In the old days iron filement lamps were used. You can use a single lamp into the transfomer if in USA and using step up, it also protects the transformer. Dull red glow usually is ideal, same principle as a Wien Oscillator. Most USA houses have 230 V if required. BTW the 230 V US voltage is cleaner as it hasn't the Neutral shift of the 115-0-115.
Never believe the Folklaw about flat top waves on the mains. It's just how it is regulated. The transformers are allowed to saturate a bit. Doubtless how we draw current is the extra distortion.
re: penny pinched motor. The E50. In Bung's book he does mention that the TD124 designer did intentionally choose a weaker motor for the TD124 in his quest to keep drive train vibes/noise to a minimum. Some might think he went a little too far in the direction of 'weak'. 10 watts.
I could also complain that the case work on the E50 does not assemble accurately. It requires some alignment in order to accomplish two things; 1: get the self aligning bushings in-line with the rotor shaft once all the pieces are in place...and....2: to get the rotor cerntered to the stator core.
3rdly, a gripe. I have seen some stator core laminates so severely warped that it becomes quite difficult to get a good rotor shaft-to-bushing alignment once the upper and lower casings are assembled and tightened down. Other examples, however, appear nearly perfect in condition and assemble with hardly any need of 'tuning' the alignment of rotor to bushings and rotor to stator core.
So, yes. There was obviously too much cost cutting going on with the motor. And once that motor maker got their production up to full speed it seems likely, if not apparent, that there was some defective product that escaped whatever their quality processes were and found their way into a finished product.
If I wanted to create a "super" TD124, the first component I'd look into improving would be that E50. And by improving I mean replacing with another example of the shaded pole induction motor. One with greater output and with a more precise build. Got any?
re: 3-in-One oil. I've no doubt that many different sorts of lubes may work in the motor. and if 3-in-one is mineral based, it should match with what's already in the Oilite bronze bushings when it comes out of that foundry in The UK, where Oilite bronze gets produced.
Perhaps Thorens custom ordered their porous bronze stock to be impregnated with a lube of their choice before any machining was done. Detailed information like that is lost with the people who worked at Thorens in Sainte-Croix. People who had worked there and lived out their life spans and are now mostly lost to the ages.
I have replaced motor bushings with new replacements and I have made use of the existing bushings after a thorough cleaning. These days I lean toward keeping the old bushings in use.
I have tried some different lubes within the E50. From thick to thin. I know that differential lube (for spiral bevel gears) is too viscous. (the motor came upt to speed far too slowly) I also tried some red and runny ATF (like 5 wt)...and that seemed to work fine...but I did not leave it that way for long. The 20 wt turbine oil I'm using now seems to be problem free. But different thinner lubes seem possible provided there is compatibility with those porous bronze bushings. I'm not certain about minimum viscosities. How thin is too thin....maybe 5wt was pushing the limits of thin.
re: the belt. Yes, this does introduce an inaccuracy into the drive. The stretch of the belt with every cog pulse of the motor. (keep in mind that the shaded pole motors do slip their cogging a bit) I suspect that the audible end effect of the belt is a slight 'softness' to the leading edge of transients. And I don't take that as a negative. The sound reproduction of a healthy TD124 doing its thing is quite beguiling to my ears.
So, if I were to work toward creating a 'super' TD124, as noted above, I would retain the belt and stepped pulley arrangement just as Thorens produced it. But that motor just seems to be its biggest weakness. And I would work on that before looking at alternate platter materials...which is another worthwhile topic.
-Steve
Concerning the better motor the Papst Thorens used as replacement for the E50 give better results I have done speed measurements they are in the a posting somewere. With a three phase drive the results are better the 100hz vibration is then gone.
I think the problems with motorspeed are over when using the new sinterbushings from Simone , yes this E50 motor is difficult to revise then a 301 ,401, l 75 motor.
The belt tension has influence on the noise , and steppulley bearing noise .
I selected a 6mm belt which gives the best results against the NOS original one.
Volken
Just to be clear. Given the highest voltage you can reliably use and the lowest distortion on that supply plus 3 in 1 oil you have that wonderful new motor. My girlfriend in the 1970's dad was Mike Hailwoods mechanic. He advised me to blueprint an engine and then leave it alone. He taught me how to use kitchen scales to do it and to be careful with connecting rods. He said that alone would be worth 10 to 15 % power. It would also mean I didn't have to tell the insurance company. He said if you don't and then tune the engine it will snap. He also went on to say it would use less fuel. I doubted his words until part owning a Triumph racing twin. It would do more than 130 MPH. On stripping the engine nothing unusual could be seen to explain the power. I was later told they were just best tollerence components. The Triumph problem was said to be crank bending or valve bounce. It wasn't. It was connecting rods not at 90 degrees. This was worth 7500 rpm and nothing would go snap. These turntables are the same. It's the little things that matter. If you own an old Triumph sometimes it works better at 6 volts. The 12 volt " upgrade " produced too many spare sparks ( cam lobe and voltage ). Thanks Lucas. It holded pistons.
Just to be clear. Given the highest voltage you can reliably use and the lowest distortion on that supply plus 3 in 1 oil you have that wonderful new motor. My girlfriend in the 1970's dad was Mike Hailwoods mechanic.
I'll give it a try...the 3-in-1 lube (the thinner stuff). I can alter voltage levels that I feed to the motor. In increments of 5 volts up or down.

with one of these. It is a rather large 400 watt transformer with multiple steps on the output side. Apart from being able to manipulate output voltage, whatever 'isolation' it achieves by the addition of one more transformer between the component and the mains isn't audibly apparent.
I tend to feed the TD124 115 vac and have my eddy brake adjusted / centered to it.
What is apparent when using this device is that the E50 alters its rpm with voltage level changes. It can step the voltage up as high as 150 vac or step down to as low as 5 vac. And with 5 volt increments between those extremes. On the E50 I've set voltage as high as 125 vac and as low as 90 vac. The lower setting does not maintain operational speed.
So, thusly equipped I'll crack open the motor again, clean out the 20 wt lube and make the bushings and felts wet with 3-in-1.
Volken:
Yes, I recall your experiments ith the 3-phase Pabst. It does look promising. But just how much superior in terms of actual operation and normal listening does it present itself?
-Steve
Thorens TD124 E50 motor powersupply measurements
Are preparing for a HiFi show next weekend, we let hear the difference between a Garrard 401 and Thorens TD124 turntable .Also a demo with the turntable powersupply to let the people hear the difference .
Some measurements I did here at home at our mains supply 225 Volt the TD124 E 50 motor connected , reference the third harmonic 150 hz with mains -38db with the powersupply on 210 Volt -53 db.
The the improvement in the sound is not subtle , black background, more detail , better and stable soundstage.
Volken
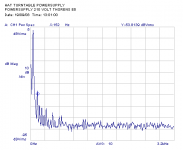
Are preparing for a HiFi show next weekend, we let hear the difference between a Garrard 401 and Thorens TD124 turntable .Also a demo with the turntable powersupply to let the people hear the difference .
Some measurements I did here at home at our mains supply 225 Volt the TD124 E 50 motor connected , reference the third harmonic 150 hz with mains -38db with the powersupply on 210 Volt -53 db.
The the improvement in the sound is not subtle , black background, more detail , better and stable soundstage.
Volken
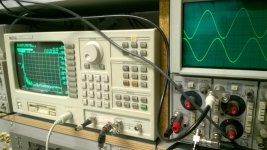
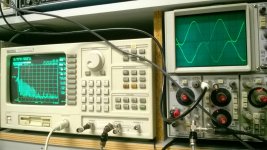
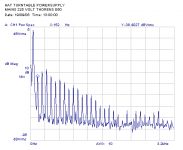
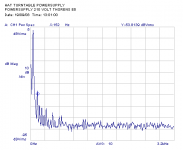
OK. I guess Rubber grommets having low compliance compared to belt will have little effect on cogging and belt stretching noise. Is there any advantage of motor hanging on three 45 degree springs like garrard 301/401 motor ? If there are; then that can be incorporated in TD124.
Regards.
Regards.
Really good thing about hysterisis motor is no real cogging. If you rotate the rotor there are no jumps. The major defeat of this motor type is a great advantage for us. This is why I say the TD124 motor is exactly the motor you need. If no one does the harmonic distortion reduction idea soon I will have to borrow a TD124. My friend has 5 he isn't using. I might even try 350 VAC as it is a typical valve voltage. If we call the motor 1 K and I want to loose 120 V ( 240 V start ) that suggests 1 K/3 or 330 R. If we make the corner frequency 60 Hz the resistors need be 220R at a good guess. 12 uF. Motor caps should work well. That's ball park values I would start with. Doubtless it won't be those as the load is reactive. 7 watt resistors are cheap enough. As said 40 Hz filter might be better as the slope is slightly better. Remember the voltage will drop if 40 Hz and this needs to be factored in. The results should be very good for the low cost. 230 V people you can do it cheaper. Remember you are at 50 Hz so different values of R. The average regenerative PSU for this is about 50% efficient if class AB. 60 % on a good example. This would be about the same.
There are a few problems. 3 % THD is considered a good device. 1% can be found. Then there is the frequency which is said to be +/- 0.5% at best. That's OK again but not as good as domestic mains power. What I suggest should produce levels well below 1% for very little money. You may also find the inverter runs at 110V rather than 120V we would like ( our even 126V we might run ). It could be a lot of money for less good.
Really good thing about hysterisis motor is no real cogging. If you rotate the rotor there are no jumps. The major defeat of this motor type is a great advantage for us. This is why I say the TD124 motor is exactly the motor you need. If no one does the harmonic distortion reduction idea soon I will have to borrow a TD124. My friend has 5 he isn't using. I might even try 350 VAC as it is a typical valve voltage. If we call the motor 1 K and I want to loose 120 V ( 240 V start ) that suggests 1 K/3 or 330 R. If we make the corner frequency 60 Hz the resistors need be 220R at a good guess. 12 uF. Motor caps should work well. That's ball park values I would start with. Doubtless it won't be those as the load is reactive. 7 watt resistors are cheap enough. As said 40 Hz filter might be better as the slope is slightly better. Remember the voltage will drop if 40 Hz and this needs to be factored in. The results should be very good for the low cost. 230 V people you can do it cheaper. Remember you are at 50 Hz so different values of R. The average regenerative PSU for this is about 50% efficient if class AB. 60 % on a good example. This would be about the same.
The Papst E50 motor is not a hysteresis motor but a induction motor otherwise it won't work with the speed regulation .
How about the quality of pure sine wave inverter?
I did this but you create a lot off unwanted noise , switching freq., in your system better build a Wien oscillator or something with a EXAR 2206 generator.
Volken
The original TD124 motor is hysterisis, having taken apart a modern Papst I am not sure what it is. A hybrid is my thought. The great defect of the hysterisis is it's wonderful advantage. The " elastic " link between rotating field and rotor allows the motor to slow under load without excessive vibration. After about 20 minutes this becomes stable, oil and heat is the reason as best I know ( drag ). After that if the load and voltage is constant, so is the speed strictly linked to mains frequency. Garrard fitted a +/- 3% speed control to allow for 190 to 270 V ( 95 to 135 V ) and 50 or 60 Hz. It wasn't for golden ears, Garrard said usually frequency is very good as it was used for clocks and it was set by law. It also tells the National Grid to bring in more capacity if it slows, thus it is retained. This is still run by mathamatians to this very day and not completely computer controlled. The voltage has to be fixed to say speed is constant. 50 Hz drives the turntable harder for a given voltage as the motor inductance counts in the mix. The motor works best between 40 and 60 Hz. If building a 78 transcription turntable use the 50 Hz pully and +/- 10 Hz.
I have a big Papst motor I am playing with which is 100% a hysterisis. A hysterisis motor is said to be effectively synchronous at low load. The reason 1/3 rd harmonic is so harmfull is that it rotates against the rotor direction. Second harmonic will not. Thus a cascade of passive filters will deal with 1/3 rd and 1/5 th and the evil 1/9 th ( 1/9 th is very high on typical mains ), the 2nd which the filter almost ignores is not as important.
I have a big Papst motor I am playing with which is 100% a hysterisis. A hysterisis motor is said to be effectively synchronous at low load. The reason 1/3 rd harmonic is so harmfull is that it rotates against the rotor direction. Second harmonic will not. Thus a cascade of passive filters will deal with 1/3 rd and 1/5 th and the evil 1/9 th ( 1/9 th is very high on typical mains ), the 2nd which the filter almost ignores is not as important.

The lamp might require that the voltage is above 230V at the filter. It's function is to reduce voltage variation ( 30 % I found, 6 V becomes 2 V ) . 60 watt type if 230V is where to start. These are the filement type. USA types I am not sure about. 230V people use the 115V winding and no transformer if lucky.
The original TD124 motor is hysterisis, having taken apart a modern Papst I am not sure what it is. A hybrid is my thought. The great defect of the hysterisis is it's wonderful advantage. The " elastic " link between rotating field and rotor allows the motor to slow under load without excessive vibration. After about 20 minutes this becomes stable, oil and heat is the reason as best I know ( drag ). After that if the load and voltage is constant, so is the speed strictly linked to mains frequency. Garrard fitted a +/- 3% speed control to allow for 190 to 270 V ( 95 to 135 V ) and 50 or 60 Hz. It wasn't for golden ears, Garrard said usually frequency is very good as it was used for clocks and it was set by law. It also tells the National Grid to bring in more capacity if it slows, thus it is retained. This is still run by mathamatians to this very day and not completely computer controlled. The voltage has to be fixed to say speed is constant. 50 Hz drives the turntable harder for a given voltage as the motor inductance counts in the mix. The motor works best between 40 and 60 Hz. If building a 78 transcription turntable use the 50 Hz pully and +/- 10 Hz.
I have a big Papst motor I am playing with which is 100% a hysterisis. A hysterisis motor is said to be effectively synchronous at low load. The reason 1/3 rd harmonic is so harmfull is that it rotates against the rotor direction. Second harmonic will not. Thus a cascade of passive filters will deal with 1/3 rd and 1/5 th and the evil 1/9 th ( 1/9 th is very high on typical mains ), the 2nd which the filter almost ignores is not as important.
Nigel you creates more uncertainty about the original Thorens E50 motor this motor is a squirrel-cage motor same as the Garrard 301,401 and Lenco L75 motor , not a hysteresis the last locked to the mains frequency.
About the Papst outerrotor motor people think they are all hysteresis motors but they are not , depents how the outerrotor is made. The replacement Papstmotor for the E50 is a squirrel-cage motor!
From the Papstmotors on the picture there are two hystereris rest squirrel-cage .
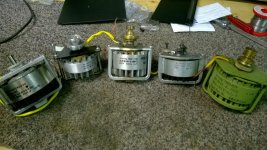
The outcome is the same. We get the same with Beam Tetrode and Petode valves. Important thing to know the same observations work for all. I studdied and have qualifications as an electrical engineer with electronics endorsement. We looked at all these types and it wasn't yet 1974. It won't help you get better results to know the exact trade name. If true synchronous it will lock to frequency until the voltage too low. These motors react to frequency and voltage. That's all there is to know. I do not know other than the original motor so can't say if this is all of them. The other thing is to reject text book ways of thinking as Thorens , Lenco , and Garrard did. They found this route gave lower vibration. The main thing text books suggest is phase shift in the original type is less than ideal. That has to be true. Of the perhaps 10 TD124's I've looked at all were Garrard type. I am assuming 90 % are.
There is a similar text book misunderstanding with the vacuum cleaner motors. These are DC motors run with AC and refer to a time when DC was a possible option. Folk law has it that the people who make vacuum cleaners are too lazy to design induction types. This isn't true. The universal motor actually has advantages for the job it does. It is wasteful of energy, that is true.
There is a similar text book misunderstanding with the vacuum cleaner motors. These are DC motors run with AC and refer to a time when DC was a possible option. Folk law has it that the people who make vacuum cleaners are too lazy to design induction types. This isn't true. The universal motor actually has advantages for the job it does. It is wasteful of energy, that is true.
DAC1282 seems easier with -125db THD.
- Home
- Source & Line
- Analogue Source
- Restoring and Improving A Thorens TD-124 MKII