Thanks haven't seen this one before but there are a couple paper crimpers out there that are similar. Also those squeezers that professional hair salons use to squeeze hair dye out of tubes are pretty much perfect
Member
Joined 2003
I'm very impressed by the ingenuity posters have shown when devising ways to corrugate, or otherwise pattern, their ribbons. My admittedly limited research on the subject has uncovered more evidence suggesting the corrugation does not help than evidence that it does. I certainly don't want to devalue the contributions of those who have developed nice ways to pattern their ribbons, but is there compelling evidence that it's worth the effort?
I will, of course, shamelessly copy the approaches of those who have come up with nice ways to corrugate the drivers if it is shown to help, but at the moment I remain distracted by the evidence which suggests it doesn't buy you much. Have I just missed the set of data making it clear we all ought to ruffle our ribbons?
Eager to be shown ignorant...
Few
For my 1"x45" ribbons some years ago, I experimented with several foil patterns...plain flat foil, corrugated, foil pressed with patterns (window screen & fabric patterns). The main difference was that corrugated ribbons did not "twist in the gap" as much as the others when driven with strong LF signals...so corrugated was selected.
For resonance control, the ribbons were suspended from wool felt pads at the ends and at the 1/3 length points.
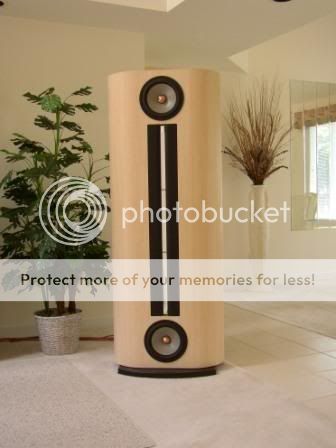
Here's my contribution to the corrugator show.
Never guess which one was my first?
I would very much like to find a finer pitch corrugator roller.
None of mine can produce the fine pitch of Apogee Scintilla midrange.
Well, I can always make one e.g. by 3D printing..
Never guess which one was my first?
I would very much like to find a finer pitch corrugator roller.
None of mine can produce the fine pitch of Apogee Scintilla midrange.
Well, I can always make one e.g. by 3D printing..
Attachments
You guys have done some great work.....Thanks for the info...When well we see All base driver diyed.....Like the Apogee...thay sound so good an i am only useing the smallest ones the stages.... i have found the sweet spot to at the top of the ribbon...for base an tweeter/mid...the biger the panels the ear in out of the sweet spot ...so all that needed is 21/2'X 16"base driver 3' off the floor...Just onemans O-pine .....goodluck
Hanski. I take it that you know about this man i Sweden. He is making ribbons to your specs. I am using one pair he has produced right now. Quality is excellent. Right now I am concentrating on the bass corrugator.
DahlbergAudioDesign
Pictures added. Use the arrow on the right side
Here are, as promised, some pictures from my playroom: https://picasaweb.google.com/tsundsd/October292012?authkey=Gv1sRgCPv0qfqR9oKrAw#5804518306051868834
DahlbergAudioDesign
Pictures added. Use the arrow on the right side
Here are, as promised, some pictures from my playroom: https://picasaweb.google.com/tsundsd/October292012?authkey=Gv1sRgCPv0qfqR9oKrAw#5804518306051868834
Last edited:
Here's my contribution to the corrugator show.
Never guess which one was my first?
I would very much like to find a finer pitch corrugator roller.
None of mine can produce the fine pitch of Apogee Scintilla midrange.
Well, I can always make one e.g. by 3D printing..
Exactly right. The one on eBay is the only one I've seen that looks right for the corrugations for the MR and TW. I've looked at quite a few of the paper crimpers, and they all have quite wide corrugations, not even close to the Apogee. Those dough rollers posted a few above look promising. I'll search that out a bit
Last edited:
DahlbergAudioDesign site has great info for ribbon builder. He has a fine pitch corrugator:
http://www.dahlbergaudiodesign.se/del3/images/korrvals.jpg
Thanks AudioquestM-40 for the corrugator ebay link. Well, it doesn't look like a fine pitch corrugator but I can always ask it from the seller.
http://www.dahlbergaudiodesign.se/del3/images/korrvals.jpg
Thanks AudioquestM-40 for the corrugator ebay link. Well, it doesn't look like a fine pitch corrugator but I can always ask it from the seller.
DahlbergAudioDesign site has great info for ribbon builder. He has a fine pitch corrugator:
http://www.dahlbergaudiodesign.se/del3/images/korrvals.jpg
Thanks AudioquestM-40 for the corrugator ebay link. Well, it doesn't look like a fine pitch corrugator but I can always ask it from the seller.
They look like that dough roller don't they?
Hello all,
I haven't yet made a fine pitch corrugation roller.
I'm still open for all kinds of suggestions where to find proper gears suitable for corrugation.
Btw, here's a link for Apogee Grand ribbon:
http://d1xw7fnq30zy05.cloudfront.net/uploads/image/image/703809/scaled_IMG_1515.JPG
It shows an interesteresting pattern in multitrace ribbon.
I haven't yet made a fine pitch corrugation roller.
I'm still open for all kinds of suggestions where to find proper gears suitable for corrugation.
Btw, here's a link for Apogee Grand ribbon:
http://d1xw7fnq30zy05.cloudfront.net/uploads/image/image/703809/scaled_IMG_1515.JPG
It shows an interesteresting pattern in multitrace ribbon.
Hello.
I see that I'm figuring in this thread so.....
The corrugation wheels was made by a mechanical company in Sweden that
specialises in gears. Quite expensive if you just want one pair but as always
prices go down with numbers. I always recomend people asking to try and find
a fine mechanical school nearby. They somtimes think that it's an interesting
project, a lot cheaper as well. My first pair was done that way.
"The tall neodymium ribbon". Part 1
There will be some rewriting of the article in the future, sometime next year.
Just some minor adjustments for things learned since it was first publiched.
I see that I'm figuring in this thread so.....
The corrugation wheels was made by a mechanical company in Sweden that
specialises in gears. Quite expensive if you just want one pair but as always
prices go down with numbers. I always recomend people asking to try and find
a fine mechanical school nearby. They somtimes think that it's an interesting
project, a lot cheaper as well. My first pair was done that way.
"The tall neodymium ribbon". Part 1
There will be some rewriting of the article in the future, sometime next year.
Just some minor adjustments for things learned since it was first publiched.
Last edited:
Thanks for the info Dahlberg,
would you like to share your thoughts about fine pitch corrugation vs. coarse pitch corrugation?
My experience is the finer the pitch the better (foil only ribbon). I also tighten the foil so that corrugations are pulled almost flat. This takes away the bass rattle of a flat foil and has very little resonances compared with deep corrugations.
Btw, here's a picture of amp update. Hypex Ncores making friends with UCD modules.
would you like to share your thoughts about fine pitch corrugation vs. coarse pitch corrugation?
My experience is the finer the pitch the better (foil only ribbon). I also tighten the foil so that corrugations are pulled almost flat. This takes away the bass rattle of a flat foil and has very little resonances compared with deep corrugations.
Btw, here's a picture of amp update. Hypex Ncores making friends with UCD modules.
Attachments
The only experience of fine/cource corrugation I have is from a short ribbon
project where the cource one gave a higher output due to less shrinkage and
obviously a lower resistance. I haven't done any other tests with pure foil
ribbons and different corrugations besides that one so I'm not of much help in
that department. On the longer ribbons the fine corrugation is a winner in every
way, except finding/manufactoring the gears.
project where the cource one gave a higher output due to less shrinkage and
obviously a lower resistance. I haven't done any other tests with pure foil
ribbons and different corrugations besides that one so I'm not of much help in
that department. On the longer ribbons the fine corrugation is a winner in every
way, except finding/manufactoring the gears.
Somewhere in the dark past .. I think i recall reading about the usage of a fine smear of vaseline / petroleum jelly to the ribbon diaphram of some decca london /dk30 type tweeters
Ring any bells for anybody else ??
not sure about this idea as i suspect it would add some noticeable amount of mass to the ribbon...
Ring any bells for anybody else ??
not sure about this idea as i suspect it would add some noticeable amount of mass to the ribbon...
I have couple questions about arranging magnets when constructing ribbon tweeter.
Here's a link http://www.saunalahti.fi/~hellmann/index_files/DiskanttiProto.PDF to a 3D pdf-file.
Is that correct way to arrange magnets?
And the other question is how do you manage put the magnets to rows so that they're touching each other without using glue? Does it have something to do with shape or are the polarities flipped?
Here's a link http://www.saunalahti.fi/~hellmann/index_files/DiskanttiProto.PDF to a 3D pdf-file.
Is that correct way to arrange magnets?
And the other question is how do you manage put the magnets to rows so that they're touching each other without using glue? Does it have something to do with shape or are the polarities flipped?
This is the way you are supposed to mount them if you are going for two rows.
They absolutly do not want to sit like this so it's quite a struggle to mount them.
They will repell (with significant force since there are a lot of them) sideways
and be attracted by the ones on the other steelbar.
If you are unlucky they can actually flip and jump to the nearest magnet and sometimes
breaks when doing so as well (buy a few extras).
I used to use a rubber strip squeezed in between the magnets to prevent them
from rotating in place, they need to be able to rotate to flip so.....
Now I'm gluing all magnets with slow hardening 2-comp epoxy since I came to
the conclusion that I would never remount any magnetsystems.
I see that you are from Finland, if you read Swedish there is an old thread of
mine at "hififorum.nu"
HiFiForum.nu - En lång neodymium-banddiskant.
where you most likely can find answers to a lot of your questions.
Ps. Hope that this wasn't to much OT.
They absolutly do not want to sit like this so it's quite a struggle to mount them.
They will repell (with significant force since there are a lot of them) sideways
and be attracted by the ones on the other steelbar.
If you are unlucky they can actually flip and jump to the nearest magnet and sometimes
breaks when doing so as well (buy a few extras).
I used to use a rubber strip squeezed in between the magnets to prevent them
from rotating in place, they need to be able to rotate to flip so.....
Now I'm gluing all magnets with slow hardening 2-comp epoxy since I came to
the conclusion that I would never remount any magnetsystems.
I see that you are from Finland, if you read Swedish there is an old thread of
mine at "hififorum.nu"
HiFiForum.nu - En lång neodymium-banddiskant.
where you most likely can find answers to a lot of your questions.
Ps. Hope that this wasn't to much OT.
Member
Joined 2003
Here, single magnets are used across the face of each pole. Using long and wide magnets on stout pole pieces reduces the tendency to repel and flip. Aluminum strips attached to the poles bridge the sides of the magnets and hold them in place.
Gently slide one end of the long magnets onto each pole and push them into place, otherwise they will "slam" onto the poles and break. Placing a wooden spacer in the gap during assembly helps prevent accidents.
Gently slide one end of the long magnets onto each pole and push them into place, otherwise they will "slam" onto the poles and break. Placing a wooden spacer in the gap during assembly helps prevent accidents.
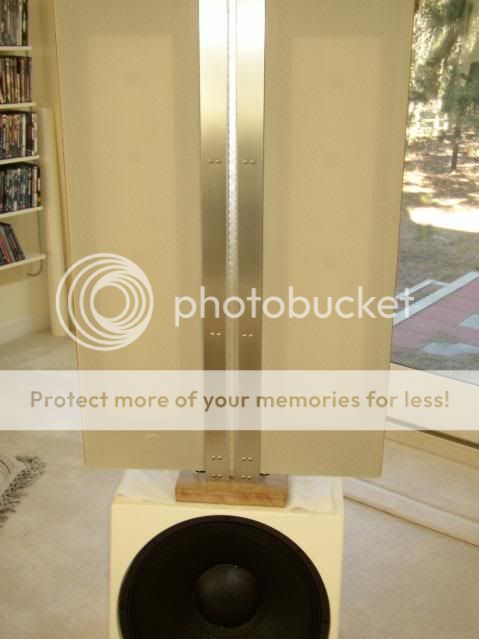
- Status
- This old topic is closed. If you want to reopen this topic, contact a moderator using the "Report Post" button.
- Home
- Loudspeakers
- Planars & Exotics
- Suggestions for aluminium ribbon damping?