In mechanical analogue terms,
Mmd = mass
Cms = spring
Rms = damper
Rather similar to a car suspension really.
Huuummmmm... yes, but but a car suspension has a spring and a oil bath damper and the damper is flabby !
Huuummmmm... yes, but but a car suspension has a spring and a oil bath damper and the damper is flabby !
What does flabby mean?
What does flabby mean?
Flabby=humor+viscosity
Flabby=humor+viscosity
Ok. Because I fail to see how a damper can be flabby by how I would understand it.
Ah, a welcome thought from McBean. Yes, I often make the comparison - many aspects analogous but the role is quite different.In mechanical analogue terms,
Mmd = mass
Cms = spring
Rms = damper
Rather similar to a car suspension really.
For a car, the object of design is to take the "inputs" from the road and turn them into no movement for the car (except for super low frequency inputs such as hills).
I drove a Maserati for a decade or so that could take Toronto's everywhere speed bumps at say 40 MPH while other cars had to slow to say 15 MPH. Great suspension. My motorcycles have even more sophisticated suspensions. Vast engineering sophistication goes into car suspensions unlike the crude Rice-Kellogg drivers we use. If you studied motorcycle shock absorbers, you'd discover maybe 10 design choices. There are maybe 5 performance-related choices made by those designing the simple spring holding a motorcycle front wheel. Anything comparable in the suspension of our sub drivers?
Yet despite the engineering scope available to car suspension designers (including few constraints on weight, size, manufacturing, even price), nobody will be making cars into the future without active suspension. For speakers, that means motional feedback.
For speakers where sound quality is the principle goal, the outcome we want to simulate is: for all signals in its passband, what design adds the least noise. See the odd relation to car suspensions?
Aside from motional feedback (which I am returning to experiment with in next few months after I've devised good test methods*), I'd say the less a driver acts like a weight on a string or has any voice of its own like tuned boxes, the better, at least for producing clean sound.
Ben
*at Bell, I used to take polaroid pictures of storage scope traces of pulses.... seems like a million years ago
Last edited:
Ah, a welcome thought from McBean. Yes, I often make the comparison - many aspects analogous but the role is quite different.
For a car, the object of design is to take the "inputs" from the road and turn them into no movement for the car (except for super low frequency inputs such as hills).
I drove a Maserati for a decade or so that could take Toronto's everywhere speed bumps at say 40 MPH while other cars had to slow to say 15 MPH. Great suspension. My motorcycles have even more sophisticated suspensions. Vast engineering sophistication goes into car suspensions unlike the crude Rice-Kellogg drivers we use. If you studied motorcycle shock absorbers, you'd discover maybe 10 design choices. There are maybe 5 performance-related choices made by those designing the simple spring holding a motorcycle front wheel. Anything comparable in the suspension of our sub drivers?
Yet despite the engineering scope available to car suspension designers (including few constraints on weight, size, manufacturing, even price), nobody will be making cars into the future without active suspension. For speakers, that means motional feedback.
For speakers where sound quality is the principle goal, the outcome we want to simulate is: for all signals in its passband, what design adds the least noise. See the odd relation to car suspensions?
Aside from motional feedback (which I am returning to experiment with in next few months after I've devised good test methods*), I'd say the less a driver acts like a weight on a string or has any voice of its own like tuned boxes, the better, at least for producing clean sound.
Ben
*at Bell, I used to take polaroid pictures of storage scope traces of pulses.... seems like a million years ago
Yes, can we imagine that the spring is the suspension of the loudspeaker and its box internal air acts like the damper ?
Is it a correct image ?
First of all, there are the parameters of the driver in isolation hanging midair (not quite "isolation" but for a crude shaking-cardboard mechanism, close enough) and then the driver when located in a housing.Yes, can we imagine that the spring is the suspension of the loudspeaker and its box internal air acts like the damper ?
Is it a correct image ?
The mass of the driver is the easy part: it is the weight of the moving assembly.
The spring is the part that restores the moving part to neutral location, principally the spider, a hunk of starched fabric (or modern equivalent). Yuck, no Maserati suspension here.
The damping of the driver mostly arises from back-EMF, where the voice coil (which resides in a very strong magnetic field) is essentially shorted by the amp (which has very low output impedance, say .01 Ohm, which is like shorting a 4 Ohm voice coil* **). The gooey rubber outer surround damps a little bit, but depends on how heavy it is in relation to how heavy is the moving mass. Damping, when linear, is a kind of favourable feedback and so that's good.
Air is the problem. Just too thin for a shaking-cardboard mechanism (Saran-Wrap drivers, ESLs, make much more sense). Unless constrained in a sealed box (a really good idea) or tuned in a tuned box (a really bad idea), has little role in controlling the hunk of cardboard. Too bad. No impedance match.
Ben
*short your driver with a piece of wire and see what the cone feels like when you gently push on it
**with motional feedback, the amp acts like -4 Ohms (yes, you read that right)
Last edited:
First of all, there are the parameters of the driver in isolation hanging midair (not quite "isolation" but for a crude shaking-cardboard mechanism, close enough) and then the driver when located in a housing.
The mass of the driver is the easy part: it is the weight of the moving assembly.
The spring is the part that restores the moving part to neutral location, principally the spider, a hunk of starched fabric (or modern equivalent). Yuck, no Maserati suspension here.
The damping of the driver mostly arises from back-EMF, where the voice coil (which resides in a very strong magnetic field) is essentially shorted by the amp (which has very low output impedance, say .01 Ohm, which is like shorting a 4 Ohm voice coil* **). The gooey rubber outer surround damps a little bit, but depends on how heavy it is in relation to how heavy is the moving mass. Damping, when linear, is a kind of favourable feedback and so that's good.
Air is the problem. Just too thin for a shaking-cardboard mechanism (Saran-Wrap drivers, ESLs, make much more sense). Unless constrained in a sealed box (a really good idea) or tuned in a tuned box (a really bad idea), has little role in controlling the hunk of cardboard. Too bad. No impedance match.
Ben
*short your driver with a piece of wire and see what the cone feels like when you gently push on it
**with motional feedback, the amp acts like -4 Ohms (yes, you read that right)
In the past amplifiers damping was pretty low, now we have huge DF capable amps... why not using a small sized tuned box with a very low BR port tuning ?
In the past amplifiers damping was pretty low, now we have huge DF capable amps... why not using a small sized tuned box with a very low BR port tuning ?
Your reasoning is OK, but the values are uncooperative.
As long as there's been negative feedback, amp output impedance (AKA damping factor) have been a lot more favourable than a driver could even use.... without the help of motional feedback.
The problem is that familiar Rice-Kellogg drivers don't have enough motor power relative to unsprung weight (to use a term familiar to all motorcycle enthusiasts) for damping to mean a whole lot.
What motorcycle designers did (ignoring the life-style obsessed folks at Harley-Davidson) is reduce unsprung weight using light spokes (or mag wheels), disk brakes, smaller diameter wheels, aluminum bits and pieces, etc. Car designers used half-shaft brakes, light u-joints, etc. (I also had a Lotus).
But driver designers were playing to an audience of sim users with basic goals like flat response, peak loudness, and tolerable ringing. Not McBean's fault.
... and then there is Lowther.
Ben
Last edited:
Your reasoning is OK, but the values are uncooperative.
As long as there's been negative feedback, amp output impedance (AKA damping factor) have been a lot more favourable than a driver could even use.... without the help of motional feedback.
The problem is that familiar Rice-Kellogg drivers don't have enough motor power relative to unsprung weight (to use a term familiar to all motorcycle enthusiasts) for damping to mean a whole lot.
What motorcycle designers did is reduce unsprung weight using mag wheels, disk brakes, aluminum bits and pieces, etc.
But driver designers were playing to an audience of sim users with basic goals like flat response, peak loudness, and tolerable ringing. Not McBean's fault.
... and then there is Lowther.
Ben
You need an adequate cone rigidity to resist to the transcients of the pistonic acutation of the low frequencies... it mean weight.
You need an adequate cone rigidity to resist to the transcients of the pistonic acutation of the low frequencies... it mean weight.
Now you are getting into design. Instead of slavish adherence to the shaking-cardboard model, that is exactly what is needed today.
But as long as you have a Rice-Kellogg driver, you need stiffness to accurately transmit the coil power to the ends of the cone. If you have motor force all over, you don't need much stiffness at all.
Every heard of Magnepan?
Some day Rice-Kellogg drivers will only be seen in museums along with Model-T Fords from about the same period in history.
Ben
Hi,
Seems this thread has been hijacked by a load of
people talking utter pseudotechnobabble nonsense.
The OP should go sealed or vented depending
on the driver parameters, (he probably does not
want a tapped horn using a 70Hz Fs 96dB driver).
Get with the program and stop talking drivel about basics.
rgds, sreten.
Seems this thread has been hijacked by a load of
people talking utter pseudotechnobabble nonsense.
The OP should go sealed or vented depending
on the driver parameters, (he probably does not
want a tapped horn using a 70Hz Fs 96dB driver).
Get with the program and stop talking drivel about basics.
rgds, sreten.
Now you are getting into design. Instead of slavish adherence to the shaking-cardboard model, that is exactly what is needed today.
But as long as you have a Rice-Kellogg driver, you need stiffness to accurately transmit the coil power to the ends of the cone. If you have motor force all over, you don't need much stiffness at all.
Every heard of Magnepan?
Some day Rice-Kellogg drivers will only be seen in museums along with Model-T Fords from about the same period in history.
Ben
No, only Martin Logan pannels.
Hi,
Seems this thread has been hijacked by a load of
people talking utter pseudotechnobabble nonsense.
The OP should go sealed or vented depending
on the driver parameters, (he probably does not
want a tapped horn using a 70Hz Fs 96dB driver).
Get with the program and stop talking drivel about basics.
rgds, sreten.
OK
Thanks for the replies! I recently acquired a scope, so I'll do some measuring. I'm sure a scope will make it easy to measure.
What parameters should I measure? Maybe Fs, and if it's too high, pack it up? Am i looking for Fs=30Hz or so? What else should I measure?
Qes and Vas?
You can use Limp to measure all the T&S you need !
http://www.artalabs.hr/AppNotes/LIMP_Tutorial_Version_2_4_English.pdf
For the shake-the-earth bass you need the largest cone with the largest Xmax possible.
Last edited:
Ben - do as I say and not as I do, right?
Let's look at what you use for bass.
Your previous subwoofer was a Klipschhorn. The frequency response is plagued by resonances all through the passband. It uses a conventional antique moving coil driver with low excursion potential and no motional feedback. It's not a good design by modern standards.
Your current subwoofer (a) is an antique small sealed box design using a conventional moving coil driver with low excursion potential and no motional feedback. It's not a good design by modern standards.
Your current subwoofer (b) is an antique conventional woofer with very low excursion potential and no motional feedback on an open baffle hybrid. It's an absolutely terrible design by modern standards.
Your arguments against resonances, small sealed boxes (bigger is better), conventional moving coil drivers and lack of motional feedback are ALL violated in your own subwoofer choices. Not only that but you prefer antique items that don't perform up to today's standards in both driver and enclosure technology.
And then there's the esl panel argument. If esl panels are so great where's your esl panel subwoofer? You talk about esl extensively here on the subwoofer forum, say it's so much better than moving coil drivers but you don't use it yourself because esl cannot produce bass.
Esl can produce midbass and up, and you do use esl panels for that purpose but they are not perfect by any means. Your antique 1 meter square esl panels have horrifying dispersion issues. This is why Martin Logan attempts to keep their panels narrow and curved. Your esl panels are by contrast the worst possible design choice.
Esl can do some things a bit better than moving coil drivers but they do other things a lot worse. And since they can't do bass at all, why do continue to constantly talk about esl on the subwoofer forum, especially when you don't use esl subwoofers yourself?
You have claimed all your various personal subwoofers are great, despite the fact that they violate ALL the evils that you constantly rail against. They don't employ any of the technologies that you advocate (esl, motional feedback), they do employ 60 year old technology that is not up to date with today's standards and yet you insist that no one should use anything without esl and motional feedback.
You are suggesting there are problems that don't exist and providing no solutions, in fact the equipment you use if far more plagued by these evil issues than most. This is hypocrisy at it's worst.
Driver designers are not "playing to an audience of sim users with basic goals". Clearly you don't understand the industry at all. The diy market is so small it's negligible and has no impact whatsoever on driver designers. Drivers are sold en masse to companies that produce speakers and items with built in speakers with a very small amount diverted to raw driver sales for diy purposes.
Driver designers are constantly riding the wave of new technology, which mainly comes in the form of newer, better, higher heat resistant glues and newer (sometimes better) cone materials. If there was a better way to do things and it was even remotely comparable with conventional methods in terms of value it would be made.
The idea that the OEM driver industry is being held back by a bunch of sim using diy morons is incredibly naive.
Let's look at what you use for bass.
Your previous subwoofer was a Klipschhorn. The frequency response is plagued by resonances all through the passband. It uses a conventional antique moving coil driver with low excursion potential and no motional feedback. It's not a good design by modern standards.
Your current subwoofer (a) is an antique small sealed box design using a conventional moving coil driver with low excursion potential and no motional feedback. It's not a good design by modern standards.
Your current subwoofer (b) is an antique conventional woofer with very low excursion potential and no motional feedback on an open baffle hybrid. It's an absolutely terrible design by modern standards.
Your arguments against resonances, small sealed boxes (bigger is better), conventional moving coil drivers and lack of motional feedback are ALL violated in your own subwoofer choices. Not only that but you prefer antique items that don't perform up to today's standards in both driver and enclosure technology.
And then there's the esl panel argument. If esl panels are so great where's your esl panel subwoofer? You talk about esl extensively here on the subwoofer forum, say it's so much better than moving coil drivers but you don't use it yourself because esl cannot produce bass.
Esl can produce midbass and up, and you do use esl panels for that purpose but they are not perfect by any means. Your antique 1 meter square esl panels have horrifying dispersion issues. This is why Martin Logan attempts to keep their panels narrow and curved. Your esl panels are by contrast the worst possible design choice.
Esl can do some things a bit better than moving coil drivers but they do other things a lot worse. And since they can't do bass at all, why do continue to constantly talk about esl on the subwoofer forum, especially when you don't use esl subwoofers yourself?
You have claimed all your various personal subwoofers are great, despite the fact that they violate ALL the evils that you constantly rail against. They don't employ any of the technologies that you advocate (esl, motional feedback), they do employ 60 year old technology that is not up to date with today's standards and yet you insist that no one should use anything without esl and motional feedback.
You are suggesting there are problems that don't exist and providing no solutions, in fact the equipment you use if far more plagued by these evil issues than most. This is hypocrisy at it's worst.
Driver designers are not "playing to an audience of sim users with basic goals". Clearly you don't understand the industry at all. The diy market is so small it's negligible and has no impact whatsoever on driver designers. Drivers are sold en masse to companies that produce speakers and items with built in speakers with a very small amount diverted to raw driver sales for diy purposes.
Driver designers are constantly riding the wave of new technology, which mainly comes in the form of newer, better, higher heat resistant glues and newer (sometimes better) cone materials. If there was a better way to do things and it was even remotely comparable with conventional methods in terms of value it would be made.
The idea that the OEM driver industry is being held back by a bunch of sim using diy morons is incredibly naive.
The OP should go sealed or vented depending
on the driver parameters, (he probably does not
want a tapped horn using a 70Hz Fs 96dB driver).
Just to be very clear about this, my simulated examples were to show that high fs on it's own is not an insurmountable issue. Fs higher than the enclosure's low frequency knee is often desirable.
The fact is that the driver suggested in post 2 is not a good subwoofer driver but it's not fs that precludes it from subwoofer use, it's got much more important issues like low xmax.
Thanks, I'm reading everything.
Streten, I'm going sealed (more on that below).
I'm not worried about the hijack. I'm picking the cherries of knowledge. At least I have enough sense and knowledge to sift through everything.
I've been playing with online simulators and many different combinations of TS parameters. That along with everything I'm learning, I want a sealed sub. I need 15 - 40 Hz response at about 105dB SPL. That should complement my current system. My woofer at the moment complements my Celestions beautifully. I just need the extra low down rumble that's lacking.
I'm going to put both my 10s in as small a box as possible to allow eq to give me good response to 15Hz with 140W. Don't shoot me down here - I haven't done any calculations yet. If I achieve 20Hz, I'll be very happy.
I've learned that my two 10s will do fine. I suspect they have fairly low resonance, and I know for a fact they can move decently far. I'm going with sealed because of the extra damping, faster response and much better predictably.
Importantly, I'm going to build a very solid box, and I'll mount the subs facing down and backward, and face the one which shows the most distortion downward. I'll design the eq filter for compensation and a fixed response.
This project could take between a week and a year. But I'll post all my progress as it happens.
Streten, I'm going sealed (more on that below).
I'm not worried about the hijack. I'm picking the cherries of knowledge. At least I have enough sense and knowledge to sift through everything.
I've been playing with online simulators and many different combinations of TS parameters. That along with everything I'm learning, I want a sealed sub. I need 15 - 40 Hz response at about 105dB SPL. That should complement my current system. My woofer at the moment complements my Celestions beautifully. I just need the extra low down rumble that's lacking.
I'm going to put both my 10s in as small a box as possible to allow eq to give me good response to 15Hz with 140W. Don't shoot me down here - I haven't done any calculations yet. If I achieve 20Hz, I'll be very happy.
I've learned that my two 10s will do fine. I suspect they have fairly low resonance, and I know for a fact they can move decently far. I'm going with sealed because of the extra damping, faster response and much better predictably.
Importantly, I'm going to build a very solid box, and I'll mount the subs facing down and backward, and face the one which shows the most distortion downward. I'll design the eq filter for compensation and a fixed response.
This project could take between a week and a year. But I'll post all my progress as it happens.
I'm going to design my enclosure according to my driver specifications, and I want to filter the input as in the attached images. I'm really just looking for that sub-bass, everything else is well sorted.
Now, I do have a quick question. How do you design for 2 drivers with quite different parameters? As I said, I am going for a sealed enclosure. My guess would be that I can make the enclosure as big as possible, finding a balance between physical limits and response curve shape. Or I can build an enclosure with two sealed chambers? Which would give the best performance? The problem with two chambers for me is simply size and shape. Is it really worth the effort of building two chambers, or will one be fine?
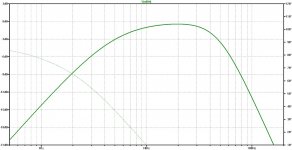
Now, I do have a quick question. How do you design for 2 drivers with quite different parameters? As I said, I am going for a sealed enclosure. My guess would be that I can make the enclosure as big as possible, finding a balance between physical limits and response curve shape. Or I can build an enclosure with two sealed chambers? Which would give the best performance? The problem with two chambers for me is simply size and shape. Is it really worth the effort of building two chambers, or will one be fine?
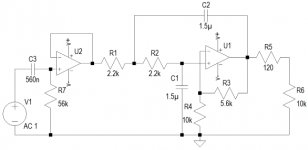
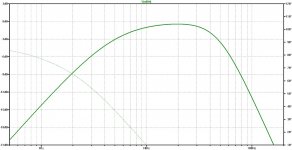
You need two chambers (or two separate boxes). Ideally you also need to power and eq them separately. But the latter is not as important as the former.
Thanks. I'll aim for a similar Fs final for both then. Unfortunately they're each 4 ohm, and i only have amplifiers for 8 ohm. I did over-design the amplifiers, so I'll see what they can do. I'll need to power each from it's own supply as well, but i already have the two supplies. I think the amplifiers can drive enough to get 220W out of 4 ohm, so that would be plenty. I'll do some measurements in the near future. Again, thanks for the tips!
Ok, so I designed the amplifiers to use a parallel BJT output, but they're only using one side of that at the moment. I have spare transistors to use, so it's all good news. The heatsinks are large enough for the power as well. And I did the simulations and calculations, and I will indeed get 220W per amplifier. So here goes a 440W 2x10" sub. It's not going to be a quick one though. I don't suspect I'll have it done in the near future, WAF playing a big role. 
- Status
- This old topic is closed. If you want to reopen this topic, contact a moderator using the "Report Post" button.
- Home
- Loudspeakers
- Subwoofers
- Subwoofer build - where do I start?