I should look at data sheets more often. It turns out that the LM3886 will take as much as +/- 42V. I hooked it up a couple of RT-204 transformers and was able to atain 82 RPM with 28VAC, but just, and the amp got quite hot. The Kenwood did better but With the RT-204s there was a high frequency riding on the waveform. With the single lower voltage transformer the wave is clean. I donno. Is 78 RPM worth the trouble?
This is the setup I use to oil my spindle bearing sleeves:
On the right is a refrigeration vacuum pump. They are inexpensive compared to lab quality oil-free pumps, but obviously a little oil isn't going to compromise the process. The chamber is a 6" PVC pipe coupling. I've glued 3/8" acrylic sheet to the bottom and I seal the removable acrylic top with petroleum jelly. I submerge the sleeves in oil. I run the pump for about 10 minutes. After the air is pumped out oil fills the voids when the pump is turned off.
I love to watch the air boil out of the bearing sleeves. Here's a little video:
Vacuum Spindle Bearing Oiling
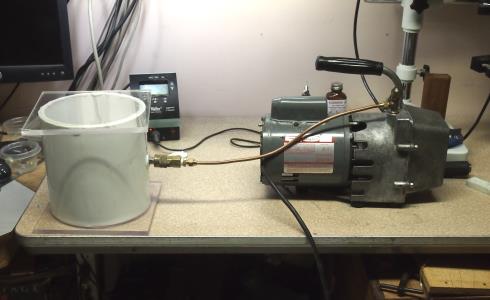
On the right is a refrigeration vacuum pump. They are inexpensive compared to lab quality oil-free pumps, but obviously a little oil isn't going to compromise the process. The chamber is a 6" PVC pipe coupling. I've glued 3/8" acrylic sheet to the bottom and I seal the removable acrylic top with petroleum jelly. I submerge the sleeves in oil. I run the pump for about 10 minutes. After the air is pumped out oil fills the voids when the pump is turned off.
I love to watch the air boil out of the bearing sleeves. Here's a little video:
Vacuum Spindle Bearing Oiling
A lot more air than I expected.
And it lasts for a long time.
Yeah, even after 10 minutes there are still bubbles, but remember, those big bubbles would be microscopic at atmospheric pressure.
Indeed, I use the process to get deep penetration of shellac in small wood fittings.When impregnating wood, they use a Vac Vac process.
Have you tried that?
Doing it twice for better penetration of the oil?
That might be an interesting experiment. Logic would suggest that on the second stage the bubbling would commence at the rate it left off after the first. Next time I'll try it.
Have you tried to use the setup to remove old oil from spindle bearing sleeves, then used your process to infuse new oil?
This is the setup I use to oil my spindle bearing sleeves:
I run the pump for about 10 minutes. After the air is pumped out oil fills the voids when the pump is turned off.
Tons of good info- thanks!!
I've been struggling with my Rek-O-Kut that is also idler wheel drive (My Thorens 124 is long gone). Motor noise is a big problem. I've tried a lot of different motors - including the lovely Studer reel to reel motors - but all are too noisy.
So Douglas, it's nice to see you using the Hurst 300 RPM motor. I had been looking at those too, but didn't get one being afraid of the noise. Are you still thinking 600 RPM might be better?
I've been struggling with my Rek-O-Kut that is also idler wheel drive (My Thorens 124 is long gone). Motor noise is a big problem. I've tried a lot of different motors - including the lovely Studer reel to reel motors - but all are too noisy.
So Douglas, it's nice to see you using the Hurst 300 RPM motor. I had been looking at those too, but didn't get one being afraid of the noise. Are you still thinking 600 RPM might be better?
You guys still playing around with these klunky old tables.. lol
Joking aside the trend towards 300rpm motors in belt drive tables back in the day was driven by the observation and measurements that the noise spectra of lower speed motors is displaced downwards. Look at the noise spectra of the E50 used in the TD-124 and you will find spurs well above 1kHz, lower speed motors probably do not exhibit noise this far up into the spectrum.
Ultimately if you can push all of this extraneous noise sufficiently below the medium's noise floor (say 10dB) it becomes a non-issue.
Pano how are you determining that these motors are all too noisy and what is the drive mechanism, belt or idler? (Note that I am not saying they are not too noisy, just curious how the determination was made.)
I'm taking a short digital interlude. (Bought a Sony HAP-Z1ES recently to replace the old multi-box solution.)
Joking aside the trend towards 300rpm motors in belt drive tables back in the day was driven by the observation and measurements that the noise spectra of lower speed motors is displaced downwards. Look at the noise spectra of the E50 used in the TD-124 and you will find spurs well above 1kHz, lower speed motors probably do not exhibit noise this far up into the spectrum.
Ultimately if you can push all of this extraneous noise sufficiently below the medium's noise floor (say 10dB) it becomes a non-issue.
Pano how are you determining that these motors are all too noisy and what is the drive mechanism, belt or idler? (Note that I am not saying they are not too noisy, just curious how the determination was made.)
I'm taking a short digital interlude. (Bought a Sony HAP-Z1ES recently to replace the old multi-box solution.)
Hey Kevin - I just use my ears! If I can hear the motor from across the room, I reckon it's too loud. No joke, that loud.
I have a little DC motor and servo that I pulled from a plastic Techinics TT. It's a little noisy with no load, but as a.wayne points out - just the pull from the belt calms it down. I love it, it's soooooo quiet. Can't get the servo to run it fast enough, tho.
I have a little DC motor and servo that I pulled from a plastic Techinics TT. It's a little noisy with no load, but as a.wayne points out - just the pull from the belt calms it down. I love it, it's soooooo quiet. Can't get the servo to run it fast enough, tho.
Aha, I had an SL-23 long ago that had a good dc servo, and later a Pink Triangle that used the same exact motor, but not the Technics drive board, never the same speed from record to record or across a single side, drove me nuts...
You will probably need to change the pulley, the motor is brushed and higher speed operation is limited by motor design - you can only increase the voltage safely to a limited extent or maybe not at all - I take it that even 45 rpm setting is not fast enough for 33 rpm with your platter?
You will probably need to change the pulley, the motor is brushed and higher speed operation is limited by motor design - you can only increase the voltage safely to a limited extent or maybe not at all - I take it that even 45 rpm setting is not fast enough for 33 rpm with your platter?
Impregnating Oilite
Instead of going to the cost and trouble of using AC vacuum pumps, a Mightyvac at about 40 dollars from Harbor Freight is fine. It draws to 27 inches Hg and a small container is provided. Besides, it has plenty of other uses around the home and garage. Heating the oil also helps.
Instead of going to the cost and trouble of using AC vacuum pumps, a Mightyvac at about 40 dollars from Harbor Freight is fine. It draws to 27 inches Hg and a small container is provided. Besides, it has plenty of other uses around the home and garage. Heating the oil also helps.
Nope. I need about a 56% speed increase. Going from a 7.75" subplater to the 12" outside of the Rek-O-Kut platter. Gets up to speed within 1/2 a turn, tho.I take it that even 45 rpm setting is not fast enough for 33 rpm with your platter?
It's a brushed DC motor, you think?
This is the motor I chose:
It's 59mm diameter, 7.5 watts, with 8.5 oz-in torque
This is the one I'm considering:
It's 49mm diameter, 3 watts, with 2.7 oz-in torque.
Both come in 117 and 24 volt versions as well as 300 and 600 RPM. I'm thinking that the smaller motor may have lower vibration levels. Also If I use the drive system that employs the existing idler drive ring the motor ends up in the corner of the chassis. The smaller motor with the diamond mounting flange will leave more space between the motor and chassis edge. I think I'll stick with 300 RPM.
The vibration is not audible but you can feel it. Actually to hear anything at all I had to turn off anything nearby that had a transformer or fan as well as florescent lights. I had to connect a long cord to the motor so its transformer could be in an adjacent room. I used the MK II motor suspension. The vibration was difficult to feel on the chassis and nothing came through the speaker. However if this motor were driving an idler directly I doubt the vibration could be controlled.
As Kevin said, the low RPM lowers the frequency of the noise making it easier to control. The permanent magnet design makes it possible to get enough torque at low RPM at the expense of cogging. Reducing the motor drive voltage doesn't reduce the vibration significantly. You can feel the cogging when you rotate the motor without power applied. I had a thought. What if the motor were made with electromagnets. It could be provided a high current to get the system up to speed then reduced for lower vibration.
Indeed there are many inexpensive Chinese pumps on the market. I chose the Dayton pump because I'd experience with it and it's made in the USA. I bought it used on Ebay for a price similar to the Chinese pumps and it came with a set of refrigeration gauges, hoses and connectors.
I Don't think that would work. Since oil is not compressible I doubt that it is expandable the way air is so vacuum won't drive out the oil.
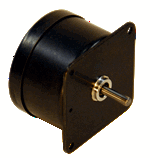
It's 59mm diameter, 7.5 watts, with 8.5 oz-in torque
This is the one I'm considering:
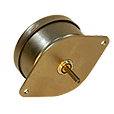
It's 49mm diameter, 3 watts, with 2.7 oz-in torque.
Both come in 117 and 24 volt versions as well as 300 and 600 RPM. I'm thinking that the smaller motor may have lower vibration levels. Also If I use the drive system that employs the existing idler drive ring the motor ends up in the corner of the chassis. The smaller motor with the diamond mounting flange will leave more space between the motor and chassis edge. I think I'll stick with 300 RPM.
The vibration is not audible but you can feel it. Actually to hear anything at all I had to turn off anything nearby that had a transformer or fan as well as florescent lights. I had to connect a long cord to the motor so its transformer could be in an adjacent room. I used the MK II motor suspension. The vibration was difficult to feel on the chassis and nothing came through the speaker. However if this motor were driving an idler directly I doubt the vibration could be controlled.
As Kevin said, the low RPM lowers the frequency of the noise making it easier to control. The permanent magnet design makes it possible to get enough torque at low RPM at the expense of cogging. Reducing the motor drive voltage doesn't reduce the vibration significantly. You can feel the cogging when you rotate the motor without power applied. I had a thought. What if the motor were made with electromagnets. It could be provided a high current to get the system up to speed then reduced for lower vibration.
Indeed there are many inexpensive Chinese pumps on the market. I chose the Dayton pump because I'd experience with it and it's made in the USA. I bought it used on Ebay for a price similar to the Chinese pumps and it came with a set of refrigeration gauges, hoses and connectors.
Have you tried to use the setup to remove old oil from spindle bearing sleeves, then used your process to infuse new oil?
I Don't think that would work. Since oil is not compressible I doubt that it is expandable the way air is so vacuum won't drive out the oil.
The bearings are probably sintered.
This is a very high pressure and high temperature process.
The sintered bearing will be resistant to heating, I suspect at least 200°C will do absolutely no harm.
Try cooking the sintered bearing in the oven set to 150°C, or even 175°C.
Some of the old oil will run out.
The sintered bearing may even tolerate 300°C, but I cannot give any warranty if you try going that high.
This is a very high pressure and high temperature process.
The sintered bearing will be resistant to heating, I suspect at least 200°C will do absolutely no harm.
Try cooking the sintered bearing in the oven set to 150°C, or even 175°C.
Some of the old oil will run out.
The sintered bearing may even tolerate 300°C, but I cannot give any warranty if you try going that high.
- Home
- Source & Line
- Analogue Source
- Restoring and Improving A Thorens TD-124 MKII