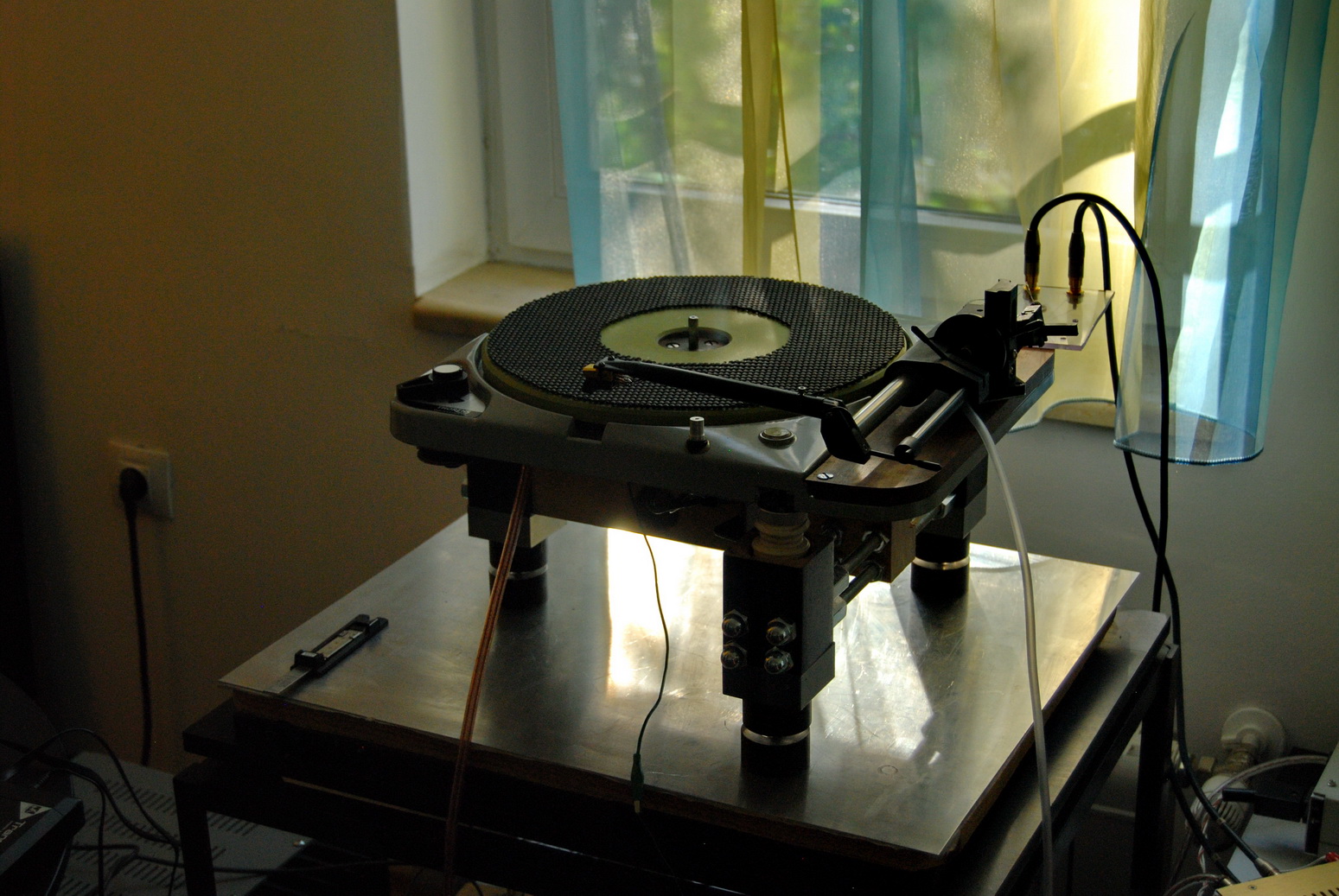
This is an interesting approach and one, I think, that could serve to illustrate something I am coming around to think.
First, an observation about the tinkering I've done on my own:
The quieter the motor runs. The quieter and smoother the belt/stepped pulley/idler wheel runs. The less one is tempted to categorize this model in the same league with other idlers known to produce obvious rumble.
Why? Because at a certain level of performance, it becomes apparent that this model does not produce any obvious rumble. At least not rumble that can be heard through the speakers on a needle drop into the lead-in groove.
Once the TD124 is operating to this level of performance, plinth selection becomes less of an issue. High mass. Medium mass. Naked? To mushroom or not. These things matter less to the sound output of the turntable.
And the key to obtaining this level of performance in my early model units has been centered around the motor and its bushings and thrust.
So the first I would check on the above pictured Thorens is to find a record to play and then drop the stylus down into the lead-in groove to see/hear if there is any evidence of rumble. And this would tell me if the experimenting that ultimately lead to this design of support, was chasing substantial audible improvements or if it had been chasing ghosts down blind alleys.
If no rumble, then the process that led to the design might be valid and worth a try. If rumble, then the result was achieved on false information and the sound quality of it being touted would not be comparable to that of a properly running TT in any design of plinth.
About the missing outer platter:
It is common to find these players with damaged or lost outer platters. The lightweight aluminum shell is easily dented and by minimal force. So among the latest generation of tuners it becomes somewhat popular to simply discard the outer platter and work without.
But this outer platter was more than just a disc jockey tool. It served to isolate the record from the bearing. A true-spinning outer platter on fresh rubber pucks and with a good standard mat should not be discounted. This piece may not be the "weak link" that some would suggest that it is.
-Steve
I use the upper aluminum platter with a Merill-Scillia mat (cork, rubber and lead amalgam) and am very happy with the result. I do recommend running with the upper platter if available. Sadly I do not have one for my second 124, but it would have it if I did.
I will second the rumble comment, my 124/II is extremely quiet, no audible rumble that was not there on the original recording. It took quite a lot of effort to get it there, the second one was much easier..
I will second the rumble comment, my 124/II is extremely quiet, no audible rumble that was not there on the original recording. It took quite a lot of effort to get it there, the second one was much easier..
Vibrating motor solution.
Kevin,
As per everything AC a solution can be had after rebuilding the motor to reduce any possible vibration to essentially "0".
And for all that think that it is virtually impossible, consider that the well known Airpax/Thomson motors typically sound best when fed 72-85 VAC. Hmmm, wonder what it could be.
Not shown in the previous pix is my pride and joy () a very mint TD-124/II. It was almost as if it had spent the past 40yrs in a time capsule - which in a sense it had since it was in a console with a lid that the owner never opened after the very early 1970s..
The motors in these tables vibrate pretty badly, but the belt, good motor mounting bushings and a massive plinth keep the whole thing pretty quiet. Careful tweaking does help. Lots of torque comparatively speaking, when warm it is fully up to speed in about 1 revolution of the platter.
Kevin,
As per everything AC a solution can be had after rebuilding the motor to reduce any possible vibration to essentially "0".
And for all that think that it is virtually impossible, consider that the well known Airpax/Thomson motors typically sound best when fed 72-85 VAC. Hmmm, wonder what it could be.
Have a lead on a stamped upper platter for my series I table, wish me luck!![]()
Luck.
Interesting about the upper platters. I've seen some that appear have been formed by "spinning". Others appear to have been stamped. The spun ones will indicate concentric tool marks typical of that process. The stamped ones will not have any tooling marks.
-Steve
@ Steve:
I've noticed the variation in upper platters as well, mine has concentric tooling marks consistent with your description of a spun platter.
@ Nanook:
I tried operating the E50 (shaded 4 pole induction motor) in my table on reduced line voltage to see what effect it had on vibration, it helped slightly, and completely killed the dynamics.. Same effect could be achieved by operating the motor on the next higher voltage tap.. (125V - 150V tap) I've managed to quiet both of my TD-124 to the extent that most recordings have a much higher LF noise floor than either of these tables. From a performance perspective I've found running at normal line voltages results in the best overall perceived performance.
I've noticed the variation in upper platters as well, mine has concentric tooling marks consistent with your description of a spun platter.
@ Nanook:
I tried operating the E50 (shaded 4 pole induction motor) in my table on reduced line voltage to see what effect it had on vibration, it helped slightly, and completely killed the dynamics.. Same effect could be achieved by operating the motor on the next higher voltage tap.. (125V - 150V tap) I've managed to quiet both of my TD-124 to the extent that most recordings have a much higher LF noise floor than either of these tables. From a performance perspective I've found running at normal line voltages results in the best overall perceived performance.
"Oo, oo, oo I wanna be just like you..." (a quote from King Louie)
A very wise man suggested to me to use 2 variacs for AC induction motors. One for each pair of windings on an induction motor. Adjust both variacs (let's call the first one #1, the 2nd one with the capacitor call #2) to the same level where the motor quiets down significantly. Obviously there should be no interconnection of the winding pair at the motor. Just ensure that both variacs are fed from the same input voltage source. Then adjust #2 until less noise (again). This should provide almost the "ultimate" way of driving the AC motors. But the cost of 2 variacs is not cheap by any means. Now full current capability of #2 windings will be improved and be more efficient.
These are only my thoughts and could be completely wrong, however I don't think so. Another possible way would to use a 2 channel digital signal generator at the correct 50Hz/60Hz as needed that can allow for phase adjustment and output of both channels individually (perhaps a digital mono volume for each variac?).
I've decided that when I grow up, I wannabe just like you
As always a great thread to read.
@ Nanook:
I tried operating the E50 (shaded 4 pole induction motor) in my table on reduced line voltage to see what effect it had on vibration, it helped slightly, and completely killed the dynamics.. Same effect could be achieved by operating the motor on the next higher voltage tap.. (125V - 150V tap) I've managed to quiet both of my TD-124 to the extent that most recordings have a much higher LF noise floor than either of these tables. From a performance perspective I've found running at normal line voltages results in the best overall perceived performance.
A very wise man suggested to me to use 2 variacs for AC induction motors. One for each pair of windings on an induction motor. Adjust both variacs (let's call the first one #1, the 2nd one with the capacitor call #2) to the same level where the motor quiets down significantly. Obviously there should be no interconnection of the winding pair at the motor. Just ensure that both variacs are fed from the same input voltage source. Then adjust #2 until less noise (again). This should provide almost the "ultimate" way of driving the AC motors. But the cost of 2 variacs is not cheap by any means. Now full current capability of #2 windings will be improved and be more efficient.
These are only my thoughts and could be completely wrong, however I don't think so. Another possible way would to use a 2 channel digital signal generator at the correct 50Hz/60Hz as needed that can allow for phase adjustment and output of both channels individually (perhaps a digital mono volume for each variac?).
I've decided that when I grow up, I wannabe just like you
As always a great thread to read.
Nanook, interesting idea.. And I have plenty of variacs and a spare motor to experiment with once I rebuild it.. So at some point as schedule permits I will have a look at it.
I believe in fact that it would be possible to run one winding fixed and vary the other one +/- a few percent to see what effect that has..(Each winding independently end to end can operate from 100 - 125V)
The individual windings are tapped and connected in series at the taps selected for the required voltage operating range, but it is imminently doable without permanent alterations to the motor.
I posted some actual details regarding motor wiring on another TD-124 thread here: http://www.diyaudio.com/forums/analogue-source/223136-thorens-td-124-power-question.html#post3235028
I believe in fact that it would be possible to run one winding fixed and vary the other one +/- a few percent to see what effect that has..(Each winding independently end to end can operate from 100 - 125V)
The individual windings are tapped and connected in series at the taps selected for the required voltage operating range, but it is imminently doable without permanent alterations to the motor.
I posted some actual details regarding motor wiring on another TD-124 thread here: http://www.diyaudio.com/forums/analogue-source/223136-thorens-td-124-power-question.html#post3235028
Attachments
This only works with the synchrone motor where you need a capacitor to get the 90gr.lead for the second coil then you can get much lower noise if you tune this .
I have done this for the Thorens TD160 motor with very good results.
The main vibration with the E50 motor comes from the ,,twice line frequency vibration, at your place 120 hz .
This vibration is always there and get influenced from the airgap between the stator and rotor, eccentricity of the rotor , bearing play etc.
If you carefull align the upper and lower bearings you can minimize it .
regards Volken
I have done this for the Thorens TD160 motor with very good results.
The main vibration with the E50 motor comes from the ,,twice line frequency vibration, at your place 120 hz .
This vibration is always there and get influenced from the airgap between the stator and rotor, eccentricity of the rotor , bearing play etc.
If you carefull align the upper and lower bearings you can minimize it .
regards Volken
Those Eddy Current Brake Magnets...
Worked on a 1962 vintage TD-124 tonight, one of the complaints the owner had was that no matter what he did it just ran too fast. He had adjusted the magnet to the point where there was no more than 10 mils (0.25mm) of clearance between the magnet and the stepped pulley and still it ran too fast.
I decided to test it by substitution with a known good magnet which worked fine with a spacing of about 0.2" (5mm).
These magnets are usually strongly attracted to the vane in the eddy current brake assembly as the retaining screw is loosened - this one exhibited no such tendency.. It was extremely weak.
So if the table runs way too fast no matter what you do you might want to have a look at that magnet.
I suspect the typical speaker repair shop could probably remagnetize these magnets
Worked on a 1962 vintage TD-124 tonight, one of the complaints the owner had was that no matter what he did it just ran too fast. He had adjusted the magnet to the point where there was no more than 10 mils (0.25mm) of clearance between the magnet and the stepped pulley and still it ran too fast.
I decided to test it by substitution with a known good magnet which worked fine with a spacing of about 0.2" (5mm).
These magnets are usually strongly attracted to the vane in the eddy current brake assembly as the retaining screw is loosened - this one exhibited no such tendency.. It was extremely weak.
So if the table runs way too fast no matter what you do you might want to have a look at that magnet.
I suspect the typical speaker repair shop could probably remagnetize these magnets
Kevin,
Just to let you know,
My brother and his wife-to-be just happened into a bonanza.
Her uncle passed away and left them a TD124, and some McIntosh equipment, a MC 275 and a McIntosh Tuner and Preamp, (I don't remember the model numbers.)
The McIntosh pre and amp work, but the tuner has problems. Next time I'm over, I will be bringing my B&K 747, and see if there are problems with a tube or two.
As for the 124, I'm guessing I will be re-building it.
Gene
Just to let you know,
My brother and his wife-to-be just happened into a bonanza.
Her uncle passed away and left them a TD124, and some McIntosh equipment, a MC 275 and a McIntosh Tuner and Preamp, (I don't remember the model numbers.)
The McIntosh pre and amp work, but the tuner has problems. Next time I'm over, I will be bringing my B&K 747, and see if there are problems with a tube or two.
As for the 124, I'm guessing I will be re-building it.
Gene
TD 124
Why don't you ask him? His website is:
Classic Turntables
Gene
Hi there , is there any news that Mirko ( the one that makes these idler wheels ) is still making and selling them ? With regards Paul
Why don't you ask him? His website is:
Classic Turntables
Gene
Hi Gene,
Sounds like they hit the jackpot for sure, before going too much further all of that McIntosh gear should be carefully gone over. It is well overdue for power supply and coupling capacitor replacement. In the case of the tuner it is pretty unlikely to be a tube. Have them find someone they trust to go over the gear and do what must be done.. It'll be worth in terms of not frying expensive to replace parts..
The 124 of course will make a worth project, if they're really lucky it came with an SPU in tow..
Sounds like they hit the jackpot for sure, before going too much further all of that McIntosh gear should be carefully gone over. It is well overdue for power supply and coupling capacitor replacement. In the case of the tuner it is pretty unlikely to be a tube. Have them find someone they trust to go over the gear and do what must be done.. It'll be worth in terms of not frying expensive to replace parts..
The 124 of course will make a worth project, if they're really lucky it came with an SPU in tow..
Hello everyone.
I "hijacked" this helpful thread from Lenco Heaven, a great resource. This might help some of us that have noise problems with our TD124's.
"The idler wheel that I got with a flea market L78 was really noisy. At first I thought was the bronze bushing. It was probably run for a very long time without any lubrication at all, and I thought that the idler wheel is beyond repair. But it turned out that most of the noise is there because of the brown resin washers. They started making a sort of a very soft grinding noise as soon as they weren't completely covered in oil."
I had a sheet of 1mm PFTE lying around, and used a set of punches to make PFTE washers"
Wonder if that might work for us also?
I "hijacked" this helpful thread from Lenco Heaven, a great resource. This might help some of us that have noise problems with our TD124's.
"The idler wheel that I got with a flea market L78 was really noisy. At first I thought was the bronze bushing. It was probably run for a very long time without any lubrication at all, and I thought that the idler wheel is beyond repair. But it turned out that most of the noise is there because of the brown resin washers. They started making a sort of a very soft grinding noise as soon as they weren't completely covered in oil."
I had a sheet of 1mm PFTE lying around, and used a set of punches to make PFTE washers"
Wonder if that might work for us also?
Last edited:
Hello everyone,
I am Maurizio and I own a Thorens TD 124 MKI, that I received from my girlfriend's grandfather. When I picked up the table, it was practically dead; only the stroboscope turned up and nothing else. I managed to bring it again in service, dismounting, cleaning and re-lubing the motor, polishing the motor pulley and stepped pulley and relubing the idler wheel bearing. The TT reach its speed in about 3 turns and, after the warming up, speed remain constant except some imperceptible fluctuations, due to the stylus going from the outer to the inner tracks. The tonearm is a SME 3009 Serie II not improved, which I think it's a very beautiful and excellent arm. By the way, there are still margins of improvement in the way the turntable works. First of all, when the motor is on without the belt, it's silent; I managed to align the bearing after having warmed up the motor itself, by tightening the four screws in order to reach the minor possible noise. As soon as the belt is mounted, I start to hear some whirring, which, I suppose, derives from the belt itself. The belt is the original one, I've only clean it with warm water and soap and, then, with alcohol. It doesn't show any crack, by the way I don't know if it has lost its tension, because I don't have a reference belt to judge it. Do you think that it should be changed? I've already contacted Schopper in Switzerland, it should not be a problem to receive a belt from them here in Munich in a few days (it's about 300 km from here). Then the idler wheel, it's always a little bit noisy, though I cannot hear it in the normal listening. Is it maybe the bearing that needs to be changed too? I've checked that the idler wheel height is correct, with respect to the stepped pulley (about 1/64 of inch, right?) and it should be ok. Last but not least, a motor rumble audible only during silent tracks: it's like a noise, with a frequency of 50 hz, coming from the motor through the chassis and than to the tone arm. The noise appears only when the motor is engaged and the stylus on the vynil; I am sure it comes from the motor, because I've made different tries:
1) motor on, belt engaged, idler wheel mounted: noise on
2) motor on, belt engaged, idler wheel dismounted: noise on
3) motor on, belt disengaged: noise on
It's always the same frequency, therefore I suppose that the source is the motor itself. I've tried to mount the chassis on the plinth without the four mushrooms (that are new from StereoLab) and I could notice a decrease in motor noise but the sound of the TD 124 was colder and flatter, therefore not a good solution for me. The motor suspensions are still the original one, but seem to be ok: I know that there's a conversion kit from the MKI to MKII, would it bring good results? Or changing at least only the 3 motor suspension? In any case, the table is superb, I am discovering new aspects of my vinyls which I haven't noticed before! Thanks to everyone for sharing such precious informations and have a good day.
Maurizio
I am Maurizio and I own a Thorens TD 124 MKI, that I received from my girlfriend's grandfather. When I picked up the table, it was practically dead; only the stroboscope turned up and nothing else. I managed to bring it again in service, dismounting, cleaning and re-lubing the motor, polishing the motor pulley and stepped pulley and relubing the idler wheel bearing. The TT reach its speed in about 3 turns and, after the warming up, speed remain constant except some imperceptible fluctuations, due to the stylus going from the outer to the inner tracks. The tonearm is a SME 3009 Serie II not improved, which I think it's a very beautiful and excellent arm. By the way, there are still margins of improvement in the way the turntable works. First of all, when the motor is on without the belt, it's silent; I managed to align the bearing after having warmed up the motor itself, by tightening the four screws in order to reach the minor possible noise. As soon as the belt is mounted, I start to hear some whirring, which, I suppose, derives from the belt itself. The belt is the original one, I've only clean it with warm water and soap and, then, with alcohol. It doesn't show any crack, by the way I don't know if it has lost its tension, because I don't have a reference belt to judge it. Do you think that it should be changed? I've already contacted Schopper in Switzerland, it should not be a problem to receive a belt from them here in Munich in a few days (it's about 300 km from here). Then the idler wheel, it's always a little bit noisy, though I cannot hear it in the normal listening. Is it maybe the bearing that needs to be changed too? I've checked that the idler wheel height is correct, with respect to the stepped pulley (about 1/64 of inch, right?) and it should be ok. Last but not least, a motor rumble audible only during silent tracks: it's like a noise, with a frequency of 50 hz, coming from the motor through the chassis and than to the tone arm. The noise appears only when the motor is engaged and the stylus on the vynil; I am sure it comes from the motor, because I've made different tries:
1) motor on, belt engaged, idler wheel mounted: noise on
2) motor on, belt engaged, idler wheel dismounted: noise on
3) motor on, belt disengaged: noise on
It's always the same frequency, therefore I suppose that the source is the motor itself. I've tried to mount the chassis on the plinth without the four mushrooms (that are new from StereoLab) and I could notice a decrease in motor noise but the sound of the TD 124 was colder and flatter, therefore not a good solution for me. The motor suspensions are still the original one, but seem to be ok: I know that there's a conversion kit from the MKI to MKII, would it bring good results? Or changing at least only the 3 motor suspension? In any case, the table is superb, I am discovering new aspects of my vinyls which I haven't noticed before! Thanks to everyone for sharing such precious informations and have a good day.
Maurizio
Hello everyone,
I am back again: today I tried to record and to analyze the sound, coming out from my Thorens TD 124. I used the software Audacity, a very useful freeware; I don't intend to make a "scientific" post, nor to say that my method is 100% correct, but the results I obtained are incredible. First of all, I did two measurements: one with amplifier turned off, microphone directly on the chassis and turntable operating at 33.3 rpm. Then I did an analysis of the frequency spectrum of the recorded file and what was the result? I have a pick of -42 db at 50 hz, exactly the operating frequency of the motor!
As second measurement, I recorded the first mute track of a vynil and I put the microphone in front of my speaker. Now the result was a peak of about -38 db between 50 and 60 hz, which means that other noise sources are involved.
As previously said, it's an empirical method but it seems to confirm the fact that the motor is the principal noise source. Furthermore I wanna try to calculate the rumble noise, in order to check if I reach at least the Thorens standard of the time (I read somewhere it was -40 dB).
Cheers
Maurizio
I am back again: today I tried to record and to analyze the sound, coming out from my Thorens TD 124. I used the software Audacity, a very useful freeware; I don't intend to make a "scientific" post, nor to say that my method is 100% correct, but the results I obtained are incredible. First of all, I did two measurements: one with amplifier turned off, microphone directly on the chassis and turntable operating at 33.3 rpm. Then I did an analysis of the frequency spectrum of the recorded file and what was the result? I have a pick of -42 db at 50 hz, exactly the operating frequency of the motor!
An externally hosted image should be here but it was not working when we last tested it.
As second measurement, I recorded the first mute track of a vynil and I put the microphone in front of my speaker. Now the result was a peak of about -38 db between 50 and 60 hz, which means that other noise sources are involved.
An externally hosted image should be here but it was not working when we last tested it.
As previously said, it's an empirical method but it seems to confirm the fact that the motor is the principal noise source. Furthermore I wanna try to calculate the rumble noise, in order to check if I reach at least the Thorens standard of the time (I read somewhere it was -40 dB).
Cheers
Maurizio
Good stuff Maurizio!
The Schopper belt is a good bit of kit, and is what I am using on both of mine. The motor mount kit to upgrade to the motor mounting used on the 124/II is a very worthwhile upgrade.
Assuming the main bearing does not use nylon bushings you should be fine with the original main bearing unless the table has very high hours. If nylon you can get replacement sintered bronze bearings on eBay.
A good plinth is a great help wrt to attenuating motor noise. I have a Schick on my 124/II with a Meister Silver SPU on a four layer slate plinth, and on my 124/I an SME 3009 Series II (Unimproved) with supplemental weights and an SPU GM E II on a crummy homebrew wood plinth..
The Schopper belt is a good bit of kit, and is what I am using on both of mine. The motor mount kit to upgrade to the motor mounting used on the 124/II is a very worthwhile upgrade.
Assuming the main bearing does not use nylon bushings you should be fine with the original main bearing unless the table has very high hours. If nylon you can get replacement sintered bronze bearings on eBay.
A good plinth is a great help wrt to attenuating motor noise. I have a Schick on my 124/II with a Meister Silver SPU on a four layer slate plinth, and on my 124/I an SME 3009 Series II (Unimproved) with supplemental weights and an SPU GM E II on a crummy homebrew wood plinth..
- Home
- Source & Line
- Analogue Source
- Restoring and Improving A Thorens TD-124 MKII