I have worked with Polyurethane foam and it's use is dependent on many variables, age of the mix ingredients; mixing time and ambient temperature being only three.
But if you leave the tops open there shouldn't be too much expansion of the mix sideways.
Why don't you make a set trial panels, and then try various pours of different foam types to see which is the best for your application?
Water based Urea/Formaldehyde foam would probably be a better mix to use if it wasn't for the fact that you need such expensive equipment to mix and pour it, back when I worked for Bostik we played around with many different additives for rigid PU foam, carbon filler ( charcoal ) talc powder, cellulose ( dried sawdust ) and fiberglass.
But if you leave the tops open there shouldn't be too much expansion of the mix sideways.
Why don't you make a set trial panels, and then try various pours of different foam types to see which is the best for your application?
Water based Urea/Formaldehyde foam would probably be a better mix to use if it wasn't for the fact that you need such expensive equipment to mix and pour it, back when I worked for Bostik we played around with many different additives for rigid PU foam, carbon filler ( charcoal ) talc powder, cellulose ( dried sawdust ) and fiberglass.
Hi crazyhub,
First, you wrote a bunch of other stuff in response to my quote:

There you have it. These panels are braced.
First, you wrote a bunch of other stuff in response to my quote:
Study how a large wind turbine blade is constructed. I think the lads that design those know a thing or two about physical laws.**** Oh YES! in myself, but only sometimes...however always in physical laws
We will see.**** indeed..."massively"...but not enough!
See above.**** Unfortunately the actual weak point will be the entire panel
I can see from most of your arguments that you really don't have any kind of practical understanding of the science involved.**** good material and shape for the divider; problem isn't the divider, problem is the entire structure; think about: what are the stiffness properties of thin hardwood vs really stiff materials such as concrete or steels and on...? How much do you gain by bending such panels? Between the two sheets you have only two choices: dampen or stiffen...foam will not make the job.
Please John, don't think I regard your project as a bad one; the idea of a sandwich structure using bended sheets isn't bad and is even nicely innovative! Only the materials you choose aren't enough performing for such a large enclosure; please consider at least to place some braces...![]()
There you have it. These panels are braced.
Interesting project! I will be watching![]()
Thanks for dropping by Dr.
I have worked with Polyurethane foam and it's use is dependent on many variables, age of the mix ingredients; mixing time and ambient temperature being only three.
But if you leave the tops open there shouldn't be too much expansion of the mix sideways.
Why don't you make a set trial panels, and then try various pours of different foam types to see which is the best for your application?
Water based Urea/Formaldehyde foam would probably be a better mix to use if it wasn't for the fact that you need such expensive equipment to mix and pour it, back when I worked for Bostik we played around with many different additives for rigid PU foam, carbon filler ( charcoal ) talc powder, cellulose ( dried sawdust ) and fiberglass.
Hi Moondog,
I'm having a bit of difficulty finding a local source for any pourable foam, let alone a variety. I will go to a marine equipment store tomorrow and see if they have any. I've found a good variety online but from the US. One is HERE. I found one online marine supply here and they have 2lb foam for more than double what US Composites is charging.
It sounds like you know a thing or two about the topic. What density do you feel would be the best for this?
Lowest density possible, more like a mass of holes surrounded by thin layer of the plastic substrate, it has been 30 years since I was in that industry so I know that everything regarding the chemicals has changed but the basics are still the same.
Personally I would look at the foaming mix sold for flotation filling of hollow sections, 2lb per cubic foot? sounds about right.
If mass wasn't an issue try casting with my favorite mixture, PVA wood-glue; shredded newspaper and Plaster of Paris
Personally I would look at the foaming mix sold for flotation filling of hollow sections, 2lb per cubic foot? sounds about right.
If mass wasn't an issue try casting with my favorite mixture, PVA wood-glue; shredded newspaper and Plaster of Paris
Hi John; I have read through the FAQ on your link, all good solid information, especially the warning regarding ambient temperature, if you want it to be less dense pour on a really hot day.
You can gain a few seconds of mixing time by cooling the 2-parts mix, but if too cool the become so thick and syrupy they wont pour or mix well.
With 2lb mix there is no advantage to adding any fillers, it would probably interfere with cell wall formation.
Those prices are much better than we get over here,
You can gain a few seconds of mixing time by cooling the 2-parts mix, but if too cool the become so thick and syrupy they wont pour or mix well.
With 2lb mix there is no advantage to adding any fillers, it would probably interfere with cell wall formation.
Those prices are much better than we get over here,
I'm blushing Cal...
OR was that an mild taunt? Whatever, I can handle either.
Gee, no one has commented on my driver selection or box design...everyone is hung up on the construction.
One concern I have is the sensitivity of the drivers, in particular the mid. At 87db it is quite a bit lower than the woofers and tweeter.
I may do some more digging to find a driver that is a bit more efficient.
Suggestions are welcome but I do want a 6-7 inch driver for this.
Cool box construction design! but 9-10 cu ft / low WAF approval rating
ie
Since you are going active, it ( sensitivity mismatch between drivers) should not be a huge concern.
I like your choice of the Morel horn loaded tweeter it should be at the top of the heap (for a dome) for sheer max spl. I'm a Big fan/user of dynaudio/morel anyway.
I would like to see a passive crossover design with a more sensistive mid just for fun.
Lowest density possible, more like a mass of holes surrounded by thin layer of the plastic substrate...
If mass wasn't an issue try casting with my favorite mixture, PVA wood-glue; shredded newspaper and Plaster of Paris
I was thinking the same way. I think the stuff in the spray cans would be good enough but the drawback is how long it takes for it to set - hours as opposed to minutes.
These will be heavy if left empty - filling with anything heavier than foam and I'd need a folklift to move them.
if you want it to be less dense pour on a really hot day.
You can gain a few seconds of mixing time by cooling the 2-parts mix, but if too cool the become so thick and syrupy they wont pour or mix well.
With 2lb mix there is no advantage to adding any fillers, it would probably interfere with cell wall formation.
Those prices are much better than we get over here,
I'm probably looking at $100-$150 for 2 gallons locally of the 2lb foam so that's most likely what I'll use. When you consider how inexpensive the panel material is, it works out to a very reasonable amount. 2 gallons should be more than I need.
No hot days here now - winter and I'll need to do the filling inside where there is heat. The idea is to mix a small amount at a time and pour it in, let it set then mix and pour more until each panel is filled. Each panel will be filled before the box is assembled.
Cool box construction design! but 9-10 cu ft / low WAF approval rating![]()
Thanks
WAF is never a concern where speakers are involved. Sound first!
Since you are going active, it ( sensitivity mismatch between drivers) should not be a huge concern.
I like your choice of the Morel horn loaded tweeter it should be at the top of the heap (for a dome) for sheer max spl. I'm a Big fan/user of dynaudio/morel anyway.
I would like to see a passive crossover design with a more sensitive mid just for fun.![]()
I've been looking for a more sensitive mid but wasn't having any luck in the usual places. I did find THIS and it doesn't look bad for this application. A bit bigger than I wanted but nearly 4db more sensitive. Frequency response looks like a good fit. Thoughts?
Perhaps this driver warrants consideration:
MONACOR INTERNATIONAL:New products
90db sensitivity, very flat and broad frequency response (it will play low too, -3db @ 75Hz in sealed 0.7Q box) and the correct size for your project. On paper it seems simple to implement but I have no first hand experience with it. Unfortunate it is a European driver, but I'm sure you could obtain it for reasonable shipping cost, it's quite cheap in the first place at least
MONACOR INTERNATIONAL:New products
90db sensitivity, very flat and broad frequency response (it will play low too, -3db @ 75Hz in sealed 0.7Q box) and the correct size for your project. On paper it seems simple to implement but I have no first hand experience with it. Unfortunate it is a European driver, but I'm sure you could obtain it for reasonable shipping cost, it's quite cheap in the first place at least
Hi MJL, don't let them sidetrack you on box construction. Get on and do it your way. We'll never learn if folk never try something.
Now back to the project.
When can I expect to hear about the speakers, the DCX setting up. How the EQ worked out. How you listened and measured and how you found and corrected anomalies? How you decided what amplifier for which driver, whether you use one amp for both bass drivers or two separate amps.
I want the nitty gritty of making a 3way sound good.
Now back to the project.
When can I expect to hear about the speakers, the DCX setting up. How the EQ worked out. How you listened and measured and how you found and corrected anomalies? How you decided what amplifier for which driver, whether you use one amp for both bass drivers or two separate amps.
I want the nitty gritty of making a 3way sound good.
ACOUSTINATOR™ CX2008
well atleast its got a funky name ( maybe there is a job for someone naming speakers)
offhandedly seems more on the woofer end than a mid. I wonder about porous dustcaps as though it might sound funky like its name ie up at the higher freq end.
It's a musical instrument speaker but I have a good feeling about it. Response looks good and the sensitivity is a near perfect match for the woofer and tweeter.
I have many parts cut and I have one of the biggest panels assembled:
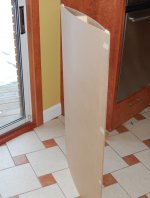
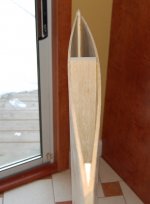
I changed the dimensions slightly to avoid a lot of sheet waste. That panel is 48" high and 28" wide. In making the panel wider, I also increased the thickness of the backbone to 2". Also, you'll notice that the backbone is NOT steel - in the end I thought it would be less practical to try to glue steel into this position. The backbone is solid hard maple - 3/4" thick by 2" wide and should be strong enough here.
Gluing this together was a bit tricky, I glued the fillets(which I have made wider) and backbone to the outer skin first, let that dry and then glued on the inner skin, using a jig to clamp it and hold it straight on the edges.
Along with sensitivity I would look for a 2" dia VC (power handling) with perhaps more under than overhung. Id look more at cones with hard domes same dia as VC or maybe a pole piece for cooling/directivity control. Slim-pickins me thinks...
u might look at doubling up on the mids too. gains 6dB right there for paralleing to 4 ohms.
u might look at doubling up on the mids too. gains 6dB right there for paralleing to 4 ohms.
\man u are fast builderIt's a musical instrument speaker but I have a good feeling about it. Response looks good and the sensitivity is a near perfect match for the woofer and tweeter.
I thought it is a coax ie well if you don't like the sound you can add a HF horn to it later,
Thanks Dr.,
That's a very good looking choice but it's not available locally which is where I want to be buying everything. TBH I'm sick of the duty/brokerage fees doubling the price of everything. Plus the time it takes for shipping. I'm not in any rush on this but I'd like to have the driver in hand as soon as possible for testing.
I won't/haven't.Hi MJL, don't let them sidetrack you on box construction.
Now back to the project.
When can I expect to hear about the speakers, the DCX setting up. How the EQ worked out. How you listened and measured and how you found and corrected anomalies? How you decided what amplifier for which driver, whether you use one amp for both bass drivers or two separate amps.
I want the nitty gritty of making a 3way sound good.
Without exaggeration this is a huge project - it could be a year or years from now before they are fully complete. Follow along is all I can say and contribute if you feel you have something constructive to say - I promise: I won't report any of your posts.
Last edited:
\man u are fast builder
I thought it is a coax ie well if you don't like the sound you can add a HF horn to it later,
It is meant for acoustic guitar so maybe it works well as my midrange. I'm going to get them anyway to try out, I can always get rid of them if I don't like the way they sound.
HERE'S another possibility. Though it is not as efficient, it has excellent FR. Nice price too.
I did another load experiment on that mock-up piece, bringing the weight up to ~57lbs (25lbs bricks, 32lbs woofers
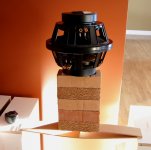
If that section were full of foam I think it could easily hold up twice that weight or more.
It's the year of living dangerously so I left the speakers and bricks on there for about 2 hours (I did put a big cushion under it) to see if it made a difference - no measurable difference and when I took the weight off, it returned to it's original shape.
Yikes the weight of your whole project is resting on the result of your little wing experiment
Nahh it's a 8" coax built for compact wide range sounds with an apt mounted in back. As such it has comprises galore. been there before...sounds like boof-boof-tweet-tweet
Nahh it's a 8" coax built for compact wide range sounds with an apt mounted in back. As such it has comprises galore. been there before...sounds like boof-boof-tweet-tweet
Last edited:
Yikes the weight of your whole project is resting on the result of your little wing experiment
No there is more to it than this. Any structure needs to be practically tested and compared. For example: I've already taken a strip of 1/2" Baltic birch plywood, put this much weight on it and measured the deflection - it was 3 times more (nearly 1/4") than the "wing". 1/2" particle board fractured when I attempted to place the first woofer and I don't think I need to say what would happen to just a double layer of 1/4" hardboard when laid flat.
This is just a demo - there is a lot going on in the completed panel and how it will attach to the rest of the box. The real test will happen when it is completed.
Nahh it's a 8" coax built for compact wide range sounds with an apt mounted in back. As such it has comprises galore. been there before...sounds like boof-boof-tweet-tweet
You are correct, I didn't see that it is a coax. Next...
Yikes the weight of your whole project is resting on the result of your little wing experiment
I was merely observing if an accident happens, your woofers might go bye-bye.
Good stuff otherwise
I was merely observing if an accident happens, your woofers might go bye-bye.
Good stuff otherwise
Like I said, the year of living dangerously.
One must have faith.
Here's panel #2 with the fillets and backbone glued in:
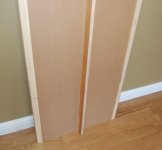
And here it is in the clamping jig with the inner skin glued on:
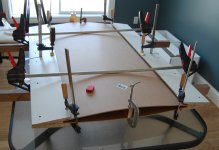
Part of the fun in a project like this is figuring out how to do these tricky things, like gluing the panel together straight and true.
- Status
- This old topic is closed. If you want to reopen this topic, contact a moderator using the "Report Post" button.
- Home
- Loudspeakers
- Multi-Way
- Large 3-ways design / build