Finally located the article I was remembering(1978 Audio Amateur) that clearly shows that the oven was used to shrink/temper/stabilize the Mylar while being held under uniform tension by distributed weights. Here are the relevant pics pulled from the article. The thermoset adhesive isn't mentioned until step 6 after the diaphragm has been removed from the oven, and an iron is used.I'd heard the tensioning hypotheses a lot, and I'm not convinced. Sure, it will heat shrink the mylar a bit (some mylar types shrink more than others), but I don't think that was the primary reason. Quad LOVED (and I mean loved) thermoset glues, they are all over all the quad speaker designs.
My guess is that the oven is used to melt the glue to bond the diaphram to the stator.
Attachments
Thank you bolserst for this information. Can you please supply the URL where I can find the archive of this magazine it was published in. Maybe there is more of interest in the article to read.Finally located the article I was remembering(1978 Audio Amateur) that clearly shows that the oven was used to shrink/temper/stabilize the Mylar while being held under uniform tension by distributed weights. Here are the relevant pics pulled from the article. The thermoset adhesive isn't mentioned until step 6 after the diaphragm has been removed from the oven, and an iron is used.
My 2 cents is that the oven was used to pre-heat the Mylar to be able to apply the coating more easily/evenly. But maybe you're right and were these pictures taken in a period when Mylar was quite new and was not pre-tensilized yet. All available Mylar now is, so doesn't need any pre-treatment any more as far as I understand. Never seen these pictures before, so thanks again for your effort in finding them.
Look at my post #1100 for the use of that "iron" in Germany.
I had downloaded the magazine when it was available from THE HISTORY OF RADIO documented in thousands of PDF books and magazinesCan you please supply the URL where I can find the archive of this magazine it was published in. Maybe there is more of interest in the article to read.
It has since been removed at request of the copyright holder, Circuit Cellar.
The text of the interview can be downloaded from the archived onthingaudio website where it had been posted with permission.
One Thing Audio/Manufacturers/Quad/History/Peter Walker
The Ross Walker interview is also archived there.
One Thing Audio/Manufacturers/Quad/History/Peter Walker
Quote from the Ross interview…”We stretch it up to the required tension and stick it in the oven. In its cold form, if you stretch it, it will creep. But by putting it in the oven under tension all the molecules will line up to the most stable position so the tension won't change…”
The same method was used for the ESL-63 diaphragm.
My experience agrees with this that even pre-tensilized mylar will creep and lose a small amount of tension if mechanically stretched before bonding to the stators. This creep occurs over weeks to months before it finally stabilizes at some lower tension.
The text of the interview can be downloaded from the archived onthingaudio website where it had been posted with permission.
One Thing Audio/Manufacturers/Quad/History/Peter Walker
Thanks for link. A fun read.
You gotta love the Brits of that older generation - the guys who drove their industries into the ground. Fun to read but mostly for nostalgic reasons. A mix of arrogantly held common sense with firmly held biases (like doubting you could successfully add a sub to Quad ESLs).
Walker can't understand why anybody would want to bi-amp. But near the end, Walker says passive crossovers can't work right due to "speech coil" heating.
B.
Hi there,
I have a (maybe stupid
) question regarding coating: does it last for long time in bottle? I bought some coating from ER-Audio 6 years ago and I would like to know if I can use it to refurbish one pannel?
If not, is EC-coating from martin-jan still available?
Regards,
Emmanuel
I have a (maybe stupid
If not, is EC-coating from martin-jan still available?
Regards,
Emmanuel
Hi there,
I have a (maybe stupid) question regarding coating: does it last for long time in bottle? I bought some coating from ER-Audio 6 years ago and I would like to know if I can use it to refurbish one pannel?
If not, is EC-coating from martin-jan still available?
Regards,
Emmanuel
Hello Emmanuel,
I got coating right on stock. Due to a different formula it is called HTEC-coating instead of EC-coating.
The coating must be used within aprox. 5 months (storage in refrigerator) and the exact exp. date is printed on the bottle.
I dont know about the shelf-life of the ER-coating so you should contact them.
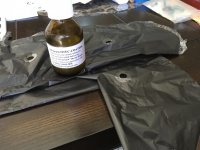
Martins coating worked perfectly on the 988 panels.
Still have over half a bottle left. If I gave it a shot on some 57 mid/twt panels with higher resistance I believe , what would happen for example ?
I could see micro bubbles in the coating (after being used) that slowly disappeared after many months in the refrigerator
You can send a PM if you wish.
Regards
David
If you mean arend-jan, he is gone, car accident. If you mean MJ Dijkstra then drop him an email.
My apologies for not having answered before and for the mistake between both of them.
I meant MJ Dijkstra, thanks for your replies.
I got coating right on stock. Due to a different formula it is called HTEC-coating instead of EC-coating.
The coating must be used within aprox. 5 months (storage in refrigerator) and the exact exp. date is printed on the bottle.
Ok, so my coating is out (more than 6 years), I will start refurbishment in two months, I will PM you at this moment, thank you MJ!
All the best,
Emmanuel
Hello Emmanuel,
I got coating right on stock. Due to a different formula it is called HTEC-coating instead of EC-coating.
The coating must be used within aprox. 5 months (storage in refrigerator) and the exact exp. date is printed on the bottle.
I dont know about the shelf-life of the ER-coating so you should contact them.
MJ Dijkstra - can I kindly ask you to look in your PM?
I did send you a p.m.
As written, coating is currently not available.
I have to make the coating from the individual components which makes it very time laborous. Due to the limited stability of the fluid system I have to make small batches as well which doesnt help.
@MJ Dijkstra
Few months passed - any plans to run a new batch?
Dear diyAudio forum,
at the High-End Munich in 2016 I heard the electrostatic loudspeakers at the Helixir audio stand and was thoroughly impressed. I found CharlieM’s web-page that same evening and decided to attempt to build hybrid panels myself. At the time I had Markaudio Alpair 12p back loaded horn-reflex speakers. Knowing, that the electrostatic loudspeakers would be dipoles, I combined the Alpairs with some Peerless woofers (picture attached). Those speakers already sound pretty good and dispersed my last skepticism towards dipoles.
I’m now following up on the electrostatic top panels. My overarching design goal is constant dipolar directivity. I’ve designed the following pcb stators and had them fabricated. Most of the design is already planned out, but I’m still missing 6um mylar foil and the diaphragm coating to proceed with the prototype. From what I’ve gathered, MJ Dijkstras coating would be the preferred solution. He hasn’t yet responded to my PMs, therefore I’m trying to get his attention here. Also, does anyone have a better source for the mylar than the following ebay seller from taiwan? Electrostatic Speaker Membrane Dupont Mylar C 6um 40m for sale online | eBay
If someone wants to discuss the design or is interested in a build update in due time, then let me know.
Best regards,
Karl
@MJ Dijkstra: Please check your private messages.
at the High-End Munich in 2016 I heard the electrostatic loudspeakers at the Helixir audio stand and was thoroughly impressed. I found CharlieM’s web-page that same evening and decided to attempt to build hybrid panels myself. At the time I had Markaudio Alpair 12p back loaded horn-reflex speakers. Knowing, that the electrostatic loudspeakers would be dipoles, I combined the Alpairs with some Peerless woofers (picture attached). Those speakers already sound pretty good and dispersed my last skepticism towards dipoles.
I’m now following up on the electrostatic top panels. My overarching design goal is constant dipolar directivity. I’ve designed the following pcb stators and had them fabricated. Most of the design is already planned out, but I’m still missing 6um mylar foil and the diaphragm coating to proceed with the prototype. From what I’ve gathered, MJ Dijkstras coating would be the preferred solution. He hasn’t yet responded to my PMs, therefore I’m trying to get his attention here. Also, does anyone have a better source for the mylar than the following ebay seller from taiwan? Electrostatic Speaker Membrane Dupont Mylar C 6um 40m for sale online | eBay
If someone wants to discuss the design or is interested in a build update in due time, then let me know.
Best regards,
Karl
@MJ Dijkstra: Please check your private messages.
Attachments
- Home
- Loudspeakers
- Planars & Exotics
- ESL Diaphragm coating