These handmade papers sound warmer, has more lush.
I have more than just China and Japanese papers in my workshop.
I have Thailand Mulberry paper, Nepal Lokta paper, wood veneers from Africa. I had made Lokta paper cones which I published on my Facebook, I seldom post here nowadays.
Nevertheless paper to me are just paper, not really rocket science to make them. China has pretty big source of handmade paper which I had purchased quite a few of them to reprocess them into paper weight and density I needed.
I have more than just China and Japanese papers in my workshop.
I have Thailand Mulberry paper, Nepal Lokta paper, wood veneers from Africa. I had made Lokta paper cones which I published on my Facebook, I seldom post here nowadays.
Nevertheless paper to me are just paper, not really rocket science to make them. China has pretty big source of handmade paper which I had purchased quite a few of them to reprocess them into paper weight and density I needed.
Speaking of paper, I'm in the middle of reading a book titled "On Paper" - it seems to cover just about everything paper is used for, and how it's made both historically and in modern mass production and such. No mention of loudspeaker drivers yet ...
Also, there's a papermaking museum on the Georgia Tech campus that's NOW a bucket list location for me. I've been to the Tech campus many times, but didn't know this was there until recently:
Robert C. Williams Museum of Papermaking | Robert C. Williams Museum of Papermaking | Georgia Tech
Also, there's a papermaking museum on the Georgia Tech campus that's NOW a bucket list location for me. I've been to the Tech campus many times, but didn't know this was there until recently:
Robert C. Williams Museum of Papermaking | Robert C. Williams Museum of Papermaking | Georgia Tech
@perceval, yeah the COVID is making travel weebit more quiet than usual. You can visit my friend's showroom where I place my drivers for demo.
@benb, the most important to the paper making is the additives. For example paper pulp sizing which you can read more about it.
@benb, the most important to the paper making is the additives. For example paper pulp sizing which you can read more about it.
Thanks for the comments
I think beside having to try all types of paper, there is still a importance to have a CNC Winding machine for making Voice Coil
Youtube Video: CNC Winding @300 rpm
Youtube Video: CNC Winding @450 rpm
I think beside having to try all types of paper, there is still a importance to have a CNC Winding machine for making Voice Coil
Youtube Video: CNC Winding @300 rpm
Youtube Video: CNC Winding @450 rpm
An externally hosted image should be here but it was not working when we last tested it.
An externally hosted image should be here but it was not working when we last tested it.
Last edited:
For DIYers who are interested in building your own cones/VC for Lowther and other fullrange speakers
Lowther Modification Support Group
Lowther Modification Support Group
I'm watching this video posted there and he's measuring the "impedance" of a VC he's winding with a DMM, taking turns off until he gets a reading of "8.0". I'm sure it'll be operational and work well enough with most any reasonable number of turns and wire resistance, but technically there's so much wrong here. He's actually measuring DC resistance and I don't trust an average DMM to have 0.1 ohm accuracy even if it has 0.1 ohm resolution. I trust my BK 878 for resistance measurement, but only with alligator clips on the wires, not pressing the usual meter lead contacts. It's my experience that measuring low resistance takes some extra care. Measuring impedance would be another thing, and the drill chuck surely doesn't have the magnetic characteristics of the coil in the driver gap.For DIYers who are interested in building your own cones/VC for Lowther and other fullrange speakers
Lowther Modification Support Group
Otherwise, this is an interesting video.
I just had to post.
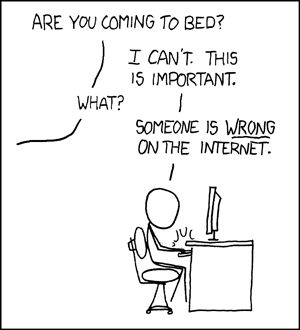
Hi Ghemml,
Wonderful effort bravo, question pls Im sure cone materials affects sound greatly but what about cone shape ? I also notice that the cones are cut in circular shape but only join on one spot , would this not affect SQ & would not say cutting up the cone & glueing up in equals segments be better or ????
Many thanks
Wonderful effort bravo, question pls Im sure cone materials affects sound greatly but what about cone shape ? I also notice that the cones are cut in circular shape but only join on one spot , would this not affect SQ & would not say cutting up the cone & glueing up in equals segments be better or ????
Many thanks
I'm watching this video posted there and he's measuring the "impedance" of a VC he's winding with a DMM, taking turns off until he gets a reading of "8.0". I'm sure it'll be operational and work well enough with most any reasonable number of turns and wire resistance, but technically there's so much wrong here. He's actually measuring DC resistance and I don't trust an average DMM to have 0.1 ohm accuracy even if it has 0.1 ohm resolution. I trust my BK 878 for resistance measurement, but only with alligator clips on the wires, not pressing the usual meter lead contacts. It's my experience that measuring low resistance takes some extra care. Measuring impedance would be another thing, and the drill chuck surely doesn't have the magnetic characteristics of the coil in the driver gap.
Otherwise, this is an interesting video.
I just had to post.
The reason to why we do that is to have a quick method to determine the DRC before the final design.
Do note, the ends of those enamel wire is less than 0.2mm diameter, using sweep measurement can be a hassle to setup and VERY VERY ANNOYING to clip the ends with crocodile clamps while trying not to snap the wire. Even myself uses a normal Digital Multi-meter to get a rough idea how much turns I need before fine tuning.
And we need to verify many wire gauges to come to a final selection, imagine testing so many sizes ø0.1, ø0.11, ø0.12, ø0.13, ø0.14....etc.. with so many different number of turns to achieve required VC height. Bloody annoying setup a special measurement tools to measure it. Beside, when we measure this way, we still need to determine the additional DRC of the extra enamel wire to the lead out.
Trust me, winding VC can be an very annoy process. That why I design my own CNC Winding machine, so I can have a quick release bobbin design.
could a spider be made in the same way as yours but out of a conductive material and connect directly to the voice coil?
I assume you are using metal with suitable flexural strength. It can be done with material like stainless steel, but it will add more weight to the overall structure.
Hi Ghemml,
Wonderful effort bravo, question pls Im sure cone materials affects sound greatly but what about cone shape ? I also notice that the cones are cut in circular shape but only join on one spot , would this not affect SQ & would not say cutting up the cone & glueing up in equals segments be better or ????
Many thanks
From what I understand, cone profile effects less on acoustic differences compared to size of VC, type of V Former and magnetic intensity. VC diameter and Material rules most of the acoustic signature of a driver, I feel everything starts from VC before moving on to the cone profile, which I find it amusing that so many DIYers don't bother about it.
Joining area doesn't effect the overall listening experience. But too many cuts require more processes and quality control will have an impact without elaborate tools and fixtures.
The reason to why we do that is to have a quick method to determine the DRC before the final design.
Do note, the ends of those enamel wire is less than 0.2mm diameter, using sweep measurement can be a hassle to setup and VERY VERY ANNOYING to clip the ends with crocodile clamps while trying not to snap the wire. Even myself uses a normal Digital Multi-meter to get a rough idea how much turns I need before fine tuning.
And we need to verify many wire gauges to come to a final selection, imagine testing so many sizes ø0.1, ø0.11, ø0.12, ø0.13, ø0.14....etc.. with so many different number of turns to achieve required VC height. Bloody annoying setup a special measurement tools to measure it. Beside, when we measure this way, we still need to determine the additional DRC of the extra enamel wire to the lead out.
Trust me, winding VC can be an very annoy process. That why I design my own CNC Winding machine, so I can have a quick release bobbin design.
I assume you are using metal with suitable flexural strength. It can be done with material like stainless steel, but it will add more weight to the overall structure.
From what I understand, cone profile effects less on acoustic differences compared to size of VC, type of V Former and magnetic intensity. VC diameter and Material rules most of the acoustic signature of a driver, I feel everything starts from VC before moving on to the cone profile, which I find it amusing that so many DIYers don't bother about it.
Joining area doesn't effect the overall listening experience. But too many cuts require more processes and quality control will have an impact without elaborate tools and fixtures.
Thanks for your reply & thoughts. Yes the cone shape/profile is what I was trying to get at. It is the cone that translate your efforts in the VC into sound waves. Would it not be better if you could get a moulded cone that suits & capitalizes on your design ?
Thanks again
Thanks for your reply & thoughts. Yes the cone shape/profile is what I was trying to get at. It is the cone that translate your efforts in the VC into sound waves. Would it not be better if you could get a moulded cone that suits & capitalizes on your design ?
Thanks again
To make custom mold, the average cost of the mold is around USD$5000. And requires a MOQ of 5000 pieces, anything below that they wouldn't enterain. The total average cost can be more than USD$10K, excluding shipping.
Unless you are a big time manufacturer making large orders(At least supplying 50000 units per month to cover operational cost), making custom mold for paper pulp is not cost effective and they are very expensive. You need water irrigation pool for the pulp, heater, and lots of space for the machinery.
Many cone manufacturers wouldn't even bother to entertain such orders.
To make custom mold, the average cost of the mold is around USD$5000
It cost around 200$ when performed on a small lathe, and around 0$ in a school if you ask them kindly.
I've paid mine ...0$ because i'm gentleman
It cost around 200$ when performed on a small lathe, and around 0$ in a school if you ask them kindly.
I've paid mine ...0$ because i'm gentleman![]()
Not this mold, i can do those simple lathe mold myself.
The paper pulp press mold, is actually a piece of cone with water drainage. In fact the mold has many small holes on it that it almost see through.
Not that simple as it see, you also need a holding tank for the pulp.
YouTube
Not this mold, i can do those simple lathe mold myself.
The paper pulp press mold, is actually a piece of cone with water drainage. In fact the mold has many small holes on it that it almost see through.
Not that simple as it see, you also need a holding tank for the pulp.
YouTube
My 0$ parts were realized on a high precision modern CNC lathe, but a really skilled ancient guy with a traditional old lathe can perform this kind of work (at a cost of more time).
Drilling small holes is not really a challenge and it can be performed also with a simple lathe (and its inherent very high concentricity precision), i've done high percision parts and adjustements in my young years with reformed old lathes of the 60s
Give me just an old lathe... and it will not take a whole day but i need this specific tool :

Yeah, I get all that (I'd see if I could find some flat-bladed clips), but my big point here is if he's looking to make an 8-ohm nominal impedance driver, the impedance is going to be too high. If he's looking to have a consistent impedance from driver to driver, then that should do.The reason to why we do that is to have a quick method to determine the DRC before the final design.
- Status
- This old topic is closed. If you want to reopen this topic, contact a moderator using the "Report Post" button.
- Home
- Loudspeakers
- Full Range
- Custom DIY 8" Fullrange Driver