Hi Entropy455,
There a quite a few others who have gone to extremes in the name of bass reproduction: here is one more:
REALHORNS - Ultimative High-End Surround Hornlautsprecher
Regards,
There a quite a few others who have gone to extremes in the name of bass reproduction: here is one more:
REALHORNS - Ultimative High-End Surround Hornlautsprecher
Regards,
Attachments
Entropy455,In an equivalent spring-mass system, the horn’s throat impedance is simply a damper – in which case you need raw & blunt applied-force to overcome the damper (i.e. a high BL). You specifically do not need extra mass (MMS), nor do you need additional spring-K (high Vas), to overcome the damper. The ideal horn driver has a low Qts, mainly due to the high BL, and low MMS. Or am I completely out-to-lunch on my understanding of horn driver selection???
Your understanding of horn driver selection is theoretically correct, but the theory was from an era when a 50 watt amplifier would have been considered quite high powered. The state of the art has evolved, drivers handling two or more orders of magnitude (5000+ peak watts) more power are now commonly available, and in terms of $$ adjusted for inflation, actually cost less than the 50 watt "high power" drivers that were common when horns ruled the playback and PA world.
To withstand the equivalent of several horsepower requires increased MMS and even more BL than classic "old school" theory would indicate. As an example, while in the testing phase of my Keystone "tapped horn" design, I tried an Eminence 4015LF 15" driver, a pair of LAB 12s, and a B&C 18SW115-4.
The low MMS 4015LF was the most sensitive, but well before reaching Xmax the distortion from cone flex was intolerable. The 4015LF has no problem in a BR (bass reflex) cabinet, but can not withstand high power horn loading without sounding awful, the distortion was so bad I did not bother testing it, though I wish I had in retrospect, simply to demonstrate the point to others.
Both the LAB 12s and B&C 18SW115-4 could withstand the throat pressure of the TH with relatively low distortion up to (and slightly beyond) Xmax. "Relatively" is an operative term, both drivers have less distortion at the same excursion in BR cabinets, but the Keystone TH has an average of 6 dB more sensitivity in the pass band of 35 to 100 Hz. Although the 18SW115 was less sensitive than the LAB12 pair, it's far superior heat removal system results in it having several dB more output potential, as it does not have anywhere near the "thermal compression" (voice coil RE increase with heat causing less delivered power) that the decades old LAB 12 has.
Amplification has become a relatively trivial expense, the Berhringer NU4-6000 with four 1500 watt channels, or two bridged mono pairs of 3000 watts each costs only $450, 13.3 pennies per watt. I can clearly remember that when I bought my first Phase Linear (AKA Flame Linear) amplifiers, they were the first to deliver power for under $1 per watt. The "dollar per watt" value held for decades, but now that technology has advanced to the point where there are less than 10 pounds of materials in a 6000 watt amp, compared to hundreds, cost also has dropped by an order of magnitude.
Although JAG and I frequently disagree on some minor issues, I agree with all he has written in the posts in this thread, other than this bit from #18:
"Besides, listening outside isn't all that great. Rooms create a spaciousness effect that you can't get outside (unless you are setting up a 7.1 system outside, which at this point wouldn't surprise me)."
Having mixed live sound (and playback) outdoors for over 40 years, I prefer the sound of no room to the sound of the best rated indoor venues. Outdoors, the sound is as close to the source as it possibly can be, with no room modes or "spaciousness effect" to interfere with accuracy to the source. Digital reverberation is now available for low cost that can duplicate the "spaciousness effect" of any venue, real or imagined, should you desire.
That said, being older and less tolerant of the often nasty outdoor conditions, I'd gladly trade a decent climate controlled room for outdoors for my listening enjoyment. Of course, hearing discreet echos two seconds after returning from a tree line 1000 feet away is kind of a "spiritual experience"...
Art
Last edited:
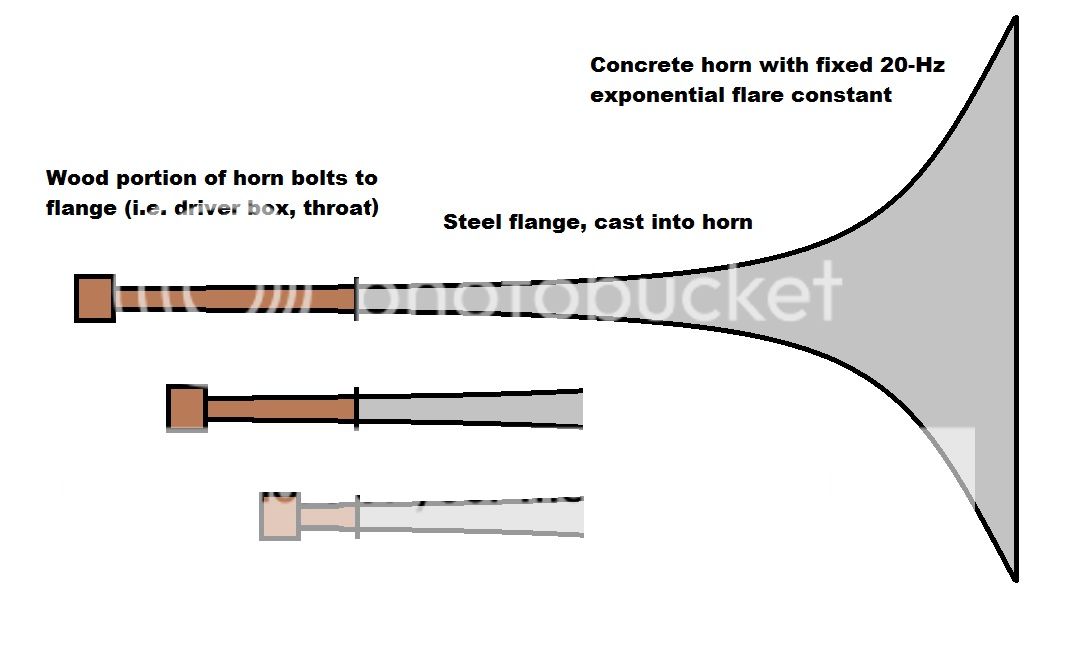
Weltersys, I feel like you’re confirming what I have originally suspected – in that no one really knows how a set of horns will sound, until they actually build & listen to them. My original plan (above) was to construct the main portion of the horns from concrete, and leave the throat slightly oversized with a steel flange cast into the horn body. This will permit me to bolt on a wooden rear chamber – permitting adjustments to the horn’s throat area (and respective length accordingly) - for a wide range of potential driver types & configurations. I want to be able to take the Pepsi Challenge, and actually hear what sounds best - without having to take a jack-hammer to my horns & mixing fresh concrete. . . . . This was my original question, on my first post on these forums. However I received some negativity for wanting to build full-size horns (i.e. full-space) – and for wanting to use concrete as a construction medium. . . .
And I do have a tree line. . . . About that. .. . Below is a black-powder cannon that I built for the 4th of July. . . . . It's 1028 mild steel, and weighs about 2000 pounds. It's road-towable. I normally fire it (shooting blanks only) over the open water of the Hood Canal. The echo from the mountains on the other side is pretty impressive. It takes about seven seconds - and it’s way more exciting to hear than the initial blast. It’s like rolling thunder – similar to hearing a supersonic jet flyby in the distance. The shoreline however is loaded with trees – thus I'm pretty sure the trees contribute significantly to the echo-return. I’m not sure what to do about the tree line on my property. Maybe I could selectively thin the trees, so that the impedance mismatch between the open air and the woods is not so pronounced?
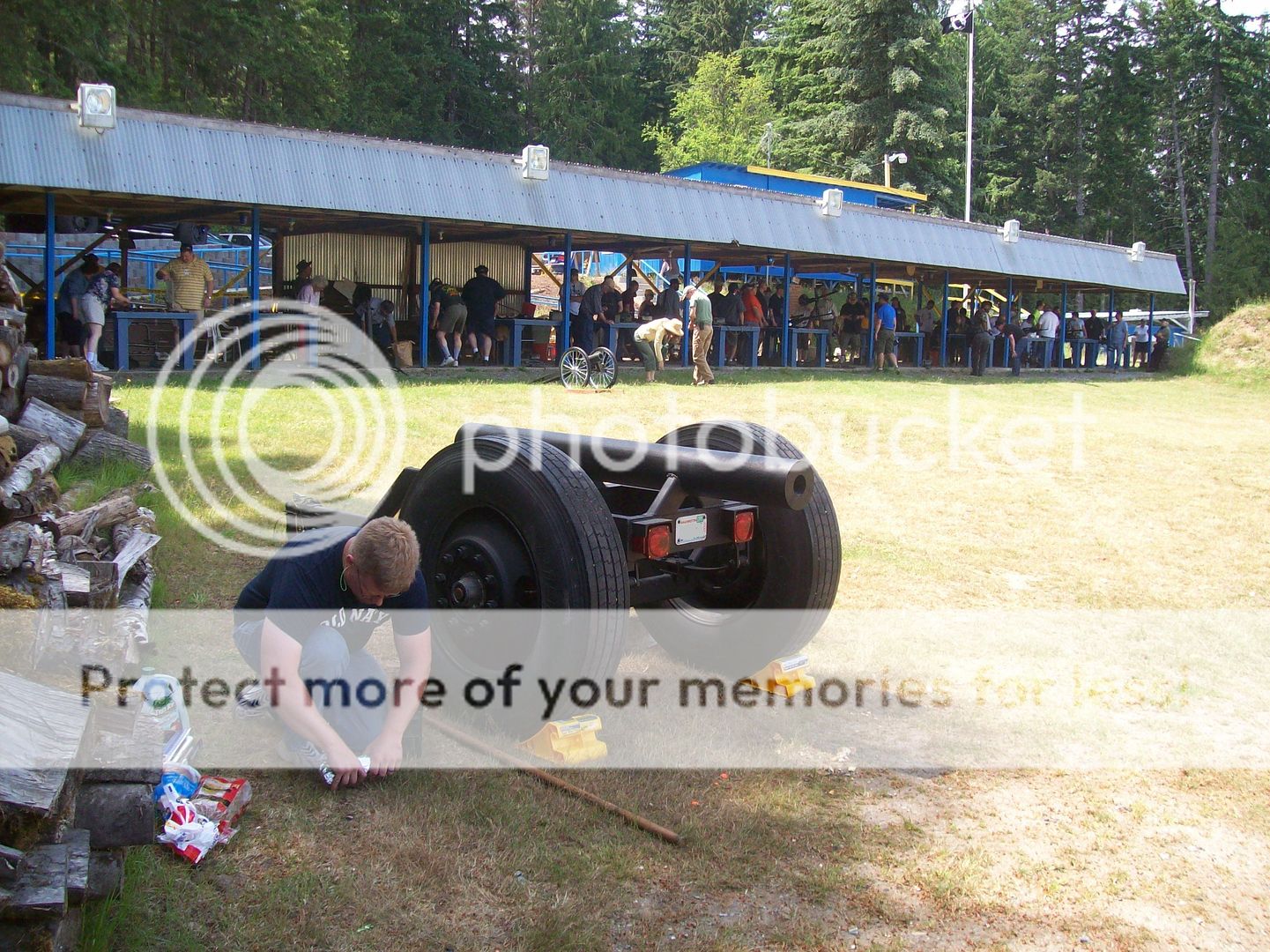
Bo's concrete bass horns. Amazing says those who heard them. Entropy increases as the louder and longer you play them 
faktiskt.se • Visa tråd - Allmän babbeltråd om högtalare, konstruktioner osv osv.
faktiskt.se • Visa tråd - Allmän babbeltråd om högtalare, konstruktioner osv osv.
Last edited:
TB46, those are some pretty clean looking horns. Do you know what the lower cutoff frequency is? Or other design specifications? (I can only read English)
TNT, when people ask me about Entropy, I tell them that Entropy is the quality of potential work-extraction from a thermodynamic heat-reservoir... Or, Entropy is the amount of thermodynamic disorder generated while extracting heat from that reservoir – depending on if you’re glass half-full, or glass half-empty kind of guy. . . . (engineering joke) If you ever want to truly test an engineer’s knowledge-retention, ask him/her to explain the difference between Enthalpy and Entropy.
They should tell you that mathematically (as related to a thermodynamic heat-reservoir) - that the partial derivative of Entropy is equal to the partial derivative of Internal Energy, divided by the absolute temperature of the heat-reservoir in which work is being extracted.
And mathematically (as it relates to a thermodynamic system) – Enthalpy is equal to the Internal Energy of the fluid medium, times the flow-work placed upon that fluid medium.
I'm telling you, this type of stuff keeps people up at night!
TNT, when people ask me about Entropy, I tell them that Entropy is the quality of potential work-extraction from a thermodynamic heat-reservoir... Or, Entropy is the amount of thermodynamic disorder generated while extracting heat from that reservoir – depending on if you’re glass half-full, or glass half-empty kind of guy. . . . (engineering joke) If you ever want to truly test an engineer’s knowledge-retention, ask him/her to explain the difference between Enthalpy and Entropy.
They should tell you that mathematically (as related to a thermodynamic heat-reservoir) - that the partial derivative of Entropy is equal to the partial derivative of Internal Energy, divided by the absolute temperature of the heat-reservoir in which work is being extracted.
And mathematically (as it relates to a thermodynamic system) – Enthalpy is equal to the Internal Energy of the fluid medium, times the flow-work placed upon that fluid medium.
I'm telling you, this type of stuff keeps people up at night!
Last edited:
Post #21 - realhorns.de
Hi Entropy455,
Post #25: "TB46, those are some pretty clean looking horns. Do you know what the lower cutoff frequency is? Or other design specifications? (I can only read English)..."
I had Google Chrome translate it for me, that seems to work. They have some diagrams under 'Produktion', and a lot more pictures throughout their site. There seem to be some interesting ideas as to the coupling of multiple drivers into the bass horn throat chamber, and water cooled drivers. But not a lot of details.
They also have a facebook page.
Regards
Hi Entropy455,
Post #25: "TB46, those are some pretty clean looking horns. Do you know what the lower cutoff frequency is? Or other design specifications? (I can only read English)..."
I had Google Chrome translate it for me, that seems to work. They have some diagrams under 'Produktion', and a lot more pictures throughout their site. There seem to be some interesting ideas as to the coupling of multiple drivers into the bass horn throat chamber, and water cooled drivers. But not a lot of details.
They also have a facebook page.
Regards
Ok TNT, now that is pretty darn cool. I didn’t realize what I was looking at initially. I wish I could read the text on the website - without having to copy & paste into a translator (I can only read English)
What is Bo using for drivers? What is the cutoff frequency of the horns? The third picture reminds me of looking down through some deck-grates and into the belly of a ship. I love it!
I've wondered about putting horns into the floor of a large room, and how one would keep people (and pets) from falling into the horn. The grates seem like an excellent idea. They appear to be fully welded assemblies - which I'm assuming would keep them from rattling. . . It's like a big speaker grill.. . .
What is Bo using for drivers? What is the cutoff frequency of the horns? The third picture reminds me of looking down through some deck-grates and into the belly of a ship. I love it!
I've wondered about putting horns into the floor of a large room, and how one would keep people (and pets) from falling into the horn. The grates seem like an excellent idea. They appear to be fully welded assemblies - which I'm assuming would keep them from rattling. . . It's like a big speaker grill.. . .
Weltersys, I’m not a big fan of Class-D amplifiers. Yes they are low-cost, lightweight, and very energy efficient. They are a blessing for DJs, and small touring bands. However the Berhringer NU4-6000 for example, has a damping factor of 120. In my opinion, 120 is a serious problem – it is way too low. The threshold for an audiophile quality amplifier is typically a damping factor greater than 300. This is why I am such a big fan of the Macro-Tech series (the older ones that were built with very heavy copper-wound transformers). The MT series packs a big-time damping factor greater than 1000. I personally can hear the difference (i.e. the sharpness in the speaker’s trainset response/fidelity), in between listening to a 1000 damping-factor amplifier, vs a 120 damping factor amplifier.
I think of a speaker like a hammer. There are 5 dollar hammers, and there are 50 dollar hammers. However the hammer alone is a poor indicator as to how well nails will be pounded – as a 50 dollar hammer in the hands of an accountant, will not perform as well as a 5 dollar hammer in the hands of a roofer. Point being - the arm swinging the hammer is a very important performance variable. I like to think of an amplifier’s damping factor as the size of the arm that’s swinging the hammer. Between all of the advertised amplifier specifications (THD, frequency response, Signal to Noise ratio, channel separator, slew rate, etc), it has been my experience that the damping factor specification alone is the best overall indicator as to how well the amp is going to sound. Again, it's just one man’s opinion. . .
Below are bass-guitar speakers that I built for the wife. They are powered by 10-kW of greater than 1000 damping factor amplification. The 18s are tuned for 30-Hz, and sound absolutely fabulous on a 5-string bass! Yes, some people prefer a wall of 10s for a bass, but this system sounds pretty good too. . .
I think of a speaker like a hammer. There are 5 dollar hammers, and there are 50 dollar hammers. However the hammer alone is a poor indicator as to how well nails will be pounded – as a 50 dollar hammer in the hands of an accountant, will not perform as well as a 5 dollar hammer in the hands of a roofer. Point being - the arm swinging the hammer is a very important performance variable. I like to think of an amplifier’s damping factor as the size of the arm that’s swinging the hammer. Between all of the advertised amplifier specifications (THD, frequency response, Signal to Noise ratio, channel separator, slew rate, etc), it has been my experience that the damping factor specification alone is the best overall indicator as to how well the amp is going to sound. Again, it's just one man’s opinion. . .
Below are bass-guitar speakers that I built for the wife. They are powered by 10-kW of greater than 1000 damping factor amplification. The 18s are tuned for 30-Hz, and sound absolutely fabulous on a 5-string bass! Yes, some people prefer a wall of 10s for a bass, but this system sounds pretty good too. . .
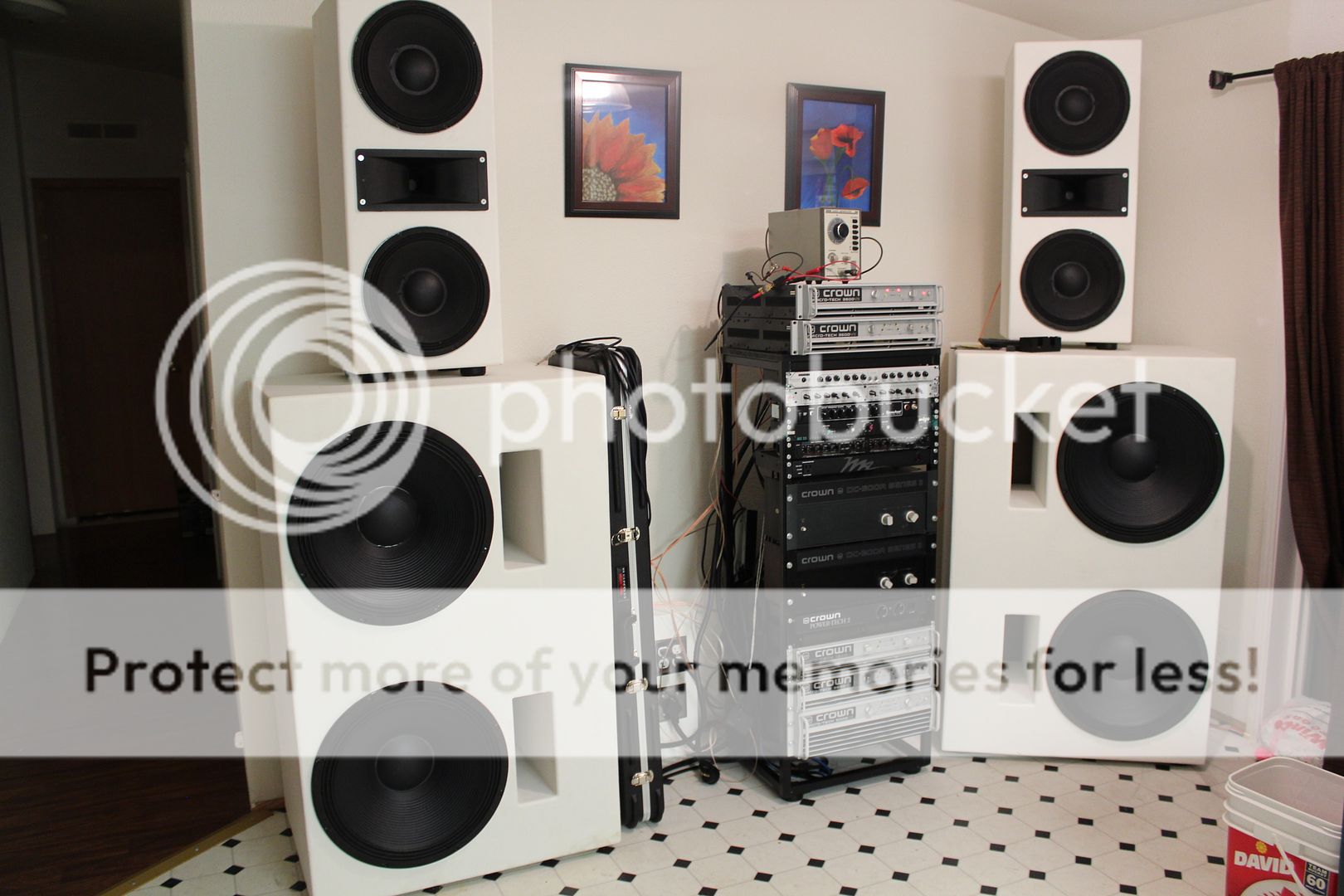
Last edited:
I had Google Chrome translate it for me, that seems to work.
Me too, I'm lost without its translation capability, though the Oriental pages can be a 'tough' read in English.
GM
You suggested that I construct a different system that will outperform a pair of 20-Hz straight exponential horns, in every performance metric - costing several times less, and at a fraction of the size.
Apologies for the late reply, I had to work all day today.
Most of the cost savings is going to be in the difference between wood and concrete construction, I though I made that pretty clear.
And your recommendation was that I build a pair of 20-Hz straight exponential horns. . . I love it!
Not straight, I specifically said I would fold my design.
20 hz low knee was your goal, I'm just following suit.
Not exponential either, hyperbolic exponential with a T much closer to 0.5 than 1. Your previous intention was a pure exponential and this new design you've shown isn't far off with it's 0.93 T. All design I show are going to have a much slower flare than yours.
You’ve recommended (qty 8) 18s in the throat to bat – I love that too! As the whole point of this thread (original post) was how to properly incorporate multiple drivers into a bass-horn design. . . .
Minimum quantity 8 - I would probably use even more Sd if I was going to build a full size 20 hz horn. But I didn't want to get too carried away here, as you are set on using very little Sd.
Incorporating multiple drivers isn't any issue, I thought we covered that in the last thread although I don't remember that well.
18s sound like 18s. Even with a mega-motor structure, the higher MMS degrades the transient response, and fidelity suffers. And 18s with a lighter cone sound better (tighter bass – primarily due to the faster transient response) – however these drivers are often Fs-limited in how low you can tune a bass-reflex enclosure - which kinda defeats the purpose when you’re trying to fill the bottom end. I’ve played around with the 15” long-throw woofers – big rubber surrounds, low FS, workable VAS, with a giant Xmas -and these speakers sound like mud also. Don’t get me wrong – they can reproduce bass, but they simply don’t sound good. They sound rubbery compared to an accordion-surround driver. And yes, I was feeding them plenty of clean power (MT-5000, active crossover, heavy-gauge leads).
21 inch drivers – I’ll never buy one. Practically every review says they sound like mud (for the reasons stated above).
12 inch drivers can chew the low-end out with clean authority. However you need a wall of them to fill a large room – which adds an additional set of problems in itself. Actual VAS values can vary quite a bit - even with speakers from the same assembly line, manufactured on the same day. When you have a wall of slightly out-of-alignment speakers, you can hear it. And sizing each enclosure for the specific driver (while pure in the realm of high-fidelity) is a cumbersome work practice in my book. It also causes problems if you ever need to replace a driver. Additionally, it has been my experience that the really good sounding 12” drivers have a higher Fs anyway (primarily due to the high BL & lower MMS), and cannot tune very low anyway.
This is what’s attracting me to horns – the idea that a speakers Fs is not a major design obstacle. The resistive load of the throat provides significant damping at FS, essentially minimizing the effect. The drivers that are suggested for bass horn applications (high BL, low MMS, low Qts), are good mid-bass drivers at best – in a bass reflex application.
Here's my question just-a-guy, will 18s still sound like 18s, in a horn application? Your simulation recommends an MMD of 323 grams. That’s nearing 21” driver territory. . . .
So many different issues to discuss here.
There's a lot more to sound than cone size and moving mass. A lot of 18s have small motors, that will give a high q response. Were you eq'ing your designs to flat to compare and did you account for the fact that larger drivers are usually tuned lower than smaller ones and have more room related issues in the response than smaller drivers due to that?
Transient response, impulse response, "speed". It's Adire that has a paper on that subject. Their conclusion is that "speed" is related to inductance, not the factors that most people think like cone size, cone mass, motor strength. Link to the paper is here - http://diy-audio.narod.ru/litr/WooferSpeed.pdf
You can take that paper for what it's worth or leave it. But 18s typically have larger coils than smaller drivers, larger coils usually amount to higher inductance. Especially the long stroke drivers you say you've experimented with.
Bass reflex tuning vs fs - this is another huge issue. Typically people that aren't that experienced will try to tune for max flat response - the flattest possible response to the lowest possible frequency. This is usually a bad idea, as that flat response will become overly bloated in the bass when placed in a room as opposed to the 2 pi space the design was simulated for. Tuning a bass reflex well below fs can give an EBS style rising response with a weak looking low knee in a sim - that's actually a good thing if you will be using the sub in a room - the room gain will offset the weak low end and bring it up to flat(ish).
Max flat ported designs are a HUGE reason that audiophiles don't like ported boxes - they sound boomy in room. Especially max flat ported boxes with 18 inch drivers, as these 18s usually have a low(ish) fs and it's easy to tune them lower in a max flat alignment.
So the design might have influenced your perception of 18s - if you make a ported box that has the same response curve shape as a sealed box (a very low q design), it will sound very "tight" and "fast" and not boomy at all.
About 21 inch drivers - I think a lot of people would disagree with you. There are some really nice 21 inch drivers out there. There's even a pretty popular 30 inch driver now, but you have to be rich to even consider it.
Here’s a much more significant design question issue. It’s the concept of half-space, vs full space. I understand the basic idea – in that if you put a horn along the ground (half-space), that the ground itself acts as an extension of the horn – where you can theoretically half the size of the horn mouth, and still achieve a reasonable SPL. Problem – one of the engineering design papers I read was able to mathematically show that the ideal horn mouth circumference – for both full-space, and for half-space loading - is equal to approximately the lower cutoff frequency wavelength of the horn – which is the full-space horn mouth area in both regards. This engineering reference clearly shows that using half-space to reduce the size of the horn mouth, while effective in its ability to reproduce the desired SPL, will cause appreciable increases in horn harmonic distortion.
Question: how significant is this introduced harmonic distortion phenomena (to what the ear hears?)
I’m trying to picture myself cutting the mouth of a trombone to half its original size, resting it up against the wall, then playing it and expecting it to sound just as good. . . . Will it really?
Ok, a solid boundary acts as a reflection, not an extension of the horn. If the boundary is solid enough it acts like an acoustic mirror, and if the boundary is large enough it acts like a mirror over the entire passband.
The ground is not perfectly rigid so it's not a perfect mirror but it's close enough, sims don't lie and accurate sims match measurements.
I didn't read the paper you are referring to but it makes sense to say that a horn that is literally 2x larger will have less THD than one that is 2x smaller. Is that really a surprise?
Instead of your trombone thought experiment try this one instead. Speakers that have flush mounted mids and tweeters (not horn loaded) and normal sized baffles are producing exactly this boundary effect. At the bottom of every driver's passband it's fairly omnidirectional, meaning that a portion of the sound that's emitted will bounce off the baffle and reflect back at the listener. This is well known and you can even simulate this diffraction phenomenon. At the top of the driver's passband the directivity narrows as the frequencies become small in relation to the size of the driver, so these higher frequencies don't bounce off the baffle at all, they just go straight ahead. Furthermore, at a frequency related to the baffle width, the low frequencies wrap right around the speaker and some of the sound heads backwards. The frequency where this happens is the baffle step frequency, and above this frequency the sound gets louder because the sound bounces off the baffle and back towards the listener.
So in most normal (non horn loaded) speakers, you have complex waves. At frequencies above the baffle step and below the frequency where the driver becomes directional, you have a range of frequencies that are louder because the sound bounces off the baffle and comes back at you. This is diffraction and it's the same thing that's happening in boundary reflection calculations. Do speakers sound bad because the baffle size bolsters the output at certain frequencies? No. In fact it's recommended that you flush mount your speakers into a wall if possible to take advantage of the boundary effect.
Part 2 coming up ...
Like I said, if your speaker is close to the ground it is operating in 2 pi space. Therefore your sim should be 2 pi, regardless of whether you designed it for a 2 pi or 4 pi environment. You can't make the ground disappear and I doubt you will be mounting your concrete horn 100 feet up in the air, so you HAVE to sim it in 2 pi space.
For this comparison, since you didn't like my last sim so much I'm showing something completely different. My driver choice for this is 2x Sundown ZV3 18s, roughly same total cost as your five B&C drivers. These Sundown drivers are the exact opposite of your low qts, low mass, high bl drivers. They have a mass of 458.4 grams EACH and due to the lossy inductance issues the effective qts is 0.87 and the effective bl is 11.9. This driver is the exact opposite of what you have chosen. Incidentally it's also rated for 30 mm xmax, which doesn't hurt, although that's where the lossy inductance issues come from.
This design is almost fully 16 times smaller than yours when calculating net volume. If you calculate the difference between wood and concrete (if mine was made of wood and yours was made of concrete) mine would probably be closer to 50 - 100 times smaller. I'm assuming you will probably using 6 inch concrete walls or something like that.
Regardless, no matter what these are made of, 16 times less net volume is very significant.
My compression ratio is very small, just over 2:1. My design doesn't need much high pass filter, it can almost take full rated power without exceeding xmax, but it does need a bit of help from a hpf. I gave your design a high pass filter too to protect it below 20 hz using the 10 mm Xvar.
Top row - Hornresp inputs, your design left (in 2 pi space), mine right
Second row - schematic, your left, mine right, mine is 16 times smaller than yours
Top row - frequency response at max spl, yours left, mine right (both are overlaid in each sim just for convenience)
Bottom row - excursion - yours limited to 10 mm, mine to 30 mm
So even though yours is 16 times bigger it only has a couple db advantage, and only over the first 2/3 of an octave above 20 hz. This is what I meant when I said you could make something a lot smaller for a lot less money and beat your design in every performance metric. While this design doesn't beat yours, if you doubled my system it would beat yours, be cheaper and still 8x smaller.
I'm not saying your design is bad, even with it's 4:1 compression ratio the pressures on the cone are extraordinarily low, peaking at about 1.6 kPa, which is several times lower than most designs. But that is purely an effect of your MASSIVE horn. So I'm not sure how bad distortion due to cone flex would be - I'm not convinced a 77 g cone will be strong enough but due to the very low pressures it won't be a disaster.
Regardless, I would still do it different than your plan. Concrete will crack, it's not mobile, it's expensive, it's work intensive, etc. On the other hand, my tiny little 2000 liter design could be moved around, you could bring it in the house if you wanted to, and you could make it with approximately 3 - 5 sheets of wood, so very inexpensive and lightweight. I'm not saying my design is great, in fact I did it just to be exactly opposite of yours, but it does how my points quite clearly.
For this comparison, since you didn't like my last sim so much I'm showing something completely different. My driver choice for this is 2x Sundown ZV3 18s, roughly same total cost as your five B&C drivers. These Sundown drivers are the exact opposite of your low qts, low mass, high bl drivers. They have a mass of 458.4 grams EACH and due to the lossy inductance issues the effective qts is 0.87 and the effective bl is 11.9. This driver is the exact opposite of what you have chosen. Incidentally it's also rated for 30 mm xmax, which doesn't hurt, although that's where the lossy inductance issues come from.
This design is almost fully 16 times smaller than yours when calculating net volume. If you calculate the difference between wood and concrete (if mine was made of wood and yours was made of concrete) mine would probably be closer to 50 - 100 times smaller. I'm assuming you will probably using 6 inch concrete walls or something like that.
Regardless, no matter what these are made of, 16 times less net volume is very significant.
My compression ratio is very small, just over 2:1. My design doesn't need much high pass filter, it can almost take full rated power without exceeding xmax, but it does need a bit of help from a hpf. I gave your design a high pass filter too to protect it below 20 hz using the 10 mm Xvar.
Top row - Hornresp inputs, your design left (in 2 pi space), mine right
Second row - schematic, your left, mine right, mine is 16 times smaller than yours
An externally hosted image should be here but it was not working when we last tested it.
Top row - frequency response at max spl, yours left, mine right (both are overlaid in each sim just for convenience)
Bottom row - excursion - yours limited to 10 mm, mine to 30 mm
An externally hosted image should be here but it was not working when we last tested it.
So even though yours is 16 times bigger it only has a couple db advantage, and only over the first 2/3 of an octave above 20 hz. This is what I meant when I said you could make something a lot smaller for a lot less money and beat your design in every performance metric. While this design doesn't beat yours, if you doubled my system it would beat yours, be cheaper and still 8x smaller.
I'm not saying your design is bad, even with it's 4:1 compression ratio the pressures on the cone are extraordinarily low, peaking at about 1.6 kPa, which is several times lower than most designs. But that is purely an effect of your MASSIVE horn. So I'm not sure how bad distortion due to cone flex would be - I'm not convinced a 77 g cone will be strong enough but due to the very low pressures it won't be a disaster.
Regardless, I would still do it different than your plan. Concrete will crack, it's not mobile, it's expensive, it's work intensive, etc. On the other hand, my tiny little 2000 liter design could be moved around, you could bring it in the house if you wanted to, and you could make it with approximately 3 - 5 sheets of wood, so very inexpensive and lightweight. I'm not saying my design is great, in fact I did it just to be exactly opposite of yours, but it does how my points quite clearly.
Last edited:
Just for fun, here's my design x2 (so 4 drivers in 4000 liters) compared to yours. Of course mine might exhibit a bit of power compression, as the drivers are getting 1500 watts each, which yours are only taking 150 watts each. But still, 8x smaller than yours (net volume not counting construction materials).
Incidentally I checked on air velocity through the throat on your design. Despite the high compression ratio it's only 5 m/s, so probably a very low distortion throat. Your design is intriguing in several ways but I would still do it different.
An externally hosted image should be here but it was not working when we last tested it.
Incidentally I checked on air velocity through the throat on your design. Despite the high compression ratio it's only 5 m/s, so probably a very low distortion throat. Your design is intriguing in several ways but I would still do it different.
Weltersys, I’m not a big fan of Class-D amplifiers.
Much like the woofer "speed" issue, I think you might be confusing causes and effects. In your analogy, the strong arm is the amp transistors, the damping factor would be something much less vital, like maybe the rubber grip on the hammer handle.
Do you really think you can rate amps accurately based on damping factor impact on transients in subwoofers playing 80 hz and lower in a blind test? I seriously doubt it. Amps can sound different for different reasons but I doubt that damping factor is the overriding factor in sound quality.
I disagree. Reason: it has been shown mathematically that the ideal horn mouth circumference for both full-space loading, and for half-space loading, is approximately equal to the lower cutoff frequency wavelength of the horn, in both regards – which happens to be the full-space horn mouth area. Cutting the mouth in half to take advantage of half-space loading, introduces very appreciable harmonic distortion. (This is does not “outperform in every performance metric. . . .”)Like I said, if your speaker is close to the ground it is operating in 2 pi space. Therefore your sim should be 2 pi, regardless of whether you designed it for a 2 pi or 4 pi environment.
I’m sorry, but you cannot cut the mouth of a tuba in half, stand next to a wall, and expect the horn to sound the same as if it weren’t cut. . . . I’ll tell you what - if you are ever down my way, stop by my house and we’ll take the Pepsi Challenge – I’ll provide the tuba, and you bring a hacksaw. . . . If the half-tuba sounds as good as a full-tuba (simply by playing the half-tuba adjacent to a planar surface), then I'll buy you a 2-liter of Pepsi.
Just-a-guy, for this thread to progress in a constructive fashion, we are in serious need of a paradigm shift. Please remember that my horn project is not space limited. I have no need to fold the horns (a compromise). I have no need to shorten the horns (a compromise). I have no need to reduce the mass of the horns (a compromise). I have no need to make the horns mobile (a compromise). I have no need to half the mouth-area (a compromise). I have no need to make budgetary cuts (within reason). Achieving low distortion & high fidelity is by far more important to me than achieving high SPL.
And I am not trying to compete with you in some online horn simulation contest. I openly acknowledge that I am brand-new at using hornresp, and brand new at horn design in general. I have never actually designed & built a set of bass horns – but I will. . . Also remember that I live in western Washington State, where it rains for about 7 months per year. I am not the slightest bit interested in constructing outdoor wooden horns, because I do not want to deal with wood-rot, mold, mildew, insect attack, damage from snow, damage from wind, damage from rain. I don’t want to clean, paint & preserve the wood every few years. I don’t want to rebuild the horns should a tree fall on them. I don’t want to worry about vandals setting them on fire.
Quality plywood is about 50 bucks per sheet. Question: how many layers of 3/4" plywood do you think I’d need to obtain the proper rigidity in full size bass horns? How many wooden stiffeners do you think I’ll need on the outside of the horn, to achieve the required snow-load & wind-shear load-bearing capacity? A reinforced concrete horn would be acoustically dead compared to virtually any wooden construction technique. Additionally, concrete costs about 100 bucks per yard. That means for the SAME cost of a 4’ x 8’ sheet of 3/4” ply (about 50 bucks), I can have a 4'x8' surface-area of reinforced concrete, 5 inches thick - with no external stiffeners required, and no paint required, or any other array of "issues” associated with outdoor wooden construction. So please stop telling me that concrete is more expensive, because it really isn't. Besides, the cost is ultimately my problem - not yours.
Much like the woofer "speed" issue, I think you might be confusing causes and effects. In your analogy, the strong arm is the amp transistors, the damping factor would be something much less vital, like maybe the rubber grip on the hammer handle.
You have got to be pulling my leg. . .. Damping factor is a function of the final-stage output impedance (aka "the transistors"). The lower the output impedance, the higher the damping factor. The damping factor is so important, that Crown recommends running 8 gauge wire (or even larger for longer runs) for most sound reinforcement applications – specifically for the purpose of maintaining the VERY PRONOUNCED ADVANTAGES inherent with high damping-factor amplifiers. You absolutely can hear the difference in a blind test. I’m actually pretty taken back that one would think otherwise...
The dream of making sound using a horn never goes away for very good reasons. It is conceptually unsatisfying to use a monstrously heavy cone to energize something as relatively light as air. So your choices become:
1. going to better impedance matches such as ESLs, charged-air, "dragon speakers", etc., or one the opposite hand, using intermediary sulphur hexafluoride,
2. corrective circuitry using feedback, or
3. impedance matching such as with a horn.
Seems to me, the appropriate question for a horn builder is what aspects of horn theory can be stretched to make construction feasible without harming valued aspects of performance. Seems to me that is the best course for this thread instead of unhelpful posts in the form of "if you want to smoke here, you must put out your cigarette or go elsewhere".
Ben
1. going to better impedance matches such as ESLs, charged-air, "dragon speakers", etc., or one the opposite hand, using intermediary sulphur hexafluoride,
2. corrective circuitry using feedback, or
3. impedance matching such as with a horn.
Seems to me, the appropriate question for a horn builder is what aspects of horn theory can be stretched to make construction feasible without harming valued aspects of performance. Seems to me that is the best course for this thread instead of unhelpful posts in the form of "if you want to smoke here, you must put out your cigarette or go elsewhere".
Ben
Last edited:
I disagree. Reason: it has been shown mathematically that the ideal horn mouth circumference for both full-space loading, and for half-space loading, is approximately equal to the lower cutoff frequency wavelength of the horn, in both regards – which happens to be the full-space horn mouth area. Cutting the mouth in half to take advantage of half-space loading, introduces very appreciable harmonic distortion.
If you are referring to the information contained in Don Keele's 1973 "Optimum Horn Mouth Size" paper, then you need to be aware that conclusion he reached is not correct. The "ideal" mouth size he observed was due to inherent limitations in the plane wavefront model he was using for his simulations. If he had employed an isophase wavefront model instead, then he would have seen that the mouth impedance mismatch reflections continue to decrease as the mouth size becomes larger, culminating in the limiting case of an infinite horn, which has no reflections. This is consistent with standard transmission line theory.
When radiating into 4 Pi space, making the mouth circumference equal to the cutoff frequency wavelength gives an acceptable performance, and from a practical viewpoint is a reasonable "rule of thumb" to use. If radiating into 2 Pi half space, that mouth area can be halved. The legendary Paul Klipsch used this to good effect in his classic Klipschorn corner horn design, which has a mouth area equal to one-eighth the size it would need to be for comparable performance in free space.
Second harmonic distortion primarily depends on the flaring rate close to the horn throat, not on the mouth area. Most of the distortion occurs near the throat. For minimum distortion the cutoff frequency should be as large as possible.
I disagree. Reason: it has been shown mathematically that the ideal horn mouth circumference for both full-space loading, and for half-space loading, is approximately equal to the lower cutoff frequency wavelength of the horn, in both regards – which happens to be the full-space horn mouth area. Cutting the mouth in half to take advantage of half-space loading, introduces very appreciable harmonic distortion. (This is does not “outperform in every performance metric. . . .”)
You are not understanding me. I didn't say you have to redesign the horn. I'm saying that if you want to simulate what you have designed and see how it will perform in real life you have to simulate it in 2 pi space. A 2 pi sim will match a measurement, a 4 pi sim will not. This is because you will be using it in a 2 pi environment and has nothing at all to do with the reasons behind the design.
I’m sorry, but you cannot cut the mouth of a tuba in half, stand next to a wall, and expect the horn to sound the same as if it weren’t cut. . . . I’ll tell you what - if you are ever down my way, stop by my house and we’ll take the Pepsi Challenge – I’ll provide the tuba, and you bring a hacksaw. . . . If the half-tuba sounds as good as a full-tuba (simply by playing the half-tuba adjacent to a planar surface), then I'll buy you a 2-liter of Pepsi.
You clearly are not understanding the concept of an acoustic mirror, boundary loading. This concept is used in the design of all speakers, it's a fundamental concept. If you can't accept this the discussion will continue to go round and round and get nowhere.
Note that I'm not telling you that you need to redesign your horn. It simulates well. It's not an efficient use of materials but if you like it, that's fine.
Just-a-guy, for this thread to progress in a constructive fashion, we are in serious need of a paradigm shift. Please remember that my horn project is not space limited. I have no need to fold the horns (a compromise). I have no need to shorten the horns (a compromise). I have no need to reduce the mass of the horns (a compromise). I have no need to make the horns mobile (a compromise). I have no need to half the mouth-area (a compromise). I have no need to make budgetary cuts (within reason). Achieving low distortion & high fidelity is by far more important to me than achieving high SPL.
I see all those things as advantages, not compromises. If you see them as non starters that's fine, I can stop trying to convince you otherwise. A mobile horn can be protected by taking it inside and it could last forever. Your concrete horn left outside has a shelf life, but if that's what you want I'm fine with that and will not try to convince you otherwise.
And I am not trying to compete with you in some online horn simulation contest.
I don't view this as a contest either. I made some points, you questioned them, I proved my points with sims of different designs.
You have got to be pulling my leg.
I'm really not that interested in amps, any type of amp can do well at subwoofer frequencies.
Last edited:
Entropy,1)The shoreline however is loaded with trees – thus I'm pretty sure the trees contribute significantly to the echo-return. I’m not sure what to do about the tree line on my property. Maybe I could selectively thin the trees, so that the impedance mismatch between the open air and the woods is not so pronounced?
2)Weltersys, I’m not a big fan of Class-D amplifiers. Yes they are low-cost, lightweight, and very energy efficient. They are a blessing for DJs, and small touring bands.
3)However the Berhringer NU4-6000 for example, has a damping factor of 120. In my opinion, 120 is a serious problem – it is way too low. The threshold for an audiophile quality amplifier is typically a damping factor greater than 300. This is why I am such a big fan of the Macro-Tech series (the older ones that were built with very heavy copper-wound transformers). The MT series packs a big-time damping factor greater than 1000. Between all of the advertised amplifier specifications (THD, frequency response, Signal to Noise ratio, channel separator, slew rate, etc), it has been my experience that the damping factor specification alone is the best overall indicator as to how well the amp is going to sound. Again, it's just one man’s opinion. . .
4)Below are bass-guitar speakers that I built for the wife. They are powered by 10-kW of greater than 1000 damping factor amplification. The 18s are tuned for 30-Hz, and sound absolutely fabulous on a 5-string bass! Yes, some people prefer a wall of 10s for a bass, but this system sounds pretty good too. . .
1) The "pronounced impedance mismatch between the open air and the woods" is an interesting concept, but acoustically has no bearings.
The tree line defines your particular outdoor venue, if you want a less defined echo, go ahead and thin the trees, though it will make little difference at the listening position.
In an open air environment, sound drops at 6.01 dB per doubling of distance from the source, with a 7 second return time the round trip distance is around 2434 meters, just over 11 doublings of distance. Even if the tree line was substituted with a hard wall of infinite height, the return echo would be a bit more than 66 dB down, 6 dB less than what is read in an RT60 (the the time needed for a test signal to drop 60dB) test. If your sub is playing at 130dB SPL at one meter, the return level in actuality will be some 10dB less than the theoretical maximum, about 54dB, lower than typical wind and animal ambient SPL levels.
2)"Small touring bands" like U2, who carry enough Class-D amplifiers to power thousands of loudspeakers in 100,000 seat stadiums. The Class-D weight reduction and 50% reduction in AC power required for the same output power has made virtually all major sound companies convert. Some have simply held on to old "heavy metal" amplifiers because they continue to work, but the damping factor issue is simply not part of the decision, since the cable length/AWG plays so much more a role, and ends up being a factor that can't be "fudged", you can save weight on amps, but not on cable.
3)The amount of attenuation that electrical damping provides at the speaker is:
DF10 = -20 dB, DF20 = -26 dB, DF30=-30 dB, DF 40=-32.5, DF50 = -33 dB, around a 6 dB difference per doubling of damping factor. A net DF of 50 is considered by most to be good enough for critical listening.
My buddy Bennett, the North American Sales & Operations Manager for B&C loudspeakers wrote this piece about damping factor, which I agree is quite important for tight bass reproduction:
http://bennettprescott.com/downloads/dampingfactor.pdf
As he explains in the PDF, a 50 foot piece of 12AWG wire on an amp with a DF of 5000 (like the Crown I-Tech 8000) has a net DF of 50.25, good enough for critical listening (about 20 is OK for PA use). An amp with a DF of 500 will reduce the damping factor to 49.14.
Dropping the amp's DF to 100, we find a still remarkably good net damping factor of 44.75, not even 12% worse than an imaginary half-million DF amp.
If you do like I do, and reduce the length of the wire connecting the sub to the amp to only 15 feet, the net damping factor of the NU4-6000 at an 8 ohm speaker is probably 50 or greater, do the math if you doubt it (which is always OK with me, math is not my strongest suit, have been corrected by other forum members from time to time when they bother to read my drivel).
4) The phase response of a TH is smoother than a BR with the same Fb, you might like it's sound better. The new Keystone B-Low version with an excursion minima at around 29 Hz, will definitely do justice to the low B of a five string bass, and will also do fine for the 27.5 Hz low note on a grand piano.
Having started off my career exclusively using straight (no fold) FLH horns, I can attest that folds make no acoustical difference below 125 Hz, and TH have similar impact to FLH, while using less material to do so.
Art
Last edited:
- Status
- This old topic is closed. If you want to reopen this topic, contact a moderator using the "Report Post" button.
- Home
- Loudspeakers
- Subwoofers
- Concrete Bass Horn Design Question