If I do glass, there is a shop on my street that would probably charge me $20 a baffle for anything I could draw or template.
Aluminum and steel are easier for me than wood - it takes a lot longer, but it is impossible to mess up unless you measure wrong. I can throw a steel speaker through a 2 story window and have less damage than my wife stubbing her toe on a veneer speaker.
A half-and-half, like Face was suggesting, might bring down the build time. That is, make a very simple rectilinear box out of substance X (steel, MDF, a laminate, whatever), then add the floating baffle to give it a face (pun intended) of solid wood, which would house all the complicated bits (driver cutouts, port, rounded edges).
A possible secondary benefit is that you could try several different baffles, to experiment with different driver layouts, while keeping the same box.
The first link contains horns not enclosure so it doesn't count. The second link contains a solid timber enclosure that is already severely cracked from the start! And they are a believer of first order crossover. IMHO it's an attractive piece of furniture meant for large pocket audiofools ...There are a few commercial examples that seem to refute the dogmatism that wood will swell "no matter what" - boutique companies, such as Sierra Brooks and OMA did build / still build with solid timber. I've not heard of their stuff disintegrating due to changing humidity.
Oswalds Mill Audio - Imperia | OMA Loudspeakers
The linked speakers are aesthetically up my alley. I would be sad to hear that they split apart the next time it rained:
https://www.fernandroby.com/products...tower-speakers
I'm not 100% sure why my own low-skilled efforts have been an exception to the "no matter what" lore, but I suspect that my preference for old (recycled) wood may be a factor.
I'm not sure I'm understanding correctly, but ***milled*** hardwood IMHO is not hardwood anymore. How are hold together all the particles?
Ralf
hollowboy,
It's not the solid wood that's a problem it's the mix of something that expands and something that does not without careful planning. In the attached photos note that the sides top and bottom all have the grain the same direction. this box expands and contracts front to back with the seasons... no problems. The baffle is plywood and sits in a groove.
Totally off topic I met Jonathan Weiss, the owner of Oswalds Mill Audio, at ICFF ICFF | High End Luxury Furniture Fair | NYC a few years ago. His stuff looked so cool. I was really excited to talk to him and was pretty disappointed when I realized what an a$$ he is.
It's not the solid wood that's a problem it's the mix of something that expands and something that does not without careful planning. In the attached photos note that the sides top and bottom all have the grain the same direction. this box expands and contracts front to back with the seasons... no problems. The baffle is plywood and sits in a groove.
Totally off topic I met Jonathan Weiss, the owner of Oswalds Mill Audio, at ICFF ICFF | High End Luxury Furniture Fair | NYC a few years ago. His stuff looked so cool. I was really excited to talk to him and was pretty disappointed when I realized what an a$$ he is.
Attachments
Everyone is building speakers out of MDF, using a router to cut an indentation for the flange, so the drivers are flush.
Wouldn't it be easier and more precise to just cut holes, surface mount the drivers, and then add an extra layer the same thickness as the flange with a larger hole?
Instead of a router, you'd probably need a planer to provide the thickness to match the driver flange. There is no standard flange thickness, in my experience.
A jointer and planer, IME.Instead of a router, you'd probably need a planer to provide the thickness to match the driver flange. There is no standard flange thickness, in my experience.
Well, to correct the first post, not everyone is building speaker boxes from MDF - but if you do, post assembly veneering is a simple enough process, and far less costly per area than many solid woods.
Someone mentioned Corian (Dupont brand name) - any acrylic solid surface material could generally work). They're a great decorative product, and relatively easy to fabricate with carbide tipped woodworking tools. But they have virtually no screw holding capacity, so should be only considered as decorative.
I've been exclusively using Baltic Birch plywood for at least 15yrs - some of the higher quality varieties "ApplePly", etc have decent enough "Architectural" grade face veneers to directly take a wide range of finishes. Notwithstanding the occasional knot patches, mineral stains, etc, even the shop grades can take a natural / clear lacquer / shellac / varnish finish very nicely.
ps: evan - yes, there are more than a few talented, brilliant, idiosyncratic artisans in the bespoke audio business whom should never be allowed to speak to prospective customers - or at least only under tight rein. I've met some of them at small audio shows.
Someone mentioned Corian (Dupont brand name) - any acrylic solid surface material could generally work). They're a great decorative product, and relatively easy to fabricate with carbide tipped woodworking tools. But they have virtually no screw holding capacity, so should be only considered as decorative.
I've been exclusively using Baltic Birch plywood for at least 15yrs - some of the higher quality varieties "ApplePly", etc have decent enough "Architectural" grade face veneers to directly take a wide range of finishes. Notwithstanding the occasional knot patches, mineral stains, etc, even the shop grades can take a natural / clear lacquer / shellac / varnish finish very nicely.
ps: evan - yes, there are more than a few talented, brilliant, idiosyncratic artisans in the bespoke audio business whom should never be allowed to speak to prospective customers - or at least only under tight rein. I've met some of them at small audio shows.
Last edited:
Why start with mdf? Start with 1/2" ply and "veneer" with 1/2" solid wood.
Holes? Up to 7" inches, use a small drill press and wing cutter.
Wing cutters can found on-line or tools shows for $5 - $10 bucks.
On a small build, cutting holes is the easiest/fastest task.
[use slowest speed on drill press]
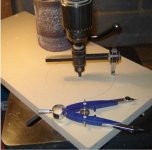
Holes? Up to 7" inches, use a small drill press and wing cutter.
Wing cutters can found on-line or tools shows for $5 - $10 bucks.
On a small build, cutting holes is the easiest/fastest task.
[use slowest speed on drill press]
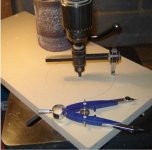
- Status
- This old topic is closed. If you want to reopen this topic, contact a moderator using the "Report Post" button.
- Home
- Loudspeakers
- Multi-Way
- 2 layers of wood