BBC Technics SP-10 Mk2-P StudioTurntables RP2/9 SH-10 EP Controls & MP1-18 Arms | eBay
I think the guy is having a giraffe with the starting price, but if you had a big enough living room that would be nice to have.
Isn't this the third time he has listed it ?
Dave
hi,
I have got a SP10 Mk2 from my neighbour. Unfortunatelly it has a few problems:
- On/Off key does not work. It spins up on power on. I have tested the switch for OK.
- Does not hold the speed. 33 is much to slow, 45 and 78 is much better.
What I have done:
- checked the Power Supply. Voltages are OK
- replaced all el. caps with Panasonic FC (a few where realy fat..).
any ideas ? I am located in Munich
many thanks
Dieter
I have got a SP10 Mk2 from my neighbour. Unfortunatelly it has a few problems:
- On/Off key does not work. It spins up on power on. I have tested the switch for OK.
- Does not hold the speed. 33 is much to slow, 45 and 78 is much better.
What I have done:
- checked the Power Supply. Voltages are OK
- replaced all el. caps with Panasonic FC (a few where realy fat..).
any ideas ? I am located in Munich
many thanks
Dieter
I havent read the whole tread (yet)...
Reducing rumble and vibrations from electric motors can be done by reducing the voltage. Since the speed of this gem is not defined by its voltage but the crystal, have you tried to lower the voltage to the point when it dies?
For me it´s not very interesting to have the record spinning up on 1/8 of a second, i do not need that power, i need it to spin just at the right speed but wit less available power. Maybe 20 volt would be a good start. Measurements shows he spectrum of the rumble and it´s mostly frequencies below 300Hz. And my feeling is that the origin is the motor itself. Anyone tried? Well i will. First i will take some nice accellerometers and connect to my B&K rig. Document the rumble results and go for some power decrease nad new measurements. The wow flutter will be measured separately by my FFT analyzer taking the signals from the stroboscope and a photo reflectometer...
Reducing rumble and vibrations from electric motors can be done by reducing the voltage. Since the speed of this gem is not defined by its voltage but the crystal, have you tried to lower the voltage to the point when it dies?
For me it´s not very interesting to have the record spinning up on 1/8 of a second, i do not need that power, i need it to spin just at the right speed but wit less available power. Maybe 20 volt would be a good start. Measurements shows he spectrum of the rumble and it´s mostly frequencies below 300Hz. And my feeling is that the origin is the motor itself. Anyone tried? Well i will. First i will take some nice accellerometers and connect to my B&K rig. Document the rumble results and go for some power decrease nad new measurements. The wow flutter will be measured separately by my FFT analyzer taking the signals from the stroboscope and a photo reflectometer...
Anyway, I don't think your idea will work as the motor drive looks at the reference freq. vs the platter speed via a comparator, and the output of that comparator adjusts drive voltage as needed to get the platter to "catch up" (or slow down) to the reference. If the platter is a teeny bit slow, it increases the voltage a teeny bit, if it's quite a bit different, it changes the voltage quite a bit. Yes, there is a voltage reference also, so it has to run at the design point.
That said, I'd love to see any data you can measure, and see if there's anything that can be improved.
After talking to a few people who've been down this road, I realize I need to just plain make the plinth heavier. So, the big drill bit comes out and Swiss cheese ensues.
![]()
"Each tuned to a different frequency. "
(One of my favorite audio marketing BS phrases...) Anyway, the green epoxy is a 3M product that never dries totally solid. The rest is just cheap 5-min.
Mass has been increased by at least 2kg. Maybe a bit more.
Next, aligning the motor drive.
I am curious about the lead shot pockets in your plinth. I see that many of these shot pockets have been infused with the green epoxy you allude to. Is there any reason in your planning to use the epoxy?
The reason I question this is that my understanding of the reasoning behind including lead shot pockets within a plinth design is to actually promote the interaction of the individual lead shot with one another as vibrations flow about within the plinth. The idea being similar to using a sand box where the individual grains of sand intereact with the flow of vibrations. It would seem that inclusion of any epoxy, which solidifies the shot into a single mass, would prevent this. Therefore, I presume the entire reason for including lead shot is simply to increase the weight of the plinth, is this correct?
-Steve
The epoxy is deep enough to secure the lead in the hole. Nothing more. I used the green (fantastically expensive) stuff because I ran out of 5-min.
Yes, it's heavier.
No, the shot is not completely infused with resin.
No, it's not "tuned to a different frequency", well, not intentionally anyway, I'm saying that tongue-in-cheek because a certain British TT manufacturer claims that for the 3 identical feet on the bottom of their plinths, because as each supports a different amount of weight, they all resonate at a different freq. ... LOL

Yes, it's heavier.
No, the shot is not completely infused with resin.
No, it's not "tuned to a different frequency", well, not intentionally anyway, I'm saying that tongue-in-cheek because a certain British TT manufacturer claims that for the 3 identical feet on the bottom of their plinths, because as each supports a different amount of weight, they all resonate at a different freq. ... LOL
Back 1-1/2 decades ago the group that started out as a diy turntable group but morphed into three different manufacturers, Teres, Galibier and RedPoint. In that group it was generally considered that shot pockets of #9 lead shot should be prepared in one of two ways; 1) dry and loose or 2) loose but filled with thin viscosity silicon lube. The argument in favor of the silicon lube was that it served to induce the lead shot to interact with vibes passing through. But it was necessary to make the pocket liquid proof. Which was easy if your material was acrylic or some other resin.
Since then I've used loose and dry #9 lead shot pockets in various plinth projects. To some observable benefit, imho.
-Steve
Since then I've used loose and dry #9 lead shot pockets in various plinth projects. To some observable benefit, imho.
-Steve
Last edited:
Sorry, the first time I read this I (incorrectly) saw "piles" (as in, 'two piles of dirt') instead of the plural of ply, which you spelled correctly. Lol

Jim how many plies do you have? 5,6? Can't see exactly
Updates -
You can see the electronics out of the way in order to get the heat on the bearing cap. I used a bit of aluminum foil as a heat shield just to be sure, but didn't get a photo of it.
The old ball, interestingly the ball is interference fit into the bearing well and it makes an oil seal, the bottom was dry, the top was wet. Neat! It needs to be bonked out with a chopstick or something non-maring, from the top.
The old thrust pad
New Si3N4 (Silicon-Nitride) bearing ball - https://www.mcmaster.com/#9576k36/=16dcmjm
I see no reason to use heat-release thread sealant (loctite) on the bearing cap, so you can see the regular blue used here.
Remember to clean the gunk off the bearing well before re-assembly (shown here before cleaning) and add a few drops of oil.
Reassemble and attach to plinth
This is starting to look pretty good! Yes, I'm missing the Technics badge in the front right. No, I don't remember where I put it...
Mounting the arm, step one. Measure the specified distance from the spindle and mark. (I don't remember what the specific distance was, it was in the manual...)
Drill hole.
Arm mounting jig. This is one of the reasons I have a complete love for Graham tonearms, they are so ridiculously easy to mount, align, and use. This jig is placed over the spindle as such and then ;
You simply place the arm in the rough hole and on the jig, then mark the armboard under the mounting holes. Easy!
Drill them out and secure the arm. That's it. Insanely simple. Thank you Bob Graham.

You can see the electronics out of the way in order to get the heat on the bearing cap. I used a bit of aluminum foil as a heat shield just to be sure, but didn't get a photo of it.
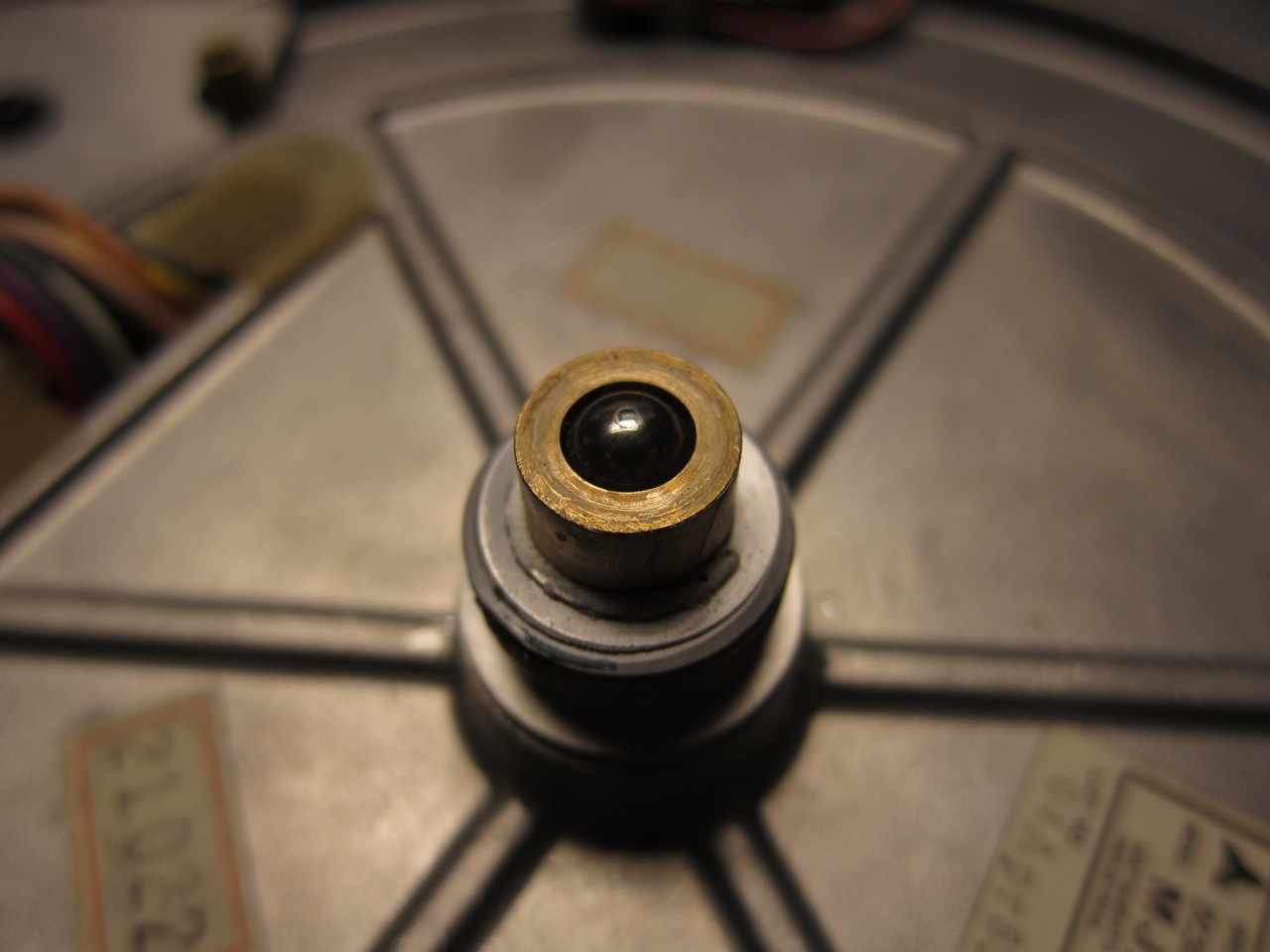
The old ball, interestingly the ball is interference fit into the bearing well and it makes an oil seal, the bottom was dry, the top was wet. Neat! It needs to be bonked out with a chopstick or something non-maring, from the top.
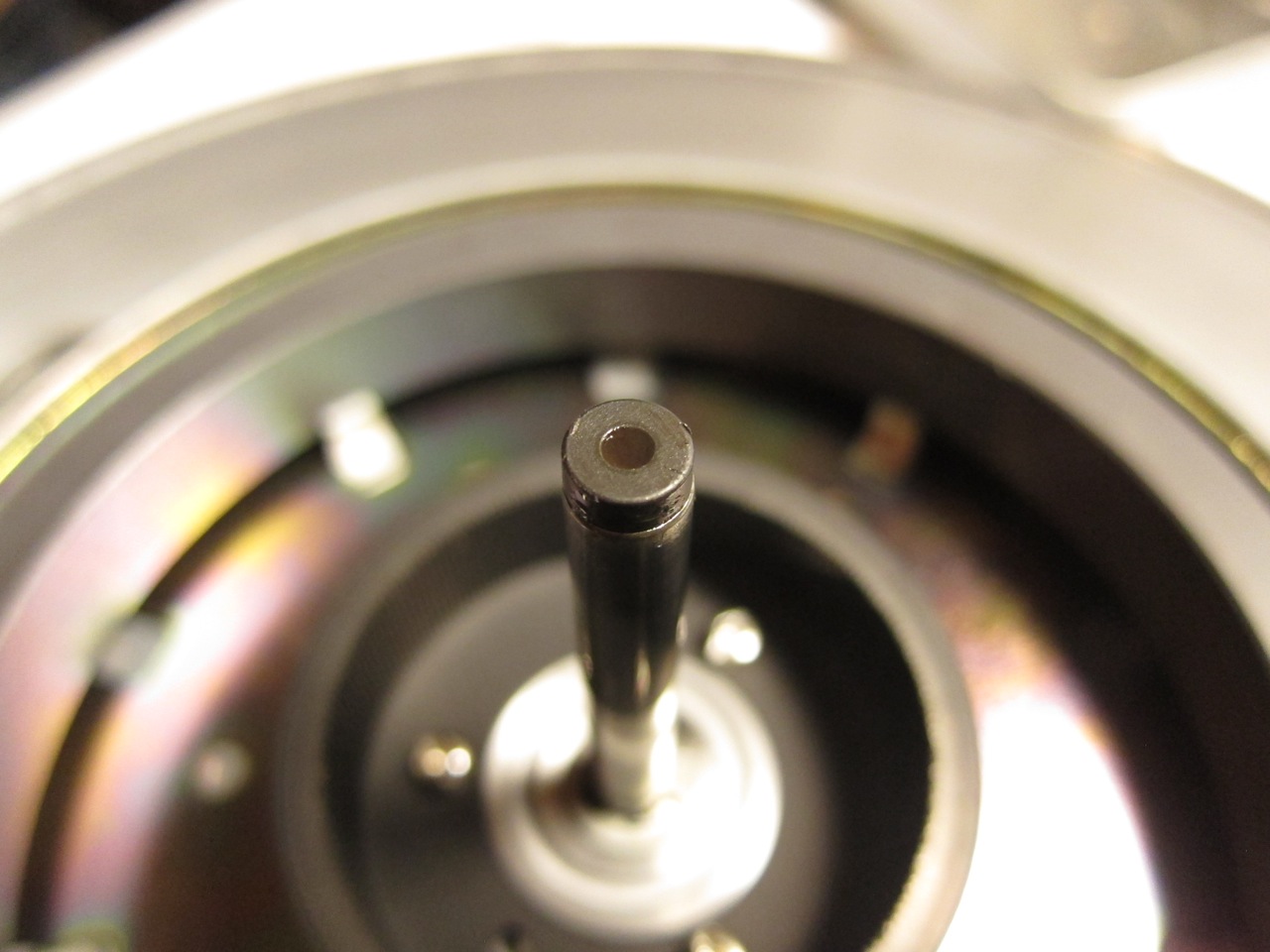
The old thrust pad
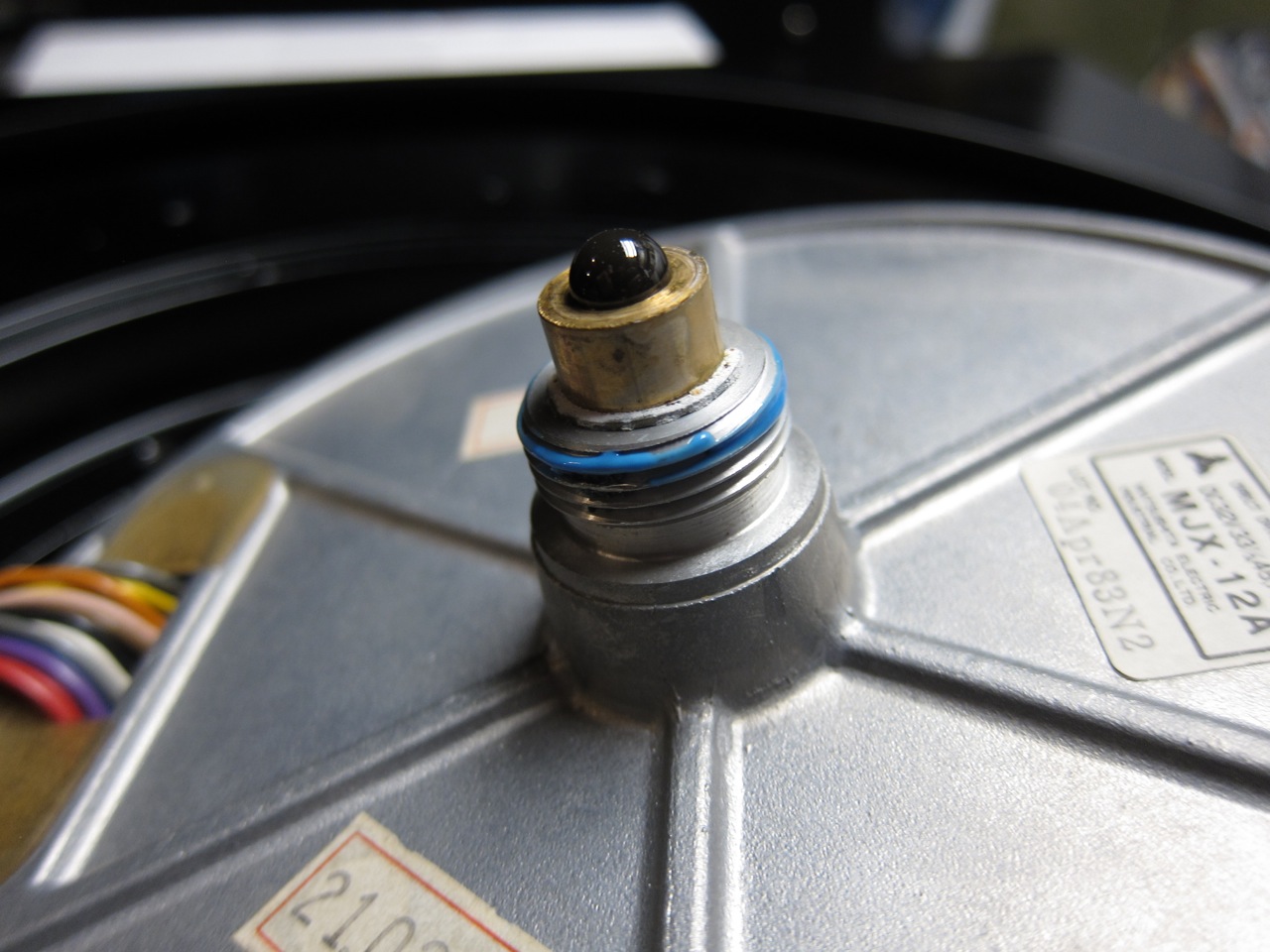
New Si3N4 (Silicon-Nitride) bearing ball - https://www.mcmaster.com/#9576k36/=16dcmjm
I see no reason to use heat-release thread sealant (loctite) on the bearing cap, so you can see the regular blue used here.
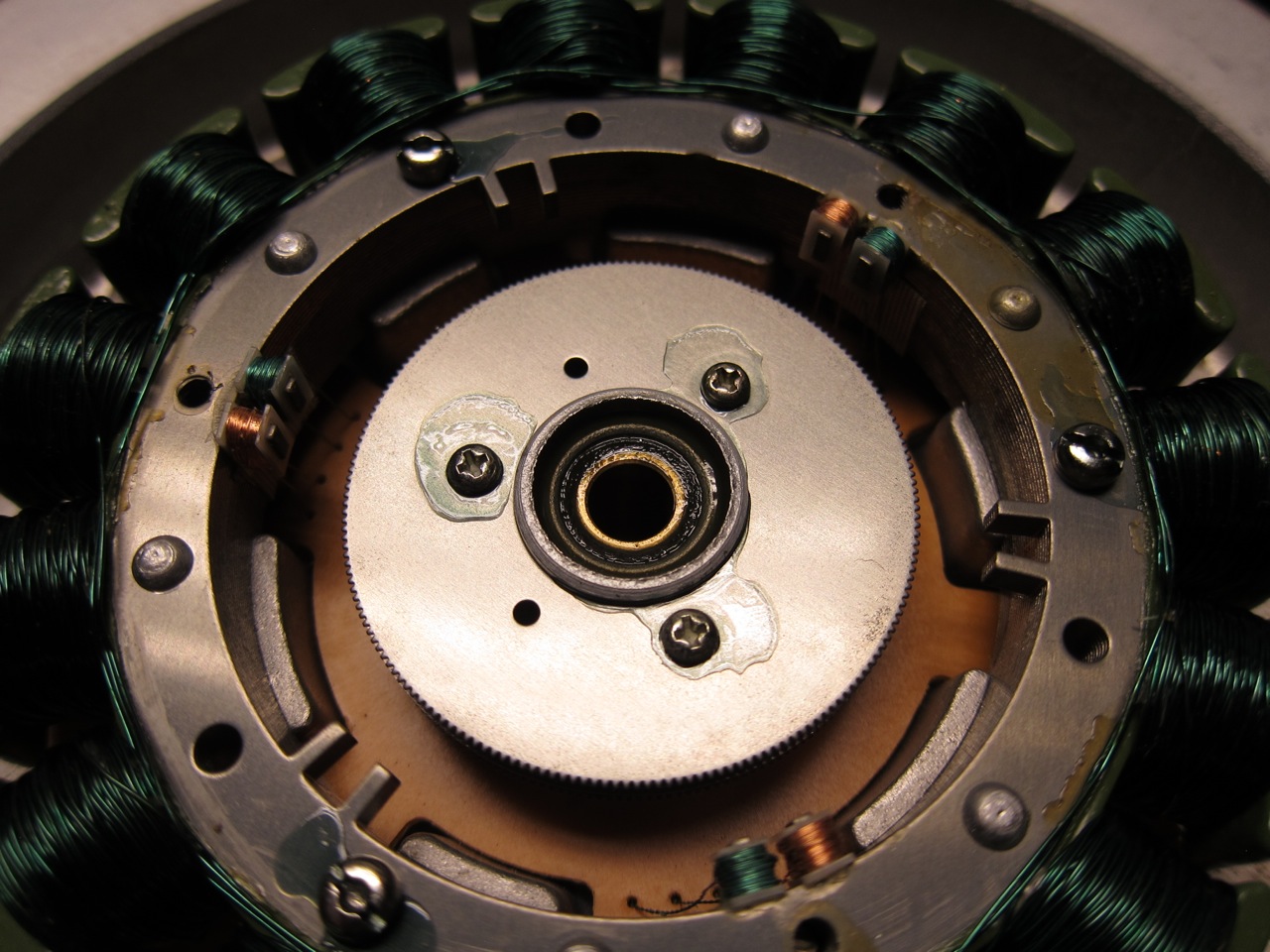
Remember to clean the gunk off the bearing well before re-assembly (shown here before cleaning) and add a few drops of oil.

Reassemble and attach to plinth
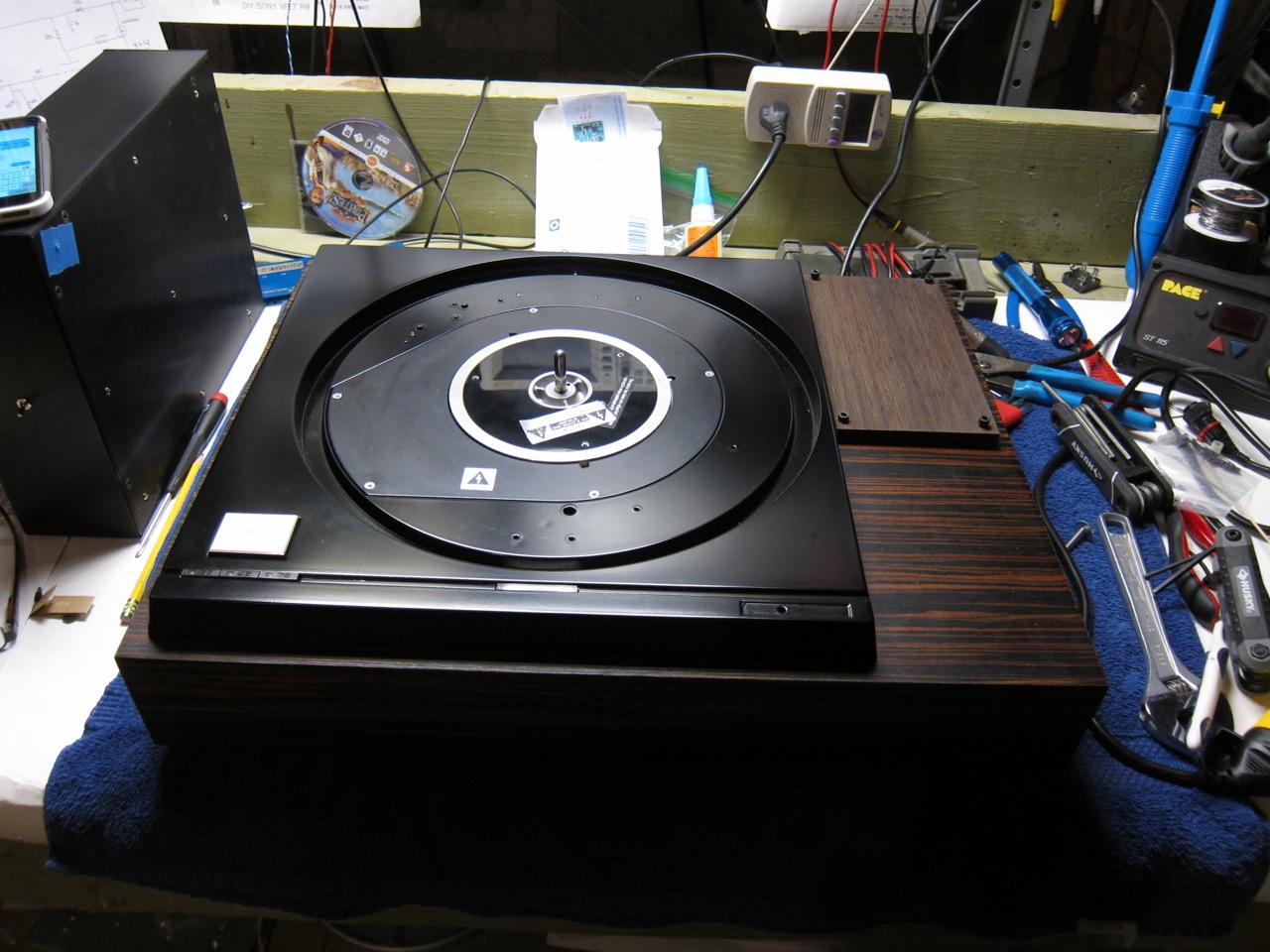
This is starting to look pretty good! Yes, I'm missing the Technics badge in the front right. No, I don't remember where I put it...
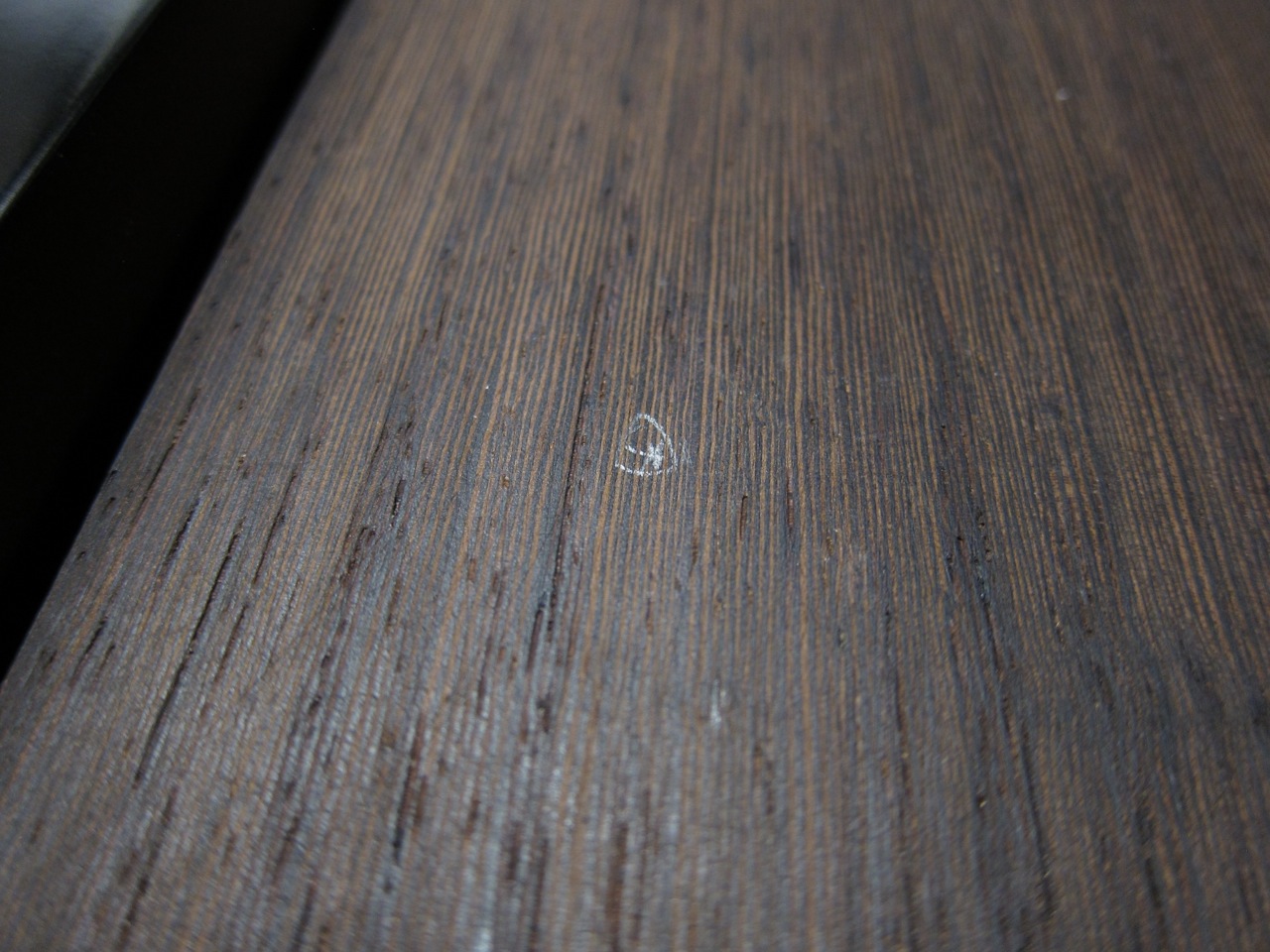
Mounting the arm, step one. Measure the specified distance from the spindle and mark. (I don't remember what the specific distance was, it was in the manual...)
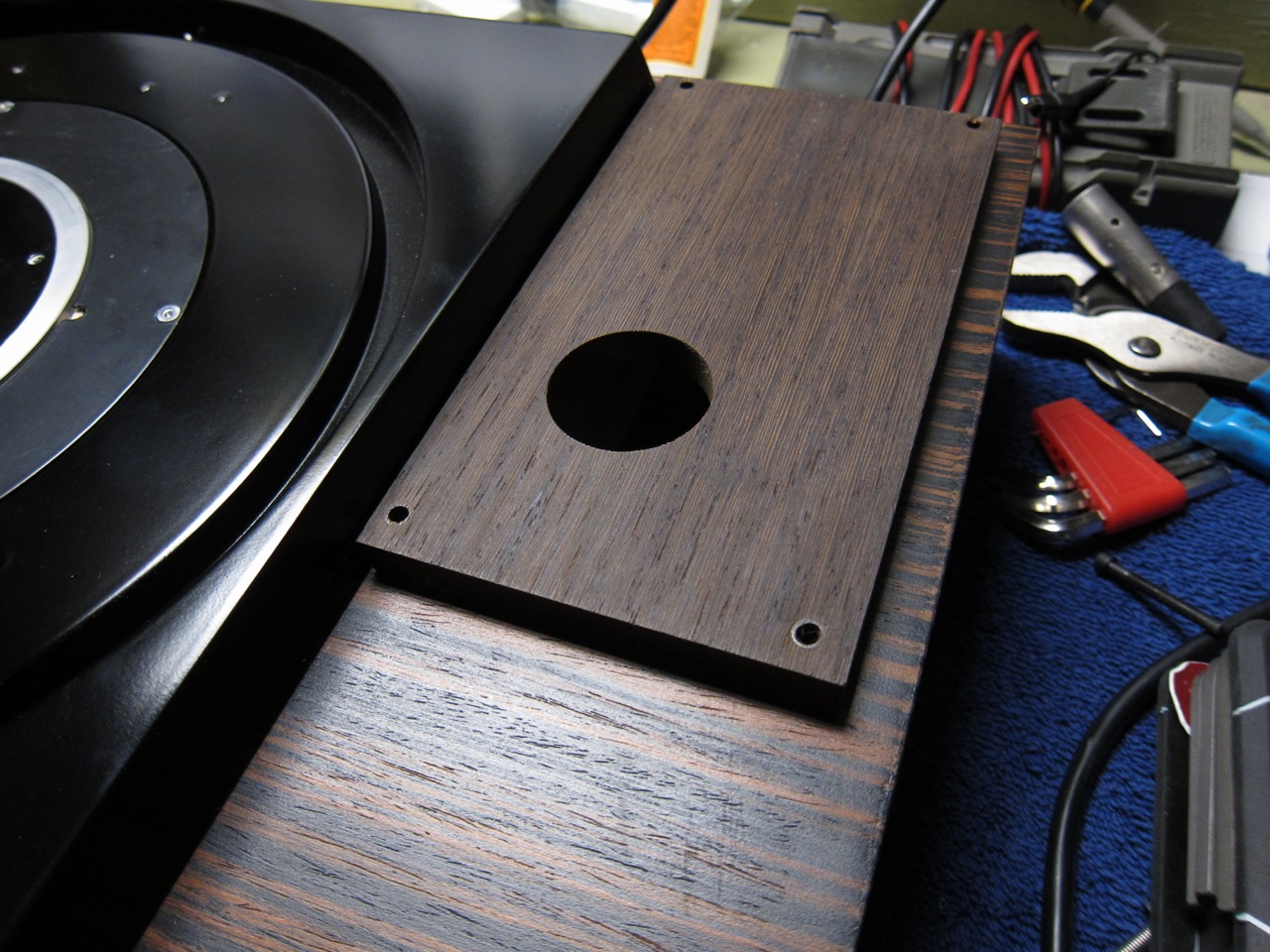
Drill hole.
Arm mounting jig. This is one of the reasons I have a complete love for Graham tonearms, they are so ridiculously easy to mount, align, and use. This jig is placed over the spindle as such and then ;
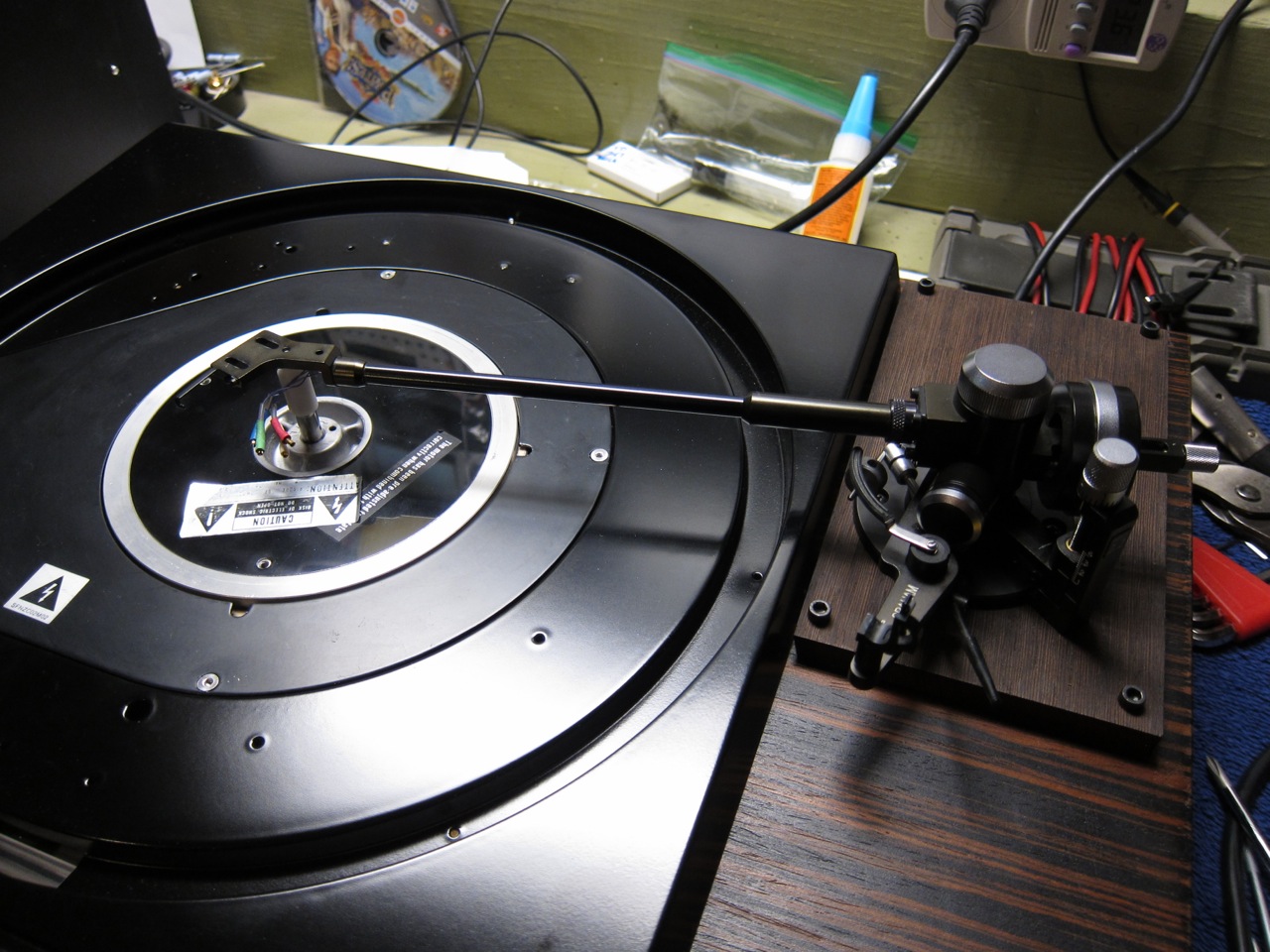
You simply place the arm in the rough hole and on the jig, then mark the armboard under the mounting holes. Easy!
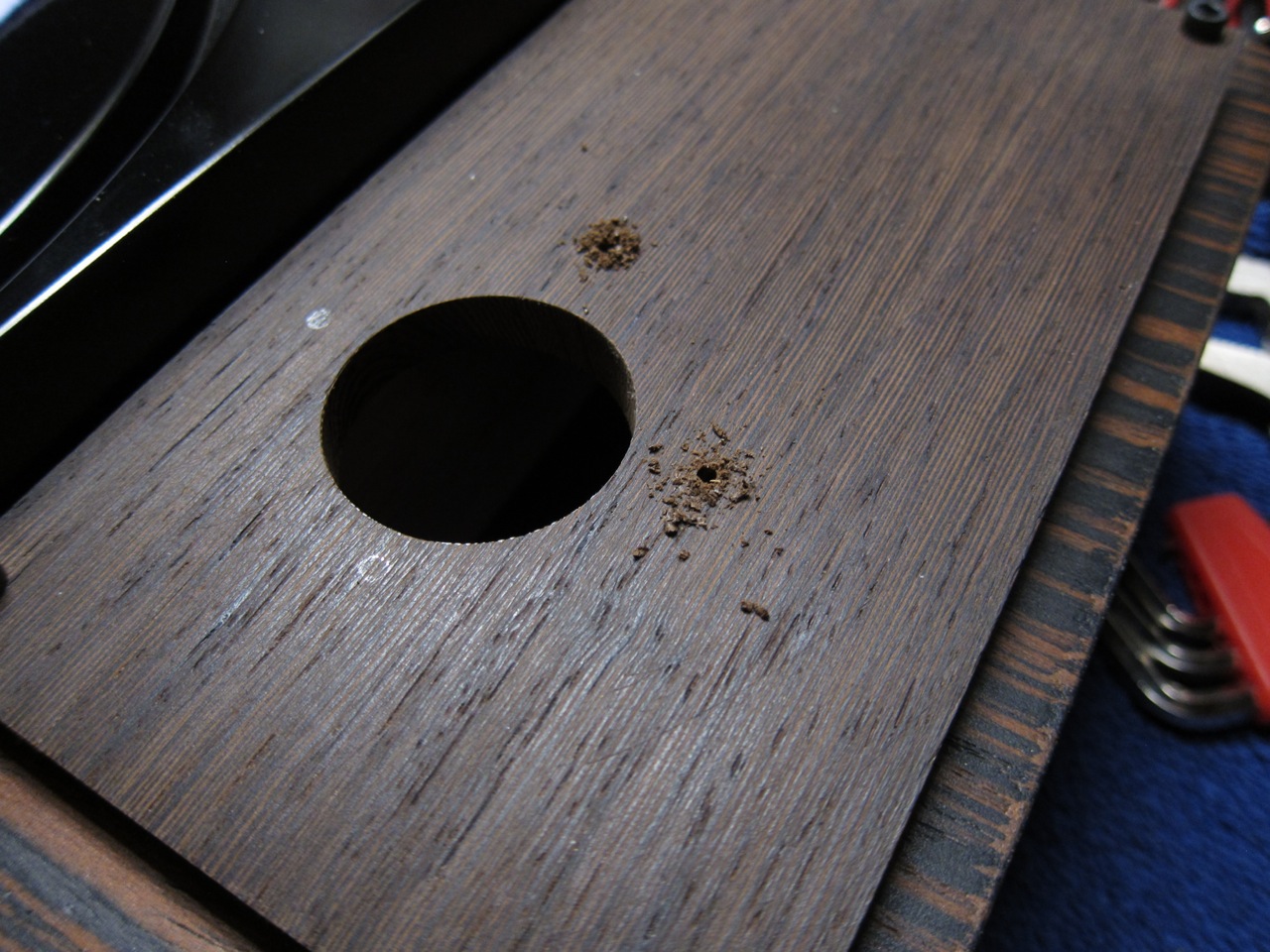
Drill them out and secure the arm. That's it. Insanely simple. Thank you Bob Graham.
Last edited:
- Home
- Source & Line
- Analogue Source
- The Incredible Technics SP-10 Thread