Design philosophy and failed experiments
Hi all,
All of the work that I have undertaken developing my new bearings has resulted in a significant sonic improvement. This improvement pales in comparison to the difference in sound quality that can be achieved with a properly sorted carriage design. I have described the goals of this design before in this thread but will expand my design philosophy further here.
The main cause of colourations in a conventional tonearm are the bending modes in the arm tube that occur at and above the resonant frequency of the arm. Below the arms resonant frequency the arm tube acts as a rigid beam controlled by the effective mass of the arm. Above the resonant frequency the arm tube is constantly flexing and is controlled by the rigidity and damping of the arm tube. Most tonearms have their resonant frequency right in the middle of the midrange, the worst possible place. Damping is then applied to try and control this. Damping helps but the arm is still not rigid over most of the audio bandwidth and therefore the cartridge is not properly controlled. At higher frequencies less energy is transmitted from the stylus/groove interface to the arm plus, as a bonus higher frequencies are easier to damp. The higher the resonant frequency the better.
My approach to solving this problem and eliminating colouration was to design an arm whose resonant frequency was outside of the audio bandwidth, above 20khz. This would mean that the arm acts as a rigid beam across the entire audio bandwidth. If there are no bending modes there are no colourations. Also virtually no damping would be required. To achieve this the arm has to be incredibly rigid. The best way of increasing rigidity is to make the arm very short. Making an arm very short dictates that it has to be a linear trackers.
Resonant frequency is not just dependent upon rigidity but also on mass and how that mass is distributed.
Making the arm short also makes it lighter .In addition to making the arm short making it short and broad will increase rigidity. However, making the arm broader will increase its mass. Tapering the arm, making it thinner at the ends and thicker in the middle, removes mass from the ends and places more material in the centre where the bending forces would be at their highest. This improves mass distribution and maximizes rigidity pushing the resonant frequency higher still.
The choice of materials used also has a great impact. Ideally you want a material that is both very stiff and lightweight. Carbon fibre composite is an ideal material in this aspect having a very high stiffness to density ratio. This ratio can be enhanced further by, instead of using solid sections, using thin skins of composite over a lightweight core. End grain balsa wood, where the grain is perpendicular to the skins, is the best material for this application. Carbon fibre/balsa composite panels have the added benefit that they have excellent self damping characteristics. The carbon fibre composite sheet that I used for this arm is not just a standard piece. I had the sheet especially made with the fibres in each lamina specifically aligned to maximize its properties.
In my design the carriage has carbon composite structural members that pass both above and below the rail. This has the advantages of not only maximizing rigidity but also makes it impossible to accidentally derail the carriage.
Rather than having a conventional headshell that protrudes from the front of the arm the cartridge sits in a recess within the carriages body. Buttresses, that connect the upper and lower panels of the arm, surround the cartridge. In order to keep the recess as small as possible, just big enough to take the cartridge, the cartridge tags have been cut down so they take up as little space as possible. The counterweight and its adjuster sit in similar recesses in the rear of the carriage, keeping the rear end as solid as possible.
Longitudinal bending waves are not the only mechanism by which vibrational energy is transmitted through the carriage though they are by far the most significant. Similar to longitudinal bending there are also torsional modes. These twist the carriage along its length. Luckily tonearms have inherently high torsional rigidity and a torsional resonant frequency above the audio bandwidth. My carriage has a torsional resonant frequency of at least 70khz, probably more than 100khz.
A mechanism of greater significance is compression waves also known as sound waves. These propagate from their source, mainly the cartridge, through the carriage at the speed of sound for the material the carriage is made of. When these waves hit a boundary or interface they reflect back. The amount that is reflected is dependent upon the impedance of the boundary. A low impedance boundary, such as between the arm and the air, will reflect a small proportion of the initial wave. A high impedance boundary, such as between the arm and a bearing yoke or counterweight, will reflect strongly.
A sound wave/impulse originating at the cartridge travels through the carriage at the speed of sound, reflects at a boundary then travels back to the cartridge. The difference in arrival time from the original sound wave/impulse to the arrival of the reflection creates a time smear. This has the effect of softening transients, masking low level detail and blurring imaging.
There are many methods of reducing this effect. The best method is to insure that the reflection arrives as soon after the initial signal as possible, ideally within a wavelength. This would mean that the distance from the cartridge to the reflection boundary is a half wavelength of the highest frequency. Two methods of achieving this exist. Make the arm from a material that has a very high speed of sound (beryllium would be lovely here with a speed of sound of 12km/s). The other is to minimize the distance from the cartridge to the reflection boundary or more simply put, make the arm short. Of course combining both of these approaches is better still. The speed of sound through carbon fibre composite is about 3.5km/s. My carriage is about 100mm long in total. A 200mm wavelength at 3.5km/s equates to a frequency of 17.5khz
Another method is to make the arm irregular with lots of low impedance boundaries that act to scatter the sound wave. More by luck than design my carriage fits this description very well.
Attenuating the sound wave as it passes through the arm will mean that there is less energy reflected back. Alternating layers of material with a high speed of sound with ones with a lower speed of sound can be effective at minimizing sound wave propagation. End grain balsa laminated with carbon fibre composite sheets is particularly good in this respect and is often used in high tech acoustic panels for this reason.
Lowering the impedance at the reflection boundary will reduce the amount of energy returning to the cartridge. This is why many tonearm designs have decoupled counterweights, to reduce the strength of the reflection. Decoupling, especially using compliant materials, can have additional benefits or create other problems and its success will be largely design dependent. Alternatively using a smaller counterweight will reduce reflection. This is undesirable with longer arms where a heavy counterweight close to the pivot is generally preferred. A short arm only requires a small counterweight anyway.
I did not just blindly chase high rigidity and high resonant frequency. The design of the carriage was carried out using a spread sheet that calculated the arms resonant frequency in both vertical and lateral planes. It also calculated effective mass, vertical and lateral (lateral is just total carriage mass), tracking force and tracking force variation due to warps and the level of warp wow. This spread sheet is like a simplified finite element analysis program set up specifically for this application. The techniques used in creating this spread sheet were developed whilst researching my dissertation whilst I was at university studying composite engineering. I had great fortune in being able to wangle having vibration analysis of composite structures as my dissertation subject. The university material lab had lots of lovely test equipment that allowed me to verify that my mathematical models were accurate. I wonder how many manufactures actually carry out vibration analysis on their designs rather than using trial and error.
An unusual feature of this design is that the carriage runs very close to the record surface with only a 2.5mm clearance. This is so that the vertical pivot can be kept as low as possible to minimize warp wow and so that the centre of mass can be on the same plane as the vertical pivot in order to minimize tracking force variation due to warps. The rear of the arm slopes upwards slightly to prevent the rear of the carriage from fouling the record whilst queuing. When queuing the stylus is lifted only 3mm from the record. This may seem alarmingly close but as the carriage sits securely on the rail this has never been an issue. Of course decent record clamping helps here.
When designing this arm I designed specifically to match an ortofon 2m black cartridge, which is the cartridge I am currently using.
When I initially started the design process I set targets for all the main tonearm parameters. I aimed to have the carriages resonant frequency above 20khz in both the vertical and lateral planes. I achieved 19.4khz in the vertical plane and 27.7khz in the lateral. Pretty close. As my hearing limit is about 16.5khz both are above my personal audible bandwidth.
I aimed for a vertical cantilever resonance of 9.5hz and achieved 9.45hz. For lateral I aimed for 4.5hz and achieved 4.58hz.
I aimed for a maximum tracking force variation for a 0.3mm warp (as much as I get with my clamp) of 2%. I achieved 0.71%.
I aimed for maximum peek warp wow of 0.1%, below the threshold for human hearing, on an average record. I achieved 0.077%. This figure is based on the measurements I made when designing the record clamping system. The clamp I ended up making performed much better than the test clamp so the actual warp wow figure will be significantly lower than this.
I designed the carriage from the start to use pin bearings. However due to my inability at the time to accurately manufacture them and a poor choice of materials I could not get them to work adequately. So, having discovered this thread, adapted the carriage to use ball race bearings running on dual glass rods. The adaptation didn't require any modifications to the actual carriage. I just ran a long threaded bar between the two bearing mounts. This did make for a very solid bearing attachment. Having got the arm working I could then move on to build the rest of the deck.
I was however never fully satisfied with the performance of the balls race bearings. Even though I had no obvious tracking issues I could tell that lateral friction was higher than desirable and the spectre of bearing chatter hunted me. I tried several approaches to reduce friction before returning to pin bearings.
The first attempt was to partially levitate the carriage using magnets. This can be done in two ways, both of which I investigated. First I played with magnetic repulsion. This requires a continuous line of small magnets along the rail and a couple of magnets on the carriage. This approach has two problems. I'm really not happy having that much magnetism that close to the cartridge, even a moving magnet model. Upgrading to a moving coil would be out of the question. The magnetic field wants to constantly slide the carriage off the front or back of the rail making it unstable.
Then I played with magnetic attraction. This used only a couple of very small attached to the carriage and a ferrous strip parallel to the rail. I did achieve an 80% reduction in lateral bearings friction. However this acted as a magnetic damper which massively overdamped the system causing more problems than it solved.
So magnetic levitation was filed under fail.
An obvious method of reducing bearing friction is to reduce carriage mass. Most of the carriages built by the contributers to this thread have a mass, including cartridge and counterweight, of about half that of mine. It was also quite possible that my entire design philosophy was flawed and the style of carriage developed by Colin and others was superior. I'm not too proud as to admit that I may be wrong. So I built a lightweight carriage. I again aimed to keep all the arm parameters in check. My main design constraint was that it had to fit my existing arm base rail system though this did not end up compromising the final design. My design differed from Colin's in having the arm tube running above the rail rather than below it, similar to the clearaudio TT1. This layout will have significantly lower warp wow and tracking force variations. The bearing yoke will also be more rigid. As with Colin's design I used a solid block headshell and underslung counterweight. One minor change is that the bearing yoke is in front of the rail rather than behind it. This allowed me to maximize armtube rigidity and helped to get the desired vertical effective mass. I'm not suggesting that placing the yoke in front of the rail is universally better. In most designs behind the rail is probably better, in the analysis of my design in front happened to be best. The total mass of this carriage, including cartridge and counterweight, is 27.95g, almost exactly half the mass of my other carriage. This would mean that lateral friction would also be halved when using the same bearings. The resonant frequency of the lightweight arm is approximately 5khz. Here are some photos of the lightweight carriage.
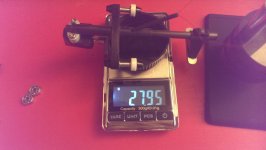
Hi all,
All of the work that I have undertaken developing my new bearings has resulted in a significant sonic improvement. This improvement pales in comparison to the difference in sound quality that can be achieved with a properly sorted carriage design. I have described the goals of this design before in this thread but will expand my design philosophy further here.
The main cause of colourations in a conventional tonearm are the bending modes in the arm tube that occur at and above the resonant frequency of the arm. Below the arms resonant frequency the arm tube acts as a rigid beam controlled by the effective mass of the arm. Above the resonant frequency the arm tube is constantly flexing and is controlled by the rigidity and damping of the arm tube. Most tonearms have their resonant frequency right in the middle of the midrange, the worst possible place. Damping is then applied to try and control this. Damping helps but the arm is still not rigid over most of the audio bandwidth and therefore the cartridge is not properly controlled. At higher frequencies less energy is transmitted from the stylus/groove interface to the arm plus, as a bonus higher frequencies are easier to damp. The higher the resonant frequency the better.
My approach to solving this problem and eliminating colouration was to design an arm whose resonant frequency was outside of the audio bandwidth, above 20khz. This would mean that the arm acts as a rigid beam across the entire audio bandwidth. If there are no bending modes there are no colourations. Also virtually no damping would be required. To achieve this the arm has to be incredibly rigid. The best way of increasing rigidity is to make the arm very short. Making an arm very short dictates that it has to be a linear trackers.
Resonant frequency is not just dependent upon rigidity but also on mass and how that mass is distributed.
Making the arm short also makes it lighter .In addition to making the arm short making it short and broad will increase rigidity. However, making the arm broader will increase its mass. Tapering the arm, making it thinner at the ends and thicker in the middle, removes mass from the ends and places more material in the centre where the bending forces would be at their highest. This improves mass distribution and maximizes rigidity pushing the resonant frequency higher still.
The choice of materials used also has a great impact. Ideally you want a material that is both very stiff and lightweight. Carbon fibre composite is an ideal material in this aspect having a very high stiffness to density ratio. This ratio can be enhanced further by, instead of using solid sections, using thin skins of composite over a lightweight core. End grain balsa wood, where the grain is perpendicular to the skins, is the best material for this application. Carbon fibre/balsa composite panels have the added benefit that they have excellent self damping characteristics. The carbon fibre composite sheet that I used for this arm is not just a standard piece. I had the sheet especially made with the fibres in each lamina specifically aligned to maximize its properties.
In my design the carriage has carbon composite structural members that pass both above and below the rail. This has the advantages of not only maximizing rigidity but also makes it impossible to accidentally derail the carriage.
Rather than having a conventional headshell that protrudes from the front of the arm the cartridge sits in a recess within the carriages body. Buttresses, that connect the upper and lower panels of the arm, surround the cartridge. In order to keep the recess as small as possible, just big enough to take the cartridge, the cartridge tags have been cut down so they take up as little space as possible. The counterweight and its adjuster sit in similar recesses in the rear of the carriage, keeping the rear end as solid as possible.
Longitudinal bending waves are not the only mechanism by which vibrational energy is transmitted through the carriage though they are by far the most significant. Similar to longitudinal bending there are also torsional modes. These twist the carriage along its length. Luckily tonearms have inherently high torsional rigidity and a torsional resonant frequency above the audio bandwidth. My carriage has a torsional resonant frequency of at least 70khz, probably more than 100khz.
A mechanism of greater significance is compression waves also known as sound waves. These propagate from their source, mainly the cartridge, through the carriage at the speed of sound for the material the carriage is made of. When these waves hit a boundary or interface they reflect back. The amount that is reflected is dependent upon the impedance of the boundary. A low impedance boundary, such as between the arm and the air, will reflect a small proportion of the initial wave. A high impedance boundary, such as between the arm and a bearing yoke or counterweight, will reflect strongly.
A sound wave/impulse originating at the cartridge travels through the carriage at the speed of sound, reflects at a boundary then travels back to the cartridge. The difference in arrival time from the original sound wave/impulse to the arrival of the reflection creates a time smear. This has the effect of softening transients, masking low level detail and blurring imaging.
There are many methods of reducing this effect. The best method is to insure that the reflection arrives as soon after the initial signal as possible, ideally within a wavelength. This would mean that the distance from the cartridge to the reflection boundary is a half wavelength of the highest frequency. Two methods of achieving this exist. Make the arm from a material that has a very high speed of sound (beryllium would be lovely here with a speed of sound of 12km/s). The other is to minimize the distance from the cartridge to the reflection boundary or more simply put, make the arm short. Of course combining both of these approaches is better still. The speed of sound through carbon fibre composite is about 3.5km/s. My carriage is about 100mm long in total. A 200mm wavelength at 3.5km/s equates to a frequency of 17.5khz
Another method is to make the arm irregular with lots of low impedance boundaries that act to scatter the sound wave. More by luck than design my carriage fits this description very well.
Attenuating the sound wave as it passes through the arm will mean that there is less energy reflected back. Alternating layers of material with a high speed of sound with ones with a lower speed of sound can be effective at minimizing sound wave propagation. End grain balsa laminated with carbon fibre composite sheets is particularly good in this respect and is often used in high tech acoustic panels for this reason.
Lowering the impedance at the reflection boundary will reduce the amount of energy returning to the cartridge. This is why many tonearm designs have decoupled counterweights, to reduce the strength of the reflection. Decoupling, especially using compliant materials, can have additional benefits or create other problems and its success will be largely design dependent. Alternatively using a smaller counterweight will reduce reflection. This is undesirable with longer arms where a heavy counterweight close to the pivot is generally preferred. A short arm only requires a small counterweight anyway.
I did not just blindly chase high rigidity and high resonant frequency. The design of the carriage was carried out using a spread sheet that calculated the arms resonant frequency in both vertical and lateral planes. It also calculated effective mass, vertical and lateral (lateral is just total carriage mass), tracking force and tracking force variation due to warps and the level of warp wow. This spread sheet is like a simplified finite element analysis program set up specifically for this application. The techniques used in creating this spread sheet were developed whilst researching my dissertation whilst I was at university studying composite engineering. I had great fortune in being able to wangle having vibration analysis of composite structures as my dissertation subject. The university material lab had lots of lovely test equipment that allowed me to verify that my mathematical models were accurate. I wonder how many manufactures actually carry out vibration analysis on their designs rather than using trial and error.
An unusual feature of this design is that the carriage runs very close to the record surface with only a 2.5mm clearance. This is so that the vertical pivot can be kept as low as possible to minimize warp wow and so that the centre of mass can be on the same plane as the vertical pivot in order to minimize tracking force variation due to warps. The rear of the arm slopes upwards slightly to prevent the rear of the carriage from fouling the record whilst queuing. When queuing the stylus is lifted only 3mm from the record. This may seem alarmingly close but as the carriage sits securely on the rail this has never been an issue. Of course decent record clamping helps here.
When designing this arm I designed specifically to match an ortofon 2m black cartridge, which is the cartridge I am currently using.
When I initially started the design process I set targets for all the main tonearm parameters. I aimed to have the carriages resonant frequency above 20khz in both the vertical and lateral planes. I achieved 19.4khz in the vertical plane and 27.7khz in the lateral. Pretty close. As my hearing limit is about 16.5khz both are above my personal audible bandwidth.
I aimed for a vertical cantilever resonance of 9.5hz and achieved 9.45hz. For lateral I aimed for 4.5hz and achieved 4.58hz.
I aimed for a maximum tracking force variation for a 0.3mm warp (as much as I get with my clamp) of 2%. I achieved 0.71%.
I aimed for maximum peek warp wow of 0.1%, below the threshold for human hearing, on an average record. I achieved 0.077%. This figure is based on the measurements I made when designing the record clamping system. The clamp I ended up making performed much better than the test clamp so the actual warp wow figure will be significantly lower than this.
I designed the carriage from the start to use pin bearings. However due to my inability at the time to accurately manufacture them and a poor choice of materials I could not get them to work adequately. So, having discovered this thread, adapted the carriage to use ball race bearings running on dual glass rods. The adaptation didn't require any modifications to the actual carriage. I just ran a long threaded bar between the two bearing mounts. This did make for a very solid bearing attachment. Having got the arm working I could then move on to build the rest of the deck.
I was however never fully satisfied with the performance of the balls race bearings. Even though I had no obvious tracking issues I could tell that lateral friction was higher than desirable and the spectre of bearing chatter hunted me. I tried several approaches to reduce friction before returning to pin bearings.
The first attempt was to partially levitate the carriage using magnets. This can be done in two ways, both of which I investigated. First I played with magnetic repulsion. This requires a continuous line of small magnets along the rail and a couple of magnets on the carriage. This approach has two problems. I'm really not happy having that much magnetism that close to the cartridge, even a moving magnet model. Upgrading to a moving coil would be out of the question. The magnetic field wants to constantly slide the carriage off the front or back of the rail making it unstable.
Then I played with magnetic attraction. This used only a couple of very small attached to the carriage and a ferrous strip parallel to the rail. I did achieve an 80% reduction in lateral bearings friction. However this acted as a magnetic damper which massively overdamped the system causing more problems than it solved.
So magnetic levitation was filed under fail.
An obvious method of reducing bearing friction is to reduce carriage mass. Most of the carriages built by the contributers to this thread have a mass, including cartridge and counterweight, of about half that of mine. It was also quite possible that my entire design philosophy was flawed and the style of carriage developed by Colin and others was superior. I'm not too proud as to admit that I may be wrong. So I built a lightweight carriage. I again aimed to keep all the arm parameters in check. My main design constraint was that it had to fit my existing arm base rail system though this did not end up compromising the final design. My design differed from Colin's in having the arm tube running above the rail rather than below it, similar to the clearaudio TT1. This layout will have significantly lower warp wow and tracking force variations. The bearing yoke will also be more rigid. As with Colin's design I used a solid block headshell and underslung counterweight. One minor change is that the bearing yoke is in front of the rail rather than behind it. This allowed me to maximize armtube rigidity and helped to get the desired vertical effective mass. I'm not suggesting that placing the yoke in front of the rail is universally better. In most designs behind the rail is probably better, in the analysis of my design in front happened to be best. The total mass of this carriage, including cartridge and counterweight, is 27.95g, almost exactly half the mass of my other carriage. This would mean that lateral friction would also be halved when using the same bearings. The resonant frequency of the lightweight arm is approximately 5khz. Here are some photos of the lightweight carriage.
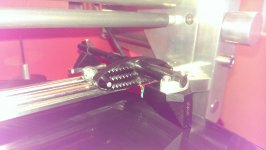
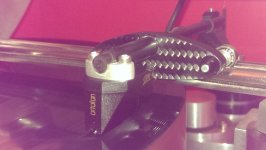
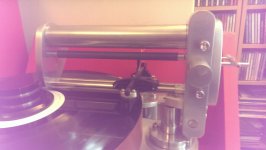
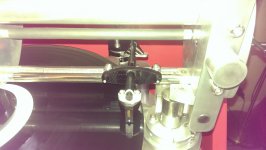
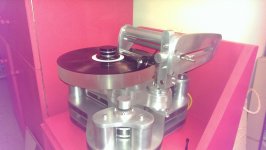
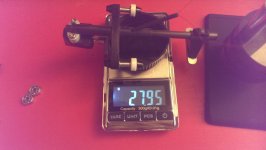
Continued
One negative aspect of this carriage is that it has no mechanism to prevent accidentally derailing.
The reduction in lateral friction was visibly apparent. With the heavier carriage there was a noticeable wobble visible on long run out grooves. This may have been due to variations in friction as the bearings rotated. With the lightweight carriage no wobble was visible. I kept this carriage on the deck for a couple of months. During this time I experimented to squeeze the best possible sound from it. I tried both the Boca hybrid and the full zirconium ceramic bearings. There was much less difference between the two types of bearings than there had been using the heavier carriage but the hybrids still had the edge. I also experimented with arm damping. The best results were with a tight fitting balsa wood dowell running inside the arm tube for its full length.
If I had built this carriage first I would have been pleased with the result. I think it would give any sub £1000 arm a good run for its money. I'm glad I didn't as I might not have built THE carriage.
The real ear opener happened when I swapped back to the original carriage. This was with the hybrid ball race bearings, I hadn't started investigating pin bearings at this point. I had expected that the lower friction of the lightweight carriage would yield better sound quality in some areas but not be as good in others. One of the aspects of sound quality that I have always found to be particularly sensitive to lateral tracking error is soundstage and the sense of space. I had expected at least this aspect to be better.
The original carriage was superior at absolutely everything. Better stereo imaging in space, focus, scale, separation etc. Bass, deeper, more solid, detailed, articulated etc. And most by a significant degree.
The one aspect that really stood out for me was the Smoothness and seamlessness of the sound. You don't realize most arms sound slightly disjointed until you hear one that isn't. I believe that this is due to the fact that the entire audio bandwidth is dealt with in the same way, below the arms resonant frequency.
The lightweight carriage experiment confirmed that resonance control is the most important aspect of tonearm design.
The road to turntable nirvana has been a long one but I now feel that I'm at least knocking on the door if not actually stepping over the threshold.
Niffy
One negative aspect of this carriage is that it has no mechanism to prevent accidentally derailing.
The reduction in lateral friction was visibly apparent. With the heavier carriage there was a noticeable wobble visible on long run out grooves. This may have been due to variations in friction as the bearings rotated. With the lightweight carriage no wobble was visible. I kept this carriage on the deck for a couple of months. During this time I experimented to squeeze the best possible sound from it. I tried both the Boca hybrid and the full zirconium ceramic bearings. There was much less difference between the two types of bearings than there had been using the heavier carriage but the hybrids still had the edge. I also experimented with arm damping. The best results were with a tight fitting balsa wood dowell running inside the arm tube for its full length.
If I had built this carriage first I would have been pleased with the result. I think it would give any sub £1000 arm a good run for its money. I'm glad I didn't as I might not have built THE carriage.
The real ear opener happened when I swapped back to the original carriage. This was with the hybrid ball race bearings, I hadn't started investigating pin bearings at this point. I had expected that the lower friction of the lightweight carriage would yield better sound quality in some areas but not be as good in others. One of the aspects of sound quality that I have always found to be particularly sensitive to lateral tracking error is soundstage and the sense of space. I had expected at least this aspect to be better.
The original carriage was superior at absolutely everything. Better stereo imaging in space, focus, scale, separation etc. Bass, deeper, more solid, detailed, articulated etc. And most by a significant degree.
The one aspect that really stood out for me was the Smoothness and seamlessness of the sound. You don't realize most arms sound slightly disjointed until you hear one that isn't. I believe that this is due to the fact that the entire audio bandwidth is dealt with in the same way, below the arms resonant frequency.
The lightweight carriage experiment confirmed that resonance control is the most important aspect of tonearm design.
The road to turntable nirvana has been a long one but I now feel that I'm at least knocking on the door if not actually stepping over the threshold.
Niffy
Your post are very informative niffy. Thanks a lot for sharing. I guess little resistance may be good as it may serve as biasing. Isn't it ? Needs to be tested by test record.
Regards.
Unfortunately any "biasing" effect of bearing friction acts in the opposite direction that the arm needs to move. Any biasing would need be applied in the same direction as arm movement. Hence the desire for minimum friction where the need for bias is removed.
Niffy
Hi Hiten,
I'm not sure I fully understand your question.
Could you explain which contact points you mean when you say tracks contact points. Relative to the carriage all the contact points in the bearings don't move. The only point of contact that does move relative to the carriage is the stylus/record contact. This is the movement that we are trying to minimize by reducing bearing friction.
Do you mean the weight distribution in the carriage? If so, weight distribution will have no effect on lateral friction. The entire carriage weight is evenly split between the two wheels, minus the small amount supported by the stylus. If weight is concentrated at the ends of the carriage or in the middle makes no difference. If the total weight is the same the load on the bearings will be the same and therefore the bearing friction will be the same.
Hopefully I've answered the questions you were actually asking. If not rephrase them and we'll have another go.
Niffy
I'm not sure I fully understand your question.
Could you explain which contact points you mean when you say tracks contact points. Relative to the carriage all the contact points in the bearings don't move. The only point of contact that does move relative to the carriage is the stylus/record contact. This is the movement that we are trying to minimize by reducing bearing friction.
Do you mean the weight distribution in the carriage? If so, weight distribution will have no effect on lateral friction. The entire carriage weight is evenly split between the two wheels, minus the small amount supported by the stylus. If weight is concentrated at the ends of the carriage or in the middle makes no difference. If the total weight is the same the load on the bearings will be the same and therefore the bearing friction will be the same.
Hopefully I've answered the questions you were actually asking. If not rephrase them and we'll have another go.
Niffy
Also wanted to know are there any software that simulates center of gravity of objects ?
Regards.
Some CAD programs will automatically find centres of mass.
I would use a spread sheet to calculate them. I'd get it to calculate tracking force and vertical effective mass at the same time so that I could see how any changes to one effected the others.
Niffy
... I also experimented with arm damping. The best results were with a tight fitting balsa wood dowell running inside the arm tube for its full length.
Niffy
Niffy,
I've used a balsa wood dowell in my own diy arm for damping and found it effective in reducing a 'ring' to a 'thud' in the arm tube when I tap it with a pencil. I don't have the training to analyze/calculate these vibration modes mathematically, nor do I have access to equipment as would be found in a university lab. Can you offer any advice on ways or methods that the average diy'er might be able to use to test for vibration modes and resonant frequencies in arms that we've already built? I have an assortment of test records, but I can never be sure how to separate what's attributable to the cartridge/stylus from what's attributable to arm structure vibration. I like that you've found a correlation between your theoretical calculations, actual measurements, and what you hear.
Any ideas that could help us tinker more effectively would be most appreciated.
Ray K
Hi Ray.
It would be theoretically possible to reverse engineer an existing arm into a mathematical model. A lot of information about the materials used would be required. It is not a task I would relish and the chances of something missed throwing the whole calculation out is quite large. Even if you know all measurements and have spare bits of material to test the task would be daunting.
I have never actually measured the resonant frequency of my carriage. I built it long after I had the resources of the university labs. I did compare my mathematical modeling method against physical test results. My model tended to overestimate the actual resonant frequency by about 2%. (which is pretty darn close). The figures for resonant frequency that I have quoted in this thread are actually 20% lower than the calculated figures. This is to account for this 2% overshoot and any other unseen factors. I would always prefer under-quoted specifications to over-quoted .
A couple of years ago Jim (super) posted some oscilloscope plots of one of his arms. I think it was his first air bearing arm. The interesting plot was one of a square wave test track. You could see a slight ringing after each transient. From this I estimated that he had an arm resonance of 6khz. Hat's off to Jim, it was the cleanest result I have seen of this test. Of course this test will show the resonances of the whole system and not just the arm.
It may be possible to measure just the carriage by hanging it my a fine thread, placing a microphone close to it and tapping it. This would have to be done with cartridge and counterweight fitted. If the microphone was connected to a recording oscilloscope you may be able to determine the resonant frequency.
Niffy
It would be theoretically possible to reverse engineer an existing arm into a mathematical model. A lot of information about the materials used would be required. It is not a task I would relish and the chances of something missed throwing the whole calculation out is quite large. Even if you know all measurements and have spare bits of material to test the task would be daunting.
I have never actually measured the resonant frequency of my carriage. I built it long after I had the resources of the university labs. I did compare my mathematical modeling method against physical test results. My model tended to overestimate the actual resonant frequency by about 2%. (which is pretty darn close). The figures for resonant frequency that I have quoted in this thread are actually 20% lower than the calculated figures. This is to account for this 2% overshoot and any other unseen factors. I would always prefer under-quoted specifications to over-quoted .
A couple of years ago Jim (super) posted some oscilloscope plots of one of his arms. I think it was his first air bearing arm. The interesting plot was one of a square wave test track. You could see a slight ringing after each transient. From this I estimated that he had an arm resonance of 6khz. Hat's off to Jim, it was the cleanest result I have seen of this test. Of course this test will show the resonances of the whole system and not just the arm.
It may be possible to measure just the carriage by hanging it my a fine thread, placing a microphone close to it and tapping it. This would have to be done with cartridge and counterweight fitted. If the microphone was connected to a recording oscilloscope you may be able to determine the resonant frequency.
Niffy
Niffy,
thanks for patiently answering my queries
.
What I want to know is suppose there is a perfectly centered record and concentric grooves forces the carriage to move towards the lable. We have (1) friction (of pin bearing and wheels rolling on tracks) and (2) mass (Carriage); shouldn't this mass, even by a small amount resist this move towards the lable and work as biasing.
Regards.
thanks for patiently answering my queries
What I want to know is suppose there is a perfectly centered record and concentric grooves forces the carriage to move towards the lable. We have (1) friction (of pin bearing and wheels rolling on tracks) and (2) mass (Carriage); shouldn't this mass, even by a small amount resist this move towards the lable and work as biasing.
Regards.
Niffy,
thanks for patiently answering my queries.
What I want to know is suppose there is a perfectly centered record and concentric grooves forces the carriage to move towards the lable. We have (1) friction (of pin bearing and wheels rolling on tracks) and (2) mass (Carriage); shouldn't this mass, even by a small amount resist this move towards the lable and work as biasing.
Regards.
Hi Hiten,
When playing a record that is not concentric the mass of the carriage has two effects.
1/ It loads the bearings which leads to bearing friction.
2/ Is the mass inertia of the carriage. (I discussed this is post 2135) A certain amount of force is required to accelerate the carriage back and forth.
As the level of eccentricity reduces the mass inertia effect reduces until, with a perfectly concentric record, it effectively becomes zero. The carriage now moves at a constant speed from right to left. (ignoring the fact that most records are recorded with variable pitch. This variation is way too small to be of concern). With a perfectly concentric record the only effect of mass on tracking error is due to bearing loading. The mass of the arm will have no biasing effect.
In post 2172 I mentioned that a purely passive bias system is possible.
The first part of this system requires that the record be perfectly concentric. This would mean that every record in your collection would have to be measured to find both the amplitude of the eccentricity and its direction. The record clamping system would have a mechanism that aligns with the direction of eccentricity then adjusts to cancel its amplitude. I did say it would make changing records a phaf.
By far the biggest advantages of making your records concentric are that the wow and lateral tracking errors caused by eccentricity are eliminated. The ability to now bias to counter bearing friction would be a minor additional benefit.
The important thing about a perfectly concentric record is that the carriage only moves from right to left. As it never moves to the right the level of bearing friction moving to the right becomes irrelevant. A biasing system can now be applied to the carriage that only acts to the left. This is set to be at the same magnitude as bearing friction. These would cancel resulting in zero friction and thus zero tracking error.
The easiest way of applying this bias is by slightly sloping the rail down towards the centre of the record. The mass of the carriage now has an additional effect in that it makes the carriage want to roll towards the centre. The angle of the slope being set so that amount the carriage wants to roll is exactly equal to the bearing friction resisting it.
Hang on I hear you say, "won't that effect VTA as the carriage moves across the record?". Here's the clever bit. You slope the surface of the platter by exactly the same amount. This would mean that the surface of the platter had a slight conical dish. When the record was clamped in would be pressed into this dish making its surface parallel to the rail. A slightly dished platter has the added benefit of helping to reduce warps when the record is clamped.
The angle of slope will be dependent on carriage mass and bearing friction. As the carriage is in constant motion rather than stop/start motion the level of friction actually decreases. Dynamic(moving) friction is lower than static friction. With my arm the required slope of the rail would be less than a tenth of a degree. That's a drop of less than 0.2mm across a record. it hardly seems worth it.
This type of biasing system is possible. It requires modification of the platter and the work required to change records increases. The benefits of reducing wow and tracking error by centering the record would be the main improvement.
Niffy
Thanks for informative post. I think I ignored the bearing loading effect on movement of carriage. Which is very important. A record clamp with slight slope induced is a new perspective for me. Thanks for sharing. I guess for the same effect instead of conical slope in record one can tilt the turntable slightly.
Regards.
Regards.
Thanks for informative post. I think I ignored the bearing loading effect on movement of carriage. Which is very important. A record clamp with slight slope induced is a new perspective for me. Thanks for sharing. I guess for the same effect instead of conical slope in record one can tilt the turntable slightly.
Regards.
Sloping the deck would have one big advantage (assuming that tilting it wouldn't upset it in some way). Having to centre the record each time it is played could become a drag, for intensive listening sessions ok but for general music not so. Unslope the deck and just use the clamp set to zero correction and its a normal record player.
I have been toying with the idea of the centreing clamp for a while though I might not add the biasing refinement. I haven't made one for two reasons even though I've pretty much designed it.
1/ it would have to be very accurate and repeatable and have to take into consideration hole size as well as eccentricity. It is beyond my capabilities to make so I'd have to outsource.
2/ I would need to make the initial measuring apparatus. This would probably look a lot like another record player and would ideally be set up permanently so new vinyl purchases could be immediately measured and played. My wife would KILL me if I had two record players, even if one wasn't a record player.
Niffy
Hi Stefano,
I've googled your cartridge collection. Those are some serious transducers. I've unfortunately not heard any of them, I doubt many have. I had read a lot of reviews. The zyx range always get very favourable reviews from reviewers who favour accuracy and neutrality and is a brand I would like to sample. I am a bit of a Ortofonophile and the candenza black and windfeld currently sit close to the top of my dream list. The top slot taken by the A95. I've jotted down the relevant information for your cartridges and will plug the data into my analysis spread sheet in the near future. It's a pity manufactures don't give the location of the cartridges centre of mass, I'll have to estimate it. Unfortunately my computer is in a different room to my deck and I'm having way too much fun spinning the black stuff at the moment.
Niffy
I've googled your cartridge collection. Those are some serious transducers. I've unfortunately not heard any of them, I doubt many have. I had read a lot of reviews. The zyx range always get very favourable reviews from reviewers who favour accuracy and neutrality and is a brand I would like to sample. I am a bit of a Ortofonophile and the candenza black and windfeld currently sit close to the top of my dream list. The top slot taken by the A95. I've jotted down the relevant information for your cartridges and will plug the data into my analysis spread sheet in the near future. It's a pity manufactures don't give the location of the cartridges centre of mass, I'll have to estimate it. Unfortunately my computer is in a different room to my deck and I'm having way too much fun spinning the black stuff at the moment.
Niffy
Nakamichi
The Nakamichi TX-1000 you referred to always seems over-engineered to me. Its smaller sibling the Dragon appears to be simpler and more elegant in its solution. Not having to deal with the motor and bearing like the TX-1000, the Dragon merely slides the glass top plate to adjust centering after its detecting system. It also decouples the spindle from the bearing shaft, which is a nice touch to me, as it isolates the noise transmitted from the bearing to the record touching the spindle. (Why high-end manufacturers continue to machine the record spindle with the bearing shaft as one piece is baffling to me!) According to TVK, some user prefer the sound of Dragon over the more expensive sibling. No surprise to me...
I wish someone can come up with an aftermarket system as an accessory that allows electronic centering without forcing the user to buy their turntable. Here is a YouTube video that demonstrating how the Dragon works.
Sorry, a little off topic from tonearm design. Back to your regular programming, please!
Would that be some kind of turntable like Nakamichi?
The Nakamichi TX-1000 you referred to always seems over-engineered to me. Its smaller sibling the Dragon appears to be simpler and more elegant in its solution. Not having to deal with the motor and bearing like the TX-1000, the Dragon merely slides the glass top plate to adjust centering after its detecting system. It also decouples the spindle from the bearing shaft, which is a nice touch to me, as it isolates the noise transmitted from the bearing to the record touching the spindle. (Why high-end manufacturers continue to machine the record spindle with the bearing shaft as one piece is baffling to me!) According to TVK, some user prefer the sound of Dragon over the more expensive sibling. No surprise to me...
I wish someone can come up with an aftermarket system as an accessory that allows electronic centering without forcing the user to buy their turntable. Here is a YouTube video that demonstrating how the Dragon works.
Sorry, a little off topic from tonearm design. Back to your regular programming, please!
Niffy
that would be an interesting apparatus of measuring records.
Would that be some kind of turntable like Nakamichi ? I have a magazine which has detailed explanation of Nakamichi self centering turntable. I can scan and post.
Regards.
Hi Hiten.
That would be an interesting article. An easy method of centering a record that didn't impact the sonic character (or lack thereof) of the deck would be worth pursuing.
The discussion of clamping and record centering may seem to be off topic but I don't believe it is. In many respects the record clamping system is more a part of the arm than it is the deck. The traditional method of dealing with warps and eccentricity is to let the arm deal with them. There are two main problems with this approach.
1/ The arm isn't very good at these tasks. With warps arm design can do little to alleviate VTA error, the majority of this error is due to the slope of the record surface. By eliminating warps VTA error, warp wow and warp induced tracking force variation are also eliminated. The arm can do nothing to reduce the LTA error and wow caused by eccentricity. A well centred record doesn't have these problems.
2/ The design of the arm is compromised by trying to solve these problems. To minimize warp wow and tracking force variation the vertical pivot is aligned with the record surface. This puts a constraint on the arm design, the arm has to be at least long enough to clear the edge of the record.
The effective masses of the arm have to be kept low. With no warps or eccentricity the masses can be higher which will improve the arms control of the cartridge.
This is not an exhaustive list but a sample of the major problems.
Removing warps and eccentricity frees up the arms design.
Niffy
Thanks directdriver,
Nakamichi system is surprisingly similar to the system that I came up with. Both systems use a separate arm and the run out groove to measure the amplitude and direction of the eccentricity.
The major differences are that in my system the measurement system is separate from the main deck so its implementation cannot effect the operation or sonic character of the deck.
Rather than moving the entire top section of the platter, which creates a balance problem to solve, my system only moves the spindle, which in my design is now part of the clamp. By only moving 5-10g rather than a kilogram balance is no longer a problem.
The Nakamichi system in the video took ages to align the record. In my system each side of each record is measured only once. The direction of the eccentricity is marked on the record label with a small adhesive dot. And the amplitude written on a label attached to the records protective sleeve. The clamp is set to the correct amplitude correction, aligned with the mark on the label and tightened. This would take much less time when changing records but longer whilst taking the initial measurement.
I think my system would be much simpler, much less likely to negatively effect the deck and quicker. The main down side to my design is that the measurement system is similar in appearance to a record player and would take up valuable shelf space in the listening room. One of these days I'll have to build it.
Niffy
Nakamichi system is surprisingly similar to the system that I came up with. Both systems use a separate arm and the run out groove to measure the amplitude and direction of the eccentricity.
The major differences are that in my system the measurement system is separate from the main deck so its implementation cannot effect the operation or sonic character of the deck.
Rather than moving the entire top section of the platter, which creates a balance problem to solve, my system only moves the spindle, which in my design is now part of the clamp. By only moving 5-10g rather than a kilogram balance is no longer a problem.
The Nakamichi system in the video took ages to align the record. In my system each side of each record is measured only once. The direction of the eccentricity is marked on the record label with a small adhesive dot. And the amplitude written on a label attached to the records protective sleeve. The clamp is set to the correct amplitude correction, aligned with the mark on the label and tightened. This would take much less time when changing records but longer whilst taking the initial measurement.
I think my system would be much simpler, much less likely to negatively effect the deck and quicker. The main down side to my design is that the measurement system is similar in appearance to a record player and would take up valuable shelf space in the listening room. One of these days I'll have to build it.
Niffy
- Home
- Source & Line
- Analogue Source
- DIY linear tonearm