Stamp of individuality would be last thing on my mind and honestly don't want to complicate things. Sorry if it came across that way. I was just sharing my thoughts but I see you have experimented comprehensively.Heating the oil facilitates it flowing into the tiny pores in the sintered bronze (oilite), but a vacuum pump would not hurt if you had one. I'm not sure cold oil would flow into the tiny pores of the bushing even with a vacuum pump if the oil were not warm, and you need to cool the bushings so that the coil stays in place. Seem like additional complication, it won't hurt, but I am not sure it really helps either.
I doubt it would work at all for removing the old oil given that the old oil is a sludgy gell with little or no entrapped air mixed in.
I wonder what this constant desire is to complicate a simple and proven process - no special equipment is required and the results are excellent. We all want to put our stamp of individuality on the things we do, but sometimes the best trail has already been blazed and experience tells me this is probably the case here.![]()
There are some solvent which I guess would be inert to react. Not sure. Though a chemistry graduate I don't have any idea as I am no longer in touch with that subject, but of alcohol reacting with bronze needs to be explored. I remember in college before starting experiments all glass equipments were used to be rinsed with a some solvent so any impurities would not interfere with intended experiment.
Would a dried oil when heated leave any residue ? This also needs to be looked at. Or one can put bush in a appropriate solvent and see if bush can be cleaned with ultrasonic sound. If it cleans, one can immediately put the bush in to use and let the oil work its way while TT is running. And with sufficient time re-lubricate the felt and bush again. Don't know if Companies while assembling motors oil the bush and assemble them or do the other way around.
Regards.
I serviced a Garrard 301 that had run continuously since 1964 at what was PYE records, later Telstar. Someone had said never switch it off and that's what happened. I stopped it for 30 minutes to crack the motor. After refilling the bearings it was back in use. The thing to note was no obvious bearing play. The BBC never switched them off. For the 20 watts they might use it is a small price to pay. Bearing wear was not obvious in the main bearing also. 20 VA is a typical reading.
I serviced a Garrard 301 that had run continuously since 1964 at what was PYE records, later Telstar. Someone had said never switch it off and that's what happened. I stopped it for 30 minutes to crack the motor. After refilling the bearings it was back in use. The thing to note was no obvious bearing play. The BBC never switched them off. For the 20 watts they might use it is a small price to pay. Bearing wear was not obvious in the main bearing also. 20 VA is a typical reading.
Thanks for that interesting ancecdote Nigel. I think it might be tempting to read certain things into it. Given this thread has spent some considerable bandwidth discussing the start-up behavior of the TD124 and its E50 powered drive train, there might be some inclination for those among us to suggest that the Garrard motor may take some time to get fully speed stable.
But there aren't many discussion on the subject of 301 warm up times around the web, so I suppose that the Garrard does not exhibit the same tendencies as the TD124 in regard to cold-starting.
Certainly, it would make sense that the BBC or any radio station would want to ensure that their turntables were speed stable before airing any of their playback. Probably that is what I read into the above anecdote.
The other part about not seeing any significant wear is another useful point that those among us Td124 users may consider with regard to motor bushings and whether or not to replace.
I try to take a mechanic's pragmatic approach; without evidence to suggest bushing wear, I'd see to real reason to replace the original bushings.
Lastly I think it might be interesting to discuss the cold starting behavior of a well sorted 301.
-Steve
301's can take 10 minutes. 2 minutes seems very good. As my old boss Terry O'Sullivan says " Just about enough time to make a cup of tea ". Do not confuse synchronous used by many belt drives. These usually have instant speed ability given the belt can grip enough. I suspect this aspect of them is not ideal. A diesil engine when you want a jet or at least a petrol V12. 301 and TD124 motors are nearly identical. 2 minutes on a 301 usually takes it to -0.1% of it's final speed if on a fixed frequency and voltage PSU.
I just wanted to add a little to what I've said about my desire to add a vacuum system to the process of re-infusing E50 bearings (or any of the other sintered bronze bearings for that matter).
Everything I've been able to find related to the subject suggests a vacuum process is what was used commercially, and in fact is still what's used for stock Oilite. One could posit a number of reasons why it would be done that way, including the possibility that it simply speeds up the process.
But I can't help but wonder if it also assures all of the air is driven out of the part. We might think that it's all removed through the heated oil bath process alone, but simply observing that no more air is coming out is no guarantee of it. Perhaps there is air farther in, or in such small capillaries it simply refuses to budge. Perhaps on one part, the heated oil bath does all we think it does, but on another part it doesn't.
Does getting every little micro-bubble of air out matter? I suppose that's debatable. Personally though, critical as these parts are, I'd rather not have to worry about it. If one is simply adding lubrication to a bushing that's in service, perhaps it's not that important, but in those cases where one has gone to great pains to remove all old oil and contamination from a bushing (thereby filling it with air) it may matter quite a bit.
To that end, trying to duplicate the process that is used commercially, to the extent possible, doesn't strike me as making things unnecessarily complicated, more providing additional assurance that the job really gets done.
What I plan to do is to try and set up a system that allows me to first use the standard soak in hot oil bath to remove as much air as possible, then seal the jar and turn on the vacuum. If after having done that with several bushings the vacuum does not remove any additional air, then I'd say it's only worth the time if it actually ends up saving time.
Everything I've been able to find related to the subject suggests a vacuum process is what was used commercially, and in fact is still what's used for stock Oilite. One could posit a number of reasons why it would be done that way, including the possibility that it simply speeds up the process.
But I can't help but wonder if it also assures all of the air is driven out of the part. We might think that it's all removed through the heated oil bath process alone, but simply observing that no more air is coming out is no guarantee of it. Perhaps there is air farther in, or in such small capillaries it simply refuses to budge. Perhaps on one part, the heated oil bath does all we think it does, but on another part it doesn't.
Does getting every little micro-bubble of air out matter? I suppose that's debatable. Personally though, critical as these parts are, I'd rather not have to worry about it. If one is simply adding lubrication to a bushing that's in service, perhaps it's not that important, but in those cases where one has gone to great pains to remove all old oil and contamination from a bushing (thereby filling it with air) it may matter quite a bit.
To that end, trying to duplicate the process that is used commercially, to the extent possible, doesn't strike me as making things unnecessarily complicated, more providing additional assurance that the job really gets done.
What I plan to do is to try and set up a system that allows me to first use the standard soak in hot oil bath to remove as much air as possible, then seal the jar and turn on the vacuum. If after having done that with several bushings the vacuum does not remove any additional air, then I'd say it's only worth the time if it actually ends up saving time.
Using a vacuum process to infuse the bushings in the first place makes some sense as the nooks and crannies in the bushing are full of air, (and some carbonized wood) such should not be the case with used bushings which would generally be full of congealed oil. In a commercial scenario speed is of the essence.
I don't believe vacuum on its own would do a good job of extracting old oil from a bushing, but in conjunction with heat it might improve the results slightly to significantly.
I have observed that hot oil is a pretty good solvent, and would expect that soaking the bushings in hot oil with some limited agitation would tend to displace most of the remaining residue. Vacuum could help here too.
I don't believe these bushings were made by Oilite, and have not been able to find any reference to how these bushings were actually manufactured. (I'm assuming these were made either by the motor manufacturer or one of its suppliers in Switzerland.)
I don't believe vacuum on its own would do a good job of extracting old oil from a bushing, but in conjunction with heat it might improve the results slightly to significantly.
I have observed that hot oil is a pretty good solvent, and would expect that soaking the bushings in hot oil with some limited agitation would tend to displace most of the remaining residue. Vacuum could help here too.
I don't believe these bushings were made by Oilite, and have not been able to find any reference to how these bushings were actually manufactured. (I'm assuming these were made either by the motor manufacturer or one of its suppliers in Switzerland.)
Thanks for that interesting ancecdote Nigel. I think it might be tempting to read certain things into it. Given this thread has spent some considerable bandwidth discussing the start-up behavior of the TD124 and its E50 powered drive train, there might be some inclination for those among us to suggest that the Garrard motor may take some time to get fully speed stable.
But there aren't many discussion on the subject of 301 warm up times around the web, so I suppose that the Garrard does not exhibit the same tendencies as the TD124 in regard to cold-starting.
Certainly, it would make sense that the BBC or any radio station would want to ensure that their turntables were speed stable before airing any of their playback. Probably that is what I read into the above anecdote.
The other part about not seeing any significant wear is another useful point that those among us Td124 users may consider with regard to motor bushings and whether or not to replace.
I try to take a mechanic's pragmatic approach; without evidence to suggest bushing wear, I'd see to real reason to replace the original bushings.
Lastly I think it might be interesting to discuss the cold starting behavior of a well sorted 301.
-Steve
The Garrard motor is more sturdier then the TD124 motor same for the bushings I have never replaced them.
About the motor (Schopper site)
The fundamental problem of the TD 124 was (and remains) the motor - a problem which is, incidentally, common to all other turntables using the E 50 motor. The motor, which was not produced by Thorens but sourced from suppliers, inevitably suffered from technical limitations, namely the quality of the bearing. Cost considerations - at the beginning of the 60's an E 50-type motor cost some 10 euros to manufacture - meant that the motor quality is simply no match for the other elements which define the astonishing overall quality of the TD 124. The original motor bearings were made from tinned bronze. After 40 years, these have become dried and brittle. No simple oiling can solve the problem!
Volken
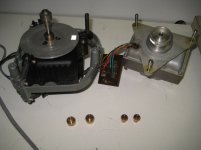
I agree about the quality of the motors. I have probably stripped 100 plus 301/401 and I guess 5 x TD124. If only ones teeth were as good as these bearings. The metal is formed in a pressed mold. It is like coral. The size is set by the mold and never is different sample to sample. If run without oil they last less than a day. If they have enough oil I dare say 500 years. The only problem the oil can have is if it solidifies. If like the Garrard the critical thing is the felt inside the bearing must not dry up. The heat of the motor makes for a tidal pumping of oil. The heat replacing the moon as the tidal motive force. Most of what is said here is highly unimportant. These bearings are binary. They work or they don't work ( replacements may not be as good as seen here ). 2 minutes to speed means as good as it gets. The oil is the reason and not the bearing, The oils has to swim in the rotational direction. It takes time and heat. The elements that swim look like tadpoles. Water does not do this and some modern lubricants are more like water. Usually the bronze does not like these modern types and sends out crystals of phosphoric acid. Now if you want a problem that will work every time. Mobile One comes to mind. 10 minutes to speed would not be too bad. When they are dead the noise is high. Also the bearing often looks egg shaped. 100 % more important is the motor thrust bearing. Do what you can. To be honest the Garrard and Thorens only have a 2 week life from new on that. Removing that noise is to have a much better turntable. How you do it takes some imagination. Don't repair the one you have. Two weeks later it will be the same. I never tried graphite. It might work.
What about impregnating a high porosity graphite bearing in a vacuum at high temperature?
Ticks many boxes and easy to try. Might have to play around to find the right viscosity oil.
Maybe an oil that changes the most at the E50's operating temp. Sluggish/sticky when cold and smooth at running temp.
Ticks many boxes and easy to try. Might have to play around to find the right viscosity oil.
Maybe an oil that changes the most at the E50's operating temp. Sluggish/sticky when cold and smooth at running temp.
That could work very well. I suspect 60 to 80 C is the ideal temperture. SAE 20 or 30 in a simple mineral oil . ATF is OK ( the red stuff used for power steering and gearboxes, not EP80/90 ). I dare say SAE 10 OK if graphite loaded. Slick 50 PTFE oil was tried. Not sure it was sucessful. I think it gummed up the bearings over time . Molyslip is an interesting idea if it still exists.
Why does the motor speed up as the temperature rises?
Or put that another way:
why does it slow down when the little bit of extra drag from cooler lubricant does not affect motor speed in all other types of motors?
It sounds like the "slip" is round the corner and getting worse as extra drag is applied.
Is this a consequence that goes along with the speed adjuster? or is this slip vs drag due to some other factor of these motors?
Or put that another way:
why does it slow down when the little bit of extra drag from cooler lubricant does not affect motor speed in all other types of motors?
It sounds like the "slip" is round the corner and getting worse as extra drag is applied.
Is this a consequence that goes along with the speed adjuster? or is this slip vs drag due to some other factor of these motors?
Kevinkr - I agree the concept of using a vacuum makes more sense for re-infusion, and that the hot oil may actually be a safe way to help clean out old oil - go through the standard process, re-infuse, then gently heat the bushing again. A rinse and repeat process. It does require additional new oil, but at least nothing other than oil ever touches the bushing.
nigel pearson - That's the first mention I can recall that the original bushings were pressed. If anyone would know, I'd think it would be you. As you say, the use of a mold assures consistency in dimensions, but also gets you that "coral" surface that's indicative of a good porous part. It also speaks to critical differences between new and old bushings, consistency being only one. The pressed parts may have gone through some fairly gentle cleaning process before being infused with Thorens-specified oil, but that was it.
I also agree with you, Nigel that it's the oil doing the work. My focus on trying to properly clean the old bushings is to assure the oil "tadpoles" have multiple clear paths from the felt to the interior of the bushing (top to bottom).
In a perfect world, someone with the means and interest in these turntables would couple with a fabricator capable of making new molds and pressing new bushings, but I imagine the initial cost, coupled with inability to sell them in any volume to more than recoup that cost probably makes that a pipe dream. Thus my desire to safely "restore" bushings that are not worn.
Nigel, I would appreciate hearing your thoughts on the possibility of "re-forming" original E50 bushings, as I've heard of one person who states it can be done and that it was something recommended by one or more engineers who at some point worked for Thorens. I have only a rough understanding of the process, but it sounds similar to the original manufacturing process, in that in involves pressure and heat. Perhaps a mold of sorts that duplicates the original, coupled with a shaft of proper diameter?
nigel pearson - That's the first mention I can recall that the original bushings were pressed. If anyone would know, I'd think it would be you. As you say, the use of a mold assures consistency in dimensions, but also gets you that "coral" surface that's indicative of a good porous part. It also speaks to critical differences between new and old bushings, consistency being only one. The pressed parts may have gone through some fairly gentle cleaning process before being infused with Thorens-specified oil, but that was it.
I also agree with you, Nigel that it's the oil doing the work. My focus on trying to properly clean the old bushings is to assure the oil "tadpoles" have multiple clear paths from the felt to the interior of the bushing (top to bottom).
In a perfect world, someone with the means and interest in these turntables would couple with a fabricator capable of making new molds and pressing new bushings, but I imagine the initial cost, coupled with inability to sell them in any volume to more than recoup that cost probably makes that a pipe dream. Thus my desire to safely "restore" bushings that are not worn.
Nigel, I would appreciate hearing your thoughts on the possibility of "re-forming" original E50 bushings, as I've heard of one person who states it can be done and that it was something recommended by one or more engineers who at some point worked for Thorens. I have only a rough understanding of the process, but it sounds similar to the original manufacturing process, in that in involves pressure and heat. Perhaps a mold of sorts that duplicates the original, coupled with a shaft of proper diameter?
Using a vacuum process to infuse the bushings in the first place makes some sense as the nooks and crannies in the bushing are full of air, (and some carbonized wood) such should not be the case with used bushings which would generally be full of congealed oil. In a commercial scenario speed is of the essence.
I don't believe vacuum on its own would do a good job of extracting old oil from a bushing, but in conjunction with heat it might improve the results slightly to significantly.
I have observed that hot oil is a pretty good solvent, and would expect that soaking the bushings in hot oil with some limited agitation would tend to displace most of the remaining residue. Vacuum could help here too.
I don't believe these bushings were made by Oilite, and have not been able to find any reference to how these bushings were actually manufactured. (I'm assuming these were made either by the motor manufacturer or one of its suppliers in Switzerland.)
The process as described to me is intended to true up an out-of-round, worn bearing, not to duplicate the pressure and heat used to create the original part.
Sintered bearing use very high pressure and very high temperature during manufacture.
Way beyond what us amateurs can conceive and/or build.
Standard Oilite works and is made to the highest standards. Machining a badly worn original and dropping in the Oilite is an option . A high quality pillar drill and reamer to finish would be possible. The problem is the inferface is now blocked by the machining . Drilling two oilways East West in the original will help rescue that ( Bearing is North South ). Space them to be 90 degress apart ( Two drillings, four holes, ream to deburr ). If a 5 x 8 x 10 mm Oilite bush was used for example the original might be large enough to take it. I have done this where Oilite was dropped into cast iron. I am assuming felt oil pads to retain some oil.
As Andrew says the processs to make these bearing is exacting. They seldom cost $1 each making us think they are cheap and nasty.
Andrew is right to say the magnetic brake comes into it. Verdier firmly beleived these things to be of advantage. Once stasis is reached the stylus less likely to cause reaction from the drive system asd it is a damped system. Mr Verdier spoke of the force to overcome drag as being 10 times that of what the stylus could do. Not sure I completely got the picture he was painting, sounds about right. I think the speed is simply drag and the way oil thins when hot. The bearing gap is small enough to make it a noticable. In percentage terms it is about 1.5 % and only 0.1 % after a minute very often. We could invent a servo to regulate the magnet. That would be excellent.
As Andrew says the processs to make these bearing is exacting. They seldom cost $1 each making us think they are cheap and nasty.
Andrew is right to say the magnetic brake comes into it. Verdier firmly beleived these things to be of advantage. Once stasis is reached the stylus less likely to cause reaction from the drive system asd it is a damped system. Mr Verdier spoke of the force to overcome drag as being 10 times that of what the stylus could do. Not sure I completely got the picture he was painting, sounds about right. I think the speed is simply drag and the way oil thins when hot. The bearing gap is small enough to make it a noticable. In percentage terms it is about 1.5 % and only 0.1 % after a minute very often. We could invent a servo to regulate the magnet. That would be excellent.
I've done it a number of times with different motor bushings, most of which have no history known to me. Others have done it countless times without having the bushings catch on fire. I'm relatively confident that the combustion temperature for these sorts of oils is well beyond 200 degrees F. You could use a solvent to clean out the bushings, but my understanding is that you may remove the carbon in the bushing which is an integral part of how the oil is stored and wicks through the bushing. This I am told ruins the bushing, this might be hearsay..
I am almost 100% confident that vacuum will not remove the old oil from the bushing, there should be nothing for it to act against, and the original lubricant will have turned to goo or worse.
If you are concerned I would just purchase proper new bushings from a reliable source like Simone Luchetti here: Thorens TD 124 E50 Thorens 135 121 184 Complete Motor Rebuild Kit Made in Italy | eBay
These are real sintered bronze bushings, and should work quite well given his attention to detail.
To my knowledge these bearings are not sintered self-lubricating bearings !
There have been good oilite replacement bushings made for these motors in the past - I've installed them. The ones Simone Luchetti offers on eBay have the correct appearance in photographs and I suspect work just fine.
I have no way of knowing for certain but I suspect the problem with my bushings could be due to inappropriate machining practices during fabrication or incorrect material or both. The originals look a lot better under close inspection, and in several days of use seem to fully address my issues..
Volken has a very good point about the age and condition of the originals, but I fell that these old bushings even with the stated shortcomings may be substantially better performers than a badly made replacement. It would be great if someone made something with high tech materials as a replacement.
Everyone talks about the bearing as it if were really the only thing wrong with these motors, which is clearly not the case. Good tight bearings do not change the fact that these motors are quite noisy and being shaded pole induction motors are quite sensitive to voltage, temperature and loading.
Finally I have commented before and will do so again about these tables loosing their sonic soul (really their great dynamics as much as anything) if motor torque is reduced by substantially lowering line voltage and backing the brake off. I had no rational explanation for this - the table is running at the proper speed, but perhaps the instantaneous speed is now modulated to some extent be tracking induced drag.
I have no way of knowing for certain but I suspect the problem with my bushings could be due to inappropriate machining practices during fabrication or incorrect material or both. The originals look a lot better under close inspection, and in several days of use seem to fully address my issues..
Volken has a very good point about the age and condition of the originals, but I fell that these old bushings even with the stated shortcomings may be substantially better performers than a badly made replacement. It would be great if someone made something with high tech materials as a replacement.
Everyone talks about the bearing as it if were really the only thing wrong with these motors, which is clearly not the case. Good tight bearings do not change the fact that these motors are quite noisy and being shaded pole induction motors are quite sensitive to voltage, temperature and loading.
Finally I have commented before and will do so again about these tables loosing their sonic soul (really their great dynamics as much as anything) if motor torque is reduced by substantially lowering line voltage and backing the brake off. I had no rational explanation for this - the table is running at the proper speed, but perhaps the instantaneous speed is now modulated to some extent be tracking induced drag.
To my knowledge these bearings are not sintered self-lubricating bearings !
Stated very clearly in the auction that they are!
You should find if you remove the brake it is marginally worse. If you lower the voltage also. The idea of a flywheel with just enough power to give correct speed seems false. You could try a larger pulley and more brake and higher voltage. You could try a pulley as in cambelts to get the ideal belt loading.
Based entirely on visual inspection, as I've yet to install them, I agree Simone's replacement bushings do seem to be well made. All I've read on the subject of machining from stock Oilite suggests it takes great care and experience working with the material. I don't think it's something one masters simply by reading the documentation found on the web.
I'll be posting a few photos of my own bushings later in the day. Sadly, I have not disassembled my E50 so I can't at this time provide a closeup photo of the originals. I believe Volken may have a set he could photograph, as they appear in the photo of the disassembled motor he posted.
About your comments on losing the "soul" of the turntable by backing off on the brake too much - it makes total sense to me. I would think the tension in the drive system provided by the eddy brake "pushing back" against the motor would tend to further stabilize the entire system.
I'll be posting a few photos of my own bushings later in the day. Sadly, I have not disassembled my E50 so I can't at this time provide a closeup photo of the originals. I believe Volken may have a set he could photograph, as they appear in the photo of the disassembled motor he posted.
About your comments on losing the "soul" of the turntable by backing off on the brake too much - it makes total sense to me. I would think the tension in the drive system provided by the eddy brake "pushing back" against the motor would tend to further stabilize the entire system.
There have been good oilite replacement bushings made for these motors in the past - I've installed them. The ones Simone Luchetti offers on eBay have the correct appearance in photographs and I suspect work just fine.
I have no way of knowing for certain but I suspect the problem with my bushings could be due to inappropriate machining practices during fabrication or incorrect material or both. The originals look a lot better under close inspection, and in several days of use seem to fully address my issues..
Everyone talks about the bearing as it if were really the only thing wrong with these motors, which is clearly not the case. Good tight bearings do not change the fact that these motors are quite noisy and being shaded pole induction motors are quite sensitive to voltage, temperature and loading.
Finally I have commented before and will do so again about these tables loosing their sonic soul (really their great dynamics as much as anything) if motor torque is reduced by substantially lowering line voltage and backing the brake off. I had no rational explanation for this - the table is running at the proper speed, but perhaps the instantaneous speed is now modulated to some extent be tracking induced drag.
- Home
- Source & Line
- Analogue Source
- Restoring and Improving A Thorens TD-124 MKII