I'm building an Extreme Slop Crossover for the Klipschorns. the inductors are very big (~2-3-4 mH) so I decided to test my skill in winding them myself. the result is far better than I expected. all wires are twisted in order and side by side
BUT I used an aluminum core as bobbin, I know aluminum is a metal of no magnetic properties, but wanted to check if it would cause a problem in sound
any help appreciated
pic:
pic:
An externally hosted image should be here but it was not working when we last tested it.
Hi ARIYAHOOR,
I have to say that your inductor looks great and you were wise to raise the question about the aluminum core. Unfortunately, having an aluminum core will significantly affect it. The problem is that the core acts as a shorted turn and affects the main winding via transformer action.
Regards
Peter
I have to say that your inductor looks great and you were wise to raise the question about the aluminum core. Unfortunately, having an aluminum core will significantly affect it. The problem is that the core acts as a shorted turn and affects the main winding via transformer action.
Regards
Peter
Not inductive, but you could set up eddy currents in it.
You have quite a piece of art there that took a lot to build. I try and make my air core coils purely air core. I wind them on a wood rod with wax paper protecting the spool sides. Then dip in varnish. When dry, slip it off and a nice neat coil. Will it effect the sound of a K-Horn? I doubt it.
You have quite a piece of art there that took a lot to build. I try and make my air core coils purely air core. I wind them on a wood rod with wax paper protecting the spool sides. Then dip in varnish. When dry, slip it off and a nice neat coil. Will it effect the sound of a K-Horn? I doubt it.
What's your day job?...Nice work!
Alum...I don't know, I would have used wood.
What is the value? It doesn't look much bigger than a 1mh.
I'm surprised more speaker companies don't install/show XO's on top, back, etc. They are nice to look at and would make it easier to work on them.
btw, how did you cut the slots?
Alum...I don't know, I would have used wood.
What is the value? It doesn't look much bigger than a 1mh.
I'm surprised more speaker companies don't install/show XO's on top, back, etc. They are nice to look at and would make it easier to work on them.
btw, how did you cut the slots?
Hi ARIYAHOOR,
I have to say that your inductor looks great and you were wise to raise the question about the aluminum core. Unfortunately, having an aluminum core will significantly affect it. The problem is that the core acts as a shorted turn and affects the main winding via transformer action.
Regards
Peter
Uh thanks Peter
so aluminum is not good as a bobbin
Not inductive, but you could set up eddy currents in it.
You have quite a piece of art there that took a lot to build. I try and make my air core coils purely air core. I wind them on a wood rod with wax paper protecting the spool sides. Then dip in varnish. When dry, slip it off and a nice neat coil. Will it effect the sound of a K-Horn? I doubt it.
thanks. yeah they look great to me. I didn't expect this look
so what to do now? I can't wind them without any core. the bobbin won't come out after winding. it's tightly stuck and berried under a ton of wires
What's your day job?...Nice work!
Alum...I don't know, I would have used wood.
What is the value? It doesn't look much bigger than a 1mh.
I'm surprised more speaker companies don't install/show XO's on top, back, etc. They are nice to look at and would make it easier to work on them.
btw, how did you cut the slots?
Uh thanks
actually my job has nothing to do with any kinda hi-fi activity
and yes. I think a well-designed and good-looking XO is worth to be at sight . they are piece of art work, just like tube gears so why hid them inside?
BTW, slots are cut using laser CNC as I said.
look at these extreme XOs:
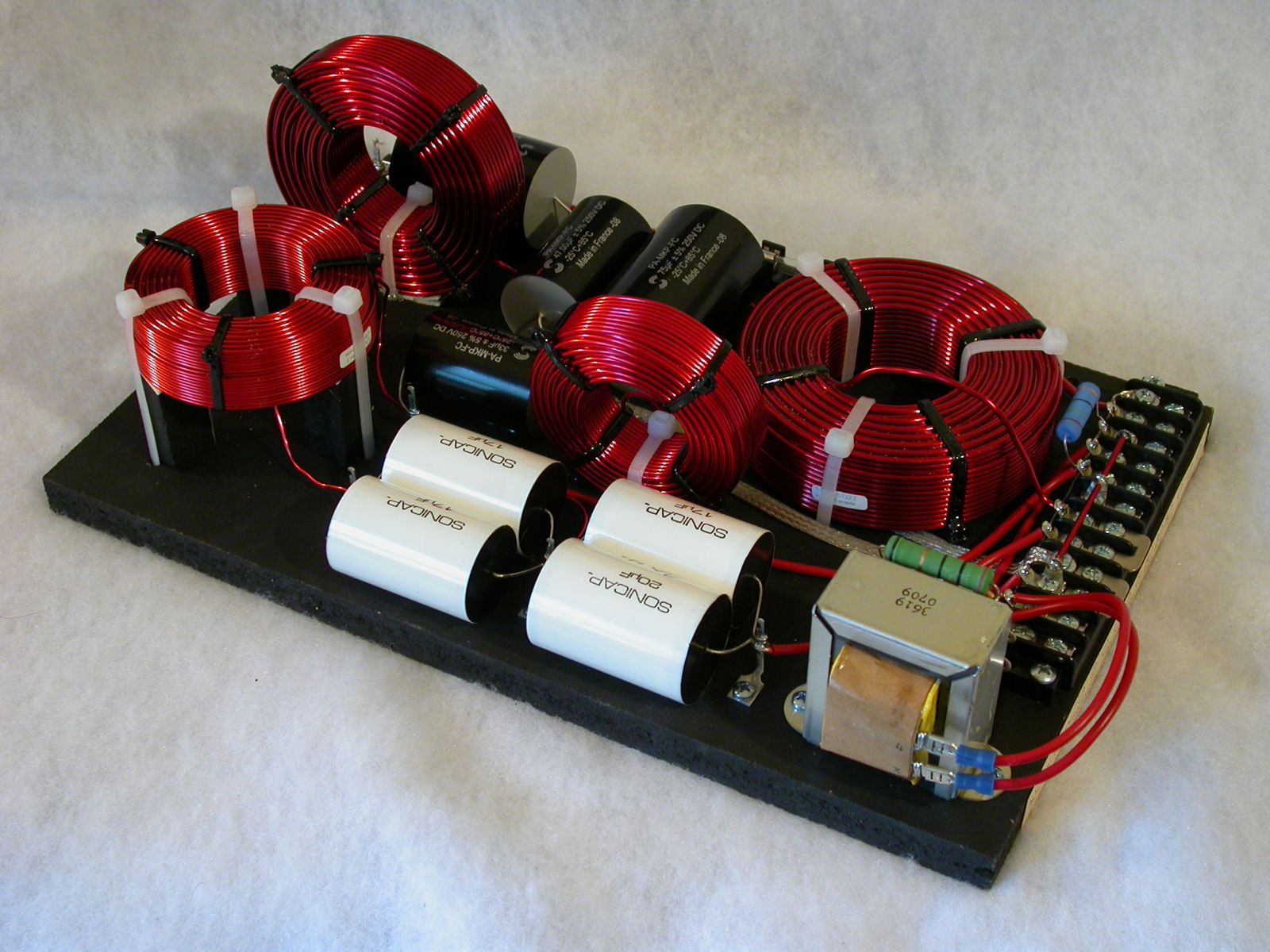
An externally hosted image should be here but it was not working when we last tested it.
Hmmm. Might take a look at those resistors. Are they non-inductive wound?
I use the wax paper to keep the varnish from sticking to the spool. I wrap enough on the bobbin that I can get it to slide off with a piece of tubing pushing the bobbin side.
What is killing me around here is a spool of wire to wind my own costs more than buying coils from PE. It is hard to believe 500' of wire from the factory costs more than manufactured parts, but that seems to be the situation.
How to get your spool out? I think I would try to press it out with a wood or plastic plug of the same size. The plug becomes the new spool. Looks like a job for a hammer!
I use the wax paper to keep the varnish from sticking to the spool. I wrap enough on the bobbin that I can get it to slide off with a piece of tubing pushing the bobbin side.
What is killing me around here is a spool of wire to wind my own costs more than buying coils from PE. It is hard to believe 500' of wire from the factory costs more than manufactured parts, but that seems to be the situation.
How to get your spool out? I think I would try to press it out with a wood or plastic plug of the same size. The plug becomes the new spool. Looks like a job for a hammer!
To get an idea how bad the effect of aluminium on a coil is, you can look at Troels Gravesen's experiments. A sheet of aluminium near a coil reduced measured inductance form 3.3mH to 2.832mH, never mind resistive changes. Yours is worse, I'd reckon:
Placement of coils in crossover networks
Shame that such a nice piece of work is messed up. I made a similar error "tidily" fitting a capacitor inside a coil, which AllenB put me right about. You can just see it inside the red coil here.
Placement of coils in crossover networks
Shame that such a nice piece of work is messed up. I made a similar error "tidily" fitting a capacitor inside a coil, which AllenB put me right about. You can just see it inside the red coil here.
An externally hosted image should be here but it was not working when we last tested it.
To get an idea how bad the effect of aluminium on a coil is, you can look at Troels Gravesen's experiments. A sheet of aluminium near a coil reduced measured inductance form 3.3mH to 2.832mH, never mind resistive changes. Yours is worse, I'd reckon:
Placement of coils in crossover networks
Shame that such a nice piece of work is messed up. I made a similar error "tidily" fitting a capacitor inside a coil, which AllenB put me right about. You can just see it inside the red coil here.
An externally hosted image should be here but it was not working when we last tested it.
Uh you're hundred percent right. it was my first experience of winding inductors and I think I did it fine as everybody who saw this inductor kept telling me "it's wonderful ... a piece of art ... etc..)
Uh you're hundred percent right. it was my first experience of winding inductors and I think I did it fine as everybody who saw this inductor kept telling me "it's wonderful ... a piece of art ... etc..)I think my only mistake was about aluminum but it's ok. you're right about the affect of aluminum on magnetic field. I used 18# wire at 195 turns and diameter was 1.58inches and length of coil is 0.68" ... on the paper it would show 2.4 mH but it turned out to be 1.8 mH!!!
but it'd ok. it was just a prototype. I'll use non-metal bobbins in next ones
I hope Plexiglas is just ok
Wonderful coils , how do you wind it
They look very pretty, but that aluminum in the center is a very bad idea, as has already been said. It acts like a big shorted turn and will reduce the inductance of the inductor while not reducing the resistance --makes it a much worse inductor and uses more copper than needed to achieve the inductance, too. Maybe a plastic dowel for the core? You want something both nonmagnetic AND nonconductive.
Plastic is fine. You do know you have everyone here jealous over your CNC capability!
the laser CNC is my friend's
Wonderful coils , how do you wind it
Uh thanks. I used a 50USD handy winding machine (just counts the turns nothing more) I twisted using hand
They look very pretty, but that aluminum in the center is a very bad idea, as has already been said. It acts like a big shorted turn and will reduce the inductance of the inductor while not reducing the resistance --makes it a much worse inductor and uses more copper than needed to achieve the inductance, too. Maybe a plastic dowel for the core? You want something both nonmagnetic AND nonconductive.
yes I'll use Plexiglas as bobbin. does Plexiglas calssify under plastic category?
Very nice work on the aluminium former. I agree with the others that it isn't the appropriate material. However, if you were to put some notches in the side of it you could use it as a former to make more. Once wound, feed cable ties through the slots to hold the coils stable once you remove the former, similar to the ones you posted later (Solen?). There is no need to have a permanent centre former in the coil.
Very nice work on the aluminium former. I agree with the others that it isn't the appropriate material. However, if you were to put some notches in the side of it you could use it as a former to make more. Once wound, feed cable ties through the slots to hold the coils stable once you remove the former, similar to the ones you posted later (Solen?). There is no need to have a permanent centre former in the coil.
I see but my problem is when I want to take bobbin out and suddenley all the wires jump out like spring coil
I haven't expressed myself well enough. With the 'notches' in the sides almost like gear teeth, you could apply and tighten say 8 cable ties with the former still in place to hold the windings secure. Then remove the former and the windings will still be in place, held by the tightened cable ties.
I haven't expressed myself well enough. With the 'notches' in the sides almost like gear teeth, you could apply and tighten say 8 cable ties with the former still in place to hold the windings secure. Then remove the former and the windings will still be in place, held by the tightened cable ties.
so I'll CNC a bobbin like this with 4 or 8 slots for plastic ties
Attachments
btw, if you have a good helper you can wind them quickly and neatly with a battery drill (makeshift arbor). The helper needs to spool the wire with a lot of friction.
I use a generator, resistor, 2-way switch and volt meter to check values, you can measure them with a good deal of accuracy, down to one turn of wire.
I use a generator, resistor, 2-way switch and volt meter to check values, you can measure them with a good deal of accuracy, down to one turn of wire.
- Status
- This old topic is closed. If you want to reopen this topic, contact a moderator using the "Report Post" button.
- Home
- Loudspeakers
- Multi-Way
- quick question about inductor