"As to design by warranty this is a basic principle of modern quality control theory. If you produce a million units and have no warranty failures then the theory says you spent too much".
Ed Simon,
I guess you don't believe in or work with 6-sigma design goals as that is aimed at having no more than one failure per million. This is the common standard these day in many industries. I don't think it has anything to do with overspending as much as taking the failure modes out of a process. 6-Sigma and Lean manufacturing are more than expected these days in many things I deal with, it is the modern equivalent to what we called SPC when I was much younger.
Ed Simon,
I guess you don't believe in or work with 6-sigma design goals as that is aimed at having no more than one failure per million. This is the common standard these day in many industries. I don't think it has anything to do with overspending as much as taking the failure modes out of a process. 6-Sigma and Lean manufacturing are more than expected these days in many things I deal with, it is the modern equivalent to what we called SPC when I was much younger.
Last edited:
What apparently is missing here is the notion that when you organise your production in such a way that there are no rejects, it sort of automagically leads to the most effective and efficient manufacturing process for the lowest cost.
If you think that production with no rejects is 'spending too much' there's some important things about mass production you haven't understood yet.
To be honest, there ARE some exceptions to this rule but these have to do with really cutting edge production like the next 8-core Intel CPU for instance. But for simple things like audio stuff, make it zero defect and you also make it cheapest.
jan
If you think that production with no rejects is 'spending too much' there's some important things about mass production you haven't understood yet.
To be honest, there ARE some exceptions to this rule but these have to do with really cutting edge production like the next 8-core Intel CPU for instance. But for simple things like audio stuff, make it zero defect and you also make it cheapest.
jan
Zero defects over what time span ?....that is the gotcha/spoiler........ But for simple things like audio stuff, make it zero defect and you also make it cheapest.
jan
Rigorously, by ensuring perfect new parts/sub assy quality, and perfect assembly processing (pcb/stuffing/soldering/final assy/final testing etc), yield of 999,999/1 million is to be entirely expected......and the one failure would need explanation.
Modern manufacturing consistency repeatedly really is that good for entirely electronic items....for example, modern pc mb and i/o boards, modern smart phones, and pretty much any modern item/gadget around the home/workplace.
Every modern thing that I have bought works exactly as advertised when new.....I forget what doa is.
Manufacturing practice used to subscribe to the 'bathtub' theory.
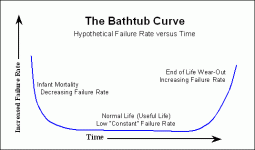
Ime, with the quality of modern manufacturing, it seems that the left side of the graph has collapsed to zero.
Ime, the midpart of the graph is at zero also.
So, that leaves end of life failures only.
That gives rise to the questions, what is considered as suitable/acceptable eol, and is eol predetermined ?.
The main determinant here is the lifetime of aluminium electrolytic capacitors as used in the majority of consumer oriented items.
Most modern equipment runs forever reliable boards/electronics ultimately crippled by little cylindrical time bombs....a perfectly reliable method of obsoleting/executing older equipment.
This 'method' applies to smps mostly.
Dan.
Last edited:
Programmed obsolescence.is eol predetermined ?.
Most modern equipment runs forever reliable boards/electronics ultimately crippled by little cylindrical time bombs....a perfectly reliable method of obsoleting/executing older equipment.
This 'method' applies to smps mostly.
Dan.
Reliability figures, MTBF calculations etc...
There are SMPS's with electros that will work for 15 yrs guaranteed...
I would be more worried about tin whisker failure than electrolytic caps, use a good quality one 3X overvoltage and you should get a good life expectancy. Doing rel figures though these caps are the worst offenders for low MTBF figures unless they are specified correctly.
Sure, commercial gear is expected to run very long lifetime caps...I was more so talking about consumer gear.Reliability figures, MTBF calculations etc...
There are SMPS's with electros that will work for 15 yrs guaranteed...
I would be more worried about tin whisker failure than electrolytic caps, use a good quality one 3X overvoltage and you should get a good life expectancy. Doing rel figures though these caps are the worst offenders for low MTBF figures unless they are specified correctly.
You comment run 3X overvoltage....is this for electrochemical reasons, or larger diameter rubber bung ?....ie what is the mechanism ?.
Yes, I am seeking to understand MTBF electrolytic cap recommendations.
Dan.
What was strange was the comment that the bolt torque was the same with and without the bellevilles. Did he think it would be different?
jn
It was for the MTBF figures for some mil designs, we were getting silly figures of 2 or 3 hours for electrolytic caps with standard overspecyfying so had to go to 3 times... With resistors we had to calculate the voltage across each one and double the power rating. Everything we did was based on MIL-HBK-217 (not the most up to date tome), but from what we could gather (it is a bit of a black art is getting these figures!) the more prone to failure due to heat the greater the over specification has to be to limit the stress on the components.
We had spread sheets going and added attributes to the components so we could do reports from the layout to the spread sheet to the reliability software. it involved several people and a lot of effort, I can see why a lot of commercial stuff dose not bother with MTBF figures these days.
Oh the other good thing about electrolytic caps is they end up in the bottom of the enclosure after ballistic tests, unless you smother them in about a square meter of electronic grade silicone or similar....
Relex Reliability Software - General Information
http://www.sre.org/pubs/Mil-Hdbk-217F.pdf
We had spread sheets going and added attributes to the components so we could do reports from the layout to the spread sheet to the reliability software. it involved several people and a lot of effort, I can see why a lot of commercial stuff dose not bother with MTBF figures these days.
Oh the other good thing about electrolytic caps is they end up in the bottom of the enclosure after ballistic tests, unless you smother them in about a square meter of electronic grade silicone or similar....
Relex Reliability Software - General Information
http://www.sre.org/pubs/Mil-Hdbk-217F.pdf
A perfect example of **** poor planning would be the first generation of the Apple Imac computers where the caps failed on the mother boards. I attempted to fix one of these for a friend but the solder they used on those boards made replacing those caps a major foo pah. What was the cost in bad publicity, even though Apple tried real hard to cover this up as always. What were the cost to fix those early models vs the cost of a quality capacitor?
Lean/ Six-sigma is the industry standard in most places today and anyone not understanding the principals and methods is sorely behind the time I must say. These were the standards that I have had to work to in aerospace and I will carry that with me in anything I would do today. Anything less is just not going to be competitive these days.
Lean/ Six-sigma is the industry standard in most places today and anyone not understanding the principals and methods is sorely behind the time I must say. These were the standards that I have had to work to in aerospace and I will carry that with me in anything I would do today. Anything less is just not going to be competitive these days.
snip... based on MIL-HBK-217......
Yuk, hated using that.
Still have nightmares.
MTBF figures can be pointless when an operator runs a process at the edge as well.
John
A bellleville washer is mainly effective in high mechanical shock situations where the fastener is torqued with in its hook's law cure and stretches further under the load of the device being clamped. The washer helps maintain contact and hence slippage orthogonal to the clamping force. And since screws like to back out and never tighten, they help to maintain the torque. They do not affect the initial torque values of the fastener.
The coolest example of the are the screws that are used on every automobile flywheel in the world. Designed in the thirties, this fastener had a counterbore on its head with radial slots. This allows the head to flex and essentially become a belleville washer.
The coolest example of the are the screws that are used on every automobile flywheel in the world. Designed in the thirties, this fastener had a counterbore on its head with radial slots. This allows the head to flex and essentially become a belleville washer.
Last edited:
Lean/ Six-sigma is the industry standard in most places today and anyone not understanding the principals and methods is sorely behind the time I must say. These were the standards that I have had to work to in aerospace and I will carry that with me in anything I would do today. Anything less is just not going to be competitive these days.
A place I worked at for many years, we studied the full Toyota Way, now ingrained in my mind and work ethic. I totally agree a company has to follow these philosophies to compete and stay successful...
John, I agree, MTBF is a pain, we had a team working on it...trying to relate MIL-HBK-217 to modern components was fun, it is rather dated. The resistors were probably the biggest pain, recording the actual voltage they would see in circuit for everyone, then extracting that data kept a couple of engineers busy for quite a while,,,then replacing any that were getting near to half power rating as well as covering the extremes of the operating temperature. This project was up to 2.4 billion so we could afford to do this, commercial projects just cant recoup the costs, so its only the mil/space where I hear those dreaded words "can we have mtbf figures"
Last edited:
Last I looked five 9s was a measure of availability. Not the same as warranty failures. Maybe you folks should read up on Deming and statistical quality control.
Automated processes do allow for consistent processes, but virtually every product starts with some variation of processed dirt!
Even the "precision" steel I buy varies in strength by 5% typically. That means when it gets bent the amount of elongation is not always exactly the same.
It is as you build systems you can add redundancy and other techniques to increase the system reliability.
The knowledgable bean counters do understand that increased reliability costs more. When you buy a cheap item you don't expect it to last as long as a premium version. So more warranty failures can be tolerated and less costs.
Automated processes do allow for consistent processes, but virtually every product starts with some variation of processed dirt!
Even the "precision" steel I buy varies in strength by 5% typically. That means when it gets bent the amount of elongation is not always exactly the same.
It is as you build systems you can add redundancy and other techniques to increase the system reliability.
The knowledgable bean counters do understand that increased reliability costs more. When you buy a cheap item you don't expect it to last as long as a premium version. So more warranty failures can be tolerated and less costs.
Warranty failures, do more damage than just a few returned parts though, the most critical one is the company getting a bad name. Disregarding very cheep consumer products that you get in discount store etc. All high volume designs and companies I have worked with have designed and worked to not have failures. Designing based on warranty failures is "designing for failure" not the best ethic to have.
Reminds me of talking, many decades ago, to an old school, white goods service chappy who once worked for one of the biggest local manufacturers of fridges, washing machines, etc - and he mentioned that one of the most important tests they did way back in those days was throwing a specimen of a new design, in its packing crate, on the back of an ordinary truck - and driving across the Nullarbor Plain and back, an extremely long and at the time bone jarring road. Of course it had to survive this, still be perfect - the point being that many extremely isolated properties were big buyers of such items, and the warranty costs would have been a killer if such goods weren't able to take this abuse while being transported to their new home ...
Warranty failures, do more damage than just a few returned parts though, the most critical one is the company getting a bad name. Disregarding very cheep consumer products that you get in discount store etc. All high volume designs and companies I have worked with have designed and worked to not have failures. Designing based on warranty failures is "designing for failure" not the best ethic to have.
We are talking about "bean counters." Many products have design lifetimes, others planned obsolescence.
Even with perfect products there is still a warranty claim rate. Some folks will deliberately damage goods to return them.
There really is a reason why warranty service stations have to fill out repair claim forms.
Crest amplifiers used to use warranty failures to determine how many output devices were required for use by their customers in the real world.
I have an issue now with a 70 volt amplifier driving a small system that has three auto transformer 75 watt volume controls. What do you think happens when the amplifier is driven hard and all the controls are set to zero?
Is that a warranty failure?
- Status
- Not open for further replies.
- Home
- Member Areas
- The Lounge
- John Curl's Blowtorch preamplifier part II