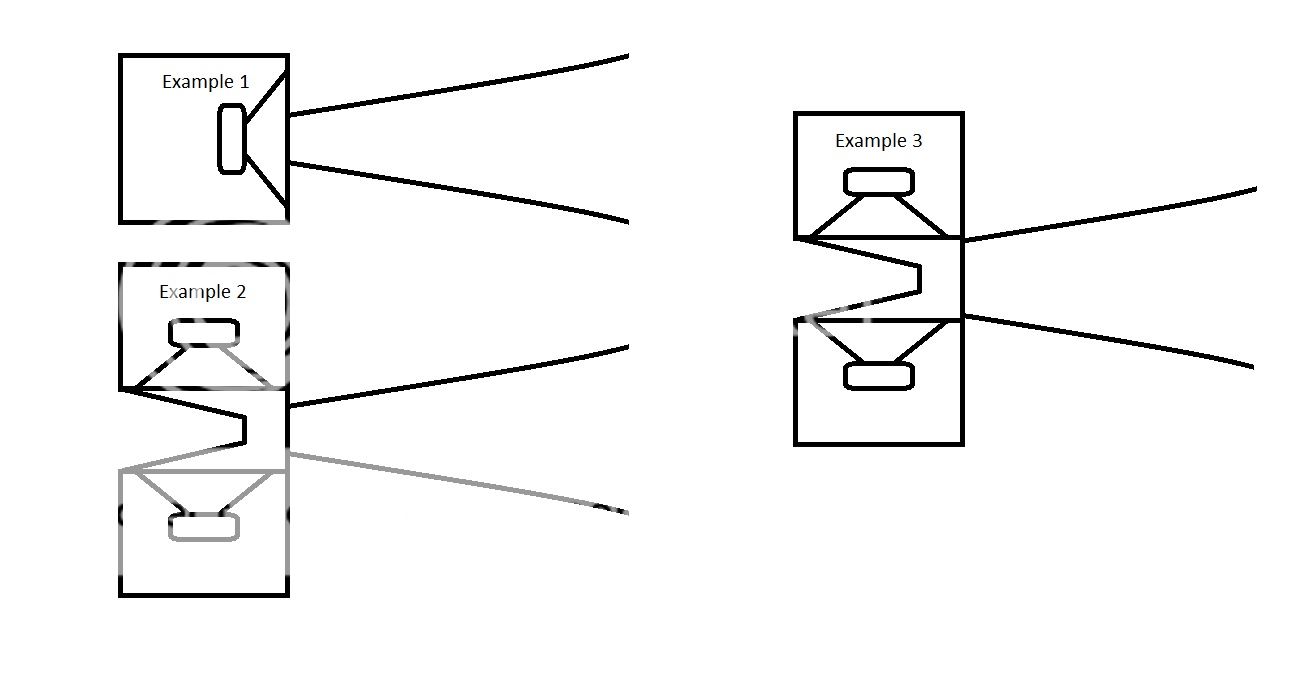
I have a conceptual question that I’ve been unable to answer. Specifically, in example 1 above (a hypothetical 20-Hz exponential bass horn - please forgive the crudeness of my Microsoft paint drawing) - I’ve got a 12” driver (Sd = 500 cm^2), mated with a 167 cm^2 throat, for a compression ratio of 3:1.
Question: if I add a second driver (as shown in Example 2 - to achieve greater overall output from the horn), do simply double the Sd value when computing my new compression ratio? I.E. a resultant 6:1 compression ratio – provided my 167 cm^2 throat size remained unchanged? I know this seems like an extremely trivial question, but I’ve been unable to find the answer. And I’m not even sure that adding a second driver is a good idea. . . . Which is why I’m asking.
Assuming it is a good idea - is readjusting the compression ratio back down to 3 as simple as shortening the short-end of the horn (to double the throat area, per example 3)?
Thanks!
Eric.M
Question: if I add a second driver (as shown in Example 2 - to achieve greater overall output from the horn), do simply double the Sd value when computing my new compression ratio? I.E. a resultant 6:1 compression ratio – provided my 167 cm^2 throat size remained unchanged?
Yes, the compression ratio will be doubled.
Assuming it is a good idea - is readjusting the compression ratio back down to 3 as simple as shortening the short-end of the horn (to double the throat area, per example 3)?
Yes, but preferably maintain the same horn length by extending the mouth end of the horn to compensate for the length removed from the throat end.
First of all, it's almost impossible to physically make a bass horn as depicted in Example 1. It has been done but it requires either a symmetrical layout or a bunch of wasted space surrounding the throat area or a really complex fold.
Given that, horns are almost always laid out with the driver offset like example 2 and example 3 depicts, such that the driver doesn't fire into the beginning of the horn like example 1.
That also means that in example 2 and 3 the horn doesn't start at the black line, it starts at the very left edge of the driver, as shown the horn begins at the very point at the leftmost edge of the drivers.
Compression ratio is always Sd / the cross sectional area of the horn path where the driver enters the horn. If you have multiple drivers and/or multiple horn paths, add up the cross sectional areas of all the paths and add up the Sd of all the drivers and perform the same equation, Sd / cross sectional area of the horn where the drivers enter the horn.
In example 2 and 3, your driver enters the horn at the midpoint of the driver. So if you were using Hornresp, S1 (the beginning of the horn flare) would be at the leftmost point of the driver, S2 would be the midpoint of the driver and compression ratio would be Sd/S2.
But in reality you won't ever see a notched out space wasting area at the beginning of the line like you showed in example 2 and 3. It will look more like this.
or like this
Given that, horns are almost always laid out with the driver offset like example 2 and example 3 depicts, such that the driver doesn't fire into the beginning of the horn like example 1.
That also means that in example 2 and 3 the horn doesn't start at the black line, it starts at the very left edge of the driver, as shown the horn begins at the very point at the leftmost edge of the drivers.
Compression ratio is always Sd / the cross sectional area of the horn path where the driver enters the horn. If you have multiple drivers and/or multiple horn paths, add up the cross sectional areas of all the paths and add up the Sd of all the drivers and perform the same equation, Sd / cross sectional area of the horn where the drivers enter the horn.
In example 2 and 3, your driver enters the horn at the midpoint of the driver. So if you were using Hornresp, S1 (the beginning of the horn flare) would be at the leftmost point of the driver, S2 would be the midpoint of the driver and compression ratio would be Sd/S2.
But in reality you won't ever see a notched out space wasting area at the beginning of the line like you showed in example 2 and 3. It will look more like this.
An externally hosted image should be here but it was not working when we last tested it.
or like this
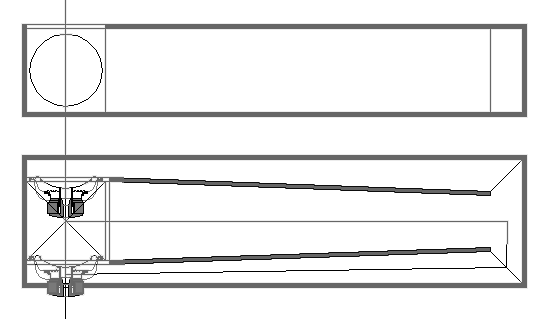
Last edited:
That also means that in example 2 and 3 the horn doesn't start at the black line, it starts at the very left edge of the driver, as shown the horn begins at the very point at the leftmost edge of the drivers.
Being a bass horn, it is probably easier just to simulate the example design with S1 assumed to be at the black "throat" line, and the volume between the drivers and S1 treated as a simple throat chamber (specified in Hornresp using Vtc and Atc).
It's just as easy to sim it accurately though. If you do it the way you suggested you won't see the monster notch that OD designs have. If it's a small driver and pushed right to the beginning of the flare and the desired bandwidth isn't too high it might not matter, but if any or all of those assumptions are incorrect it could cause really big problems.
Aside from the huge notch there will be other small discrepancies from not doing the sim accurately too.
IMO it's always best to do it right, especially when it requires little or no extra effort.
Aside from the huge notch there will be other small discrepancies from not doing the sim accurately too.
IMO it's always best to do it right, especially when it requires little or no extra effort.
Also if you do it the way you suggested Hornresp will not calculate compression ratio properly because you are telling the simulator that the drivers are entering the line much further down than they actually are.
There's literally no downside to doing the sim properly and at least a few potential consequences if you don't.
It's actually probably easier to do it properly, since S1 to S3 is usually going to be a linear PAR expansion anyway, so just calculate the actual beginning of the flare in sq cm, make that S1 and then you don't have to worry about anything until S3. If you do the area in front of the drivers as a bulk throat chamber you actually have to calculate the volume of the irregular shape and then calculate your S1 at the end of the throat chamber as well, so it's more work and the results are not accurate since they are based on less accurate dimensional geometric inputs.
There's literally no downside to doing the sim properly and at least a few potential consequences if you don't.
It's actually probably easier to do it properly, since S1 to S3 is usually going to be a linear PAR expansion anyway, so just calculate the actual beginning of the flare in sq cm, make that S1 and then you don't have to worry about anything until S3. If you do the area in front of the drivers as a bulk throat chamber you actually have to calculate the volume of the irregular shape and then calculate your S1 at the end of the throat chamber as well, so it's more work and the results are not accurate since they are based on less accurate dimensional geometric inputs.
Hi Entropy455,
Apparently, I'm also confused on the subject. Here is what I come up w/ for Hornresp simulations:
Your Example 1 is the classic text book arrangement of a horn w/ sealed back chamber, and a front chamber coupled to the horn w/ a throat opening. Here you should use "Driver Arrangement Normal Nd", and specify chambers/throat/horn. The sound from the throat chamber is coupled through the throat into the horn @ S1.
Your Examples 2 and 3 are similar w/ the main difference being the compression ratio/throat area (chambers/throat/Nd/S1).
If you choose a different construction-as indicated by JAG in Post #3 (top drawing)-you are looking at "Driver Arrangement Offset Driver OD". Here the the sound enters the horn @ S2, and there are no chambers involved; the "throat" is simply the apex between the drivers (S1). This may also be the correct driver arrangement for chambered horns, depending on your construction.
Going on to Post #3, bottom drawing: here you are dealing w/ a tapped horn that should be simulated using "Driver Arrangement Tapped Horn TH"; this is a double throat design (entry port @ S2), and I don't think pertains to your initial question.
So, I second David's answers from Post #2. As JAG pointed out, it also depends a lot on your actual construction.
Post #1: "...I’m not even sure that adding a second driver is a good idea.."
Don't see any reason why not.
Regards,
Apparently, I'm also confused on the subject. Here is what I come up w/ for Hornresp simulations:
Your Example 1 is the classic text book arrangement of a horn w/ sealed back chamber, and a front chamber coupled to the horn w/ a throat opening. Here you should use "Driver Arrangement Normal Nd", and specify chambers/throat/horn. The sound from the throat chamber is coupled through the throat into the horn @ S1.
Your Examples 2 and 3 are similar w/ the main difference being the compression ratio/throat area (chambers/throat/Nd/S1).
If you choose a different construction-as indicated by JAG in Post #3 (top drawing)-you are looking at "Driver Arrangement Offset Driver OD". Here the the sound enters the horn @ S2, and there are no chambers involved; the "throat" is simply the apex between the drivers (S1). This may also be the correct driver arrangement for chambered horns, depending on your construction.
Going on to Post #3, bottom drawing: here you are dealing w/ a tapped horn that should be simulated using "Driver Arrangement Tapped Horn TH"; this is a double throat design (entry port @ S2), and I don't think pertains to your initial question.
So, I second David's answers from Post #2. As JAG pointed out, it also depends a lot on your actual construction.
Post #1: "...I’m not even sure that adding a second driver is a good idea.."
Don't see any reason why not.
Regards,
Your Examples 2 and 3 are similar w/ the main difference being the compression ratio/throat area (chambers/throat/Nd/S1).
If you choose a different construction-as indicated by JAG in Post #3 (top drawing)-you are looking at "Driver Arrangement Offset Driver OD". Here the the sound enters the horn @ S2, and there are no chambers involved; the "throat" is simply the apex between the drivers (S1). This may also be the correct driver arrangement for chambered horns, depending on your construction.
Example 2 and 3 as shown are both OD arrangements. This becomes very clear if you delete the bottom half of the picture and picture it as a single driver horn, it's a classic OD arrangement. If you simulate the area of the horn flare in front of the driver as a bulk throat chamber the sim absolutely will not be accurate for the reasons I mentioned.
Here's example 3 shown as a single driver horn with the bottom half of the pic deleted. As you can see it's a classic OD arrangement there's no way to argue that it's not. Example 2 is the same thing. It doesn't matter if it's shown as a single driver (as shown here) or a dual driver (as OP originally showed) it's very clearly a OD arrangement and Nd will not sim it accurately.
An externally hosted image should be here but it was not working when we last tested it.
Going on to Post #3, bottom drawing: here you are dealing w/ a tapped horn that should be simulated using "Driver Arrangement Tapped Horn TH"; this is a double throat design (entry port @ S2), and I don't think pertains to your initial question.
The point of showing the pictures was to show how horns are normally built. They are definitely not normally built as example 2 and 3 show.
The tapped horn pic is shown to define the fact that you can use dual drivers firing into a single throat (as shown in the first pic I showed) or you can fire into dual throats (as the tapped horn pic shows). The fact that the horn shown is tapped is irrelevant, I couldn't find a flh showing this arrangement in a quick search and didn't feel like editing the pic to only show the throat area with the driver loading topology.
Last edited:
When the wavefront can be reconciled with the horn, such as where the source size is within 1/4wl, it isn't. This places a frequency based limit on the simulation but doesn't declare it null and void. This frequency is likely linked to the upper useful range of the horn anyway.it's a classic OD arrangement there's no way to argue that it's not.
This is two sims of the exact same horn overlaid but one is simulated as Od and one is simulated as Nd. The one with the massive notch in response is obviously the Od one, all Od designs have this. The driver is an 18 inch and pushed as far as possible towards the closed end in the Od sim to keep the notch as high in frequency as possible.
All through the passband (from the low knee up to 120 hz) there is a difference of 1 db, at some places it's higher, at others it's lower. And then right outside the passband is that huge monster notch that will make crossover design a lot different than you might think if you don't simulate it accurately. Also the excursion is different through the entire passband.
Is this worth worrying about? IMO absolutely. YMMV. I'm the guy that talks about accurate sims all the time and I want my sims accurate, not off by a db through the entire passband (and several db right outside the passband) and off by 1 mm excursion all through the passband.
What is the point to doing it wrong when it's literally easier and visibly more accurate to do it right?
All through the passband (from the low knee up to 120 hz) there is a difference of 1 db, at some places it's higher, at others it's lower. And then right outside the passband is that huge monster notch that will make crossover design a lot different than you might think if you don't simulate it accurately. Also the excursion is different through the entire passband.
Is this worth worrying about? IMO absolutely. YMMV. I'm the guy that talks about accurate sims all the time and I want my sims accurate, not off by a db through the entire passband (and several db right outside the passband) and off by 1 mm excursion all through the passband.
What is the point to doing it wrong when it's literally easier and visibly more accurate to do it right?
An externally hosted image should be here but it was not working when we last tested it.
This is why some people refuse to trust sims. If you don't simulate accurately you won't get accurate results. An unexpected 30 db dip right outside the passband in the crossover region? I'd prefer to know about that beforehand, thank you very much. 1 db too high and 1 db too low at different places in the passband? That might seem trivial but it changes the curve shape pretty dramatically. If you don't care that's fine but I care very much.
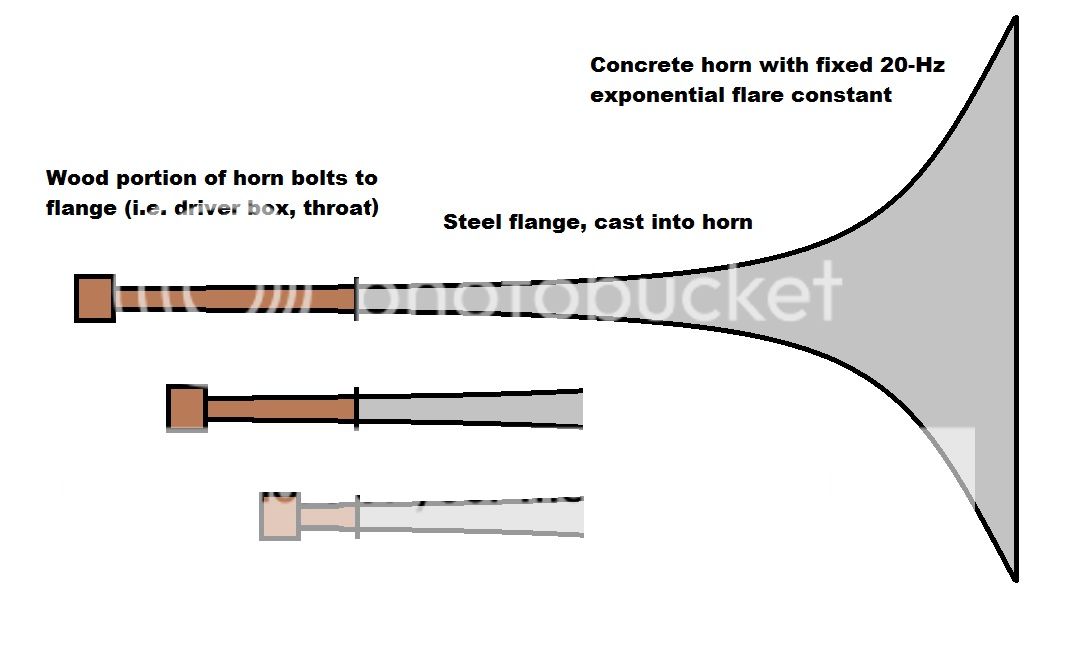
Just-a-guy, I am confused about the monster notch? Is that a function of having a chamber in front of the throat? I read that the front chamber volume (in a front loaded exponential horn) will act as a low-pass acoustic filter. Is that the notch you are referring to?
Hornresp will only model exponential bass horns down to 30.7 Hz (i.e 11.7 foot diameter mouth, assuming Mach is equal to 1126 ft/s). An ideal 20 Hz exponential horn requires a 17.9 foot diameter mouth.
Because I cannot model the horn in Hornresp, I’ve been reading various engineering papers on horn design (the ones published in the early 70s), and I’m attempting to design by hand. One article in particular states that to minimize harmonic distortion (in both the open-space, and half-space loading), that the ideal mouth circumference should be equal to the cutoff frequency wavelength divided by pi. This is why I’m targeting the full 17.9 foot diameter mouth.
My idea is to build the horns out of concrete (outdoor system), and build a small shed to house the rear of the horns. This way I can tinker with the horn design (changing drivers, change throat size, throat geometry, number of drivers, etc), without having to bust away & recast concrete. (I’m trying to take advantage of the fact that the horn’s exponential constant is independent of the finite throat size.)
The old engineering papers made reference to compression ratios, indicating that somewhere between 2:1 and 5:1 as being the typical range for bass horns – with 3:1 being a reoccurring recommendation. The old papers did not make much reference to actual magnitudes of port velocity – only that they must be kept in check. I have read on these forums however that to prevent distortion & nonlinearities, that the throat velocity should be kept below Mach 0.05.
In my original Example 1 (at the top of this thread), a 500 cm^2 driver, into a 167 cm^2 throat (3:1 compression ratio), with a 13-mm Xmax - the driver will pump 1.836 cubic feet of air per second across the throat at 20-Hz (this is at full Xmax, and neglecting any airflow related choking effects). This equates to an instantons peak velocity of 14.45 ft/s across the throat, or Mach 0.0128 - which is well below Mach 0.05. The compression ratio need to hit Mach 0.05 with this driver would need to be upwards of 11.6:1 at 20-Hz.
I also considered frequency-dependence as it relates to Mach in the throat. The old engineering texts state that exponential horns are acoustically as close to a pure resistive load as one can get. This would imply that the cone excursion cleanly increases by a factor of four, every time the frequency is halved. Thus at 80 Hz, the driver's peak-to-peak excrusion will be 16 times less than at 20-Hz. There will be 0.459 cubic feet of air per second flowing across the throat, with a peak velocity of 3.611 ft/s, or Mach 0.0032 – which is much less than the same driver pumping at 20 Hz. Thus increasing the driver frequency, will actually decrease the throat velocity. Again, I’ve neglected the non-linear port-choking effects at higher Mach values.
Nonetheless, using back of the napkin calculations, the need to keep compression ratios low appears to have much more to do with driver-loading, and much less to do with keeping Mach numbers below 0.05 – or am I missing something?
V/R
Eric.M
Using the offset driver function of hornresp, it is assumed that sound goes in both directions. Sound that goes toward the throat and returns will be out of phase with the other at some higher frequency. This is not dissimilar to what happens in a throat chamber only the clear shape of the offset horn gives a more distinct result.Just-a-guy, I am confused about the monster notch? Is that a function of having a chamber in front of the throat? I read that the front chamber volume (in a front loaded exponential horn) will act as a low-pass acoustic filter. Is that the notch you are referring to?
Just a guy.. it seems we agree.
Entropy, the throat region is a bit of a wild card unless you analyse it a little. In short, a given size of region where the sound may get mixed up a bit won't cause a problem below some frequency related to that dimension, so it comes down to higher frequency issues.
The frequency can be extended with effort in the throat region, however this is a bass horn and a compromise can be made.
Hornresp is quite accurate up to the limits of its model.
Just-a-guy, I am confused about the monster notch? Is that a function of having a chamber in front of the throat? I read that the front chamber volume (in a front loaded exponential horn) will act as a low-pass acoustic filter. Is that the notch you are referring to?
Wow, there's a lot of questions in this post, I'll break it down and answer a couple at a time.
Allan is correct, the notch is caused by the sound entering the horn and then diverging, some goes towards the closed end, some goes towards the open end. The waves that go toward the closed end bounce off the closed end and converge with the later waves entering the horn, this causes a cancellation at a frequency based on the distance from the center of the driver to the closed end (x2, it has to travel to the closed end and back).
This notch is apparent and measurable in all offset driver horns, like example 2 and 3 that you posted and the two pics I posted. This notch does not appear in end loaded drivers where the waves exit the driver, go through the throat chamber and enter the horn flare in a straight shot. It doesn't happen because there's nothing to bounce off and redirect the wave.
Hornresp and other simulators calculate in one direction, the length dimension. They do not calculate the width dimension resonances, which can be significant as well, but only when the cross sectional area of the horn becomes significant in size compared to the wavelengths in and directly above the passband.
Hornresp will only model exponential bass horns down to 30.7 Hz (i.e 11.7 foot diameter mouth, assuming Mach is equal to 1126 ft/s). An ideal 20 Hz exponential horn requires a 17.9 foot diameter mouth.
Hornresp couldn't simulate really big horns a year or two ago but I didn't like that limitation and requested that it be increased. David McBean indulged my request and now it can model huge horns. Maybe time for you to update.
This is a 2 pi 14 hz horn with a massive mouth and almost 50000 liters total size. Do a Hornresp update and try again, you can sim whatever you want.
Also note the 2:1 compression ratio - just for you.
An externally hosted image should be here but it was not working when we last tested it.
Now before I continue answering your questions let me show you something super cool. David incorporated a Hypex approximator probably because I complain all the time about how I like to sim accurately and you can't do certain things with hypex flare sims.
So here's another example. (I couldn't show the previous horn example because running the hypex approximator on that huge horn gave runtime error 380 or something consistently every time I tried to run it, and the program closed.)
This example is a 22 hz horn designed with the system design tool (Leach's math) and designed for a 2:1 compression ratio. Note that the compression ratio for this horn will be Sd/S2 because the driver enters the horn at S2. Using the hypex approximator I chopped the horn into 4 CON segments (I wasn't thinking, I should have made them PAR segments) and pushed the driver at S2 as close to the closed end of the flare as possible to lower the notch frequency. Super simple, designing this horn and chopping it into segments you can actually build took about 42 seconds.
Here's the hypex flare designed by Leach's math.
Now here's the hypex approximator at work. Both the original flare response and the chopped up flare response are shown overlaid here.
Now you can do all kinds of neat stuff with this horn that you can't do with a hypex flare horn. You can make it OD (as I did here), you can open this in the loudspeaker wizard, you basically have the full functionality of Hornresp features to use on this - many things are not available with hypex flare horns so this is just a huge bonus because it's so easy to use and so useful.
I'll continue answering your questions but I have to get something to eat first. It will be awhile.
So here's another example. (I couldn't show the previous horn example because running the hypex approximator on that huge horn gave runtime error 380 or something consistently every time I tried to run it, and the program closed.)
This example is a 22 hz horn designed with the system design tool (Leach's math) and designed for a 2:1 compression ratio. Note that the compression ratio for this horn will be Sd/S2 because the driver enters the horn at S2. Using the hypex approximator I chopped the horn into 4 CON segments (I wasn't thinking, I should have made them PAR segments) and pushed the driver at S2 as close to the closed end of the flare as possible to lower the notch frequency. Super simple, designing this horn and chopping it into segments you can actually build took about 42 seconds.
Here's the hypex flare designed by Leach's math.
An externally hosted image should be here but it was not working when we last tested it.
Now here's the hypex approximator at work. Both the original flare response and the chopped up flare response are shown overlaid here.
An externally hosted image should be here but it was not working when we last tested it.
Now you can do all kinds of neat stuff with this horn that you can't do with a hypex flare horn. You can make it OD (as I did here), you can open this in the loudspeaker wizard, you basically have the full functionality of Hornresp features to use on this - many things are not available with hypex flare horns so this is just a huge bonus because it's so easy to use and so useful.
I'll continue answering your questions but I have to get something to eat first. It will be awhile.
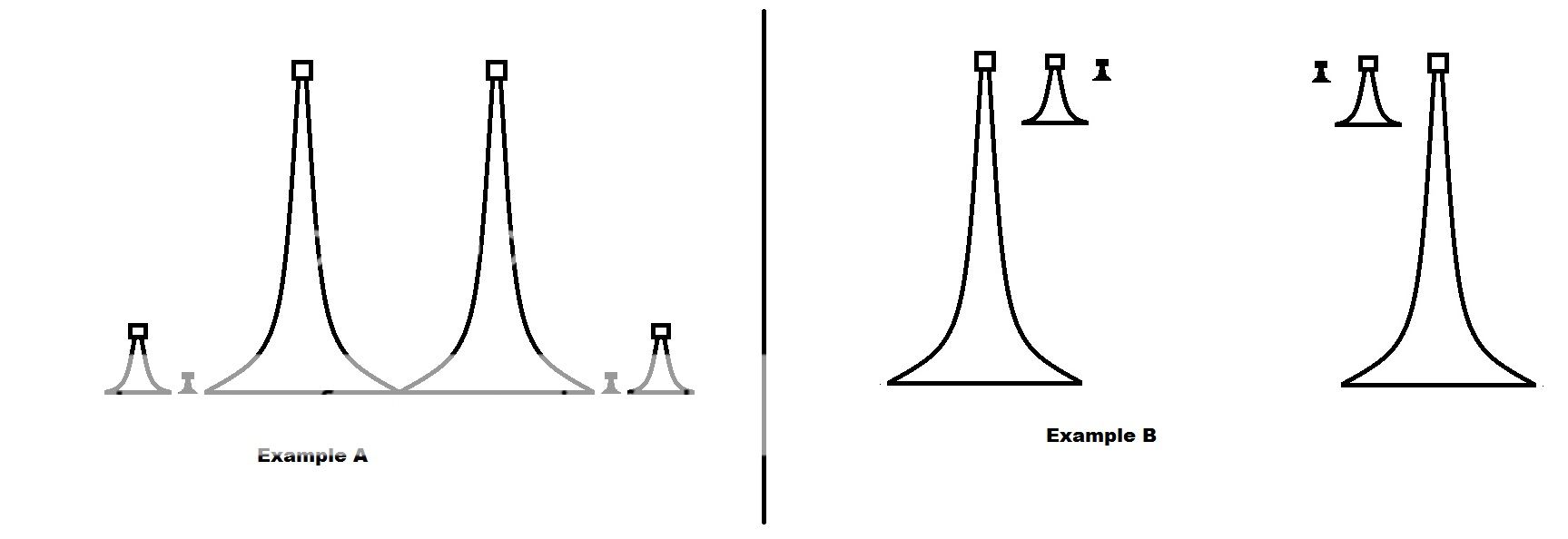
I downloaded Hornresp just a few days ago (it was version 39.70.0.0.) The program limits the mouth size to 99,999 cm^2. Where do I get the most recent version?
Using the 3-octave rule, my bass-horns should be crossed no higher than 160-Hz. My assumption is that if I use multiple drivers (to increase SPL) - , provided my front compression chamber remains small (volumetrically), and my compression ratio remains fixed at approximately 3:1, and each driver’s spacing to the throat remains uniform - I “should” have no impedance dips from 160-Hz and down, from the front chamber loading. My plan is to make no-kidding curved exponential horns, using several layers of thin plywood and a crap-load of form-stiffeners. I must admit, four conical segments would be MUCH easier to frame & cast from concrete. . . . I really need the most recent version of Hornresp. . . .
From what I’ve been reading, a pair of 20-Hz horns, each powered by a single 12” driver, will reportedly produce very impressive sound. Thus I might not even need the extra drivers. I want to listen to music. But I’d like to throw the occasional party also - so the system must also have good dynamic range. Nonetheless, I don’t want to “cast” in a mistake that I made during the design process. . . . I really like the idea of keeping the back section of the horn wood-construction, that way I can play around with the design – and make changes without cutting into reinforced concrete. . . . .
The next large design obstacle on my mind, is the time delay caused by the physical driver offset. I’ve got 5 acres of land out in the woods to build this system, with almost 600 acres of vacant Department of Natural Resources land (DNR) bordering me to the North (thus there are no neighbors to complain about my music). But I digress.
Assuming the ideal listening position is about 100 feet away, I’d like to arrange the horns shown in Example A. But I’d need a time-delay circuit. Does anyone make a fully digital domain circuit, to accomplish this task? I’d like to keep my signal processing fully digital – i.e. from the CD source, through the time delay processor, and through the coross-over network (if possible). I’d prefer to go analog just prior to amplification. I found one delay circuit on the market, however it has an A/D converter on the front-end, and a D/A converter on the output - which is a big turnoff for me. . . . In my opinion, these type of devices tend to be noisy.
My non-time-delay option would be to space the bass horns apart as shown in Example B (which I have room to do), and setback the mid and high compression horns – to physically eliminate the time delay. The only problem I see with this, is the air itself becomes an impedance problem across long distances – particularly above 7-kHz (which is why thunder at distance only booms, and doesn’t crack). I’m not sure if the extra 50 feet or so will make a noticeable difference or not? The bass horn walls & mouth might actually get in the way. My gut tells me Example B will cause more problems than it solves. . .
... I’ve been reading various engineering papers on horn design (the ones published in the early 70s), and I’m attempting to design by hand.
IMO this is a very bad idea. Even if Hornresp could sim a horn this large I'm sure Akabak and TL.app and probably a few other programs could. No need to design this on the back of an envelope.
And while scientific papers are great and have their place, they can't teach you what a lot of playing with a simulator can. Stuff like the offset driver issues isn't going to be covered at all in most horn papers even though most bass horns have offset drivers.
I've read a lot of theory but most of what I learned was from playing with simulators.
My idea is to build the horns out of concrete ..
Again, I think this is a really bad idea. There's two kinds of concrete - concrete with cracks and concrete that's going to crack. Obviously you don't want cracks in your bass horn.
Assuming you can build concrete that doesn't crack I still wouldn't do it. It's a lot easier and probably a lot cheaper to do conventional construction in modular form like the Labhorn, which was designed to work as a single horn with 6 - 8 units stacked. There are so many advantages to conventional construction that I would strongly advise you to think about it.
Anyway, assuming you can build a crackless concrete horn, you can probably build it with curved walls, so you don't need the hypex approximator in that case. Also, since it doesn't need to be folded into a box you can build a true end loaded horn if you want instead of an offset driver horn, in which case you don't have to worry about any of those issues either. It would still probably be a lot easier to do offset though but those details are up to you.
The old engineering papers made reference to compression ratios, indicating that somewhere between 2:1 and 5:1 as being the typical range for bass horns – with 3:1 being a reoccurring recommendation. The old papers did not make much reference to actual magnitudes of port velocity – only that they must be kept in check. I have read on these forums however that to prevent distortion & nonlinearities, that the throat velocity should be kept below Mach 0.05.
Antique drivers used to have paper thin very weak cones, so I assume the talk about low compression ratio was to prevent driver damage. Today's cones can be a lot thicker and stronger and I've seen compression ratios in diy projects in excess of 9:1. Maybe not a good idea in a once in a lifetime full size concrete project to overdo the compression ratio. Danley keeps his compression ratio around 2:1 and he knows what he's doing.
Your project probably won't be subjected to the abuses of Danley's commercial products but a low compression ratio is a good safety feature and it can't possibly hurt with respect to distortion.
If you want to know your air speed, Akabak can simulate velocity at any node in the sim and you can chop your horn up into a LOT of segments if you want so you can check velocity virtually anywhere inside the horn.
Being able to calculate all this stuff is nice but it's not necessary. There's a simulator for virtually everything you can imagine. You can check velocity, pressure on the cone, all kinds of stuff.
I don't particularly care for pure exponential (T=1) flares. They flare out way too fast. This may not be an issue for you.
I prefer hyperbolic exponential flares from the Salmon family (T= less than 1). Usually a hypex flare around T=0.5 will give a nice design when you use Leach's math. When you use flares with a high T you usually end up with very high compression ratios and unrealistically small rear chambers, sometimes too small to fit the driver. I've even seen errors in sims due to chamber volume being less than zero.
This type of design is super simple if you use Leach's math that's built into Hornresp's system design - with driver tool. Simply make sure the driver specs, radiation angle and number of drivers are correctly entered, then start the system design tool, and enter either the desired bandwidth or the desired low frequency knee and flare T and it will automatically design a full size ideal reactance annulled horn for you. If the rear chamber size is too small and the compression ratio is too high run the tool again with a smaller bandwidth or a lower flare T until you get a horn that makes practical sense. It takes seconds to design this way, compared to hours (or days or weeks) to design by hand by going through Leach's paper.
Good luck. Sounds like a fun journey for you.
I downloaded Hornresp just a few days ago (it was version 39.70.0.0.) The program limits the mouth size to 99,999 cm^2. Where do I get the most recent version?
I'm using version 39.7. Hornresp has had the ability to sim very large horns for over a year now. Even if you were limited to 99999.99 you could still sim a 22 hz horn as I just showed. If you are having problems with your sims just show your inputs or even just tell me what you want simulated and I will show you how to do it.
Using the 3-octave rule, my bass-horns should be crossed no higher than 160-Hz. My assumption is that if I use multiple drivers (to increase SPL) - , provided my front compression chamber remains small (volumetrically), and my compression ratio remains fixed at approximately 3:1, and each driver’s spacing to the throat remains uniform - I “should” have no impedance dips from 160-Hz and down, from the front chamber loading. My plan is to make no-kidding curved exponential horns, using several layers of thin plywood and a crap-load of form-stiffeners. I must admit, four conical segments would be MUCH easier to frame & cast from concrete. . . . I really need the most recent version of Hornresp. . . .
If your expansion through the throat chamber and into the flare is smooth with no reflective boundaries in the length dimension you will be fine, no notch problems. If you have a throat chamber with a reflective boundary that reflects the wave back toward the driver or an offset driver horn you will have reflections and notches.
From what I’ve been reading, a pair of 20-Hz horns, each powered by a single 12” driver, will reportedly produce very impressive sound.
Yes, but drivers and very high power amps are much cheaper than building materials and concrete. A few 18s in a much smaller horn would do the same or better performance. But of course it's all up to you.
Why do you want dual bass horns? There's no point, just make one. At a listening distance of 100 feet there shouldn't be any practical advantage to having stereo subs even if crossed over as high as 160 hz.
Does anyone make a fully digital domain circuit, to accomplish this task? I’d like to keep my signal processing fully digital – i.e. from the CD source, through the time delay processor, and through the coross-over network (if possible). I’d prefer to go analog just prior to amplification. I found one delay circuit on the market, however it has an A/D converter on the front-end, and a D/A converter on the output - which is a big turnoff for me. . . . In my opinion, these type of devices tend to be noisy.
There are probably a few but I don't know details as I haven't shopped for my own unit yet. Maybe check out mini dsp and behringer for cost effective options that might do what you want.
Last edited:
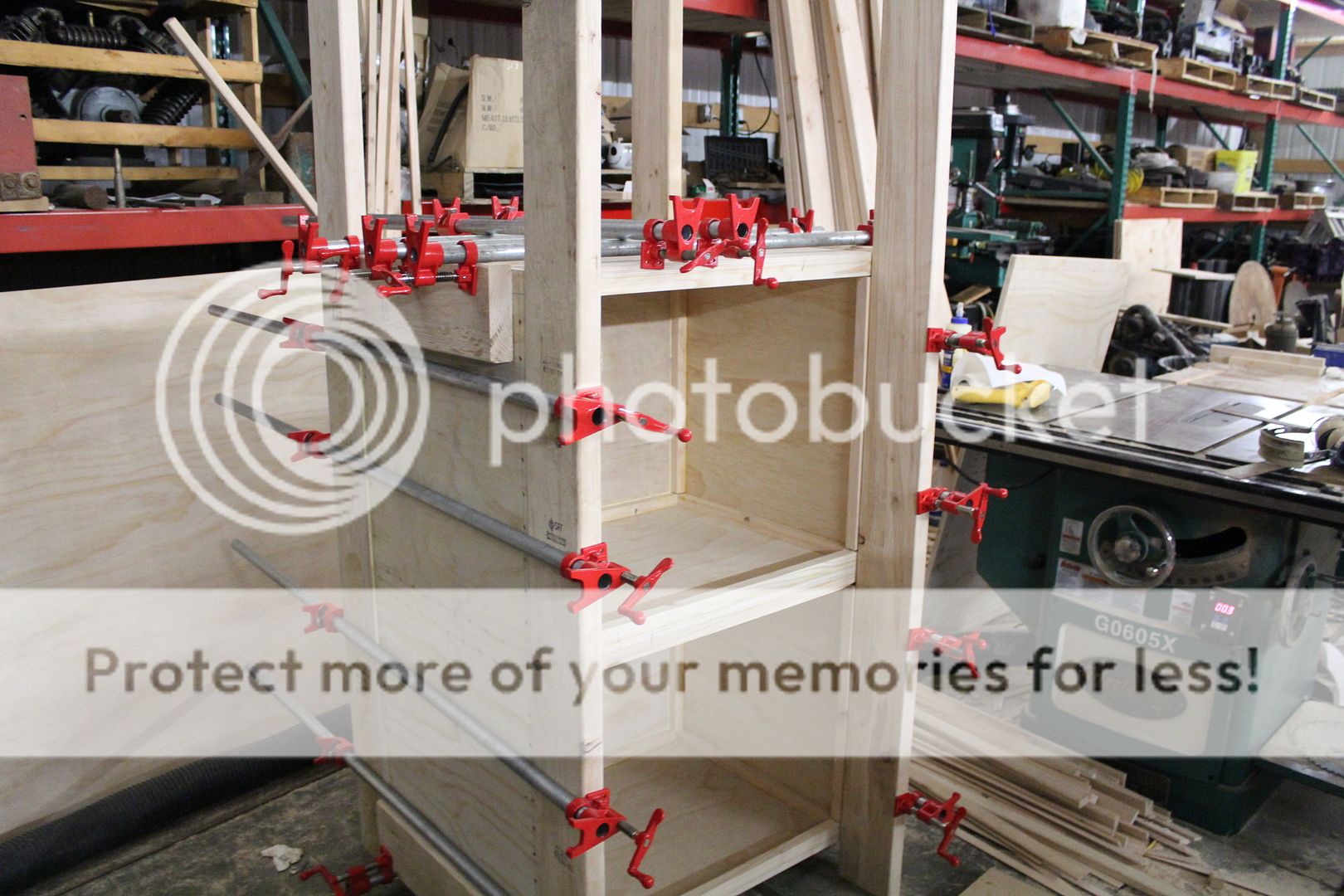
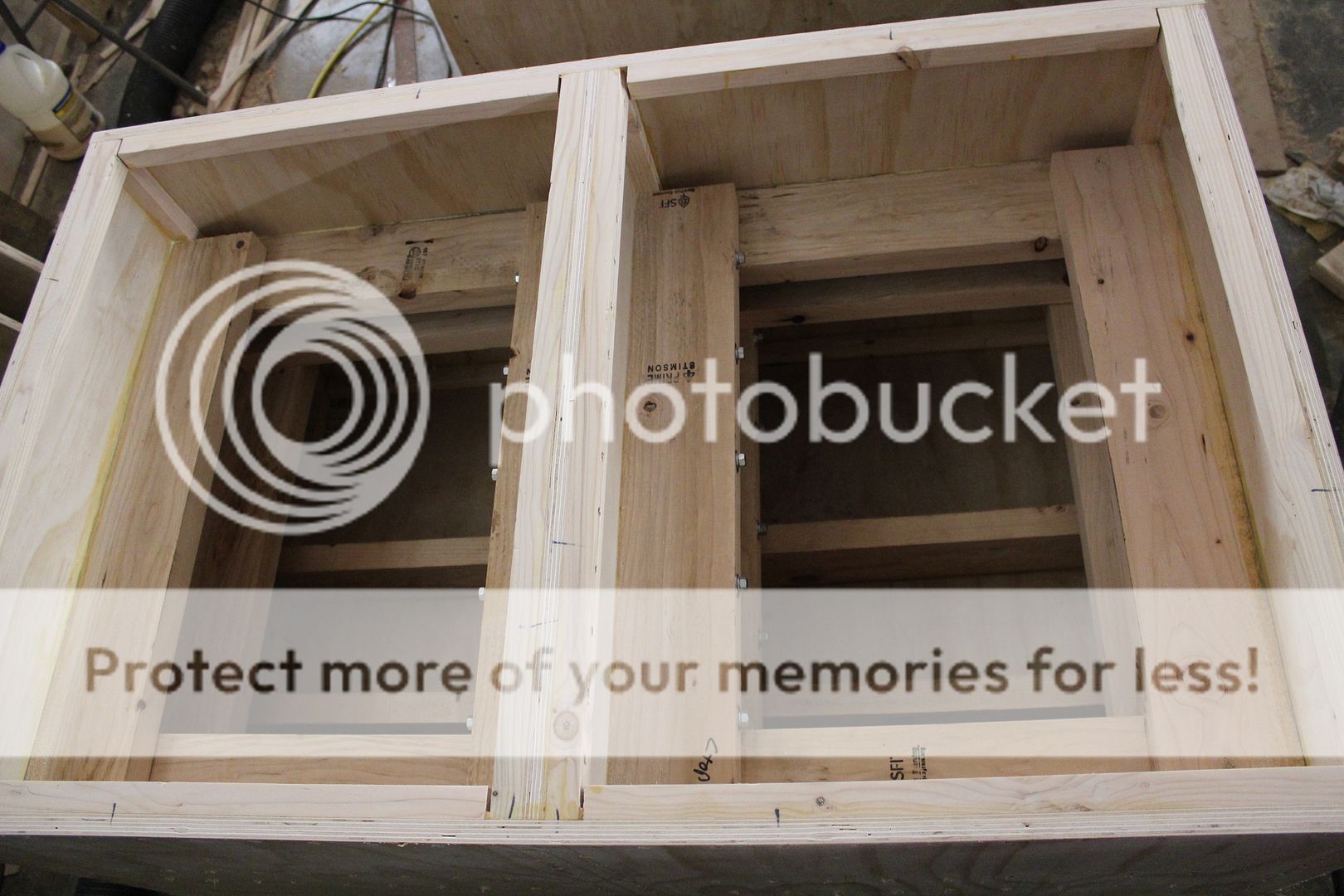
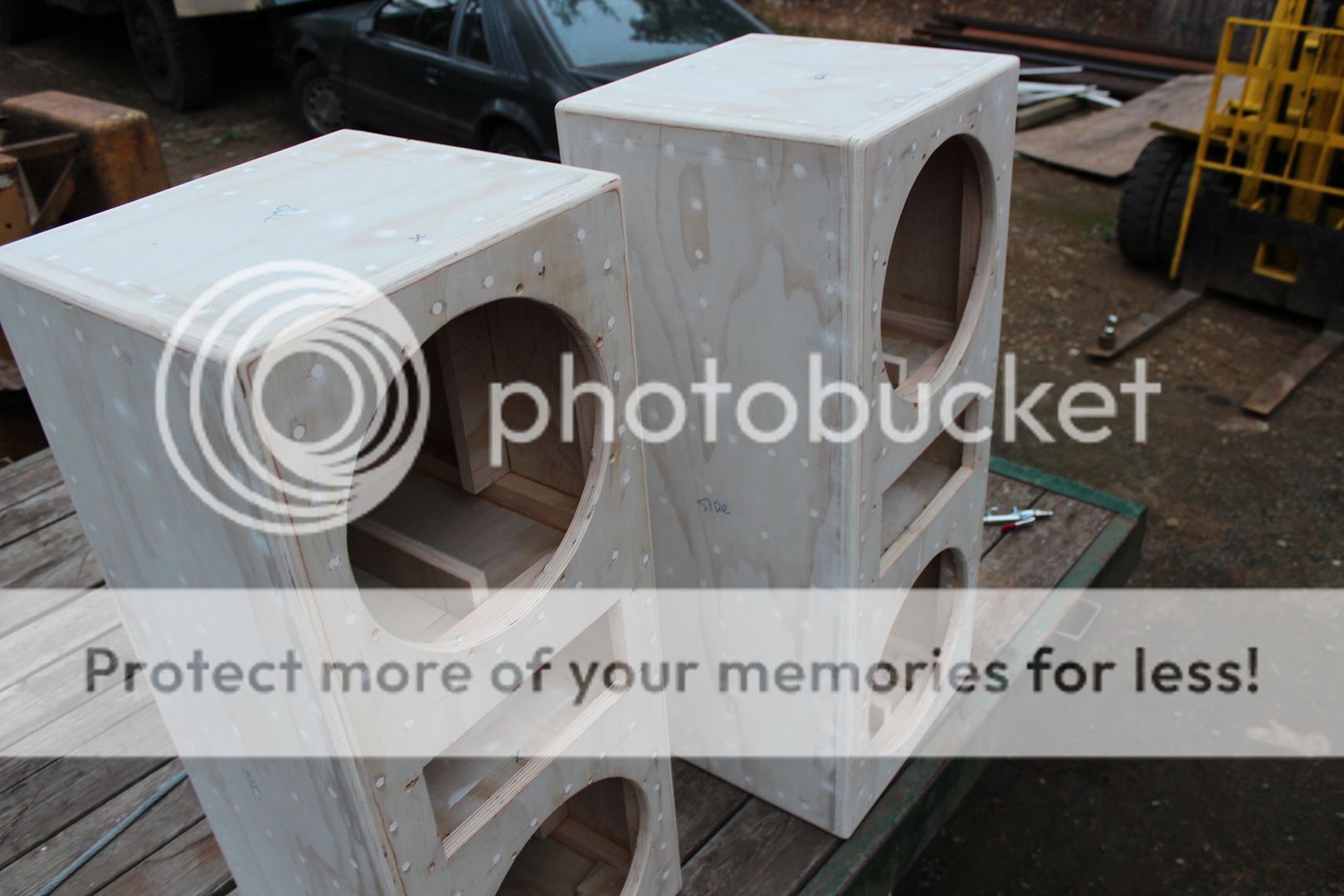
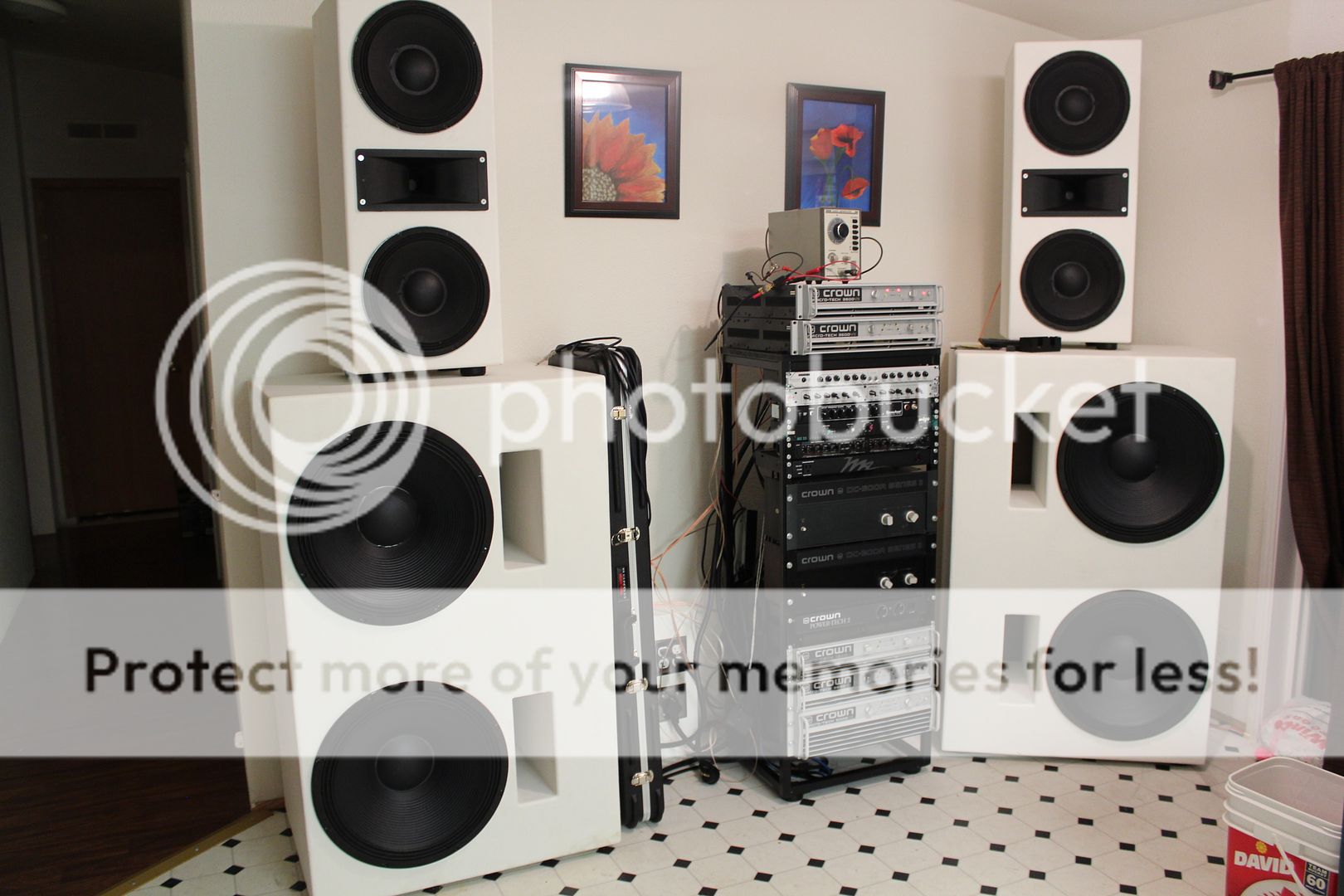
I am able to recreate the same 14-Hz Hyperbolic-Exponential horn in Hornresp. I am still however unable to create an Exponential horn, with a throat area greater than 99,999 cm^2.
I’ll keep tinkering with the hornresp program. I am confident that I’ll be asking more questions. I am still a novice at using the program. . . .
I’m pretty set on building a pair of outdoor 20-Hz concrete bass horns. I was initially contemplating building four of them – two on each side. . . . . (that’s when my wife drew a line). Above is the system that I built for her 5-string bass.
Hi Entropy455,
Nice bass speakers in Post #19.
What is the F3 of the subs? Have you evaluated the port particle velocity @ Xmax for these speakers, e.g.: w/ Hornresp?
Also, as to subwoofers in general, you may want to take a look @ djk's PPSL subwoofer design:
http://www.diyaudio.com/forums/subwoofers/177905-thread-those-interested-ppsl-enclosures.html
PPSL is about mounting the drivers in a common plenum in push-pull configuration. This provides substantial 2nd harmonic distortion cancellation from the push-pull arrangement, as well as additional distortion cancellation depending on the actual construction/size of the plenum (mounting cavity).
PPSL can be applied to any type of enclosure: sealed, ventend, horn... (even outdoor 20-Hz concrete bass horns); djk summarized some of his experiences w/ this driver arrangement in the attached post.
Regards,
Nice bass speakers in Post #19.
What is the F3 of the subs? Have you evaluated the port particle velocity @ Xmax for these speakers, e.g.: w/ Hornresp?
Also, as to subwoofers in general, you may want to take a look @ djk's PPSL subwoofer design:
http://www.diyaudio.com/forums/subwoofers/177905-thread-those-interested-ppsl-enclosures.html
PPSL is about mounting the drivers in a common plenum in push-pull configuration. This provides substantial 2nd harmonic distortion cancellation from the push-pull arrangement, as well as additional distortion cancellation depending on the actual construction/size of the plenum (mounting cavity).
PPSL can be applied to any type of enclosure: sealed, ventend, horn... (even outdoor 20-Hz concrete bass horns); djk summarized some of his experiences w/ this driver arrangement in the attached post.
Regards,
Attachments
- Status
- This old topic is closed. If you want to reopen this topic, contact a moderator using the "Report Post" button.
- Home
- Loudspeakers
- Subwoofers
- Bass Horn Design Question (throat)