Cut list for 18x1250x2500 mm - Excluding part 12
Gentlemen,
For those of you who gets their wood in sheets measuring 1250x2500mm.
I have enclosed a Cut list for two TH18, minus item 12 - top reflector.
/ Andy
View attachment TH-18_Cut_List_DK_1.pdf
Gentlemen,
For those of you who gets their wood in sheets measuring 1250x2500mm.
I have enclosed a Cut list for two TH18, minus item 12 - top reflector.
/ Andy
View attachment TH-18_Cut_List_DK_1.pdf
Hi Djim,
Thanks a lot for the input and explanations.
I see where you are going with the example of total output with the same power source. You definitely have a point there. I must do the math some day of the total power consumption from my setup
I can see from NeoDan's drawing (Post1587) of one of his scheches / builds how including the cone volume can be done.
My questions are then:
1. For the TH18 version1, the cone volume was not added to the horn (S2 area) and should be added after the build?
I tried my best to capture the information about cone corrections in this thread and ended up doing the kctess5 solution by adding the cutout for the driver and I am waiting to get more knowledge about this before adding more cone correction.
3. I am considering the CRESCENDO solution adding some more material (Post 1144) but I am not understanding the relation between the S2 area and the load on the driver? Could that pose a problem with my drivers(18sw100)?
/ Regards Andy
Thanks a lot for the input and explanations.
I see where you are going with the example of total output with the same power source. You definitely have a point there. I must do the math some day of the total power consumption from my setup
In simulation cones are threaded as 'perfect flat' membranes with the acoustic centre in the middle. But in a real built, this volume does exist and the acoustic centre is situated in the cone. This cone volume does not work like an acoustic chamber but is added to the horn (S2 area in HornResp).
I can see from NeoDan's drawing (Post1587) of one of his scheches / builds how including the cone volume can be done.
My questions are then:
1. For the TH18 version1, the cone volume was not added to the horn (S2 area) and should be added after the build?
I tried my best to capture the information about cone corrections in this thread and ended up doing the kctess5 solution by adding the cutout for the driver and I am waiting to get more knowledge about this before adding more cone correction.
3. I am considering the CRESCENDO solution adding some more material (Post 1144) but I am not understanding the relation between the S2 area and the load on the driver? Could that pose a problem with my drivers(18sw100)?
/ Regards Andy
Hi Andy!
Made six SS15 and tried both solutions (perpendicular slots=wide measurement as well as with dishes of diferent diameters around same area in front of the cone, which both result in a bit better cone control).
But what make it play better, a bit lower, and more defined in the upper bass notes reproduction was bracing the mouth and fixing it with the grill moldure.
Regards,
Made six SS15 and tried both solutions (perpendicular slots=wide measurement as well as with dishes of diferent diameters around same area in front of the cone, which both result in a bit better cone control).
But what make it play better, a bit lower, and more defined in the upper bass notes reproduction was bracing the mouth and fixing it with the grill moldure.
Regards,
Hi Andy!
Made six SS15 and tried both solutions (perpendicular slots=wide measurement as well as with dishes of diferent diameters around same area in front of the cone, which both result in a bit better cone control).
But what make it play better, a bit lower, and more defined in the upper bass notes reproduction was bracing the mouth and fixing it with the grill moldure.
Regards,
Hi PASC,
Thanks a lot for sharing.
May I ask how you are using these monsters in your setup?
Not sure what you mean by perpendicular slots in that context -sorry :0)
In the case of the TH18 I am not even sure how much cone volume I should account for in the correction. That is why I am leaning toward CRESCENDO, who is using the same drivers, and made some very nice measurements to document the better results with his cone correction.
I hope i can find the right material to do a grill. Something must be done to protect the driver when wanting to use them in real live. But as NeoDan experienced it doesn't take much covering up of the mouth to reduce the output.
Can i find pictures of your build?
Regards,
Andy
Hi Andy1967,My questions are then:
1. For the TH18 version1, the cone volume was not added to the horn (S2 area) and should be added after the build?
I tried my best to capture the information about cone corrections in this thread and ended up doing the kctess5 solution by adding the cutout for the driver and I am waiting to get more knowledge about this before adding more cone correction.
3. I am considering the CRESCENDO solution adding some more material (Post 1144) but I am not understanding the relation between the S2 area and the load on the driver? Could that pose a problem with my drivers(18sw100)?
Cone-correction can become a little confusing and posts about this subject are spread around this forum. While I explained in rough lines in post#1589 what cone-correction stands for, in practice it is a little different for existing designs, like the Xoc1-TH18.
In designs that don’t have cone-correction, an afterwards installation is not about correcting the complete cone volume. You only correct the volume up to a point that the acoustic centre is corrected and nothing more.
If you would correct for the entire cone-volume in an existing design it will increase the compression ratio of the ‘horn’. For a complete cone volume correction, or perhaps I should say ‘exact’ cone correction, you need to design in 3d like Xoc1 did in post#523 and is implemented in NEO dan’s example.
Personally, I prefer a lay-out with an increased volume around S1, to release pressure from that side of the cone.
In practice, cone correction in 18” loaded TH’s only need two 18mm sheet-strips. Crescendo’s cone correction is a good example of that method.

The cone-volume of your B&C 18SW100 is almost identical to Crescendo’s 18NW100’s, so you can use his work as guideline.
Besides cone-correction, sufficient bracing and mouth reinforcement, I really can recommend using the “broomstick” method, see Link1 Link2 Link3.
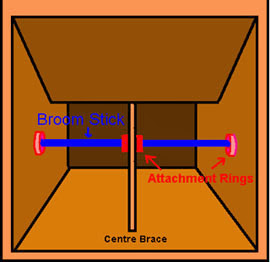
All these structural reinforcements do really improve the performance of any TH.
Last edited:
Dimensions - Cone Correction
Hi Djim, with the cone correction, simple enough solution, however what are the dimensions of each 18mm piece used in the photo? Am I correct to assume an angle on one piece? (looking at the photo)
Regards
Hi Djim, with the cone correction, simple enough solution, however what are the dimensions of each 18mm piece used in the photo? Am I correct to assume an angle on one piece? (looking at the photo)
Regards
Hi Andy1967,
Cone-correction can become a little confusing and posts about this subject are spread around this forum. While I explained in rough lines in post#1589 what cone-correction stands for, in practice it is a little different for existing designs, like the Xoc1-TH18.
In designs that don’t have cone-correction, an afterwards installation is not about correcting the complete cone volume. You only correct the volume up to a point that the acoustic centre is corrected and nothing more.
If you would correct for the entire cone-volume in an existing design it will increase the compression ratio of the ‘horn’. For a complete cone volume correction, or perhaps I should say ‘exact’ cone correction, you need to design in 3d like Xoc1 did in post#523 and is implemented in NEO dan’s example.
Personally, I prefer a lay-out with an increased volume around S1, to release pressure from that side of the cone.
In practice, cone correction in 18” loaded TH’s only need two 18mm sheet-strips. Crescendo’s cone correction is a good example of that method.
![]()
The cone-volume of your B&C 18SW100 is almost identical to Crescendo’s 18NW100’s, so you can use his work as guideline.
Besides cone-correction, sufficient bracing and mouth reinforcement, I really can recommend using the “broomstick” method, see Link1 Link2 Link3.
![]()
All these structural reinforcements do really improve the performance of any TH.
Hi Andy!
To be clear put slots like above picture in 2 boxes and dishes in the others.
But reinforcement was different.
Build only one TH18 and I mean what I did into 6 TH SS15, which has very similar layout should work similarly in TH18.
Firstly put the front longitudinal stiffeners 5cm x 1,5cm(*) to the bottom, from edge to but still continued to vibrate.
Then I reinforced the edges around the mouth with battens(*) to which the iron display was bolted to, and it greatly increases the strength of these walls, so that the hands touch the outside of the walls no longer seems to vibrate as before.
Works great to me.
Regards,
To be clear put slots like above picture in 2 boxes and dishes in the others.
But reinforcement was different.
Build only one TH18 and I mean what I did into 6 TH SS15, which has very similar layout should work similarly in TH18.
Firstly put the front longitudinal stiffeners 5cm x 1,5cm(*) to the bottom, from edge to but still continued to vibrate.
Then I reinforced the edges around the mouth with battens(*) to which the iron display was bolted to, and it greatly increases the strength of these walls, so that the hands touch the outside of the walls no longer seems to vibrate as before.
Works great to me.
Regards,
Hi djcharlyc,Hi Djim, with the cone correction, simple enough solution, however what are the dimensions of each 18mm piece used in the photo? Am I correct to assume an angle on one piece?
The size is one thing but the exact location is even more important since you don't want to increase an uneven loading.
Like some already know I have to visit the hospital again tomorrow so I'm not sure if I have the energy next few days to make calculations/drawings, but I will see what I can do.
Hi PASC,
One extra note. When you use the disk method for cone-volume-correction, the compression is often changed in the first section of the 'horn' (S1 to S2). If this section is not parallel, like in the Xoc1-TH18, it can lead to extreme pressure on the cone side closest to S1.
Hi Djim,
Thanks a lot for doing all that work on the cone correction
. Especially considering that you have other important things to attend to. I hope it is not to serious.
I will try to incorporate your CC in one of my new builds during the weekend
I hope to be able to do some measurements, when I have done some more studying on the mesurement topic. I see people in here are using REW? Recommendations on a specific tool(not to academic) would be appreciated.
I am also considering an excursion measurment, but method is not yet decided.
TimLewis method (post 1585) utilizing a plastic spoon to set a max(safety) excursion actually sounds doable
Regards, Andy
Thanks a lot for doing all that work on the cone correction

I will try to incorporate your CC in one of my new builds during the weekend
I hope to be able to do some measurements, when I have done some more studying on the mesurement topic. I see people in here are using REW? Recommendations on a specific tool(not to academic) would be appreciated.
I am also considering an excursion measurment, but method is not yet decided.
TimLewis method (post 1585) utilizing a plastic spoon to set a max(safety) excursion actually sounds doable
Regards, Andy
Hi Djim!
Re post 1610:
Thanks for advice.
It is extremely severe in the apex of the slot in the SB1000 which deteriorates several of the external suspension of it's loudspeakers with time; there were a try correction by shifting the position of the cone by turning it, instead of modifying the slot...
How did the fixes in SS15, where the shaft walls s1 and s2 are not as different as in (1.28 cm on a side and 0.64 cm on the other side of the edge of the speaker), I think I'll have no problems and still the technique of rotating a clockwise or anti-clockwise so the cone will be influencing menosdesde I care to keep track of the tour and correct settings in the processor.
Also commented in other posts that had increased compression placing a ring under the baffle as suggested by jbell.
All the work we do here is in the sense that we can better control the excursion of the speaker cone that inhabits the THs, and techniques so that what moves in the boxes are the cones of the loudspeakers and nothing else. The market provide us with expensive options in talking to us "help", so we need bigger amps, ... instead we are able to use speakers that can best reproduce what play the instruments and singing the vocals.
Greetings!
Re post 1610:
Thanks for advice.
It is extremely severe in the apex of the slot in the SB1000 which deteriorates several of the external suspension of it's loudspeakers with time; there were a try correction by shifting the position of the cone by turning it, instead of modifying the slot...
How did the fixes in SS15, where the shaft walls s1 and s2 are not as different as in (1.28 cm on a side and 0.64 cm on the other side of the edge of the speaker), I think I'll have no problems and still the technique of rotating a clockwise or anti-clockwise so the cone will be influencing menosdesde I care to keep track of the tour and correct settings in the processor.
Also commented in other posts that had increased compression placing a ring under the baffle as suggested by jbell.
All the work we do here is in the sense that we can better control the excursion of the speaker cone that inhabits the THs, and techniques so that what moves in the boxes are the cones of the loudspeakers and nothing else. The market provide us with expensive options in talking to us "help", so we need bigger amps, ... instead we are able to use speakers that can best reproduce what play the instruments and singing the vocals.
Greetings!
Hi Andy1967,
Thanks, just lacking sleep and feeling like I’ve been hit by a
truck, but in a few days I’m okay again. Nevertheless I’m looking forwards to see your results.
Hi sine143,
You can sim it in HornResp in two ways but both are not ideal. Using 3 reference points can give accurate results but will limit the possibilities for the rest of the 'horn'. Otherwise you will have to use Atc/Vtc for an indication but that isn’t always accurate.
I use the acoustic centre that is hidden in the cone as reference for the height of the cone correction. If you would compensate the complete volume of the cone, the correction will become too large in TH’s with a 'straight' first section. For a full volume compensation the 'horn' path needs to bend and follows the contours of the cone.
Hi PASC,
The SS15 does allow quiet some modification since the compression ratio in the original version is fairly low. I don’t have experiences with cone corrections for the 3015LF since that driver was never cheap (or popular) around here. With other drivers it worked out fine and allowed to increase the compression ratio considerably.
"All the work we do here is in the sense that we can better control the excursion of the speaker cone that inhabits the THs, and techniques so that what moves in the boxes are the cones of the loudspeakers and nothing else. The market provide us with expensive options in talking to us "help", so we need bigger amps, ... instead we are able to use speakers that can best reproduce what play the instruments and singing the vocals.
Greetings!"
I can’t agree more...
Thanks, just lacking sleep and feeling like I’ve been hit by a

Hi sine143,
You can sim it in HornResp in two ways but both are not ideal. Using 3 reference points can give accurate results but will limit the possibilities for the rest of the 'horn'. Otherwise you will have to use Atc/Vtc for an indication but that isn’t always accurate.
I use the acoustic centre that is hidden in the cone as reference for the height of the cone correction. If you would compensate the complete volume of the cone, the correction will become too large in TH’s with a 'straight' first section. For a full volume compensation the 'horn' path needs to bend and follows the contours of the cone.
Hi PASC,
The SS15 does allow quiet some modification since the compression ratio in the original version is fairly low. I don’t have experiences with cone corrections for the 3015LF since that driver was never cheap (or popular) around here. With other drivers it worked out fine and allowed to increase the compression ratio considerably.
"All the work we do here is in the sense that we can better control the excursion of the speaker cone that inhabits the THs, and techniques so that what moves in the boxes are the cones of the loudspeakers and nothing else. The market provide us with expensive options in talking to us "help", so we need bigger amps, ... instead we are able to use speakers that can best reproduce what play the instruments and singing the vocals.
Greetings!"
I can’t agree more...
Last edited:
- Home
- Loudspeakers
- Subwoofers
- TH-18 Flat to 35hz! (Xoc1's design)