I'm interested in picking up one of these amps. BUT, it doesn't work.
I was told with use the amp's driver board becomes conductive. This results in more DC than then the DC Servo can handle and it doesn't engage (turn off [switch]) the speaker protection relay.
I don't know what they made these boards from though.
Anyone run into this problem?
I'll find a schematic and attach it here.
Anyone know how to fix it and have the the speaker protection work along with the DC Servo in the amp?
Here's a PDF, it's on Page 13
From HiFiEngine: LINK
Cheers,
I was told with use the amp's driver board becomes conductive. This results in more DC than then the DC Servo can handle and it doesn't engage (turn off [switch]) the speaker protection relay.
I don't know what they made these boards from though.
Anyone run into this problem?
I'll find a schematic and attach it here.
Anyone know how to fix it and have the the speaker protection work along with the DC Servo in the amp?
Here's a PDF, it's on Page 13
From HiFiEngine: LINK
Cheers,
Hi Sync,
The boards do not become conductive by themselves. Something has to be put on the board and it might become conductive. I have never heard of this problem with Yamaha though.
So what could become conductive? Well, our old friend that killed a number of Adcom (and other brands) amplifiers - bad capacitor electrolyte leaking from ... capacitors! Then there was Sony's gift to the world (I was told it was a Sony chemical product), Sony-bond. It is used to hold parts in place on a PCB as it goes through a wave soldering machine. All is well for a few years, but then other factors turn that stuff into corrosive and conductive solids. When it goes from being a yellow-tan colour to brown and then black it is busy causing problems. High impedance circuits are especially vulnerable to this onslaught.
For the glue, it is just a case of removing it mechanically. You may have to replace components with rotted leads, and maybe copper traces if it was used on the foil side. Sometimes if the glue flowed under and around some parts, you'll have to remove those parts and maybe replace some of them.
Capacitor electrolyte. This is a nasty problem that requires a lot of effort to clean up. Sometime it isn't visible to the naked eye. Your hot soldering iron tip will tell you if it's there. This stuff is highly corrosive and conductive also. The only way to remove it is by removing all the parts in the affected area, replacing some and cleaning all. This stuff can get in between the solder mask and the PCB, and you will have clean, clean, clean - then check with the soldering iron. I have not found any type of cleaner that will remove the electrolyte nicely without damaging anything else it comes into contact with. There has to be a cleaner out there with those properties, but I haven't found it yet.
Most designs of amplifier will work with the servo chip removed. The DC offset might be higher than normal, but the amplifier should still work without it. If you pull the chip and the DC offset comes down, you have a problem in the servo circuit - possibly the op amp or power supply for that op amp. Either way, once the chip has been pulled, you can troubleshoot like a normal amplifier accepting the higher DC offset. The same issues apply. Do you have current for the diff pair? Are the bases close to each other in voltage? If you measure 6 ~ 7 VDC between bases, one transistor has gone into reverse E-B breakdown. Time for a new matched pair after you have found and fixed the problem.
It is possible to figure out what the designed in DC offset is for an amplifier design, roughly. You assume a matched pair of transistors, and this may not be true. You can check for saturated, off and reverse biased transistors from the diff pair to the output pair. When measuring voltages in the output stage, take your meter common to be the actual output. Doing this will reduce noise in your measurements and give you sensible numbers easy to understand. From there, have a look at the schematic and mark your voltages on it (not on the original, a copy only). Using logic and deductive reasoning should lead you to the problem. Do watch for open lower value resistors and shorted diodes. I will often just browse the PCB checking all the PN junctions with my meter on diode test. Resistance check on the low value resistors help to add to the observations you can use when troubleshooting.
Never assume anything.
-Chris
The boards do not become conductive by themselves. Something has to be put on the board and it might become conductive. I have never heard of this problem with Yamaha though.
So what could become conductive? Well, our old friend that killed a number of Adcom (and other brands) amplifiers - bad capacitor electrolyte leaking from ... capacitors! Then there was Sony's gift to the world (I was told it was a Sony chemical product), Sony-bond. It is used to hold parts in place on a PCB as it goes through a wave soldering machine. All is well for a few years, but then other factors turn that stuff into corrosive and conductive solids. When it goes from being a yellow-tan colour to brown and then black it is busy causing problems. High impedance circuits are especially vulnerable to this onslaught.
For the glue, it is just a case of removing it mechanically. You may have to replace components with rotted leads, and maybe copper traces if it was used on the foil side. Sometimes if the glue flowed under and around some parts, you'll have to remove those parts and maybe replace some of them.
Capacitor electrolyte. This is a nasty problem that requires a lot of effort to clean up. Sometime it isn't visible to the naked eye. Your hot soldering iron tip will tell you if it's there. This stuff is highly corrosive and conductive also. The only way to remove it is by removing all the parts in the affected area, replacing some and cleaning all. This stuff can get in between the solder mask and the PCB, and you will have clean, clean, clean - then check with the soldering iron. I have not found any type of cleaner that will remove the electrolyte nicely without damaging anything else it comes into contact with. There has to be a cleaner out there with those properties, but I haven't found it yet.
Most designs of amplifier will work with the servo chip removed. The DC offset might be higher than normal, but the amplifier should still work without it. If you pull the chip and the DC offset comes down, you have a problem in the servo circuit - possibly the op amp or power supply for that op amp. Either way, once the chip has been pulled, you can troubleshoot like a normal amplifier accepting the higher DC offset. The same issues apply. Do you have current for the diff pair? Are the bases close to each other in voltage? If you measure 6 ~ 7 VDC between bases, one transistor has gone into reverse E-B breakdown. Time for a new matched pair after you have found and fixed the problem.
It is possible to figure out what the designed in DC offset is for an amplifier design, roughly. You assume a matched pair of transistors, and this may not be true. You can check for saturated, off and reverse biased transistors from the diff pair to the output pair. When measuring voltages in the output stage, take your meter common to be the actual output. Doing this will reduce noise in your measurements and give you sensible numbers easy to understand. From there, have a look at the schematic and mark your voltages on it (not on the original, a copy only). Using logic and deductive reasoning should lead you to the problem. Do watch for open lower value resistors and shorted diodes. I will often just browse the PCB checking all the PN junctions with my meter on diode test. Resistance check on the low value resistors help to add to the observations you can use when troubleshooting.
Never assume anything.
-Chris
Thanks Chris,
From what I can tell the DC Servo is a TL072. 1/2 and 2/of 2 from schematic. Too large a file to upload and I can't cut it down smaller...PDF doesn't like me any more. 🙁
So, if I clean these boards with laquer Thinner, then 99.99 ISO, then do a soap and water wash with natural bristel brush....then air dry of oven at say 150F...before fooling with them maybe okay? I don't see any FETs in them.
Cheers,
From what I can tell the DC Servo is a TL072. 1/2 and 2/of 2 from schematic. Too large a file to upload and I can't cut it down smaller...PDF doesn't like me any more. 🙁
So, if I clean these boards with laquer Thinner, then 99.99 ISO, then do a soap and water wash with natural bristel brush....then air dry of oven at say 150F...before fooling with them maybe okay? I don't see any FETs in them.
Cheers,
Hi Sync,
I wouldn't immerse anything in lacquer thinner! Maybe screws to clean them, but nothing else.
You're going to have to remove all the parts in the affected area for sure. Replace all the smaller electrolytic capacitors after you have it cleaned. Clean any parts you will be pulling off as well. Remember, I'm not sure what cleaner will work on this stuff. I think you should also try dishwashing soap too.
-Chris
I wouldn't immerse anything in lacquer thinner! Maybe screws to clean them, but nothing else.
You're going to have to remove all the parts in the affected area for sure. Replace all the smaller electrolytic capacitors after you have it cleaned. Clean any parts you will be pulling off as well. Remember, I'm not sure what cleaner will work on this stuff. I think you should also try dishwashing soap too.
-Chris
Hi Chris,
That was in my bag of tricks. I also use Lighter Fluid (aka BBQ Starter [liquid napalm])
oh, that is Naptha. It works to get some stuff off. Then if need be I always have
ethanol. In a pinch you get find the almost pure stuff at liquor store, it will take
most other stuff off that other chemicals won't....
Been searching around it could also be the glue from
holding down the caps and electrolytic leakage into the glue
and then contaminating the Servo OpAmps.
We'll see, it's ice cold and rainy here, a good mix for sleet and
drivers who haul-asche and brake madly on bridges or overpasses
and screw up traffis for everyone.
Anyway I'm just doing research mode because I'm redoing the bench
and installing shelves and general organizing. The pain of trying to
get reorganized with tools, parts, and plastic containers everywhere.
Cheers,
That was in my bag of tricks. I also use Lighter Fluid (aka BBQ Starter [liquid napalm])
oh, that is Naptha. It works to get some stuff off. Then if need be I always have
ethanol. In a pinch you get find the almost pure stuff at liquor store, it will take
most other stuff off that other chemicals won't....
Been searching around it could also be the glue from
holding down the caps and electrolytic leakage into the glue
and then contaminating the Servo OpAmps.
We'll see, it's ice cold and rainy here, a good mix for sleet and
drivers who haul-asche and brake madly on bridges or overpasses
and screw up traffis for everyone.
Anyway I'm just doing research mode because I'm redoing the bench
and installing shelves and general organizing. The pain of trying to
get reorganized with tools, parts, and plastic containers everywhere.
Cheers,
"I don't know what they made these boards from though."
Paper and epoxy (IIRC).
If badly discolored (from heat) they may not be serviceable.
Paper and epoxy (IIRC).
If badly discolored (from heat) they may not be serviceable.
Hi djk,
I don't know either.
They have definitely browned from use than the when
the units left the factory. I've just have to wait and see.
I don't know either.
They have definitely browned from use than the when
the units left the factory. I've just have to wait and see.
I've sometimes scraped black deposits off these type of boards, and then filled with epoxy (as needed).
Some of these companies have no idea how to de-rate components, or what a reasonable temperature rise is.
Some of these companies have no idea how to de-rate components, or what a reasonable temperature rise is.
Sync, Wash/brush/rinse with Isopropyl (both sides, remove flux/conformal coating etc), wash in sink hot water with small amount detergent, rinse ideally in RO/Distilled water, compressed air dry, bake for extended period.
I have 'rescued' hundreds of remote controls, and several amp pcb's by this method.
Phenolic paper pcb's do discolour/darken with age and temp, but do not go conductive unless totally charred/carbonised.....the 'advice' you got sounds like uninformed BS to me.
Anatech's long post is correct advice, especially regarding decomposed yellow glue turning dark/brown and corrosive.....remove every last bit.
Once this is all done you should be good to go in diagnosing the fault (if it still exists).
This series of Yamaha amps are great performing machines, clean and clear, fat and solid sounding with plenty of usable power....ie it's very well worth repairing and the meters are cool too.
Close inspection of the OPS schematic reveals a most unusual arrangement with 'sequential/series' drive of the OP transistors -
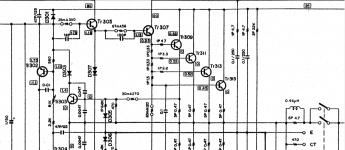
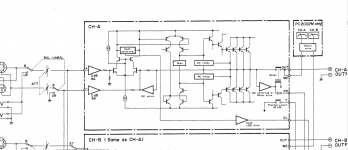
What's the deal going on here....anybody done sims ?.
Dan.
I have 'rescued' hundreds of remote controls, and several amp pcb's by this method.
Phenolic paper pcb's do discolour/darken with age and temp, but do not go conductive unless totally charred/carbonised.....the 'advice' you got sounds like uninformed BS to me.
Glycol is water soluble, and I have never had problems in removing leakages using water/detergent.The electrolyte used in aluminium electrolytic capacitors is a formulation developed to provide the required properties for the capacitor - voltage rating, operating temperature range and the like. It primarily consists of solvent and a salt (required to provide the electrical conduction). Common solvents include ethylene glycol, and common salt include ammonium borate and other ammonium salts.
Anatech's long post is correct advice, especially regarding decomposed yellow glue turning dark/brown and corrosive.....remove every last bit.
Once this is all done you should be good to go in diagnosing the fault (if it still exists).
This series of Yamaha amps are great performing machines, clean and clear, fat and solid sounding with plenty of usable power....ie it's very well worth repairing and the meters are cool too.
Close inspection of the OPS schematic reveals a most unusual arrangement with 'sequential/series' drive of the OP transistors -
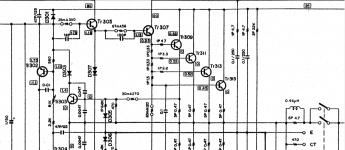
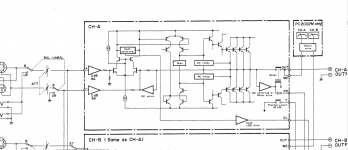
What's the deal going on here....anybody done sims ?.
Dan.
Last edited:
"the 'advice' you got sounds like uninformed BS to me."
From an authorized Yamaha service center (who at one time was also offered the position of National Service Manager for Yamaha). Naw......he doesn't know what he is talking about.
From an authorized Yamaha service center (who at one time was also offered the position of National Service Manager for Yamaha). Naw......he doesn't know what he is talking about.
Max,
Some components will wick fluids into them, capacitors if the seals are damaged for example. Some transistors will also suffer from this. In general, you want to avoid dipping entire PCBs into any fluid.
This any help Sync?
If you read what was written, I said that it would be what was on the PCB material that was conductive. You need to take more care with how you read posts, and maybe put a brake on what you write in response.Phenolic paper pcb's do discolour/darken with age and temp, but do not go conductive unless totally charred/carbonised.....the 'advice' you got sounds like uninformed BS to me.
Interesting question considering what the OP was concerned about. No need for any simulations as the circuit works fine as Yamaha designed it. I can only assume you have done zero service work in your life. Are you an armchair quarterback by chance?What's the deal going on here....anybody done sims ?.
Some components will wick fluids into them, capacitors if the seals are damaged for example. Some transistors will also suffer from this. In general, you want to avoid dipping entire PCBs into any fluid.
This any help Sync?
Gents,
Yes it is. But I have to wait and see. I got shot in the eye, so I'm down for a bit. Still planning but I have to wait until it open it up take pictures, etc. I've only seen the pics so far.
Max what is the RO in distilled water?
That is kind of what I do as a finished.
A couple years a go I got a 2.00 amp for my garage at a garage sale. It was in their garage and covered with paint, mouse and bird droppings etc.
I figured what the hell I'll give it a try, So I first treated the pots switches with the DeOxit, routing, then I hosed out the units, then scrubbbed with manual dish detergent, rinse hose, the ISO Rinse, air blew it off a few times, let it dry in the Texas Heat (Big drought that year) .
I think I MCL100 the pots and switches, and jacks.
Heck, it's been working fine. I couldn't believe it. It is a little HK3300 receiver. IN the garage. It was missing one knob, and I've not bothered to replace it.
I understand the scrape and fill if needed.
Okay going to run, thanks djk, anatech, max.
Cheers,
Yes it is. But I have to wait and see. I got shot in the eye, so I'm down for a bit. Still planning but I have to wait until it open it up take pictures, etc. I've only seen the pics so far.
Max what is the RO in distilled water?
That is kind of what I do as a finished.
A couple years a go I got a 2.00 amp for my garage at a garage sale. It was in their garage and covered with paint, mouse and bird droppings etc.
I figured what the hell I'll give it a try, So I first treated the pots switches with the DeOxit, routing, then I hosed out the units, then scrubbbed with manual dish detergent, rinse hose, the ISO Rinse, air blew it off a few times, let it dry in the Texas Heat (Big drought that year) .
I think I MCL100 the pots and switches, and jacks.
Heck, it's been working fine. I couldn't believe it. It is a little HK3300 receiver. IN the garage. It was missing one knob, and I've not bothered to replace it.
I understand the scrape and fill if needed.
Okay going to run, thanks djk, anatech, max.
Cheers,
.....I was told with use the amp's driver board becomes conductive. This results in more DC than the DC Servo can handle and it doesn't engage (turn off [switch]) the speaker protection relay.
Riiight...I don't see "From an authorized Yamaha service center"....which post please."the 'advice' you got sounds like uninformed BS to me."
From an authorized Yamaha service center (who at one time was also offered the position of National Service Manager for Yamaha). Naw......he doesn't know what he is talking about.
Max, If you read what was written, I said that it would be what was on the PCB material that was conductive. You need to take more care with how you read posts, and maybe put a brake on what you write in response.
Sure, and you said further that decomposed glue and leaked electrolyte could be causes of electrical leakage problems, all good.Hi Sync,
The boards do not become conductive by themselves. Something has to be put on the board and it might become conductive. I have never heard of this problem with Yamaha though.
You lament removing electrolyte, I'm reinforcing you by sayin' I reckon water is the best solvent in this case (after removing the solvent solubles like flux and conformal coatings) because the capacitor electrolyte constituents are glycols and salts which 'dry' solvents won't touch.
Sync, Reverse Osmosis treated water.
I'm just sayin' that for the final scrub/rinse ideally use 'pure' water....deionised/distilled/RO etc immediately before the compressed air blast and extended thermal drying cycle.
Dan.
Last edited:
Sync, what price for this 'dead' Yamaha amp, and what are the symptoms ?....ie IMHO the 'conductive pcb' 'advice' is a red herring.
Dan.
Dan.
Hi Dan,
What might help is a less argumentative posting style.
An aqueous cleaning solution might work (dish soap or grease removal cleaners), but I have yet to find one that will attack this type of residue as a "sure thing".
As for the drying process, ideally the temperature would be less than 85 °C. 50 °C might be ideal as several electronic components are sensitive to high temperatures. Semiconductors might fail at 150 °, and certainly any capacitors rated for 85 ° would have perished. Many plastics will deform and I have no idea how a trim pot might react to high temperatures. I think anything 50 °C and lower would do a fine job of drying out a circuit board without killing a bunch of parts. In the winter here, I just have to leave parts out to dry because the humidity can drop so low you don't need any heat to get the job done.
-Chris
What might help is a less argumentative posting style.
An aqueous cleaning solution might work (dish soap or grease removal cleaners), but I have yet to find one that will attack this type of residue as a "sure thing".
As for the drying process, ideally the temperature would be less than 85 °C. 50 °C might be ideal as several electronic components are sensitive to high temperatures. Semiconductors might fail at 150 °, and certainly any capacitors rated for 85 ° would have perished. Many plastics will deform and I have no idea how a trim pot might react to high temperatures. I think anything 50 °C and lower would do a fine job of drying out a circuit board without killing a bunch of parts. In the winter here, I just have to leave parts out to dry because the humidity can drop so low you don't need any heat to get the job done.
-Chris
Hi Dan,
A PCB that has conductive areas for any reason is cause for concern, and it is a very real problem. Certainly in your career, you must have run into these issues more than once.
From post #1:
So given that you disagree with other members, and you have some experience with this type of work, how about making a few suggestions of your own instead of disagreeing with everyone? I'd like to see how you would approach this problem as reported.
-Chris
What do you mean by this?ie IMHO the 'conductive pcb' 'advice' is a red herring.
A PCB that has conductive areas for any reason is cause for concern, and it is a very real problem. Certainly in your career, you must have run into these issues more than once.
From post #1:
That's everything he can tell you about the amplifier. It says enough for me to give him some pertinent suggestions and advice. The description given Sync from a person not trained in electronics is one I've heard many times to describe the issue, he really means that the PCB does suffer from conductive contamination. This would affect a DC servo in the way the problem has been described. So everything jives with some real problems that can occur. Heck, the issue may even be a spilled drink. All we know really is that the DC servo is misbehaving. Conductivity between some traces is a worst case diagnosis. An actual component failure in the amplifier is easier to repair, and I did recommend the servo IC be removed to check the circuit operation first.I was told with use the amp's driver board becomes conductive. This results in more DC than then the DC Servo can handle and it doesn't engage (turn off [switch]) the speaker protection relay.
So given that you disagree with other members, and you have some experience with this type of work, how about making a few suggestions of your own instead of disagreeing with everyone? I'd like to see how you would approach this problem as reported.
-Chris
Anatech chill, I looked at the website of your former business and we are carbon copies....I have more experience in pro live sound/staging/production.
To you and me it sounds like there is a DC offset/protection issue, sounds like no blowing fuses.
From experience you and I would be looking first for physical causes like dead glue, leaked electrolyte, smoke fluid/disco lint, spillages etc.
Second would be failed passives or actives.
IME worst and unusual case would be leakage currents due to spilled electrolyte....it usually dries and goes oc, but may corrode conductors/solder joints/vias to hr/oc as you suggest.
My experience of long term maintaining hire fleets of this series Yamaha amps is that cracked/cooked solder joints are their main failure mode, apart from that they are essentially bullet proof.
If Sync can get hold of this amp for a fair price between us the repairs should be low cost and he should gain a cool amp....win/win.
Dan.
Sync has gotten second hand information.I was told with use the amp's driver board becomes conductive. This results in more DC than then the DC Servo can handle and it doesn't engage (turn off [switch]) the speaker protection relay.
To you and me it sounds like there is a DC offset/protection issue, sounds like no blowing fuses.
From experience you and I would be looking first for physical causes like dead glue, leaked electrolyte, smoke fluid/disco lint, spillages etc.
Second would be failed passives or actives.
IME worst and unusual case would be leakage currents due to spilled electrolyte....it usually dries and goes oc, but may corrode conductors/solder joints/vias to hr/oc as you suggest.
My experience of long term maintaining hire fleets of this series Yamaha amps is that cracked/cooked solder joints are their main failure mode, apart from that they are essentially bullet proof.
If Sync can get hold of this amp for a fair price between us the repairs should be low cost and he should gain a cool amp....win/win.
Dan.
Hi Dan,
What website? I don't follow them and the web site was constructed long after I left. My pro activities were things they lost instantly. You can't really judge my experience from a website I have no part in.
I agree with you that the most common failure for these amps are solder joint failures. Otherwise they are excellent amplifiers. I would normally recommend that he buy it as well. That's assuming there isn't a real conductivity issue with the board. No telling what is really going on since we can't see it right in front of us.
-Chris
What website? I don't follow them and the web site was constructed long after I left. My pro activities were things they lost instantly. You can't really judge my experience from a website I have no part in.
I agree with you that the most common failure for these amps are solder joint failures. Otherwise they are excellent amplifiers. I would normally recommend that he buy it as well. That's assuming there isn't a real conductivity issue with the board. No telling what is really going on since we can't see it right in front of us.
-Chris
There's a guy on Audiokarma that says he has several Yamaha amplifiers that were from that "Happy Place" in Anaheim,CA. They were supposedly on 24/7 for years until they were replaced. He was told that the boards become conductive and that's the reason for the DC offset problem. Maybe this is the source of this information/disinformation.
Craig
Craig
- Status
- Not open for further replies.
- Home
- Amplifiers
- Solid State
- DC Servo Problems Yamaha P2202M